The chief supply chain executive at an award-winning integrated delivery network (IDN) in the southeast once quipped that he knows precisely when his team excels at their craft – the phones are silent and the emailboxes empty of clinician complaints about backorders, depleted shelves, empty cubbies and general stockouts.
Similar to the hospitality and retail industries, shelf, storeroom and warehouse space among healthcare providers and suppliers house precious cargo – assets that must be used by clinicians on patients for the organization to be reimbursed by insurance companies and payers.
That’s why the skeleton of a storeroom or warehouse must be designed and organized to take advantage of the available footprint and conform to desired workflow.
As a result, configuring and custom-designing shelf and storage space to maximize, if not optimize, access to inventory, ease of stocking and retrieving, tracking, tracing and transporting must start as a science before refinement as art.
Shelf, storage configuration
Eight experts in supply chain inventory and storage management share their recommendations for making shelf and storage space work effectively and efficiently.
Eliminate, use wasted space
Supply chain professionals should start with the big picture, according to Randalyn Harreld, CRCST, CIS, CER, CHL, C.S.P.D.T, C.A.S.S.P.T, BLS, AAS, clinical education manager-US, BeliMed.
“When configuring a storage area, it’s important to first have an idea of what inventory you plan to store in that space,” she told Healthcare Purchasing News. “There are a few common practices that will help streamline this process. Begin by rightsizing the instrumentation trays, sets and items to be stored in the space so there is a reduction in wasted space. Many times, with simple storage racks that offer open shelf space, it can be difficult to utilize all available space. In todays’ healthcare world, space is limited and should be used efficiently. Another consideration is to eliminate the need for redundant handling and touching of all sterilized items. Find a way to do an analysis of inventory so your team can determine the end destination of all items processed. This will help you to configure storing those items in a manner that either allows them to be closest to their end destination or easily accessible for care team members or patients. For example, completing a “tracer” of inventory to and from its starting point and ending point over a set period can help you to determine how often an item is used, who uses it, when does it need to be transported and what is the best way to transport it.”
Harreld encourages supply chain pros to pursue intuitive custom designs that enable ergonomically friendly handling, various sizes and configurations and frameworks that eliminate rusting. She further emphasizes the visual element.
“Place the inventory in a systemic manner, whether that be alphabetically, or maybe by specialty or numerical order,” she indicated. “Make sure to label each section with signage that is easy to see and visible. During the ‘tracer’ investigation you can also monitor the number of steps the employees are taking when retrieving these items and place the inventory in the best place possible to make it easily accessible.”
Wed design to workflow
Configure a layout that conforms to staff traffic, particularly for equipment, advises Todd Stewart, vice president, Solution Sales, CenTrak.
“Healthcare organizations must understand where the need for equipment lies, where it is being used and where tools are being underutilized,” Stewart noted. “Technology such as real-time location systems (RTLS) can manage, track, and automate the ebb and flow of logistics and courier operations moving in and out of the warehouse and storage spaces. By implementing an asset management solution in a hospital, staff will know which assets are going to which destinations, how often, when and if they’re appropriately cleaned. These details will help an organization develop a storage strategy to inform equipment location, based on proximity to the point of patient care – when and where it is needed most.
“Optimizing storage locations increases cost savings, reduces excess waste, informs rental decisions and can eliminate inefficient movement throughout the facility,” he added. “Furthermore, it can help management teams understand if something is over or under-utilized and determine if there is a need for additional equipment, storage space, etc.”
Place footprint in context
Designing efficient storage and shelf space always starts with a well-thought-out plan and involves a blend of organization, accessibility and optimization, emphasizes Jennifer Nageotte-Elliott, partner, Diamond Storage Solutions.
“At Diamond, we help our customers with pre-planning by focusing on stating intended goals, identifying successful outcomes and building the pathway through support of 3-D renderings and visualization of design layouts with our staged products,” Nageotte-Elliott noted. She highlights seven strategies and tactics her firm uses to stress best practices for healthcare environments.
- Material construction. “Our products are constructed with materials that limit dust attraction and offer ventilation to contents being stored, driving cleanliness and infection prevention support,” she said.
- Ease in installation. “Our shelving solutions can be installed in less than 13 minutes!”
- Regulatory requirements. “Ensure supplies are stored away from sprinkler deflectors, off the floor, away from outside walls, etc.”
- Safety and ergonomics. “Store liquids and heavy items on lower or bottom shelves, keep aisles clear of clutter to prevent tripping, stage products close to point of use and frequently accessed items at waist level for easy reach.”
- Operational efficiencies. “Consider categorization and labeling, implement zoning strategies, incorporate signage or color coding to drive visual management, develop clear [standard operating procedures] for stocking, organizing, and retrieving inventory, arrange items based on their frequency of use and expiration dates (FIFO/LIFO).”
- Adaptability. “Incorporate flexibility in storage design to ensure readiness to address any ongoing and future surges or emergencies.”
- Ask your team! “Gather feedback from staff involved in the inventory process as they might have insights into optimizing the space based on their day-to-day experiences.”
Block and tackle
Ian Loper, vice president, DSI, offers a football motif for shelving and storage design.
“Storage system mobility, product adjustability, enhanced labeling, and custom designing a department’s workflow through the lens of a storage consultant are all keys to optimizing the throughput in a department’s overall storage space,” Loper said. “With supplies constantly changing, having the ability to adjust the bin, compartment size or shelf location is key to maximizing the space. It’s like the game of football. As they say, it’s a game of inches. One cubic inch lost in one spot adds up to hundreds of cubic feet lost throughout a department. Every inch counts in the hospital, especially in the OR and Sterile Processing departments. If you can’t relate to the football analogy, then maybe you can relate to the video game Tetris. You want a storage system in your department that is good at the game of Tetris, knocking out solid lines one after the other.”
Go out on a limn
For Joseph Hagedorn, senior manager, Supply Chain Optimization, Shelving & Storage, Medline, supply chain pros should embrace their inner artist.
“The first recommended step is to draw out the room and layout racking to maximize square footage while ensuring that the drawing is to scale. Also note where light fixtures and fire sprinkler heads are to align with isle space,” he said. “The most effective way to produce a 2-bin Kanban set-up is comprising racks three feet in length and two feet wide. Casters give each storage rack mobility for cleaning and emergencies, such as water leaks, to move the racks.
“Open access or freestanding designs allow multiple staff members to be working in the same area at the same time to put up products, pull items for distribution or case pick and put away any returning items,” Hagedorn continued. “Adding as many shelves as possible will minimize potential lost vertical space in between shelves and combat the issue of dead space. Creating these spaces is all about creating a flow that is best for efficiency, so it is important to consider that from the beginning. High-density storage systems that are on a track system can sometimes aid in condensing the storage of items that aren’t accessed frequently. When the sliding racks are compressed together you lose visibility to PAR levels and access to product is limited to one staff member. Some room designs benefit from a blended mix of both traditional and high-density storage systems.”
Hagedorn further recommends healthcare organizations standardize on grocery/retail shelf strategies for shelf layout. “Find the areas that are most easily accessible and add most frequently used and critical items there,” he noted. “The items that are used the least should be placed in areas that are less accessible. The guidelines for this process should continue to be followed until all the shelves are filled and products are placed. Size, category and other compliance rules such as agencies, local/state/regional rules, and infection prevention should also be considered through this process, ensuring your set up fulfills guidelines. Having this standardization ensures all team members touching the product from supply chain to clinical have both efficiency in the room and ergonomic best practice by reducing the amount of movement needed to manage and use supplies.”
Healthcare organizations should work with the right company to design and implement shelving and storage operations, according to Hagedorn. “Working with an experienced partner/supplier that has a full portfolio of storage solutions, implementation support and design support can help administer day to day support staff to see how the storage systems will fit and look within the given space,” he said. “Medline has recently offered customers the ability to see the 3-D modeled drawings as a photographic render image. This new tool is utilized when project leaders present the overall goals and concepts of a design to administration and key stakeholders.”
Standardize to prioritize
Derek Naylor, director, Supply Chain Optimization and Technology, U.S. Medical Products and Distribution, Cardinal Health, concurs about standardization as a viable and valuable strategy.
“I’ve seen less customization and more standardization play the biggest part in a successful storage and inventory strategy,” Naylor insisted. “When creating a warehouse that is too customized, the records alignment and target utilization requirements are more challenging. Having a standard profile strategy and matching inventory parameters, such as cube and ti-hi [the number of boxes/cartons stored on a tier and the number of layers high they will be stacked on a pallet], can maximize utilization and flexibility across a multitude of items and [stock-keeping unit] profiles.
“Additionally, the standardized warehouse physical slot can enable more flexibility with any inventory slotting optimization software, that would facilitate a more optimized stocking and retrieving strategy based on SKU velocities, reducing waste in the form of excess travel,” he continued. “Finally, having a precise single location per SKU versus multiple SKUs being stored on a single shelf location enables more precise tracking and tracing down to the pallet level. Having multiple SKUs per location can increase quality defects without proper countermeasures such as check digits/strings, supplemental pictures, bar-code or RFID scanning.”
Link workflow steps
Kurt Baker, consulting director, Vizient, refers to a fundamental element of supply chain for shelving and storage connections – the link between workflow steps.
“Each warehouse workflow must be identified along with an understanding of how each warehouse process relates to the other,” Baker said. “Comprehending how inventory flows from the receiving dock, to put-away, to shipping is crucial to the design and configuration of storage space. The placement of shelving, pallet racks and conveyors, along with workflows and traffic patterns, affects the ability to use the available space.”
Options abound, Baker adds. “Vertical space for storing bulk items should be used when available. Vertical storage is accomplished with selective pallet racks, pallet flow racks and drive-in racking, etc. Wire shelving is the most efficient way to store logical unit-of-measure items. It is adjustable and can help maximize the use of available storage capacity. Gravity-flow racking, which as the name suggests, relies on gravity to load, organize and retrieve items, should be considered for high-volume items with expiration dates to help with ease of stocking and to ensure first-in-first-out rotation is followed. Product slotting of fast-moving/high-volume items in the storage area is another method to increase efficiency and ease of shipping.”
Organize to size
Adapting a retail mindset can prove beneficial to healthcare providers for enabling access to necessary products, observes Tom Redding, senior managing director, Healthcare, St. Onge Co.
“One of the most useful strategies to maximize storage space is to stock similar products together, which will most likely require similar storage bin/component sizes and allow the available storage space to be utilized effectively,” he said. “Having multiple bin/component sizes together will impact storage utilization. There is a balancing act of grouping products together to maximize storage utilization while also accommodating clinical preference for products that may be used together but may require different sizes of storage bins.”
Redding notes the many different types of storage alternatives on the market and emphasizes the importance for hospitals to understand their available storage footprint versus the frequency of access. “Too often we see hospitals that focus on minimizing their storage footprint to turn around and waste value clinical labor because there is an inventory access pinch point (e.g., using a high-density storage option when there is a high frequency of accessing the same inventory location will impact labor utilization),” he noted. “Selecting the right storage solution requires a thoughtful approach to understand the availability of storage, velocity of inventory, storage utilization and labor utilization to access the inventory – either from the ‘clinical picking’ or ‘restocking’ point of view.”
What providers want
Based on their interaction with provider customers, supply chain product and service experts see a range of attributes, benefits and features of shelving and storage equipment favored within hospital storerooms and warehouses for which supply chain pros request.
Enable flexibility, variation
Providers simply want to control their options and pivot when necessary, observes BeliMed’s Harreld.
“When looking at the variety of storage options out there in the industry today, some of the most important benefits and criteria that drives their decision making and selection process is the ability to custom-design the layout and structure in various ways throughout their department,” she said. “Not having a one-size-fits-all option is critical to the success of any department. Another important factor is the ability to accommodate all sizes of inventory – from shelves that can hold one tray of any weight from one pound to 25 pounds and be sturdy enough to last, and durability that can withstand the heavy wear and tear that comes with use. Each lane and aisle and row much be customized to hold inventory for that set configuration. Another factor that has helped many departments be successful is the unique labeling, options that are visible and color-coded so they can accommodate many different specialties and items and see from far distances clearly and legibly.”
Optimize available space
Because space can be a premium, managing it fully makes sense, urges DSI’s Loper.
“Unequivocally, the biggest benefit to innovative shelving is its ability to save space,” he noted. “Ever heard of the domino effect? When one tile falls, they all fall. When a shelving system can save a department up to 40% to 50% floor space, this reduces the time spent searching for the inventory. Less time equals better patient care with better outcomes. Saved space also saves the hospital money by removing the need to renovate or move walls to create more space for supplies, equipment, etc. Most hospitals are busting at the seams and can’t find ways to create new space without a renovation or new construction. This bottleneck becomes very costly. The positive domino effect with space savings is reduced cost, quicker retrieval, better organization, increased employee safety, better patient outcomes and a boost to the hospital’s bottom line.”
Cleanliness matters
Cleanliness is by far the most important benefit to shelving and storage design, according to Medline’s Hagedorn.
“In a healthcare setting, avoiding unwanted infections and any potential issues that stem from it is of high priority across the continuum,” he observed. “Proper storage room setups create an organized and clean environment allowing for efficiency and less physical touching of each product. Second to cleanliness would be the ability to alter the storage medium when supply mix changes. As we have seen through supply chain disruptions, there are constant changes to the items that will be stored in the room. Thus, being able to alter the height of shelves, location of items due to increased usage, and/or the ability to move and reposition racking is a vital benefit when it comes to creating a storeroom that has the ability to change with the products it is housing. Along with the ability to alter storage on a need base, health systems traditionally want to maximize the space and utility of a department or room. Creating an individualized and customized storage space not only allows it to change with your need but also maximizes the amount of space that is given. It is important that every square inch of space be used to the fullest to allow the best care.”
Squaring up the cube
Cardinal Health’s Naylor reminds supply chain pros not to overlook quality and service-level issues.
“For customers I’ve interacted with, they often seek to enable key and contractual obligations like service level agreement (SLA) and quality,” he noted. “Having shelving and storage can help maximize the cube within the warehouse, enabling our operations team to meet any contractual obligations around inventory days on hand (DOH). The more density, the more DOH we can store without negatively impacting internal flow or inventory peaks. Additionally, properly segmenting shelving into SKU-specific locations can enable greater inventory accuracy, reducing potential errors. Both attributes help us ensure we can hold sufficient on-hand quantities to support customer demand as well as supply the highest quality standards for inventory accuracy. Our customers expect products on time, with the right SKUs, and in the right quantities—so a warehouse that is flexible with system driven optimization in place helps fulfill the foundation of our contractual obligations and enables optimized picking and fulfillment strategies.”
Flex and control
Space adaptability through flexible sizing for storage can give providers desired inventory control, St. Onge’s Redding insists.
“The most important attribute for shelving is its customization capability to provide multiple storage bins sizes and the flexibility to quickly customize the vertical space within a shelving unit to maximize the use of available space,” he said. “Additionally, having the option to control access while also providing internal customization has further benefits for the right mix of inventory.”
Searching for shelf, space upgraders
Just about everyone probably has an idea or two on how to improve a product or service, shelving and storage being no exception. So Healthcare Purchasing News asked supply chain product and service experts for their notions on how they might improve shelving and storage design, functionality, structure or utility during the next decade and why their suggestions may matter. HPN cautioned them against revealing any production pipeline or trade secrets to concentrate on creative expression instead. Here’s what they shared.
“One important consideration in a season of change is the safety factor for shelving requires robust mechanical fastening, but a strong enough quick-release system for re-configuring would be helpful. From a technology perspective, proliferation of pick to light (a system that uses lights on racks or shelves to indicate pick locations) throughout an entire warehouse could help to improve accuracy of picking. There are more and more creative periphery technologies emerging such as augmented reality (AR) that I see potentially impacting general activity in a warehouse in the future. However, the more a general/standard warehouse can support emerging technologies like autonomous mobile robots (AMR)/autonomous case-handling robots (ACR) and goods-to-person (GTP) from the start can prevent obsolescence and prepare for future capabilities. I see minimizing the change and facility impact associated technology implementation will be a huge future opportunity. A technology that can best leverage existing infrastructure but facilitate greater storage density and throughput specific to fulfillment channels would be exciting to see.”
--Derek Naylor, director, Supply Chain Optimization and Technology, U.S. Medical Products and Distribution, Cardinal Health
“If I could make one improvement to the shelving and storage design, it would include an easy-to-clean function or process. One of the most difficult things is keeping our storage organized, easy to navigate in such a high-paced and highly rigorous environment. We are also tasked with keeping it clean so we can house our inventory safely for patients. Most often, especially with the highly technical storage solutions, there are crevices and small areas that hold dust, dirt and debris and limited cleaning guidance if any. I would like to see materials used that are easy to clean, durable and provide instructions and recommendations on the cleaning protocols for these devices we rely on so heavily. Maybe even a built in HEPA filter system that keeps the internal components dust-free, or a hand-held cleaning device or tool to help us maintain the life of the units.”
--Randalyn Harreld, CRCST, CIS, CER, CHL, C.S.P.D.T, C.A.S.S.P.T, BLS, AAS, clinical education manager-US, BeliMed
“I can imagine the use of artificial intelligence (AI) to support inventory optimization by predicting future demand, storage space adjustments, and safety enhancements.”
--Jennifer Nageotte-Elliott, partner, Diamond Storage Solutions
“Through the years, I have noticed that storage mediums in healthcare have stayed pretty consistent over time due heavily to controlling costs as it is a non-value-added expenditure. I would project that any advancements in the storage medium space would need to come with a serious value-added ROI. To dream, I would say something that has some voice-activated AI capabilities where a nurse or clinical staff member could say what they need, then a robot would pull that item and deliver it to the room they were in and also documenting the item on the patient chart. That would be pretty life-changing in this space. I think this could serve as an important function in efficiency, accuracy and ensuring that storerooms are consistently being stocked at the appropriate level. With anything, there is going to be human error, and in healthcare every second counts. This could save clinical staff time when trying to find a product or ensuring that the product is the correct version of the one they are looking to use.”
--Joseph Hagedorn, senior manager, Supply Chain Optimization, Shelving & Storage, Medline
“Although wire shelving is relatively easy to adjust, I would like to see the ability to adjust the shelves without having to fully remove the shelves from the poles. With the current design, clips that hold the shelves in place must be repositioned after the shelf is removed. Once the clips are repositioned, the shelf is returned to the pole and secured to the clips. If the clips were built into the corners of the shelving, the shelf could be moved in one step.”
--Kurt Baker, consulting director, Vizient
“One improvement I would make to shelving and storage design is to incorporate lighting solutions and voice command technology for clinical and materials management staff to quickly identify where certain products are stocked. Clinical and materials management staff spend a considerable amount of time searching for products within a supply room. The ability to use voice commands and quickly illuminate a product bin could be a tremendous improvement over the existing approach of labeling and color-coding.”
--Tom Redding, senior managing director, Healthcare, St. Onge Co.
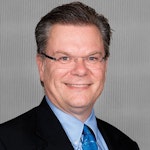
Rick Dana Barlow | Senior Editor
Rick Dana Barlow is Senior Editor for Healthcare Purchasing News, an Endeavor Business Media publication. He can be reached at [email protected].