Solving freight, shipping pain points need not hurt … too much
As healthcare organizations struggle to keep their burgeoning freight and shipping costs in check – whether due to lack of accountability, inability to track and trace, ineffective foresight and planning or even simple emergency needs – suppliers and service providers recognize the frustration and offer myriad solutions to improve workflow, reduce costs, and rescue budgets. Nine executives from eight different distribution and logistics services organizations share their recommendations for what’s possible, based on what they’ve implemented to counter or off-set excessive freight and shipping costs.
“During the pandemic, the vice president of Supply Chain from a major U.S. healthcare system contacted us seeking assistance regarding their lack of visibility into order status. To solve this problem, we developed a Real-Time Inbound Supply Chain Visibility solution. By providing real-time order status updates, clinicians can easily inquire about purchase orders, and the supply chain team can promptly respond. This streamlined workflow improves coordination between clinical operations and supply chain logistics, thereby reducing costs.
“Another obvious headwind emerging from the pandemic is the continued financial strain on health systems. To assist with this, we developed our Analytics and Data Visualization dashboards. These dashboards provide clear visibility into supplier and carrier costs, turnaround times, and fees. Our goal is to help our customers achieve continuous optimization, reducing the risk of disruption, and enabling ongoing cost-savings for their freight programs.
“We’ve also seen a dramatic increase in the volume of outbound shipping, both within the hospital network and to patients’ homes, driven by the expansion of specialty pharmacy services and its positive financial impact on health systems. In response to this trend, we brought a pharmacist on staff to run the product build out for our pharmacy solution. This solution is designed to enable health systems to excel in clinically minded shipping, tracking, and compliance for medication distribution. The integrated workflow we’ve created prioritizes patient safety, clinician satisfaction, and reduces risk of payor clawbacks.
“Finally, in response to the growing number of cybersecurity breaches in the healthcare industry, our engineering team has made significant efforts to obtain our SOC 2 Type 2 certification. This certification is aimed at safeguarding our customers from data breaches, litigation, and regulatory scrutiny. It signifies a major milestone in our ongoing commitment to ensuring strong security measures for our valued customers. Over the past six months, we have seen SOC 2 Type 2 certification progress from a nice-to-have to a must have.”
Derrek Seif, Chief Strategy and Product Officer, VPL
“One way is implementing self-sourced and on-site storage with large number of critical products to counterbalance long lead times and transportation shortages/risks. Pre-pandemic and post-pandemic, it has been critical for us to have the ability to deal with any short-term product shortages and/or longer lead times. Additionally, creating priority relationships with carriers based on being in a critical field (healthcare/medical) has helped keep products moving during peak seasons, such as the end-of-year holiday season, or during extreme weather events.”
Mike DeSimpelaere, vice president, Network Operations, Cardinal Health at-Home Solutions
“The first solution is to simply align with your priorities. When working with a third-party freight management provider, be sure to be transparent and clear on common goals and needs so you can extend the impact of your partnership. The second is leveraging visibility tools. For example, our comprehensive data analytics solution, called TotalVue Insights, helps healthcare supply chain leaders utilize predictive technology and actionable data to monitor and benchmark performance, and identify shipping and freight savings. By combining these solutions – technology and logistics expertise – a third-party freight management provider can translate your priorities into action within your program and ultimately drive long-term value.”
Emily Gallo, general manager and senior vice president, Cardinal Health OptiFreight Logistics
“One example of a countermeasure for freight/shipping is to implement an analytics platform to proactively monitor and assess lead times by product and vendor to inform purchasing decisions.
“AI is going to be a gamechanger for supply chain and logistics. We rely heavily on manual intervention and communication to make decisions where AI will give us the tools to identify, predict and address disruption issues before they actually become a disruption.
“Freight/shipping is highly complicated with many handoffs that inherently create opportunities for delays and service failures. AI will enable the shipping industry to improve its reliability by proactively taking steps to re-route goods to reduce transit time. Additionally, AI will provide a better customer service experience and improved insights into real-time location of goods and expected delivery times. Blockchain has its place for secure data transfer and communication, but it will be a support mechanism for AI.”
Tom Redding, senior managing director, Healthcare Services, St. Onge Co.
“We have implemented [solutions in] multiple optimizations, resulting in numerous successes that have led to cost reductions, labor efficiency, and streamlined operations. For instance, in one system, we achieved substantial savings by integrating the supply chain, laundry/linen and lab deliveries. This allowed us to eliminate a dedicated truck run and provide medical offices with daily service for supplies and linen, while simultaneously reducing storage requirements at the providers' location. In another system, which involved over 1,500 daily stops, we initially achieved just under $100,000 in validated savings through optimization, and subsequently achieved an additional $100,000 in savings through re-routing a year later. We love to clean up messes.”
Mark Speight, COO and partner, Caduceus Medical Logistics
“While the best may be yet to come, advanced analytics and predictive modeling is quickly becoming table stakes. This approach involves analyzing historical data and real-time information to optimize routes, anticipate disruptions, and proactively manage inventory levels. As with any analytics, the quality of data inputs directly influences the reliability of the insights.
“The adoption of radiofrequency identification (RFID) technology has significantly enhanced visibility and traceability within the healthcare supply chain, both in Tecsys-specific use cases and more broadly. By attaching RFID tags to medical products or shipping containers, real-time tracking and monitoring of their movement become possible. Complementing this, IoT devices and sensors capture additional data on environmental conditions like temperature, humidity, and light exposure during the shipping process. These innovative solutions greatly improve supply chain visibility, enabling healthcare organizations to identify and resolve bottlenecks, optimize logistics, and ensure the punctual delivery of vital medical supplies.
“In the long term, these improvements in tracking capabilities lead to more efficient and reliable freight/shipping processes in healthcare. They contribute to streamlined operations, reduced costs, and increased customer satisfaction. By addressing pain points in the freight/shipping industry, these solutions have a significant impact on the overall effectiveness and sustainability of healthcare logistics.”
Cory Turner, CMRP, senior director, Healthcare Strategy & Product Marketing, Tecsys
“With preventable challenges in mind, we recently designed and implemented a fully integrated, customized solution for a large Midwest healthcare organization that serves 14 facilities and more than 3,200 beds.
“We worked with our customer to engineer a highly automated 400,000 square-foot central warehouse for medical devices, pharmaceuticals, and everyday supplies. In addition to recruiting and managing labor, including logistics engineers, operators, and warehouse workers, we installed warehouse automation equipment. AutoStore, an automated storage and retrieval system (ASRS), increases storage capacity and fulfills orders 24 hours a day, continuously feeding 1.3 miles of conveyors and giving the supply chain increased speed and reliability. It also helps mitigate impacts from the warehouse labor shortage.
“Second, we implemented a fully optimized, dedicated outbound transportation network for guaranteed capacity and reliable, on-time deliveries from the distribution center to our customer’s 14 healthcare facilities. This includes customized vehicles, ranging from tractor-trailers to box trucks, and drivers hired and trained by Ryder specifically for the hospital network.
“And we designed the solution around fully engineered, sequenced loads that are powered by Ryder’s warehouse management system (WMS). Orders are picked by low unit of measure and put into totes that are destined to a par location — stock rooms within the hospital system. Through the WMS, each tote is labeled specifically where it is placed on a pallet and where a pallet is placed on the truck. For example, supplies needed for surgeries are on the top of a pallet located at the tail of the trailer. This allows workers who are unloading pallets at the hospital to place those more critical items on the carts for delivery first, instead of items that are not needed immediately.
“We also added Ryder’s proprietary real-time visibility and collaboration technology RyderShare, which provides real-time visibility of inventory anywhere in the supply chain — inbound, outbound, and inside the warehouse. And it gives all stakeholders access to the same information at the same time, so they can easily see across the supply chain, work together to prevent costly delays, and also find efficiency gains.
“The hospital systems receiving the deliveries can also see when the truck will arrive and what inventory is being delivered. So, from the warehouse to the point of delivery at the hospital, everyone knows what is in each delivery, even down to what’s in each tote – and that is a powerful differentiator.
“With Ryder’s fully integrated, customized solution, the hospital network achieved:
• 98% fill rate (up from 90%) within six months of startup
• 99% on-time delivery
• 100% real-time visibility
• 100% inventory control
• Significantly decreased operating and product costs
• Improved patient care by ensuring critical medical supplies are available.”
Norman Brouillette, senior vice president, Supply Chain Solutions, Retail, Tech & Health, Ryder System
“A Proprietary Real-Time Transportation Visibility (RTTV) system enables full transparency by utilizing real-time data from GPS and temperature data loggers. GPS provides real-time alerts for route deviations, unscheduled stops and locational data, such as proximity to pick-up and delivery locations. Temperature-monitoring sensors send real-time alerts for temperature excursions and other deviations in product handling requirements. Alerts are sent to dedicated in-transit security teams so that contingency plans can be executed. This provides immediate access to in-transit temperature history report to the recipient/provider.
“We work closely with a qualified group of carrier partners and their drivers that are audited by our logistics professionals on an annual basis. This enables:
· The consistency and accountability of an asset-based carrier with the flexibility and availability of a domestic transportation third-party logistics (3PL) company.
· Our carriers and their drivers are trained on our proprietary Quality Management System that is aligned with TAPA and GDP guidelines and sets industry leading standards for product security and integrity.
· Our carrier partners install our RTTV equipment on their assets to our specifications.
· We regularly audit our carriers to ensure adherence to our stringent standards for cold chain shipments, products with special handling requirements, and other sensitive time-critical cargo.”
Ron Devitt, founding partner, DeSpir
“The conventional approach to same-day logistics in this industry is point-to-point routing. This means an item goes from Point A to Point B, without any interconnectivity between those points and locations that are part of other routes. Conversely, MedSpeed creates fully integrated networks that physically connect all points of care within a healthcare operation through our hub. Overnight hubbing can allow healthcare entities to share items between locations, which would not otherwise be connected on the same route. Leveraging this connectivity, our customers unlock the immense potential to save significant supply, pharmaceutical, and capital equipment dollars, and ensure nothing goes to waste.
“Regarding labor shortages, MedSpeed operates with an error rate that is 1/20th of the industry average. Dependability means nurses spend less time hunting down missing items and lab professionals get the samples at the right time and temperature for accurate testing. Time saved by these critical clinicians can be spent on their core focus – patient care.”
Jake Crampton, CEO, MedSpeed
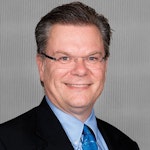
Rick Dana Barlow | Senior Editor
Rick Dana Barlow is Senior Editor for Healthcare Purchasing News, an Endeavor Business Media publication. He can be reached at [email protected].