Freight, shipping issues regroup as post-pandemic logistics strives to drone on, recoup
If anything, the pandemic reshaped and shifted our demands and expectations for freight and shipping services – including the use of automated technologies, such as drones – and showed the strain on distribution, logistics and transportation, areas that most people took for granted until eyes were opened.
Now that we’ve emerged – theoretically – from the pandemic, healthcare organizations – Supply Chain specifically – may want to determine what they’ve learned from the ordeal and how it impacted freight and shipping operations. These generally are overlooked as a granular financial annoyance that can evoke considerable fiscal pain when least desired or expected if routinely left unchecked.
Even as the pandemic subsides, financial and operational aftershocks continue within a global supply chain. Among the bevy of maladies are fuel costs, cargo/container ship reliability, cybersecurity, port access, international tariffs, labor issues, and rail and trucking challenges. Healthcare organizations must be ready to handle and douse them, whether internally or externally through a contracted supplier or service provider.
Counting down
Emily Gallo, general manager and senior vice president, Cardinal Health OptiFreight Logistics, identifies two pain points that cross her company’s radar, which are labor costs and program visibility.
“If a healthcare provider is feeling the impact of labor costs and shortages, consider looking for a freight management partner who can act as an extension of your team, as well as bring technological capabilities to help find efficiencies across your program,” Gallo said. “Technology also plays directly into needing visibility into your supply chain. Without having close to a real-time line of sight of shipments, healthcare providers don’t have the visibility they need into their freight management program, holistically. By leveraging technology to combat the lack of visibility, healthcare providers can proactively plan for any disruptions.”
Some of the basic supply chain issues linger, according to Mike DeSimpelaere, vice president, Network Operations, Cardinal Health at-Home Solutions. He oversees the company’s warehouse operations.
“Overall, in this post-pandemic environment, lead times are still a bit longer than they were pre-pandemic,” he observed. “Ensuring there is additional inventory on hand – either on-site or at the health system – or requiring distribution partners to house more inventory are two ways that can improve lead times. Currently, most systems are pushing for 60-to-90 days of stock for necessity items, such as gowns, gloves, masks, etc.”
Derrek Seif, Chief Strategy and Product Officer, VPL, raises several challenges that the pandemic brought to the forefront, such as cost inflation, labor issues, and even cybersecurity risks, which he emphasizes is essential to address immediately.
“The healthcare industry is a prime target for cyberattacks,” Seif warned. “This is because healthcare organizations collect and store a large amount of sensitive patient data, which can be used for financial gain or to disrupt healthcare operations. Two of the most common cybersecurity challenges for healthcare organizations include outdated technology that is vulnerable to cyberattacks, and third-party vendors who may not have the same level of cybersecurity as the healthcare organization itself. To address these challenges, healthcare organizations need to implement a comprehensive cybersecurity program that includes conducting regular security assessments to identify and address vulnerabilities, and carefully vetting third-party vendors to ensure that they have adequate cybersecurity measures in place. By addressing these challenges, healthcare organizations can help to protect themselves from cyberattacks and keep patient data safe.”
Seif targets fuel costs as particularly problematic, too. In fact, to better understand the impact of inflation, VPL analyzed more than 20 million healthcare shipments across multiple carriers using its Data Analytics and Visualization software, he notes. “Since 2019, national carriers have seen an increase in fuel costs between 167% and 241%. Overall, the average fuel surcharge cost has risen by 160% in the last five years. Furthermore, our data shows the average cost of shipment has increased up to 89%. These insights highlight the substantial effects of inflation on fuel costs and average shipment expenses, emphasizing the importance of using data-driven solutions to help get visibility into these charges to optimize cost efficiency and improve budget decision making,” he added.
Seif also lists burgeoning workforce challenges, including staff shortages, issues related to employee retention and turnover, skill gaps, and the prevalence of workforce burnout.
“A study we conducted a few years ago revealed that a simple phone call from a buyer to a supplier, inquiring about shipment status, took an average of over 20 minutes,” he indicated. “We found that buyers may spend 50% or more of their day tracking down shipment statuses, while clinical staff may allocate 10% or more of their day to the same task. One of our customers conducted an internal study that found it costs $45 to track and trace a shipment for a purchase order. The cost impact is high. A health system that processes 120,000 purchase orders (POs) per year could be spending $5.4 million worth of time chasing down the status of the order. These pain points highlight the urgent need for improved processes and solutions in healthcare logistics – such as real-time visibility into order status and automating mundane tasks.”
Addressing the Achilles heel
Mark Speight, COO and partner, Caduceus Medical Logistics, quotes British World War II Gen. Omar Bradley as having the proper mindset. “Amateurs talk strategy. Professionals talk logistics,” he reiterated and also declares that “fuel and labor costs are skyrocketing.”
Consequently, healthcare organizations should refocus internally.
“Healthcare providers should consider performing periodic system-wide assessments of same-day delivery needs and then optimize the requirements using computerized multi-constraint optimization,” Speight advised. “Candidly, the initial assessment can be a time-consuming and daunting task, as each delivery requirement must be thoroughly understood and documented to ensure effective optimization. Minutes matter, doors lock, overtime accumulates. However, when executed correctly, we have observed savings of up to 10% through consolidation and reduced resource utilization. Subsequent quarterly or biannual optimization is indicated to combat bloat increase operational efficiency and, in collaboration with providers, seek creative solutions.”
Tom Redding, senior managing director, Healthcare Services, St. Onge Co., warns about what healthcare providers and supply chain don’t see.
“Healthcare providers have many blind spots (e.g., shipping visibility, track and trace, regulatory compliance, temperature monitoring, etc.) when it comes to the ever-complex web of moving materials from the manufacturer to the point of use,” Redding indicated. “As we all experience on a daily basis, shipping is the Achilles heel to effectively running an operation. Healthcare providers are no different and are spending considerable resources to address disruptions in deliveries. For example, some healthcare providers are building stronger relationships with their suppliers to drive better visibility to lead times and where products are manufacturers to anticipate potential shipping disruptions. Until healthcare providers shift from being a customer to being a partner, shipping visibility will be limited.”
Relying on third-party shipping companies has its pros and cons when it comes to buffering demand variability and minimizing disruption for the supply chain, according to Redding. “In short, it could increase costs and create more complexity, but it does offer significant benefits for organizations that don’t have the scale to ‘buffer’ inventory on their own to minimize disruptions in manufacturing and/or transportation.”
Even in a “post-pandemic” environment, healthcare providers will continue to encounter freight/shipping challenges that may jeopardize access to goods and services and will need to be thoughtful about building in contingencies where they can, insists Cory Turner, CMRP, senior director, Healthcare Strategy & Product Marketing, Tecsys. “In our work with health systems, establishing a consolidated service center (CSC) is an important part of solving for that, as it provides a greater degree of flexibility needed to navigate disruptions in the flow of goods,” he indicated. “By centralizing resource allocation, optimizing the network and enabling real-time visibility, a CSC empowers healthcare providers to adapt and respond efficiently, accommodating spot shortages to essential goods and services, even under challenging circumstances.”
Making haste against waste
While the pandemic may officially be over, Jake Crampton, CEO, MedSpeed, still sees its lasting impact reverberating through the industry, leaving behind profound aftershocks.
“In the face of ongoing supply chain shortages and constrained budgets, healthcare executives have prioritized waste reduction more than ever before,” he observed. “Nothing can afford to go to waste. The significance of logistics has always been paramount for maintaining agility, but in these critical times, it has become absolutely imperative to facilitate the sharing of limited resources among facilities, encompassing supplies, pharmaceuticals, and equipment.”
Labor shortages remain problematic, too, especially among the clinical set, according to Crampton.
“With nurses in short supply, and more leaving the profession every day, helping clinicians to operate at the top of their license is critical,” he said. “According to a recent American Nurse survey, 87% said that medical courier deliveries — or lack thereof — impacted their work weekly. Those findings were echoed in another recent survey from CAP Today, which found 86% of lab professionals were unable to provide timely and accurate results for patients at least once a month due to courier issues. An efficient and reliable logistics infrastructure is necessary to weather the labor shortage storm.”
Three preventable or mitigable challenges facing healthcare organizations come to the mind of Norman Brouillette, senior vice president, Supply Chain Solutions, Retail, Tech & Health, Ryder System. They are “the lack of visibility across the supply chain, the need for guaranteed truck capacity with professional drivers with track records for dependable, on-time deliveries, and impacts of the worsening warehouse labor shortage,” he said.
Ron Devitt, founding partner, DeSpir, singles out the transportation sector as key, particularly among haulers.
“In the trucking space, in-transit risks to the safety and integrity of pharmaceutical and other products that impact the lives and wellbeing of patients remain the highest priority,” he said. “Healthcare providers must be absolutely certain that the medicines and therapies they administer have not been compromised in any way. They count on pharmaceutical shippers to have processes in place that enable real-time reporting and monitoring to confirm that the product’s integrity has remained in compliance throughout its journey. They need to be informed of potential in-transit issues in real-time. This enables shippers to immediately respond to loss or delays in a proactive versus reactive way.”
Devitt contends that in-transit monitoring and Real-Time Transportation Visibility (RTTV) provide critical and actionable information in several key areas:
- Alerts about seals or locks that have been broken and tampered with, as these breaches can compromise the product and patient safety.
- Real-time alerts about temperature excursions, drivers veering off pre-planned transit routes and other triggering events, and arming shippers and receivers alike to put their back-up plan into action. This could include when and how to offer alternative expedited shipping modes and plans for immediately shipping replacements for compromised product(s) through qualified carriers and drivers that follow stringent protocols and provide real-time updates. Having plans for immediate access to expedited services for lifesaving medicine also applies to highly demanded products that are pushed through as quickly as possible, and expediting ground shipments for life science products that have been delayed due to ocean ship delays, which have continued to be problematic in the post-pandemic era.
“Healthcare logistics professionals will benefit by taking advantage of real-time technologies that enhance accountability, monitor and protect product integrity, and enable faster, more proactive responses when things go wrong,” he concluded.
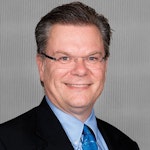
Rick Dana Barlow | Senior Editor
Rick Dana Barlow is Senior Editor for Healthcare Purchasing News, an Endeavor Business Media publication. He can be reached at [email protected].