Racked and stacked: Shelving, storage options keep supply chain on track
Shelving and storage serve as the bones, if not the entire skeleton, of a storeroom or warehouse, which represents the bulwark of a healthcare organization’s operational success.
For that reason alone, Supply Chain leaders and professionals must have a set-up that facilitates efficient workflow and pair it with effective service to clinicians and administrators in support of patient care and customer service.
While on paper, that aim may make sense, but in practice, it requires considerable design and fiscal resources to establish and implement, sources tell Healthcare Purchasing News.
Expanding outward and upward may seem to be the most obvious tactics when arranging and designing a storage footprint, but from a strategic standpoint, maximizing and optimizing available space – as in maneuvering shelving configurations within existing space – makes a realistic difference.
“When DSI thinks of efficiency we think of the people working in the department, the processes to retrieve and put away the supplies and the storage equipment being used in the department,” said Vice President Ian Loper. “It seems the most successful hospitals in the country are not only the most well-regarded by the patient community, but they are also very good operators when it comes to maximizing the efficiency of their people, the effectiveness of their processes and the adoption of specialized storage equipment throughout their facility. Capital equipment is sometimes an afterthought during the planning process of a renovation or new construction project, and this presents an opportunity for hospitals to become better. Conventional wire shelving is designed for a one-size-fits-all scenario and that leaves room for wasted space between supplies. A few inches lost here and there quite often becomes thousands of square feet lost.”
Tim Ramcoobeer, sales development representative, H+H System Inc., calls space one of the “most valuable commodities within a warehouse” that must be maximized whenever possible.
“Doing so can vastly improve efficiency and output to levels previously thought to be unattainable,” he noted. “Unfortunately, it’s not uncommon for facilities to (unknowingly) implement storage options that waste space and adversely impact workflow. Even the most powerful teams can realize operation deficiencies if their storage options don’t adequately support their work processes. We often don’t realize how much ‘dead space’ generic storage options waste and lock us into.”
Ramcoobeer encourages the use of multiple sub-divisible bins, modular configurations and bar-code labeling to facilitate quick access and reordering, which can lead to “less time spent stocking, picking and searching for inventory, affording teams more time for other valuable functions and contributing to overall efficiency.”
For David Phillips, marketing manager, Hänel Storage Systems, the prospect of designing shelving configurations should be looking up.
“Existing space can easily be optimized by storing vertically,” he insisted. “The next time you’re in your storage area, take a good look around. Is there much space between shelves, or are the shelves so tightly packed that you can barely remove what you need? Is there empty space above the rack itself? Is there room to reposition the racks to find the items you’re looking for? You need to store vital supplies, not air. Everything you see can be condensed into unused overhead space, with several racks consolidated into a single, smaller footprint. By introducing automated vertical storage, less space is needed for storage, and you can find other uses for that newly vacated area.”
Using a vertical carousel, supply chain operators can press a button to bring the items directly to them, according to Phillips. “The need to reach for and lift supplies is virtually eliminated, and stored items are much easier to access,” he indicated. “Hänel’s Rotomat also helps reduce the time it takes for staff to find what they’re looking for, because no one needs to hunt throughout the storeroom. No distractions or frustrations and less time spent searching for supplies means the staff can focus on their main tasks and become much more productive.”
Equipment options matter, too, because they can provide needed flexibility and modularity, according to Dave Salus, healthcare market manager, InterMetro Industries Corp., which makes available to healthcare organization customers high-density shelving, s-hooks, “EZ-ADD” shelves and computerized design applications to customize planning.
Salus sees high-density track shelving molded in chrome, epoxy and polymer as a solution for larger spaces. “Each unit has the potential to create as much as 50% more storage when added to your storeroom or warehouse design by placing more physical units in limited floor space,” he noted. “Track shelves include ‘active isles’ with sliding mobile units that move to access materials with ease. Tracks can be installed on top of the unit or the floor.”
S-hooks can be used for corner storage space. “S-hooks eliminate the posts in the front of corner shelving units that block access to shelving space in corners,” Salus added.
InterMetro’s “EZ-ADD” shelves enable supply chain staff to add and remove shelves without having to take apart the previously built shelving unit, according to Salus. “EZ-ADD shelves are placed with a specially designed connector that can be easily clipped and moved to wherever you need a shelf without tools,” he indicated. “This is a great solution to continuously eliminate wasted space in supply rooms that are consistently changing.”
InterMetro also offers multiple design tools – one for shelf design, one for room design and one for track shelving design – via the company website to help healthcare organizations customize their space. “These tools offer the ability to create 3-D models of your storage solutions and to view them in the room with the [augmented reality] feature,” Salus said.
Remote care rescue
If hospitals struggle for enough storage space for inventory, think about how smaller non-acute facilities fare, according to Brian Hazelwood, marketing manager, Midmark Corp.
“It’s no secret that primary care facilities are challenged with inadequate storage space,” he observed. “Many non-acute facilities have limited storage space depending on the size and configuration of the exam rooms, which can often have a negative impact on patient and caregiver experience as well as the quality of care delivered.
“There are many reasons for the shortage of storage space,” Hazelwood continued. “Sometimes storage is not a major consideration during the design phase, or the facility was not originally designed to handle continued growth and increased patient volume. Cabinetry and storage solutions oftentimes aren’t designed for the medical environment and a changing patient and provider demographic that may interact with the space and equipment in a much different way.”
That’s why Midmark focuses on ways storage equipment can be more accessible, efficient and standardized, bringing supplies closer to the point of care and maximizing floor space to help improve clinical workflow, according to Hazelwood.
Midmark studied numerous healthcare facilities across the U.S. to identify elements that were missing from much of the current cabinetry used in clinical environments and compared the findings to Bureau of Labor Statistics data that report 76% of healthcare workers are female and that the average height of females tops out at five feet four inches, according to the Centers for Disease Control and Prevention.
“We found that the typical cabinetry used in clinical environments was not designed for people of that height,” Hazelwood said. “In many instances, they need to use stools or other devices to see or reach supplies on upper shelves of cabinetry. Therefore, the upper shelves often go unused. We worked closely with healthcare staff, infection prevention specialists and ergonomics experts to design a line of wall-hung cabinetry that can improve ergonomic reach and visibility while helping enhance storage efficiency and support infection prevention.”
As a result, Midmark’s latest line of cabinetry “features base and tall cabinets that better position the most-used areas of storage for easier reach by physicians and staff,” Hazelwood described. “The lower upper height and thinner depth of the cabinets improve access to storage with less reach and lean required. The use of gravity-fed, angled flow shelving improves visibility and access to supplies, even for items stored toward the back of the cabinet.” And they can be configured for exam rooms, he added.
Don’t fear simplicity
Ed Granger, Director of Sales, Quantum Storage Systems, cautions supply chain professionals against believing that shelving and storage systems must be automated and elaborate to be effective and efficient. [See sidebar "Unsophisticated utilitarianism may be just right for you" below.]
“Quantum’s products are not sexy or sophisticated,” he said. “Nothing is motorized, no hydraulics, no automation. Quantum’s products are, however, utilized around the world in healthcare facilities. While our products are not sophisticated, they are efficient and effective at a relatively low cost compared to more elaborate systems. Do healthcare facilities want more elaborate and sophisticated items? Yes. But do they have the budget to buy those items? Quantum often becomes the best use of budgetary funds that allows healthcare facilities to operate efficiently and within their budget means.”
Bottom line? Concentrate on proper labeling and storage unit mobility with plastic bins and wire shelving carts for a closed loop system, Granger advises.
“Proper labeling makes products much easier to identify,” he said. “Gone are the issues of searching to find products. Products seem to either up and move on their own, or more likely are not put back in the registered space by a hospital employee. At Quantum Storage Systems we offer shelf labels and bin labels that assist hospital employees find and return products to an identified area. We also can help product identification by using color coding of storage bins.
“When storage systems are mobile – basic wire racks on wheels – an entire cart full of products can be moved throughout the facility either delivering or retrieving products to where they are needed most,” he continued. Mobile wire racks hold as much as 1,200 pounds and roll through the hallways quietly to go unnoticed and to not disturb patients or hospital staff.”
Shelving affects more than storage
Craig Crock, president, Southwest Solutions Group Inc., contends the secret to optimizing shelving and storage space involves the capability of doing more with fewer people and less space.
“Everything you see is adjustable, modular, moveable to the next space, not built in, and is what everybody is moving towards to store more in less space and allow quick access to what is needed to serve the patient,” he told HPN.
Crock highlights how shelving and storage can be configured by department and function.
For example, pharmacy tends to use shelving with gravity-feed and rear-loading capabilities to reinforce first-in/first-out (FIFO) consumption patterns. “This allows for a higher density of meds in the same floor space and allows fast access to everything,” he said. Gravity-feed or gravity-flow shelves are tilted at an angle toward the end user so that when someone removes an item the rest move forward and closer.
In the sterile core of Central Sterile Supply, staff can use an automated vertical carousel storage system or a compression storage system to facilitate access to surgical supplies to build cases and sets for the Operating Room (OR). “Within these rotating Ferris wheels, the units rotate around and use lights to show [staffers] what items to pick for surgical sets,” he said.
“Compression systems are floating aisles where the shelves sit on rails and can be moved along by turning a wheel on the side,” Crock explained. “The shelves spread apart to make aisles.”
Carousels and compression systems also make sense for shelving and storage for the laboratory, pathology and histology for storing lab specimens, DNA samples, glass slides and paraffin blocks even in refrigerated space, according to Crock. Further, when labs use an automated slide-sorting and block-filing system, they can reduce the amount of time and number of people doing the task as well as increase accuracy and productivity, he adds. Crock cites one customer that employed four people to sort, store and track three million samples and specimens on slides each year. By using an automated system, they were able to do it 60% percent faster and “reallocated three of the people to do something more productive with their time,” he recalled. The key is more effective and efficient use of labor, space and time, he adds.
For materials management in the warehouse, Supply Chain can use mobile pallet rack systems or automated picking carousels to reduce square footage requirements and allow faster access to items to do more with less space and fewer people, according to Crock. “You eliminate wasted aisle space and move bins to people rather than people to bins,” he noted.
Meanwhile, in the medical supply rooms staffers can use radiofrequency identification (RFID) with the two-bin Kanban system to link with order fulfillment in the warehouse, which can “eliminate stockouts, expired product and actually can reduce inventory,” Crock noted. “We did a recent project where a hospital had almost $2 million in losses for expired product, and we virtually eliminated that and the savings went back to the hospital,” he said.
Randalyn Walters, clinical education manager-US, Belimed Inc., laments the lack of priority given to storage strategies and tactics during construction or renovations, and that can prove dangerous.
“Storage and shelving options in healthcare, supply chain and surgical operations are often not given the attentiveness they deserve during the planning phases of a project,” Walters said. “Simply waiting until it is too late to determine the type of storage or the amount of size necessary can result in bottlenecks and unsafe conditions. Sometimes a stainless-steel rack is thought to be the end-all-be-all sterile storage, but why is that? With so many innovative products on the market I have found it to be extremely successful in coordinating the storage solution with inventory placed there and including a variety of options for just one department’s needs.”
Unsophisticated utilitarianism may be just right for you
Simplicity simply reinforces choice to go down to the wire
When healthcare organization leaders conjure up images of effectively and efficiently managed shelving and storage areas they likely envision automated high-tech enterprises with conveyor belts, robotic arms, vertical carousels and eyeglass-mounted, hand-held and wrist-worn computers.
But Ed Granger, director of sales, Quantam Storage Systems, insists there's nothing wrong with keeping things simple and embracing efficiency and effectiveness without being elaborate.
Simplicity may seem the obvious answer to budget and resource challenges, but it can go deeper than that, according to Granger.
“The traditional wire shelving is desirable because it is very durable,” he said. “Quite literally, it can last a lifetime if taken care of. Also, this shelving style can handle a lot of weight per shelf – 1,000 pounds 48 inches in shelf length – so the units can really store a lot of products. The different shelving brands are interchangeable with each other, so purchasing agents are not beholden to one brand. During COVID, inventory was scarce and whichever supplier had inventory on hand won the order for new shelving. If the brands were incompatible, a buyer would likely have had to wait for one particular brand to come available.”
Sometimes, simplicity also serves as a metaphor for crawling and then walking before you run, ride something or drive, Granger agrees.
“The traditional efficient and effective shelving is easier to locate and purchase and carries a much shorter lead time,” he indicated. “Some of the more sophisticated storage systems have much longer lead times and are often out of stock, as they are only made upon order. Traditional efficient and effective wire shelving is relatively maintenance-free and will only fail if the product is severely overloaded or abused. More elaborate storage systems that may contain hydraulics, a rotating shelf system powered by a small motor or contain any kind of electronics are susceptible to breakdowns and expensive maintenance calls to keep them working.”
Craig Crock, president, Southwest Solutions Group Inc., recognizes and understands the appeal and desire for simplicity that eventually can be updated or upgraded with some type of software later.
Much depends on the racks facilities buy, according to Crock. “You want something where you are utilizing your space effectively,” he noted. “If you walk into typical supply rooms or a lot of locations, you will see they use a wire shelving unit with a lot of airspace and are wasting storage space. You have to have channels that are adjustable to tighten the space.”
Crock advocates the two-bin Kanban system as organized simplicity. Kanban, which is a Lean Six Sigma concept and is a Japanese word for signal, calls for you to separate the PAR stock into two quantities – a group of products in the front and a group in the back, he explains. The inventory tech or nurse will pull from the group in the front, called the active compartment. Once that compartment is empty, they will move the group in the back, called the back-up compartment to the front, which simultaneously sends a signal to reorder stock.
“What this does is allow rotation of stock so they eliminate expired product,” Crock noted. “You would not believe how much money some hospitals [lose] on an annual basis from expired product. One hospital customer [expensed] nearly $2 million.”
Hospitals can add some technology to this process if they wanted, Crock encourages.
“Technology gives you the ability to understand the turn on your inventory,” Crock said. “We implemented something with a hospital that not only allowed them to eliminate millions of dollars of expired product but also when they ran their data they noticed they never used certain products that often so they adjusted their inventory level down.”
What did Crock’s team do for the hospital that used the 2-bin Kanban system manually? They added a radiofrequency identification (RFID) tag to the bottom of the back-up compartment so that when the active compartment was emptied and the contents of the back-up compartment were moved forward it triggered the RFID tag to send a reorder/replenish alert to the warehouse to restock.
One side benefit to this process is that it generates confidence in the system, according to Crock.
“Nurses may not have confidence in the system, so they’ll take a few of these things extra and put them in their locker or desk drawer,” he said. My daughter-in-law is a nurse and I asked her if she hid stuff. She said yes because she didn’t have confidence in their system. They were always running out of this or that. She at least had a backup because if she didn’t have the backup she’d have to call down to the warehouse and central supply and tell them that they’re out of something. Then they’d have to run somebody over to get and deliver it. That takes time. Meanwhile, there’s a patient that needs the product. With this system, however, nurses have confidence because they know something already is on order.”
If hospitals didn’t want to invest in new bins or other equipment there is software that they can attach to their existing wire shelving and plastic bins to implement and use their existing bar-code system, he assures. Other options include investing in a “Scan & Restock” mobile app, affixing tags to bins that must be pressed each time product is removed or installing “smart weighing” bins that contain built-in scales that send a replenish signal once a minimum weight has been reached, he describes.
“Right now, materials management in these warehouses are going up to the rooms and using hand-helds that read bar codes for counting,” he noted. “They might have 200 or 300 rooms to do. This can be a series of all-day events. It’s wasted labor. By implementing technology, you typically have a return on investment pretty rapidly because people are doing something else. They’re not up in these rooms counting.”
Handling space shrinkage creatively even with steady supply volume
Much may be discussed and explored about how to maximize and optimize additional space for storage during construction or renovation, but the flip side can be equally as challenging, if not more.
What happens when storeroom or warehouse space is reduced so that the space can be converted to more “revenue-generating” programs that run parallel to expected operational expense cutting? What kind of flexibility can be built into shelving and storage systems to meet daily demands, whether they soar, peak, remain steady or wane unexpectedly?
Seven storage system executives share their thoughts with Healthcare Purchasing News.
“Most of DSI’s storage products are customer-configured or custom-designed. Our project managers conduct an onsite storage assessment and space evaluation to determine a storage system that best solves the departmental needs. Space is always at a premium inside a hospital, especially in the OR suites, OR core, Sterile Processing departments and supply closets. More often than not these rooms are busting at the seams with inventory, equipment and people, and the only way to create new space is to implement a space-efficient, high-density storage system that is custom-designed and configured based on the cubic space, flow and the size of the inventory.”
Ian Loper, vice president, DSI
“One option often overlooked is how mobile furniture can be used to help increase storage space in non-acute environments and bring much-needed supplies closer to the point of care. These solutions can be especially important for surgical centers and those primary care facilities wanting to introduce procedures to the environment.
“Mobile workstations that support the use of computers and laptops, allow clinicians to make the most of their space while maintaining their focus on the patient, helping keep patient experience and interaction top of mind as opportunities for efficiency gains are considered and implemented. The mobility aspect of these workstations provides flexibility to easily customize rooms and take space-saving measures. Mobile workstations can be easily moved from room to room or within the room to meet the needs of the provider and the patient and bring technology securely to the point of care.
“Mobile procedure carts are designed to assist in supply access and storage within the exam room, as well as support room-to-room procedure work and prep. They also serve as an additional work surface positioned left or right of the caregiver and can be customized for specific workflows and procedures. Through a number of optional features, including storage racks, glove holders and mounting accessories, mobile procedure carts can be designed to support various clinical workflows and maximize storage.
“Mobile treatment cabinets are designed to bring supplies and instruments to the care zone, minimizing the need for the provider to move away from the patient and acting as a central hub for specific tasks at the point of care. Specialized designs help eliminate dead space and improve organization. When it is not in use, the mobile cabinet can be easily stored out of the way. Multiple sizes, drawer/door configurations and accessories help create an effective supply storage option without detracting from valuable floor space at the point of care.”
Brian Hazelwood, marketing manager, Midmark
“When workflow demands quickly expand and condense, as we’ve seen during the COVID-19 pandemic, it’s clear we need to employ creative solutions to keep up with these strenuous, albeit necessary, changes. Failing to do so will ultimately lead to deficiencies and sacrifices in efficiency, and ultimately, patient care. We solve this problem by bringing flexible solutions to the market. Our FlexShelf system not only can be adapted to support processes including bulk inventory storage, picking and workstations, but also can easily be scaled up or down to keep pace with users’ capacity demands. We take flexibility one step further by allowing our modular components to be effortlessly swapped out to adapt to our customers’ ever-changing needs. What was once an open-shelving tower used to store large items, can now be used to store and pick small inventory within our sub-divisible FlexModul bins — all within seconds and without the use of tools. Our solutions accomplish all of this, while saving 30% space, affording our customers the ability to accommodate other valuable equipment and resources.”
Tim Ramcoobeer, sales development representative, H+H System Inc.
“When storeroom space shrinks, automation can help. Automation enables high-density storage, which optimizes every square inch of storage space into a smaller footprint without taking the expensive step of expanding the storeroom horizontally. An automated solution like Hänel’s Rotomat Vertical Carousel has software that monitors supply quantities to reduce overstocks, shortages and loss of expired inventory. It can manage inventory by expiration date, first-in/first-out [FIFO], PAR level and many other methods. Prior to the COVID-19 pandemic, many hospitals operated on a ‘just-in-time’ basis, in which very little excess inventory was kept on hand. That method is intended to reduce waste and purchasing costs and saves a lot of time. However, when the world came to a standstill because of the lockdowns caused by the pandemic, local suppliers often failed to provide supplies on time, and hospitals were left with dwindling supplies. Remember when PPE was hard to find? This type of inventory system is inadequate now since only minimal quantities are stocked. On the contrary, a ‘just-in-case’ method means that a large stock of inventory is available at all times. Management of that excess stock can easily be done with a Rotomat because it tracks supplies at all levels, allows the continual assessment of inventory and dispenses the oldest supplies first.”
David Phillips, marketing manager, Hänel Storage Systems
“There are many ways to readjust storage spaces as needs change. Metro offers a variety of options to help you make the most of space even as it shrinks.
“EZ-ADD shelves offer a great solution to changing storage spaces. EZ-ADD shelves can add a shelf to any unit without tools and without taking apart shelving units. Having this solution on hand allows you to adjust full storage rooms without having to disassemble shelving units to accommodate more supplies.
“For everyday changes, Super Adjustable Super Erecta and qwikSLOT shelving offers the ability to adjust full shelving units easily and without tools. Super Adjustable Super Erecta includes levers that, when pulled, allow you to readjust the shelves to your ever-changing storage needs. QwikSLOT shelves are a favorite solution for regularly changing environments. These shelves can be slanted to grant easy access to supplies on upper shelves. The shelves can also be moved in one-inch increments or removed without tools to create space for taller/bulkier items.
“Another great way to handle regularly changing storage environments is investing in mobile shelving units. A shelving system that can be moved and adjusted as needs change can make the transition of storage space layouts or moving to a different storage location easier.”
Dave Salus, healthcare market manager, InterMetro Industries Corp.
“Quantum has several solutions to help increase storage capacity in defined room areas through use of empty wall space, reconfiguring current shelving or providing new shelving with more levels and introducing a live aisle system to reduce aisle space.
“Quantum has discovered that empty wall space is prevalent in many storage areas, and many staff workers do not understand the space they are failing to utilize. Quantum has several different wall mounted systems that can double their linear square footage of storage space. Wall storage should be set at a height whereby the products can easily be accessed by the healthcare staff. Once mounted to the wall, the storage system is fixed and not easily removable.
“Often storerooms or warehouses are not maximizing shelf space – meaning there is far too much unused space in between shelves. If/when there is unused storage space, the products can be reconfigured to maximize each shelf level. This often leads to adding additional shelves on to the same unit, thus providing more available storage space. While Quantum’s products are relatively basic, they do match up well for [two-bin] Kanban. Each individual facility – or even different rooms within a facility – will have a different workflow based on the defined space, the access points and the nature of the products that are stored. Workflow tends to change frequently as the facility tries to perfect their best individual method. Having mobile storage units allows the facility to change its storage footprint quickly and easily until they find the best workflow.
“Quantum’s floor track system – or live aisle system – is a collection of storage units that are affixed on a track that is on the floor. This system reduces the number of aisles used in a specific space down to only one aisle. That aisle simply floats from one section to another by moving the shelving row left or right so that the empty aisle can be placed exactly where it is needed so products to be selected by the staff member. This system increases storage by as much as 40% by reducing the number of aisles.
“Lastly, by keeping storage systems mobile, units can be moved throughout the facility to where they are needed most. Why buy more storage units for one room when another room is not utilizing all the storage units within its area? Stationary storage units can be very difficult to break down and move. Often these units are attached to the floor and cannot be moved at all. Mobile storage allows a facility to ‘flex’ units from one area to another quickly and easily. Floor tracks can be wiped down and cleaned. Quantum also offers top-track systems if this is preferred. The top-track system is the same concept as the floor-track system. Floor-track systems are the second generation of the top-track concept.”
Ed Granger, director of sales, Quantum Storage Systems
“With automated picking and space-saving ideas you can actually increase your productivity by three to four times and save space. When you design a building, you can reduce the footprint of that warehouse and accomplish the same thing.”
Craig Crock, president, Southwest Solutions Group Inc.
Shelving, storage require higher attention, priority than afterthought
Randalyn Walters, clinical education manager-US, Belimed Inc., furrows her brow with the understanding that healthcare organizations tend to give short-shrift to shelving and storage considerations during construction and renovation projects.
Just like supply chain executives and equipment planners who argue they should be tapped for their experience and knowledge before the planning phase begins lest doorways, footprints and wall space, among other concerns, be erroneously designed and sized for what’s needed for proper workflow, Walters thinks more consideration should be given to shelving and storage issues.
Walters offers a multistep plan for any organization looking to build new, renovate or upgrade existing space.
First, identify what it is you are planning to store: Supplies, sterile packages, rigid containers, or instrumentation. “This will help you determine what type of material you will require and the size necessary to create an efficient and safe working environment for the team,” she advised. “There are a variety of materials out there and it is important to understand the environmental controls in the space you will be storing. For example, wood particulate and wood would not be ideal for sterile storage or even warehouse operations but might be utilized in a smaller care facility.
“The ideal material for sterile storage of central supply would be a surface that is wipeable, cleanable and easy to label,” she continued. “The material make-up should also be durable enough to last and hold up in the environment you are using it in. Are staff members in need of storing both heavy and light items? Confirming the material is designed to hold up in the environment you are placing it will determine the life span of the shelf as well as the time it will take to maintain, repair, cost to replace and ability of staff to upkeep the shelves during regular operations.
Second, implement a solution that is ergonomically friendly and efficient for your workspace. “I have found it beneficial to implement a storage solution that offers an expansion capability,” she indicated. “High-density storage options typically include mobile shelves and cabinets or bins that are customizable. The key benefits of this type of storage are reducing worker fatigue, longer operational lifespans and the ability to fit more items into a constricted space. Having a high-density storage solution that helps you to maximize your space is of key importance. Using high-density storage for a variety of sized items gives healthcare facilities the option to store multiple items in once place and the ability to customize each row and column to fit their unique needs.”
When storing sterile supplies, devices or sterilized packs, having a specific storage solution that allows for single shelf storage is also a key component of successful sterilized packs with no damage or break in sterility. “Because there is not any ‘standard’ set sizes every department has to accommodate trays that vary anywhere from two inches to 12 inches tall,” Walters noted. “In sterile processing we experience auditors/surveyors pushing us to have a space that allows for ending the stacking of polypropylene wraps and avoidance of holes in single processed goods. This is when the single-shelf storage solution can come in handy, as well as the no-touch method.”
Having sterile storage that allows for transport trays to move from point of assembly, through sterilization and to their dedicated shelf allows for compliance with minimal touching. “Every department should have a variety of options available because not one possibility is good for all types of storage,” she said. “It is important to eliminate wasted space by having solutions that are moveable as well as interchangeable. In my experience, we have spent time collecting data around how many times things are moved to and from a shelf to determine their best location. Sometimes the location of items may not be satisfactory over long periods of time, so when those products are changed out with different products you want to be able to move your shelving around and re-align it to accommodate your needs.
“The non-sterile back-up stock of clean surgical instruments should be kept out of open environments with some form of covering so dust, dirt and debris does not contaminate these items before placing them into a set for sterilization,” she said. “Back-up inventory storage should also allow for easy-to-use, easy-to-label, and easy-to-clean access. If you have limited space, and a lot of growth potential, the best option for this is an automated product that rotates and allows for vertical growth along with rotating shelves inside the unit. These automated storage solutions can provide a much larger capacity with smaller footprint of floor space but are on the top end of cost. These are best when budgeted for and for much larger warehouses, or projects.”
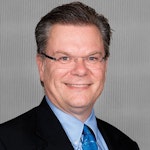
Rick Dana Barlow | Senior Editor
Rick Dana Barlow is Senior Editor for Healthcare Purchasing News, an Endeavor Business Media publication. He can be reached at [email protected].