What cart, workstation improvements would you make?
Healthcare Purchasing News asked executives at more than a half-dozen of the leading cart and workstation manufacturers how they might make one or two improvements to their products for either design, functionality, structure or utility. Here’s what they shared.
“The ideal cart would not require a nurse to unlock, bend down, open and close drawers, relock, clean the cart or even restock. Automation will one day be inexpensive enough to sense the nurse’s presence to unlock, listen to the nurse’s need, raise the drawer to an appropriate height, open and allow the nurse to retrieve the needed item… or maybe just have that item be delivered to the top of the cart. The cart would sense what item was removed and place a replenishment order. [Ultraviolet light] or other technology would sweep the cart after each use to maintain its cleanliness. All of this would reduce the amount of non-clinical activity a nurse performs today, creating more time and focus for the patient. While it may be some time for this perfect cart to come to fruition, Metro has taken strides in this direction. Our electronic locks can accept the nurse’s badge, eliminating the hassle of remembering a PIN or pressing a lot of digits. The cart will also automatically lock when it senses no activity. The cart even contains Microban antimicrobial product protection, which works 24/7 to keep the cart cleaner in between cleanings. Our goal is to continue advancing with features that increase productivity.”
Dave Salus, Market Manager, Healthcare Division, InterMetro Industries Corp.
“Mobile carts and workstations with power-assisted movement could further assist in reducing fatigue and increasing the efficiency of frontline staff. This technology has not been an affordable option in outpatient clinics. However, it is becoming a more economical option over time.
“Some new carts and workstations also have fewer gaps around the drawers to help improve infection prevention and are built using materials that do not break down from the frequent, rigorous cleaning and disinfecting now required in the wake of COVID-19. On some carts, the easy access storage areas are left susceptible to airborne viruses and bacteria. Equipment that is designed for use in the clinical space should help improve efficiency and safety without sacrificing infection prevention. Manufacturers who produce medical-grade equipment are better positioned to understand the needs of the clinical setting when designing products such as mobile carts and workstations.”
Brian Hazelwood, Marketing Manager, Midmark
“What the pandemic has done is implemented much more stringent and frequent cleaning schedules for these workstations. On the extreme end, we have seen they must be wiped down and cleaned after each entry and exit of a patient room. This means the materials used in construction need to be durable and withstand these harsh chemicals. A lot of what’s on the market use a lot of plastics, which are porous and tend to become brittle as they are exposed to these harsh chemicals. One workaround has been to coat them in an antimicrobial application – Microban – to provide further protection. This logic has proved false (Source: https://www.microban.com/message-about-covid-19) as Microban, “when incorporated into a product, has not been proven to have any antiviral properties.” These coatings are also significantly worn down with repeated cleaning.
“What manufacturers can do is use non-porous materials, such as thermofoil laminate as seen on headwalls and cabinetry, and limit the use of plastic parts on high-touch and heavily cleaned surfaces. This [is] combined with continued education. Also important is a corrosion-resistant caster. Altus uses a shrouded caster [that] seals out the bearings from any liquids, which can cause rust and degrade the performance.”
Joe Hillebrand, National Sales Director, Altus
“Carts could be impervious to contamination by protecting stored items within a six-sided, lockable box [and] with a single ergonomically correct access point to monitor each transaction, such as the Hänel Rotomat automated vertical carousel, for example. Only the staff permitted to handle sensitive supplies will be able to physically touch them, and accidental handling will become a thing of the past. A password, passcode or keycard swipe would not only keep unauthorized personnel out of the inventory, but also record every transaction to track every item. These recorded transactions could then be sent electronically to higher-level systems, such as EPIC, Cerner or Lawson, so that PAR levels could be monitored and purchases be made on time and without purchasing excess inventory.”
David Phillips, Marketing Manager, Hänel Storage Systems
“This is something we’re always working on. A trend that we’ve recognized and responded to is the need for smaller, lighter cart solutions. We designed our CareFit Slim product line with this in mind. These compact carts are easy to adjust, fit a broad range of caregivers and are easy to maneuver. Technology advancements have helped as well. Mini PCs are smaller, take up less space and use less energy, so a smaller cart battery is sufficient. Similarly, monitors are bigger, but they’re also lighter, which helps make the cart lighter.
“Discussion around infection control comes up more in conversations than it did a year ago. Recently, we introduced UV Angel Adapt technology for our StyleView medical carts. This accessory uses UV-C light to eliminate up to 99% of surface contamination, including bacteria, viruses and fungi, on the high-touch areas of the cart — the worksurface and keyboard. We also pay attention to cleanability and reducing the cracks and crevices and other places that are harder to clean. Our CareFit Pro medical cart features internal cable management for that very purpose. In the future, we might see more interest from our customers in materials that assist with pathogen reduction. Still, different regions around the globe vary widely in their interest in antimicrobial surfaces.
“Recently we’ve heard some interesting feedback about castor hardiness. We’ve seen our carts deployed into large vaccination sites, including non-traditional spaces like parking lots. Our customers have told us that our carts, including the castors, are holding up well. While we didn’t necessarily design our castors for use on asphalt, we’re pleased that they seem to be rugged enough for limited outdoor use.”
Angela Poulson, Senior Product Manager for Healthcare, Ergotron
“Medical carts come in many different shapes and sizes and are constructed with a wide range of materials, such as plastic, painted steel, painted aluminum, chrome, stainless steel, polycarbonate, etc. Each material has its upsides and downsides depending on the application and the budget. With that said, all major medical cart brands in the market offer a comprehensive range of options that will fit, form, function, and meet the current healthcare standards.”
Ian Loper, Vice President, DSI
“Patient engagement is an important area of improvement. Patient use of technology was not so common before COVID, but it suddenly increased both adoption and expectations by both patients and caregivers. It’s like the reluctance to use technology suddenly evaporated and forced so many people to try something new, and many liked it. We had many requests for adding capabilities for direct patient interaction with technology, which led to improvements like a flexible tablet arm that could be bent down for use by a patient in-bed or seated. Making it easy for patients to view displays is another area where the needs keep growing. Workstations were previously viewed as being for caregiver use; now they are increasingly serving both caregiver and patient needs directly.
“Other improvements are more part of ongoing trends, where the latest generation workstations keep benefiting from battery improvements, they keep getting lighter and easier to maneuver, they keep getting more tools to manage the fleets to keep the right number of carts ready and available in the right locations, and they keep getting easier to configure for highly variable requirements. We were the first to develop a medication cart for point-of-care back in 2003, and it is incredible to see how far workstations have advanced since then!”
Steve Torbett, Senior Product Manager, Capsa Healthcare
“Across the world in all verticals, data has become so important to drive strategies, decisions and operations. Healthcare has the opportunity to use data to improve safety, efficiency and system optimization. Automated Dispensing Systems (ADS) are data-rich and offer tremendous opportunities to harness and utilize it in a smart way to drive visibility to medication inventory, expiring medications and potential indicators of diversion. Omnicell XT automated dispensing cabinet systems currently have the ability to capture data to optimize pharmacy operations, but we are always looking for additional ways to utilize the data generated from our automation to drive more valuable insights for customers. Regarding ADS design, our XT system is modular and we offer flexible configurations in 1, 2 and 3-cell designs. Each cell is essentially a tower that maximizes the use of vertical space to maximize the number of medications that can be stored and managed within a cabinet system. The greater number of meds stored in the cabinet drives safety, efficiency and optimized time to therapy. The XT is designed to add/remove/move drawers within the cabinet at hospitals to maximize flexibility as medication management needs evolve.”
Len Hom, Director, Product Marketing, Point of Care Solutions, Omnicell
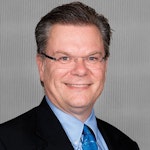
Rick Dana Barlow | Senior Editor
Rick Dana Barlow is Senior Editor for Healthcare Purchasing News, an Endeavor Business Media publication. He can be reached at [email protected].