Tips, tools, tricks for managing laboratory supply chain operations
How should Supply Chain work with Laboratory to help that department with product and service evaluation, selection, contracting, logistics and value analysis? Four experts share their thoughts.
Suzanne Meinert, JD, MT (ASCP), Contract Manager, Laboratory, ROi
Developing and maintaining strong partnerships with both supplier and laboratory distributors ensures that Supply Chain is continuously aware of opportunities for SKU consolidation and product conversions, thus allowing for savings opportunities for our members.
Regular communication with our members enables Supply Chain to be knowledgeable about our members’ needs and ensures that we are making meaningful connections within the laboratory industry that will benefit our members.
Staying informed about the latest developments in the laboratory industry, both in terms of new products and changes in laws, rules and regulations, means that Supply Chain is able to anticipate future needs of our laboratory members and find solutions to challenges arising in the laboratory field.
Being engaged with our analytics team and leveraging their expertise in evaluating pricing provides us with the best possible data to ensure that we are delivering the value that our members expect from us.
Being open and willing to consider new products and services and to present these to our members for their evaluation means that we are able to stay at the forefront of new technology and developing opportunities in the laboratory field.
Donna Showers, Senior Director, Lab/DI Specialists, Intalere
- Provide contract review, product standardization for one or multiple laboratories (within an IDN or laboratory alliance) and/or distributor optimization and consolidation. Depending on their level of sophistication, labs can save significant costs by aggregating spend through a regional laboratory alliance group or understanding and using their distributor relationships properly. Your distribution partner should be able to help you understand the cost and efficiency advantage of utilizing their distribution model as the best source of procuring product whether it is through pricing advantage, elimination of added transportation charges, improving overall tier slotting on the distribution contract, and reduction in the number of purchase orders generated and managed.
- Examine overall laboratory profitability of both in-house and outsourced testing. This includes an in-depth make-versus-buy assessment to help your lab understand both the costs of performing tests (to include both supply and labor costs) as well as the profitability of those tests by determining payer mix and payer rates. The same assessment should be performed on those tests that are outsourced to a commercial reference lab. Based on staffing levels, equipment available, and most importantly, how testing and turnaround times affect patient care, the lab can determine which tests should be done in-house versus outsourced. For example, in one of the labs we examined, we determined that the lab could generate an additional $200,000 in revenues as a result of the findings of our make-versus-buy assessment. One final process to the make-versus-buy assessment would be to conduct an RFP for the remaining reference lab testing – try to consolidate the number of reference labs that are used for the purposes of streamlining send out operations as well as realizing better pricing through economies of scale.
- It’s not all about product necessarily. Workflow and laboratory design evaluation can make huge differences in improved efficiency and productivity.
- Many lab professionals are challenged with a lack of ability to verify pricing accuracy on their purchases. Using software to identify and resolve pricing variances as quickly as possible can help reduce costs, eliminate future errors and improve overall price accuracy.
- Introduce Revenue Cycle Management. Laboratory managers should be corresponding with their billing departments. Laboratory outreach is often an overlooked revenue center in hospitals. Hospital information systems may not have the capability of measuring lab fiscal performance. The lab needs to have more control over their RCM process due to the payer-related nuances that are unique to lab. With appropriate software, coding expertise, collection strategies and denials management, the lab has the ability to improve their revenues by up to 20 percent to 30 percent.
Brent Bolton, CPSM, Regional Director, Supply Chain, Accumen
- The best sure-fire best-practice tip for supply chain involvement specifically in the laboratory is to partner with Accumen to address supply chain functions. We only focus on laboratory service evaluation, supplier section, vendor negotiating/contracting, logistics, value analysis, compliance and, most importantly, execution. We have unique hospital partners – our clients – and national vendor relationships that facilitate win-win partnerships and drive value beyond what our hospital clients are generally entitled to by standard GPO tiers.
- “Right size” equipment purchases to health system volumes. Most hospitals buy equipment that far exceeds their testing requirements. This reduces capital and increases equipment annual service costs.
- Transition to low-cost product alternatives. Typically, these items are the same products manufactured by the same supplier, but the low-cost alternative supplier typically will private-label the products.
- Don’t be fooled by suppliers that offer “free” instrumentation. Nothing is free. Those costs are hidden somewhere, and it is typically in the reagent or service costs. For products that have year-over-year volume increases, health systems end up paying a higher “total cost” for instrumentation that is burdened.
- Implement standing orders for products with minimal variation in demand. Typically, vendors will provide free shipping if standing orders are implemented. This will ensure product supply, promote quality control, better lot control and less waste, while also reducing costs.
Ryan Cox, Vice President of Sales, Laboratory Products, Cardinal Health Inc.
- When Supply Chain and Laboratory teams utilize data and analytics to assess utilization and purchasing patterns, inefficiencies within the supply chain can often be uncovered. These inefficiencies can turn into opportunities for savings when the same or similar purchases from multiple manufacturers or distributors is eliminated or lower cost alternatives are identified for substitution in product usage.
- Reducing inventory to help reduce carrying costs and improve cash flow.
- Utilizing inventory management practices and technologies to reduce or eliminate expired product.
- Optimizing the delivery of supplies to lab to help free up technical resources from performing non-clinical activities.
- Focus on product usage optimization. Space within the laboratory is at a premium and by optimizing the monthly consumption and ordering of supplies, space can be better utilized within the laboratory.
- Evaluating freight shipments and analyzing the optimum mode for freight and parcel delivery.
Akiva Faerber, Senior Principal, Vizient Inc.
- Partner with the lab team and consistently introduce competitive new supplies, services options/levels that are less expensive but meet the needs of the lab or that have the potential to improve performance.
- Work with manufacturers to enable the lab to conduct side-by-side evaluations of testing equipment to determine best platform. These side-by-side evaluations provide valuable insight in terms of floor space, technical ease of operation, test capabilities in terms of test mix and volume capacity, reliability, ease of customer capable maintenance and logistics. This also gives the lab staff the ability to have a “hands-on” assessment of the quality of the service staff in the event of platform failures.
- Negotiate and facilitate onsite training and train-the-trainer learning opportunities. Include these as part of the contract to eliminate add-on expenses should initial training found to be not adequate.
- Facilitate the frequency and ease of QA/QC, sequestration of reagents, information system interfacing.
- Entertain, educate and encourage vendors/providers to bring new lab-related products and services to lab for evaluation.
- Explore the option for support subject matter experts in lab to assist with efficiency, reducing costs, increasing revenue, performing coding billing and compliance opportunities, validation of lab information systems, Lean projects and improve TAT root cause analysis beyond lab. Ideally, there would be one SME from the vendor to assist with those tasks and one or two consultants to provide operational support.
- Assist lab department leadership in leveraging the benefits of point-of-care testing and cost versus traditional lab platform testing.
- Provide just-in-time agency staffing and interim management as necessary. Provide assessments as request for options related to outsourcing of laboratory management or sale of lab to commercial provider as well as review and negotiate pathology LLC contracts.
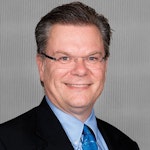
Rick Dana Barlow | Senior Editor
Rick Dana Barlow is Senior Editor for Healthcare Purchasing News, an Endeavor Business Media publication. He can be reached at [email protected].