Routine Sterilizer Maintenance Vital for Effective Operation
Routine sterilizer maintenance ensures safe and effective operation and plays a vital role in reducing the risk of contamination of sterile items. In my consulting experience, however, routine sterilizer maintenance often is not given proper attention.
For a steam sterilizer to heat and dry properly, regular chamber cleaning is required. Scheduled cleaning helps facilitate effective sterilizer function and maintain a uniform, consistent surface that is free of debris, mineral deposits, and discoloration.. The quality of water used to produce steam, high temperature, and pressure that make sterilization possible can cause unnecessary wear on the unit’s chamber and other components. Remaining residue after a cycle is run can cause buildup and surface contamination from detergents, wrapper chemicals, scale, rust, and foreign materials (e.g., autoclave tape) that can corrode the interior of the chamber, resulting in ineffective sterilization. It can also contribute to wet loads, costly unit repairs, premature replacement, and excessive downtime.
Sterile Processing leaders should stay current on standards, recommendations, and regulatory changes. For example, Section 12.4 of ANSI/AAMI ST79:2017/(R)2020 states that sterilizers should be inspected and cleaned daily. This underscores the need to follow the sterilizer manufacturer’s instructions for use (IFU) for routine inspection, cleaning, and documentation.
Maintenance, cleaning, and routine servicing
Sterilizer manufacturers may have different recommendations for routine servicing, including specific steps and recommended time intervals. Healthcare organizations are responsible for ensuring that routine maintenance occurs. If maintenance was part of the original purchase agreement or extended service contract, the SP leader must ensure the work is being performed. If routine maintenance is not part of the initial contract, the service can sometimes be added for older units as a service agreement. The manufacturer’s IFU will outline routine cleaning frequency, and the SPD’s responsibility should be added to the department’s policy, along with precise steps to follow.
When cleaning a sterilizer, it is essential to know the composition of the inner chamber. Stainless steel is most commonly used; however, some older sterilizer chambers were comprised of cold-rolled steel clad with nickel. Knowing the material helps determine which chemicals or bead-blasting methods are most appropriate for the unit. Cleaning routines should be established in policy (some aspects might be done daily, weekly, monthly, or annually) and align with manufacturer recommendations. Most sterilizer manufacturers have a pre-cleaner, descaling solutions, and brushes for use with their systems; check with the unit manufacturer for clarification.
When performing sterilizer maintenance, it’s essential that staff are properly trained and understand the manufacturers’ IFU for each sterilizer in the department. SP leaders must also ensure technicians have the appropriate personal protective equipment (PPE) and use it correctly during the process (autoclave gloves, for example, are essential for keeping employees safe when handling hot surfaces). Also vital is ensuring the correct supplies are available to prevent voiding the warranty. Some essential items required for proper sterilizer cleaning and maintenance include a special cleaner approved by the manufacturer to ensure it is safe for the unit’s surfaces. Ideally, solutions can remove scale, rust, and stains from both nickel-clad and stainless steel chamber surfaces. Water that is non-chlorinated or purified (deionized) is recommended for cleaning because impurities that can cause buildup and damage have been removed. Non-linting towels should be used to wipe external surfaces (never use abrasive clothes or brushes on metal surfaces).
Daily cleaning should involve inspecting various components of the autoclave and ensuring damaged parts are professionally repaired or replaced. Door gaskets should be checked for excessive wear or cracks, and the door must have a tight seal when closed. The gasket and mating surface should be cleaned with a mild detergent as needed. The interior chamber should be clean and debris-free, and pooled water should be wiped away before and after each cycle. Remove and inspect the chamber drain strain and clean as necessary. Further, clean the exterior surfaces, including doors, inner compartments, and controls with a manufacturer-approved cleaning solution. Always document when cleaning is performed. Following the IFU, weekly cleaning typically begins by turning off the unit to cool the chamber. Once cooled, remove the chamber drain strainer/screen and clean as needed. Apply the approved cleaning solution liberally throughout the chamber and brush all surfaces with nonabrasive cloths or brushes, rinse all surfaces with purified water, and wipe excess moisture with a non-linting towel. Inspect gaskets and mating surfaces and replace the chamber drain strainer. When the autoclave is restarted and reaches the correct temperature, run the appropriate number of biologicals. The unit should not be put back into service until all biologicals are negative. Finally, document the cleaning process and maintain the records.
Annual sterilizer maintenance typically includes a thorough inspection of all components as well as testing and calibration. Gaskets, seals, and filters should be replaced as needed to ensure safe, effective operation. Professional cleaning with chemicals or bead-blasting should also be done as needed.
Conclusion
Routine sterilizer maintenance and chamber cleaning help keep units running efficiently and effectively. Proper cleaning and maintenance may reduce wet loads, increase performance, meet standards and regulatory requirements, and contribute to successful outcomes.
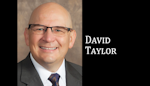
David Taylor | Principal, Resolute Advisory Group LLC
David L. Taylor, MSN, RN, CNOR is an independent hospital and ambulatory surgery center consultant and the principal of Resolute Advisory Group LLC, in San Antonio, Texas.