The 3Ps of Cleaning in Sterile Processing: People, Processes and Products
Whether it is manual soaking, brushing and flushing at a sink, or automated cleaning with ultrasonic cleaners or washer/disinfectors, effective cleaning of surgical instruments and devices in the sterile processing (SP) department is critical to patient care and safety.
HPN presents insights on three key areas of cleaning in the SP department – people, processes, and products – from Rebecca Peplau, B.S., CRCST, CER, CHL, CSPDT, manager, Central Sterilization Department, MaineGeneral Health, Augusta, Maine, along with information on some of the latest equipment, supplies, and solutions for instrument and device cleaning.
People and processes
Before diving into the products required for instrument and device cleaning, let’s start with the people using them and the processes guiding their use. Peplau provided insights on challenges she has seen in decontamination.
“One of the biggest areas of opportunity I see within decontamination areas is overall process workflow. That being said, many breakdowns of a workflow or barriers to truly effective and efficient workflows tend to stem from improper or lack of training and education coupled with a lack of proper working equipment to expedite tasks.”
Training
With the complexity of sterile processing workflows, and the vast number of different instruments reprocessed, it should go without saying that technician training and education is paramount to cleaning success.
“Training for each step of cleaning and inspecting includes utilizing the proper tools and testing all equipment daily,” said Ronald Hunsucker, CRCST, CHL, CCSVP, CIS, clinical education specialist, Healthmark. “These are just a few of the crucial steps that SPD has in place to provide the highest level of care all patients deserve. By utilizing both manual and mechanical methods, we can ensure all items are cleaned efficiently.”
Peplau recommends the trainee “buddy up” with a trainer who is competent in different types of instrumentation, including basic items and more complicated devices (e.g., robotic surgery instruments). She advises the trainer teach based on department standard work and standard operating procedures (SOP) during the training process.
Peplau also recommends that before training inside decontamination, have the trainer instruct the trainee on handling clean instrumentation in the assembly area, stating: “Getting a trainee exposure to touching and handling clean instruments can be a proactive approach to a more efficient and safer workflow within the decontamination area. Developing the muscle memory and overall feel of how to safely handle scissors without gloves on can make you more confident handling them with gloves on.”
“Decontamination training can take a long time and I feel like many people want to rush it, but it’s the most important part of the process,” Peplau added. “Failures of proper decontamination practices can double your workload when having to repeat them. The technician in training should start with the basics then work up to the more complex items, always with a dedicated trainer and never somebody working next to them, occasionally checking in. Also, the trainer or educator must drill home how the trainee can access an IFU from the beginning of their training onward.”
As a guiding source for all aspects of sterile processing, manufacturer instructions for use (IFU) should outline the steps required for effective cleaning, but Peplau noted this is not always the case. She stated:
“My biggest gripe is that IFUs can get updated or changed at any given time and it is up to us as end users to stay on top of that. Manufacturers are not required to notify us if cleaning or sterilization instructions have changed. This can be potentially hazardous to patients and SP staff. Additionally, the IFUs can be vague or have a general lack of information. Many device IFUs for hand wash only items do not indicate a step for disinfection prior to sterilization. Are these devices truly safe for our techs on inspection to handle? It is crucial to continuously look for updates with these items. Your vendor representatives can be a great help for finding this information.”
Testing
With regards to washer testing, Peplau, who is president of the Northern New England Chapter of the HSPA, explained how her chapter recently partnered with the Western Wisconsin HSPA Chapter to host a virtual seminar about protein. During their presentations, experts from Europe, Matthew Peskett and Pawel de Sternberg Stojalowski, explained European standards and how they pertain to protein and washer testing.
“In Europe, SP departments are required to test items coming out of a washer for residual protein regularly which is not yet required in America,” Peplau commented. “It makes you question the effectiveness of our current practices with routine testing and monitoring. Should departments add in protein testing to confirm every component of their automated washing system is truly working as designed? The science behind protein testing tells us why it is so important and makes you ask, ‘Why aren’t we routinely testing like that in our departments?’”
SP safety
SP professionals in decontamination are exposed to potentially dangerous bioburden, along with sharp items that pose the risk for cuts/punctures and infections. Peplau highlighted the importance of adequate personal protective equipment (PPE) and the dangers of not having it or failing to use it.
“There are still many departments that use overhead sprayers in sinks rather than spraying underneath the water’s surface,” Peplau explained. “This can indicate a gap in education and training which subsequently can impact workplace safety. Were trainees taught about aerosolization or chemical exposure? Do they know what to do if they are injured or have exposure to a chemical? Additionally, a lot of PPE isn’t adequate for decontamination, including open back gowns, exam gloves, masks with attached eye shields, and shoe covers that don’t cover your scrubs completely. PPE that doesn’t fit an employee well can pose a risk for chemical and pathogen exposure too.”
“When ANSI/AAMI PB70:2022 was updated, some PPE standards for decontamination were outlined with higher safety measures,” she added. “But there is still a lot of work to be done here. Each facility needs to find a way to protect their team the best they can given this new documentation while also adhering to OSHA and CDC guidelines. Additionally, there is the challenge of keeping your team comfortable temperature wise.”
“Another issue with manual cleaning can be the ergonomic challenges of a non-adjustable sink,” said Peplau. “If you’re shorter or taller, this can be a nightmare on your back and neck. Ergonomic assessments are critical for employee safety and injury prevention. Custom sink inserts can help allow for less bending.”
Products
Peplau stressed the importance of SP departments having the right technology and access to standards and guidelines to support effective, efficient, and safe cleaning, stating:
“With facilities trying to perform as many cases as possible to serve communities, we can’t always keep up. Therefore, having the right equipment and automation where possible is essential in our fast-paced environment. For example, having automated flushing systems in your sink is a huge advantage as opposed to repeated manual flushing steps – those seconds matter.”
As an Association for the Advancement of Medical Instrumentation (AAMI) committee voting member, Peplau feels shifts in standards should be driving more healthcare organizations to invest in SP department technology. She stated:
“Some of our IFUs require the use of a borescope, so why aren’t all facilities using them as standard inspection tools for the bulk of their instruments? We have the technology, and it should be implemented and put to use. I feel that it should be a mandatory piece of equipment in all departments given IFU changes and some standards recommendations.”
She points to a compelling example of the value of borescopes:
“Throughout my career I’ve encountered several devices that were flushed clean with fluid or air but after looking inside, it was found to have damage, rusting, or bioburden – this also includes devices new from manufacturers! If you can’t see inside of the device, how can you know it is truly safe to use on a patient? The obvious barrier here is cost. Borescopes can be a huge purchase for many departments; however, we have the resources and science to present to upper management and validate the expense. Investing here can mitigate potential legal expenses.”
Peplau also noted how she and other AAMI committee members are in the process of completing Technical Information Reports (TIR) and gearing up to begin early stage revisions to ANSI/AAMI ST79: Guide to Steam Sterilization.
Cleaning products, equipment, and solutions
Manufacturers and solutions providers continue to evolve their offerings to meet changing needs of SP professionals. Here is a highlight in the categories of brushes, sinks, and washer/disinfectors.
Brushes
“Sterile Processing professionals face new challenges every day when it comes to properly cleaning equipment and surgical instrumentation,” Hunsucker explained. “Instruments have become more complex and require choosing from a variety of styles, lengths, diameters, and bristle compositions to meticulously clean each instrument.”
Looking back on the evolution of brushes for instrument cleaning, Hunsucker pointed out how toothbrushes, scrub brushes, bottle brushes, and sometimes hairbrushes were not uncommon in the late 1970s and early 1980s.
“Now, we have acrylic, nylon, brass, polypropylene, stainless steel, and newer thermoplastic brushes,” said Hunsucker. “Specialized brushes for reamers, shavers, push through, pull through, wire, flexible and re-posable handle brushes [are available]. Reprocessing professionals must have the appropriate brush for every section and/or cannula(s) of an instrument to clean correctly.”
Cleaning chemistries
“Though our goal is to produce products that help SPDs be more efficient, we never want to lose sight of the safety of the staff,” said Chris Antonucci, Vice President of Global Marketing, STERIS. “When STERIS considered the reprocessing steps for robotic assisted surgical instruments, it was critical that we achieved both objectives. For example, Prolystica HP Instrument Cleaning Chemistries are formulated to reduce the cloudiness in the water during manual cleaning, giving the technician visibility of any sharps, helping to avoid injury when reaching into the sink.”
“From an efficiency standpoint, our patented Prolystica Ultra Concentrate HP formulations were also used to validate the RAS Cycle on the AMSCO 7000-series Washer/Disinfectors,” Antonucci added. “This cycle automates a significant portion of the cleaning process of select daVinci EndoWrist instruments, reducing manual cleaning time by at least 25% and reducing overall processing time by over 60 minutes for a set of four instruments.”
Sinks
With regards to SP department sinks for instrument cleaning, Hannah Schroeder, BSHA, CRCST, CHL, CIS, CER, Clinical Education Specialist at Pure Processing, spoke to some of the innovations her company exhibited at the 2024 Healthcare Sterile Processing Association (HSPA) Annual Conference, which was held April 21-23 in Las Vegas.
Schroeder noted how Pure Processing is using copper alloy as a safety measure for its SP and endoscopy department sinks and blacklight as a visual inspection tool for efficiency in finding cement from orthopedic cases. She stated:
“Copper alloy has anti-microbial properties that provide continuous self-disinfection and can eliminate up to 99.9% of six common microorganisms in less than two hours. These microorganisms are: MRSA, VRE, C. Difficle, E.coli, Influenza A and Norovir.”
“Torvan Medical believes that efficiency and safety are two sides of the same coin,” said Doug Brown, vice president, Sales & Marketing, Torvan Medical. “We will always strive to be a leader in promoting safety and efficiency in sterile processing environments.”
Brown described how the company’s CLEANSTATION line of reprocessing sinks have been designed from the ground up to help optimize workflows in sterile processing departments.
“Bottom-filling basins, overflow sensors, and our eDrain push-button electronic drain system help prevent spills and splashing, greatly reducing the aerosolization of micro-organisms,” said Brown. “Ergonomic wrist-comfort sink edges and electromechanical height-adjustment reduce user fatigue and strain. Our integrated eSink system improves and simplifies complex workflows by combining basin auto-fill, temperature control, and enzymatic-compatible basin dosing into an intuitive touchscreen interface. Pegboard backing with overhead LED lighting helps keep surfaces free of obstruction and improves workspace lighting for users.”
Specific to endoscope cleaning, Schroeder said Pure Processing has taken the initiative to read and understand the latest ANSI/AAMI ST91 requirements and applied this knowledge to supporting the industry’s needs both for the immediate changes and long-term investments.
“Pure Processing designs endoscopy-specific sinks that can be customized based on your department size,” Schroeder explained. “We take into consideration the recommended 2 to 3 basin workflows, including the recommended basin size of 16X30. Our added pegboards provide ergonomic working space for cleaning accessories, including leak testers and flushing systems, to be mounted up off counter space to aid in workflow compliance and open up counter space.”
“We also have single basin options to help support extended soak times by providing a specific area to prevent bottlenecking and backlogs,” she added.
At the 2024 HSPA Annual Conference, Pure Processing unveiled a new tool focused on the customization of reprocessing equipment, as Schroeder explained:
“To fully achieve ‘clean’, each department has different requirements; they require different configurations for their equipment. With our new 3D customization tool, reprocessing professionals will be able to build and configure their sinks and workstations to meet the exact needs of their department and place the equipment in their department in augmented reality to see and interact with it where it would be used.”
Pre-wash technology
Torvan Medical is partnering with BICARmed to bring the SAFE CLEANBOX to North America. This closed-cabin system uses a specially formulated sodium bicarbonate and water mixture to assist with the pre-cleaning of heavily soiled instruments. Dried-on bone cement, bioburden in hard-to-reach crevices, brush-resistant cautery char and similar substances can be removed with little to no risk to the user or the environment.
Washer/disinfectors
“Automated washer/disinfectors offer a wider range of pre-programmed cycles to improve cleaning efficiency,” said Hunsucker. “Low to high-impingement, chemical based with impingement washers, ultrasonic units with specific cycles for cannulated items, and cart washers have all become part of everyday life in a Sterile Processing Department (SPD).”
The importance of ergonomics
Schroeder spoke to the importance of ergonomics in Pure Processing’s design process:
“Our customer-centric approach focuses on the needs that our industry is speaking to and the solutions they would like to see considered. More than height-adjustability, we focus on how the technician will engage with the space throughout their day. From repetitive movements to proper body mechanics, we have features to achieve efficiency and safety.”
She noted how automated flushing can help relieve the wrist strain that can be caused by repetitive flushing requirements, and Pure Processing’s 45-degree wrist slants at its sink basins eliminate pinch points that can cause pain and strain on arms and wrist.
“That wrist slant was designed from feedback by a system in the southeast with their Ergonomics Director; we can’t take full credit for the idea,” she explained.
“We also take into consideration that things like proper lighting, inspection tools, and adequate working space play a critical role in ergonomics,” Schroeder added. “There are a variety of ways for a department to comply and meet the needs of their teams, and Pure Processing understands this by making custom options available that best achieve a department’s goals.”
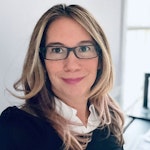
Kara Nadeau | Senior Contributing Editor
Kara Nadeau is Sterile Processing Editor for Healthcare Purchasing News.