Although many disruptions to healthcare supply chain networks have occurred in the past, none has been so widespread as the shortages experienced during the past year-plus as a result of the global pandemic. First, it was N95 respirators and other personal protective equipment (PPE) and oxygen tanks and ventilators — but the list of shortages continues to grow, and manufacturers and end users continue to scramble. Understandably, many healthcare professionals are left asking, “What’s next?”
Because of supply chain optimization efforts, many organizations have long embraced just-in-time inventory, only keeping a modest inventory of healthcare supplies in anticipation of future demand. This is an understandable approach because it’s more cost-effective than tying up money for supplies that will sit on a shelf; however, the pandemic proved challenging for facilities that lacked stockpiled supplies to get them through the wave of shortages.
Identifying shortages
Healthcare facilities — including hospitals, ambulatory surgery centers, physician offices and long-term care and rehabilitative care centers — waste critical time searching for depleted supplies, and some have had to turn to the decontamination of single-use supplies to fill the void. The U.S. Food and Drug Administration (FDA) established for the first time ever a medical supply shortage list website in an effort to improve communication.1
In March 2021, professional organizations such as the International Association of Healthcare Central Service Materiel Management (IAHCSMM) and the Association of periOperative Registered Nurses (AORN) released communications to notify their members that sterilization wrap shortages may be looming and could have a significant impact on surgical services across the country. (See sidebar for IAHCSMM’s statement)
It’s important to note that the sterilization wrap manufacturing process is similar to other products (e.g., filters, biologicals and dart test packaging). Some experts are now predicting that medical supply shortages could last for some time and will require a strategic plan to mitigate the effects.
Exploring alternatives
Sterilization wrap has been around a long time. In recent years, it has become stronger and more durable to provide better protection and resist tears. It also comes in a variety of sizes, making it an especially convenient and a heavily relied upon supply for Sterile Processing departments (SPDs). If sterilization wrap shortages affect hospitals and surgery centers in the same way PPE shortages did, it’s easy to see how surgical programs will be significantly and negatively impacted.
One alternative solution to sterilization wrap is the use of rigid sterilization containers. These also come in a variety of sizes, are produced by numerous manufacturers and provide a reusable, sustainable alternative for sterilizing instrumentation. Many organizations have incorporated rigid sterilization containers into their SPD departments as a way to reduce the amount of sterilization wrap needed within their facility. Keep in mind, however, that many of these containers require a filter, which may be made from similar material as sterilization wrap.
It’s important for manufacturers to be consulted with any questions or concerns regarding their products’ use, handling and availability, and to establish multidisciplinary purchasing committees to explore the best options for the facility/healthcare organization to help mitigate any supply shortage risks, now and in the future.
Planning ahead
The need for healthcare organizations to manage their supplies effectively to maximize the benefits for patients and employees remains critical, and it’s a need that should be explored well after the pandemic. If supply chain disruption is not managed properly, these shortages will threaten the delivery of patient care and, potentially, compromise the safety of healthcare workers.
Reference
1. U.S. Food and Drug Administration. Medical Device Shortages During the COVID-19 Public Health Emergency, https://www.fda.gov/medical-devices/coronavirus-covid-19-and-medical-devices/medical-device-shortages-during-covid-19-public-health-emergency
IAHCSMM Statement on Sterilization Packaging Shortage
IAHCSMM is aware of reports of sterilization wrap shortages throughout the U.S. These shortages may require facilities to consider alternative packaging. If your facility is considering implementing alternative packaging, be certain to ensure that:
1. The product is cleared by the FDA for use as sterilization packaging.
2. Your facility follows standards and guidelines when using the product.
3. Your facility follows the instructions for use of the packaging, sterilizer, and devices to be sterilized.
4. Appropriate testing is completed before use.
5. All user (Sterile Processing) and end users (Operating Room and other procedural areas) are educated on proper use of the products.
Specific Resources include:
• ANSI/AAMI ST65, Processing of reusable surgical textiles for use in health care facilities
• ANSI/AAMI ST79, Comprehensive guide to steam sterilization and sterility assurance in health care facilities
° Section 9 (p. 50), Packaging
° Section 10 (p. 61), Sterilization
° Annex H (p.142), Development of a prepurchase evaluation protocol for rigid container systems
• AORN Guidelines for Perioperative Practice (2021), Packaging Systems (pp. 571-590)
• AORN Guidelines for Perioperative Practice (2021), Sterilization, Steam sterilization 5.5 (pp. 994-995), www.aorn.org
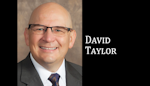
David Taylor | Principal, Resolute Advisory Group LLC
David L. Taylor, MSN, RN, CNOR is an independent hospital and ambulatory surgery center consultant and the principal of Resolute Advisory Group LLC, in San Antonio, Texas.