Why Water Quality in Sterile Processing Departments is Now a Top Priority
The topic of water quality and management has been coming up more and more in my conversations with sterile processing (SP) professionals. While the ANSI/AAMI ST108:2023 standard for water quality systems in medical device processing has certainly been a driver, concerns about water quality in the sterile processing department (SPD) aren’t new.
I reached out to those with expertise on this topic to understand why there has been growing interest and concerns about the water used in instrument and device reprocessing.
Based on these interviews, I aimed to answer high level questions those in the SP profession are likely to have about key differences between AAMI TIR34:2014/(R)2021 and ANSI/AAMI ST108:2023 and the role SP professionals should play as part of their healthcare facility’s water management teams.
I also asked each expert contributor to provide one piece of advice to SP professionals when working toward ST108:2023 compliance, with this commentary wrapping up the article.
Why does water quality matter?
With SP teams struggling with so many aspects of their profession, from rising case volumes to lack of adequate instrument inventory, why should they take time to address water quality?
After speaking with experts, the answer is clear – water quality impacts virtually every aspect of SP operations. And it doesn’t stop there. The effects of poor water management in instrument reprocessing snowballs to impact the operating room (OR), other procedural areas, and in severe cases, the reputation of the healthcare facility.
Most recently, media reports of U.S. hospitals with water quality issues in the SPD have heightened awareness of the problems that can occur.
“The headlines and social media frenzy from contaminated water incidents in healthcare facilities has spooked the public and internal healthcare leaders,” said Jhmeid Billingslea, CRCST CIS CER CHL CMRP CST HACP-IC, Managing Director Surgical Services, Advantage Support Services. “The overwhelming expense and service disruptions for instruments that do not come close to meeting their typical lifespans are killing SPD budgets. OR team members have also become more sensitive to wet packs, instrument staining and spotting, tray liner marks and other packaging variances caused non-compliant water usage in SPD.”
“My opinion is that water quality in the SPD has moved front and center,” said Aimee Space, BSN, RN, Product Owner, U.S. Medical Content, Incision. “If you're in the sterile processing world, it’s unlikely you haven't seen the stories about facilities shutting down over water quality concerns. It’s not just a safety concern but also a financial concern. If you must shut down your sterile processing department because of poor water quality that's a huge financial loss.”
The good, bad, and ugly of water quality
Jonathan A. Wilder, Ph.D., Managing Director, Quality Processing Resource Group, commented on the benefits of good water quality in the SPD:
“Water is a variable quantity when applied to processing of medical devices, depending upon where the facility is and the local water supply, and how the facility treats its water supply to generate water that is suitable for processing. Good, corrosion-free results and good cleaning with good removal of residual detergent in the washer/disinfectors and manual cleaning are a result of ensuring that the water used is up to the task and does not interfere with the action of detergent, or, if it does, that detergent is properly selected and dosed to compensate for this.”
Angela Lewellyn, Director of Development and Research, Advantage Support Services, pointed to issues such as stained instruments and chalk buildup in washers as indications of poor water quality, stating:
“These issues can mean the sterilization process isn’t working properly, which could lead to patients getting infections. Some of the science and effects of water that SP is beginning to understand is that some bacteria, like Legionella or Pseudomonas, can grow in places where water sits still, like pipes or drains. They can also spread through things like contaminated water used for rinsing instruments or even during handwashing if faucets or drains are infected.”
Herb Kaiser, PhD, Senior Principal Scientist, Analytical Services and Development at STERIS Corporation, called attention to the fact that poor quality impacts not only devices and instrumentation, but also the equipment used to reprocess them. He stated:
“With everyone in healthcare worried about dollars, it is important to understand how poor water quality can shorten the lifespan of SPD equipment, including washer/disinfectors and sterilizers. When somebody tells me they are having trouble with their equipment, one of the first questions I ask is, ‘What does the inside of your washer or sterilizer look like?’ If it looks bad, with residue and deposits, that will negatively impact your instruments and devices.”
What are key differences between TIR34:2014/(R)2021 and ST108:2023?
Wilder provided a summary of the evolution of water quality guidance and standards impacting the SPD.
“The effects of water on instrument processing were slow to be understood,” said Wilder. “The sequence of thought I have seen over my 34 years and one month in the industry from both the inside (in R&D and regulatory) was:
- Can we get it clean?
- Is our cleaning damaging the instruments?
- If our cleaning isn’t damaging the instruments, what is?”
“This is where TIR34 started,” Wilder explained. “It was first published in 2007. The second revision, which is the last revision, was published in 2014. These were both guidance documents, with a lot of progress made in understanding the effects of water between the 2007 and 2014 revisions.”
“Once the concept of the effects of water on processing was compiled into a TIR, it became clear to a group of AAMI committee chairs that enough was known to write a standard,” Wilder continued. “This led to the decision to create ST108. Detergent dosing, measures needed to provide good-quality critical water for final rinse, and how to make the best possible steam for sterilization depend greatly on the water supply.”
Kaiser offered his insights on the evolution of TIR34:2007 to TIR34:2014 to ST108: 2023, stating:
“The first version, TIR34:2007, featured many technical requirements related to testing and analysis of water for impurities, which many felt were confusing to the end user. To address this issue, TIR34:2014 featured simplified charts of the requirements. Unfortunately, this simplification came at the expense of eliminating some of the values needed to test and assess water samples. As a result, ST108: 2023 contains the values that were included in TIR34:2007 but with more detail for users to understand and apply them.”
As Kaiser noted, a major change in ST108:2023 compared with TIR34:2014 is that the standard defines three different categories of water important for device and instrument reprocessing:
- Utility Water: May be water as it comes from the tap but it may require further treatment at the facility to meet the specific requirements for Utility Water. This water is mainly used for flushing, washing, and intermediate rinsing (e.g., rinsing between cleaning and thermal disinfection in a washer/disinfector).
- Critical Water: Water that generally requires extensive treatment by a multi-step process that can include a pretreatment, does include primary treatment (e.g., reverse osmosis (RO) and/or deionization (DI)), storage, distribution, and can include final treatment to provide a level of assurance that microorganisms and inorganic and organic material are removed from the water. This water is used for final rinsing and can be used for steam generation. ST108 has no requirements for what goes into steam generators – only what comes out.
- Steam: Vaporized water that is produced by a centralized boiler or a generator/heat exchanger near the sterilizer.
“Steam is separated out as having its own values in ST108, which are pretty much identical to critical water but it's the mindset that steam is a different thing that needs to be tested,” Kaiser added.
Richard Parker, MBA, CHFM, CLSS-HC, FASHE, FACHE, associate director of life safety and physical environment, Accreditation Commission for Healthcare (ACHC), explained the difference between TIR34 and ST108, and what this means for healthcare organizations:
“The TIR is a Technical Information Report, a preliminary expert opinion statement,” said Parker. “It is not a requirement, but it contains information relevant and important to the industry and is vital for getting needed information out to the industry.”
“When it was advanced to a standard (ST108: 2023), it reached a consensus after public review and feedback,” he added. “This has been emphasized because the guidelines have advanced to an industry standard, and facilities are expected to progress to comply with the new standard.”
As Parker pointed out, the U.S. Food and Drug Administration (FDA) recognized ANSI/AAMI ST108:2023 as a standard in December 2023, which “suggests some momentum.” As of the writing of this article (December 2024), the U.S. Centers for Medicare & Medicaid Services (CMS) have not made a move to hold hospitals accountable for the standard.
He described nuances of the expanded requirements under ANSI/AAMI ST108:2023 important to SP professionals:
Definitions and testing of water quality types (including steam)
“One of the water quality types defined in the ST108 requirements is that of Utility Water. This may be mistaken for the untreated water from the local municipality but refers to softened water.”
Water system performance qualification
“This quality assurance step validates that the system designed and installed meets all predetermined requirements. It includes objective evidence, such as third-party confirmation that the water produced meets requirements.”
Communication/collaboration within a multidisciplinary water management team
“Sterile processing professionals need to know that their role is not passive. Participation and feedback are critical to ensuring that the objectives are met.”
Routine monitoring and continuous improvement
“Routine monitoring is a group effort. For example: SPD professionals will monitor the instruments during the packing process and monitor instruments that were not acceptable to the surgeon due to deficiencies. Facilities staff will likely be involved in the water quality monitoring and testing and provide this information to the team. Maintenance staff will monitor equipment performance and chemical effectiveness.”
“Like any preventive maintenance program for equipment, the intent is to maintain the system so that it provides the same quality as it did when it was installed,” Parker added.
Lewellyn commented on how the evolution of the TIR34 report to the ST108 standard has prompted some SPD teams to be proactive in water quality management, while in the past, they might have been more likely to be reactive to problems that arose.
“Water is the number one tool we use in SP, and although we have had the technical report in TIR34, most SPs did not take that information into consideration because SP relies on biomed engineers to monitor and take care of the water,” said Lewellyn. “Usually, most SPs would get involved in water and steam quality if a problem arose, like wet loads or if instruments came back from the OR due to staining or blackened discolorations. But now SP has AAMI’ndras standard 108 that defines water, its uses and how best to test and monitor it.”
Who should be part of a hospital’s water management team?
The establishment of a multidisciplinary water management team is a key element of the ANSI/AAMI ST108:2023 standard. But who should be a part of this team? And what role should SP professionals play?
“Personnel who maintain sterilization equipment, such as clinical engineering or facilities staff,” said Parker. “If equipment maintenance is outsourced, a maintenance representative from that company should be part of the water management team. This participation may involve documenting equipment performance, maintenance issues, and other observations.”
Wilder outlined the ST108 suggested team membership, describing their purpose and roles:
- Executive sponsors
- This is the C-suite, who hold the purse strings.
- Facilities engineering
- This group is responsible for the infrastructure needed to get the water to SPD in its required state.
- IP/IC
- This group is responsible for ensuring that anything that goes wrong and has potential or real effects on patient outcomes is recorded and the root cause determined.
- SPD/other processing personnel
- They do the work using the water for processing. They know when things are going wrong.
- Clinical engineering
- They support the maintenance of the water system in a state where there are no pathogens or unexpected hindrances to water’s application.
- OR/procedure area personnel
- This is the final QC test. Their observation of issues should be analyzed for trends and their needs for new instruments should be checked against the available processing capabilities.
Given the potential high cost of remediating water quality issues and the financial pressures on healthcare organizations today, Kaiser emphasized the importance of engaging hospital executive leadership in water quality management initiatives, stating:
“There definitely must be somebody involved from the executive team of the hospital. Somebody who can make decisions, take action, and allocate the resources.”
What role should SP professionals play as part of this team?
For SP professionals interested in getting involved in their hospital’s water management practices, the experts interviewed for this article offered their insights.
Wilder noted the advantages of active SP professional participation in water management, and how the consequences of poor water quality can impact the department:
“Sterile processing is where the water is used and so the team should be involved in advocating for getting the water supplies to where they need to be,” said Wilder. “Sterile processing’s axes to grind here are:
- Good cleaning leading to good productivity with minimal rework
- Avoiding corrosion
- Avoiding staining
“Since SPD (and similar specialty departments that are similar in operation, like endoscopy) is where things happen for processing instruments, they will see issues first and, sadly, be blamed for them if they get to the point of use of the instruments,” said Wilder. “It is a matter of both quality assurance/control and self-preservation.”
Get educated and give feedback on water quality
Parker recommends SP professionals first learn how water is treated before it reaches their department.
“Specific criteria must be met for either RO or DI water, and as the end user, knowing the testing results provide insight,” he explained. “Provide feedback to the water management team on issues and trends with instrument processing. The SPD performs quality assurance activities on the process and instruments. This feedback affirms or identifies whether the methods of the water management plan are effective.”
Collaborate and communicate cross functionally
As part of a multidisciplinary water management team, SP professionals will have the opportunity to collaborate and communicate with the other disciplines. Lewellyn stressed the importance of relationship building between SP and facilities engineering teams in driving successful ST108 compliance.
“ST108 requires daily, weekly, monthly, and yearly testing of the three water types at different distribution loops,” she stated. “At Advantage Support Services, we encourage SP teams to partner with facility engineers by conducting regular cross-departmental rounds. These visits can be as brief as an hour but are highly impactful. We refer to this as going past the ‘wall,’ symbolizing the cinderblock barriers that house steam boilers and equipment in the facilities department—an area many SP staff have never seen.”
“During these visits, SP staff can gain valuable insight into how steam and water systems are managed,” Lewellyn continued. “Similarly, facility engineers should visit the SP department to understand how water quality directly affects processes like decontamination.”
According to Lewellyn, regular communication and collaboration are critical for success. She recommends SP and facilities engineering stakeholders schedule regular meetings that focus on reviewing water and steam quality reports, discussing deviations, and planning corrective actions.
“Sharing resources, such as ST108 tables for performance standards and monitoring schedules, helps ensure both teams are aligned,” she added.
Keep on top of water quality testing
“Water quality results must be regularly monitored and shared between SP and facility engineering teams to maintain compliance with standards like ST108,” said Lewellyn. “Key tests include pH measurements, which should be taken at the point where the water distribution loop enters the processing area. These tests should be performed quarterly for utility water, monthly for critical water, and quarterly for steam. Additional tests, such as conductivity, total alkalinity, and total water hardness, should follow the same schedule. Bacterial testing is also essential, with samples collected quarterly for utility water and monthly for critical water.”
Lewellyn noted how the Advantage Support Services team, including a steam expert, provides a comprehensive evaluation of a facility's water quality, including an in-depth analysis of its water system; tailored education on water quality fundamentals; and a comprehensive report that outlines any identified risks, detailed test results, and actionable recommendations.
Space said even if routine water quality testing is performed by the hospital’s facilities or engineering team, the SP team needs at the very least to have awareness that this testing is taking place. She also urges facilities and engineering staff members to keep the SP informed of any issues that could impact the quality of their reprocessing water.
“Usually, facilities or engineering will be the ones who first learn of problems with city water, such as a water main break or repair,” Space explained. “They will also be aware of when boiler maintenance takes place in the hospital. In these cases, they need to notify the SPD team so they can be on high alert for any impacts on instrument and device reprocessing.”
In January 2025, Incision launched an online course, The Importance of Water Quality in Sterile Processing, as part of a sterile processing e-learning program, which can be accessed through the company’s website.
Kaiser reminded SP professionals to consider seasonable variations that influence water quality when performing testing. He stated:
“Water changes in the spring, summer, fall, winter. Droughts or flooding can impact the quality of water in your facility. So, make sure you incorporate these factors when you are setting your test limits.”
For hospitals seeking knowledge and assistance with water testing, Kaiser highlighted STERIS water and steam testing services, Knowledge Center articles, and several webinars and study guides from STERIS University, all which can be found on the STERIS website.
Water quality management advice to SP professionals
When asked for one piece of advice they would give to SP professionals when it comes to water quality management and compliance with ST108, the experts interviewed for this article provided the following statements.
Jhmeid Billingslea, CRCST CIS CER CHL CMRP CST HACP-IC, Managing Director Surgical Services, Advantage Support Services
“Be tougher customers! The responsibility for producing and maintaining the systems that produce Utility and Critical Water lies in other departments, but ST108 gives us the tools to test that water, ask for reports, and join and contribute to the steering committee that oversees the water used in our facilities. It is up to us to take this opportunity to educate ourselves so that we can ask the right questions and advocate for water that ensures patient safety.”
Herb Kaiser, PhD, Senior Principal Scientist, Analytical Services and Development at STERIS Corporation
“The first thing is to breathe. I hear and see a lot of panic out there around ST108, and believe it or not, there are others who have never even heard of TIR34. Compliance is a marathon, not a sprint. You can’t flip a switch, and all your requirements will be met. Purchase some copies of ST108 for stakeholders in your facility involved with water management and make sure they read it. Go slow with changes and make adjustments along the way. Turn to your SP equipment vendors and water suppliers for assistance because they have the knowledge and the resources to help you.”
Richard Parker, MBA, CHFM, CLSS-HC, FASHE, FACHE, Associate Director of Life Safety and Physical Environment, Accreditation Commission for Healthcare (ACHC)
“Although accrediting organizations are not holding organizations accountable for this yet, many of the requirements for water quality have been an industry best practice for nearly a decade. Some requirements may also be found in the manufacturer’s instructions for use. The FDA recognized AAMI/ANSI ST108 on 12/18/2023.”
“My advice would be for sterile processing professionals to get involved with the water management team and begin a gap analysis to determine what steps are needed to achieve the requirements in ST108. If equipment is needed, this may need to be added to the capital equipment planning process. Often, installing the equipment has a space impact, and planning would be needed for that. SPD professionals need to get the conversation started.”
“The best water quality achievable will not fix a poor process. SPD professionals must continue efforts to validate each step of the process from the OR to the end of device sterilization.”
Aimee Space, BSN, RN, Product Owner, U.S. Medical Content, Incision
“You don’t need to be an expert in chemistry or engineering to play a role in water quality management within your hospital. There are many educational resources available, like the courses we are creating at Incision, to help you in your efforts. I encourage SP technicians to seek and learn practical aspects, so they can play their part in managing and maintaining quality.”
“And when you suspect a problem in your department, don’t be afraid to stop the line and ask a question or raise an issue to your manager. You will likely learn something and many times your manager will too.”
Jonathan A. Wilder, Ph.D., Managing Director, Quality Processing Resource Group
“The standard was not created to increase the burden on SPD, but instead to help them get their work done more effectively. No one wants to do the same work twice. Water that meets the ST108 requirements will help reach that goal.”
Reference:
-
ANSI/AAMI ST108:2023— Water for Processing Medical Devices, ANSI, November 13, 2024, https://blog.ansi.org/ansi-aami-st108-2023-water-quality-medical-devices/
What is a sterile processing (SP) super user?
When defining roles and responsibilities for SP professionals as part of a multidisciplinary team, Angela Lewellyn, Director of Development and Research, Advantage Support Services, suggests SP department (SPD) teams designate a “super user” to oversee water quality compliance. She defines this role as follows:
“In sterile processing, a super-user is a staff member with specialized expertise in water quality management. It is beneficial for SP to designate and initiate education to one or more super-users on the basics of water management solely in SP.”
“Their primary role is to monitor water quality by gathering and documenting test results, identifying issues, and ensuring the department meets compliance standards. They also serve as the go-to expert for troubleshooting water-related problems, such as black-stained instruments or wet loads, working to identify and resolve the root causes.”
“Super-users are vital because they ensure ongoing education and knowledge-sharing within the department. By training other team members, they help build a sustainable culture of quality management, creating additional super-users to maintain consistent standards over time. This role not only helps address immediate issues but also supports long-term improvements.”
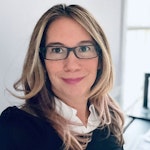
Kara Nadeau | Senior Contributing Editor
Kara Nadeau is Sterile Processing Editor for Healthcare Purchasing News.