The pressures on central sterile/sterile processing department (CS/SPD) professionals to deliver safe and effective surgical instruments to the operating room (OR) and other clinical locations are significant and are only growing as healthcare organizations attempt to deliver higher quality care at a lower cost.
While many improvements and technologies are focused on core CS/SPD processes — decontamination, cleaning, assembly and packing, sterilization — it is important not to overlook two other critical processes impacting patient care — instrument storage and transport. The practice of storing instruments until ready for use and transporting both clean and dirty instruments to and from clinical areas is one that is integral to maintaining a safe, effective and efficient care environment.
Along with some of the latest products for surgical instrument containment, storage and transport, product vendors present insights on how they are working to address the challenges that CS/SPD professionals face in these areas.
Avoid damage
Surgical instrumentation is continuously growing in complexity as manufacturers develop devices featuring greater precision and efficacy. This evolution presents to the CS/SPD devices that are far more intricate and delicate than their predecessors, and require more careful handling, processing, transport and storage.
“It is critical for healthcare organizations to invest in durable protective sterilization containers to prevent damage of their intricate surgical equipment,” said Amy Wiedre, Marketing Manager, Service Marketing for KARL STORZ Endoscopy-America. “Containers should feature a bracket system to provide a secure and protective environment for transportation, sterilization and storage of the equipment. Hearing a scope roll around inside of a container is never good, and often means there will be damage to the scope. Placing a scope inside a container without a bracket to secure it properly and then sending it up to a procedure on a case cart or through the sterilization process is irresponsible. Keeping equipment secured in a container featuring a bracket system before and after a procedure will help to reduce the rate of repairs.”
KARL STORZ offers no-wrap containers with a variety of bracket systems to secure KARL STORZ surgical equipment during transportation, sterilization and storage. KARL STORZ no-wrap containers are crafted from durable aircraft-grade anodized aluminum, creating a superior protective housing for surgical equipment. The no-wrap containers also come with customizable ID plaques to insert on the outside of the container, enabling quick and easy identification of the contents.
Streamline through standardization
“Meeting the instrument demands of the OR means having the right instruments, at the right time, in the proper condition,” said Troy Scroggins, Product Manager, Sterile Packaging for Aesculap. “Utilizing Aesculap’s SterilContainer System can help increase OR-CS/SPD reprocessing cycle efficiency.”
According to Scroggins, CS/SPDs that standardize on one method and one brand of containers can derive a variety of benefits, including simplification of process documentation and instructions for use (IFUs); reduction in cost and waste; simplified training of new employees; reduction in OR-CS/SPD employee stress; higher employee retention; and better patient outcomes through a lower chance of case delays, errors and confusion.
Aesculap’s new PrimeLine Pro lid is reliable and long lasting to meet the rigorous demands of the CS/SPD. The robust 2mm aluminum lid features an integrated, reusable, PTFE filter designed for 2,200 sterilization cycles, saving time and reducing processing costs. This premium lid option is available for Aesculap’s SteriContainer JK and JN series in full, three-quarter and half-size containers.
Size matters
Surgical instruments come in many different shapes and sizes; therefore, CS/SPDs must find ways to safely and effectively accommodate this variety during transport and storage.
Aaron Lieberman, Marketing Manager for Summit Medical, an Innovia Medical Company, highlights the challenges around extra large devices, such as da Vinci instrumentation. In particular, he points out the need for right-sized sealed transport containers that facilitate presoaking of these instruments prior to manual or automated cleaning. He states:
“If you don’t have a transport container to soak your instruments in then that process cannot start until the instruments get back to CS/SPD. This can be especially challenging for da Vinci instrumentation or other very long laparoscopic instruments because there are not many solutions for this on the market. In addition to needing something large enough to soak and transport longer instruments, facilities should be mindful of the potential instrument damage that can occur during transportation in those containers.”
To address this need, Summit Medical recently launched its XL size Transport Container, which is designed long enough to specifically transport soiled da Vinci instrumentation and other laparoscopic instruments from the OR or CS/SPD.
“Our goal when developing this product was to help our customers follow presoaking procedures in manufacturers’ IFUs more easily,” said Lieberman. “Some instruments need to presoak for a specified amount of time before they can be manually cleaned and with this container that process can start in the OR reducing reprocessing time. Our transport container also has a seal to prevent spills and a drain to accommodate removal of soiled liquid. As an accessory we will offer lifting trays that fit into the container and will protect da Vinci instruments during transportation.”
On the other end of the size spectrum, transporting and storing small items is a significant challenge as well. Liz Ostrow, Marketing Manager for gSource, points to the difficulties associated with effectively organizing and storing k-wires and pins, as there are many different lengths and diameter sizes available.
To accommodate these products, gSource offers its gRack for 9” k-wires and pins (gS 98.5409), which features 12 slots for storage and organization of common diameter sizes (0.7mm-4.5mm). The k-wire and pin diameters are marked on both the measuring gauge and the slots inside the rack for easy identification and organization. The gRack folds closed for convenient storage, and when closed, k-wires and pins are held securely in place, helping to prevent shifting of contents. When the rack is open, it converts to a tabletop stand for use in the OR. It also features a handle that allows the rack to be easily carried and transported. Made from anodized aluminum, the rack is lightweight, yet built to withstand rigorous and repeated use.
Stay sterile
CS/SPD professionals put forth tremendous time and effort to effectively decontaminate, clean and sterilize surgical instruments but the challenge doesn’t stop there. They need products that help ensure the instruments remain sterile and safe during transport and storage.
“The Joint Commission (TJC) and Association of peri-Operative Registered Nurses (AORN) acknowledge that microbial contamination of a sterile package is ‘event related’ and is caused by an event such as improper handling or transport rather than time alone,” said Brandon VanHee, Clinical Education Manager for Key Surgical. “Sterility is often compromised by physical damage to the package such as tears, punctures and abrasions in wrap material. Utilizing instrument trays that are lightweight, and free from sharp corners and edges, or surgical tray corner protectors can help prevent tears and punctures in wrap material.”
CS/SPD professionals can protect and organize delicate surgical instrumentation during the sterilization process with Key Surgical’s Plastic Sterilization Trays. Constructed of a durable polymer, the trays provide strength, durability and chemical resistance while remaining lightweight and easy to use. Available in various sizes, each Plastic Sterilization Tray includes a silicone finger mat that can be removed for easy washing. Perforations in the lid and base of tray help with steam circulation and aid in the drying process.
Accommodate increasing demand
As surgical volumes increase, so does the work of CS/SPD professionals. They face constant demand to speed instrument processing turnover times, while maintaining a high level of effectiveness and safety.
“Staff have many constraints that they work through every day but time is one element that is not on their side,” said Barbara Ann Harmer, MHA, BSN, RN, Director of Clinical Services for Innovative Sterilization Technologies. “With the exception of ONE TRAY, the average time for a packaging system to be ready for use, sterilization cycle time, dry time and cool time is 2 to 3 hours. With any surgical volume, but especially with many implant procedures being done now on a daily basis in most facilities, there are only so many instrument sets and sterilizers.”
The ONE TRAY Sealed Sterilization Container from Innovative Sterilization Technologies is FDA-cleared to hold temperature-tolerant medical devices during steam sterilization cycles and then be stored.
“CS/SPD staff can now react quickly to any changes or issues during the day schedule or addressing on call situations when dealing with emergent needs,” said Harmer. “Add on cases with insufficient instrumentation can now be scheduled knowing that a timely solution is available with the use of ONE TRAY. If vendor trays are delivered late, time from sterilizer door close to open typically is less than 25 minutes instead of the traditional 2 to 3 hours waiting for trays to be dried and cooled after the sterilization cycle.”
Identify and track instruments
“As surgical devices have become more complex, instructions for use (IFU) are not just handy, they are a necessity,” said Marcia Frieze, CEO, Case Medical. “Equally important is the need to locate sets and supplies in real time and to identify those items requiring rapid turn-around. Case Medical meets the challenges of containing and storing surgical instruments by taking a holistic approach to instrument processing. We listen to the needs of users and develop products that address the needs.”
For example, in addition to their products for cleaning, sterilization, transport and storage, Case Medical offers a software program, CaseTrak360, that ties everything together, utilizing a 2D barcode for tracking and tracing. Beginning September 24, 2018, the Food and Drug Administration (FDA) is requiring unique device identification (UDI) compliance for direct marking of class II devices. Case Medical’s SteriTite universal container system is a class II device that has universal compatibility with all devices and sterilizers. The company now offers a bar code on its containers to meet regulatory requirements and provide added value, including alerts that automatically link to the OR schedule.
Address missing instrumentation
The assembly of surgical instrument trays is both a science and an art. As with any process in the CS/SPD, there is pressure on staff to assemble trays accurately but in an efficient manner so they are ready when surgeons need them. A major roadblock in the process is the discovery of missing or damaged instrumentation.
“The absence of organized methods and appropriate storage equipment for maintaining extra instrument inventories leads to significant amounts of wasted technician time,” said Braun C. Kiess, Director of Sales and Chief Financial Officer for RST Automation. “Current methods often require technicians to leave their workstations once or multiple times while assembling a single set to hunt for these instruments. This wasted technician time is not only costly from a utilization perspective but can lead to overtime because SPDs are often inadequately staffed.”
“Furthermore, it has also been our experience that additional money is wasted when instruments are purchased because of a lack of knowledge that they already exist in current inventories,” Kiess added. “While existing computerized instrument management systems contain inventory modules, they are often too time consuming to maintain.”
RST Automation has created an Assisted Instrument Management (AIM-Tray Assembly) system, which solves the problem of instruments missing from trays while significantly reducing the time spent searching for replacements. Utilizing machine vision technology combined with artificial intelligence, AIM automatically identifies instruments, verifies their presence in the set on count sheets and automates the assembly of ringed instruments onto stringers. Missing instruments are identified at the end of the assembly process and a list of missing instruments and their storage locations is printed for efficient retrieval of replacements for missing instruments.
Keep clean from dirty
With the tremendous volume of surgical instrumentation circulating around a busy hospital — from the CS/SPD to the OR and back again — staff members must have a simple and effective way to differentiate between clean and dirty instruments.
“One of the biggest challenges is proper communication while transporting instruments,” said Matthew Smith, Marketing Manager for Healthmark. “When transporting closed containers, it can be difficult to determine if the contents inside are clean or if they are contaminated. Using labeling products help identify if instruments and equipment are clean or dirty.”
Healthmark’s Transportation Identification Tags are designed for compliance with Occupational Safety and Health Administration (OSHA) standard CFR 1910.1030. The 3.125” x 5.125” tags feature one perforated tab, a green top tab with “CLEAN” in black text, a fluorescent orange/red bottom tab with “DIRTY” in black text, and the removable OSHA approved “Biohazard Label” adhesive backing.
“The Transportation Identification Tag is produced precisely for transporting materials considered a biohazard, while acting as an essential communication tool in the process,” added Smith. “By labeling a cart or container ‘biohazard’ upon its return to the sterile processing department, the Transportation Identification Tag assists in supplying information to the OR/Procedure Room. Furthermore it has a checklist for the surgical/procedure room/sterile processing team to ensure adequate delivery of the case cart or container in question.”
Save space
“CS/SPD personnel are constrained by tight spaces and are always seeking more efficient, space- and movement-saving storage devices,” said Tom Derrick, Senior Vice President for OpenMarkets, a marketplace for buyers and sellers of healthcare equipment.
MarketLab provides a simple space saving Accessory Arm that clamps onto any bench tops or workstations. The vertical nature of this allows for convenient instrument storage that’s great for open-concept floor plans.
Miami-based Quantum Medical is a manufacturer of a wide range of storage solutions, including sterile wrap carts available in multiple designs. The chrome carts include hang bars that keep sterile wraps separated and accessible for special preps. These bars are easy to adjust and feature neoprene gaskets to hold wraps in position.
Scope safety
The challenge of safely and effectively processing scopes is well known in the healthcare industry. While healthcare organizations, CS/SPD professionals and clinicians want to avoid patient harm from contaminated scopes, scope processing is no easy task.
“Bacterial growth within the internal channels of an endoscope is a challenge most CS/SPD departments face on a daily basis,” said Jen Bonzheim, Business Development Manager, Specialty Applications for Stanley Black & Decker’s Storage Solutions group. “Drying the endoscopes after every reprocessing cycle, both between patient procedures and before storage, is a requisite practice crucial to the prevention of bacterial transmission and nosocomial infections as cleaning and HLD (Kovaleva et al., 2013; Muscarella, 2006).”
InnerSpace’s Modular Endoscope Drying System (MEDS) provides forced HEPA-filtered air directly into the internal channels of an endoscope to assist in bacterial growth prevention. InnerSpace offers a completely retrofittable unit that will turn an existing or new InnerSpace cabinet into a drying system. The MEDS system is completely retrofittable, provides an automated drying cycle, and hands free operation while providing constant airflow through all of the internal channels of an endoscope. The HEPA filer provides a 99.97% retention rate of particles that have a size > 0.3 µm. The MEDS unit is compatible with Olympus, Fugi, and Pentax scopes.
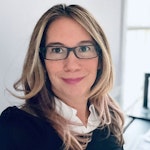
Kara Nadeau | Senior Contributing Editor
Kara Nadeau is Sterile Processing Editor for Healthcare Purchasing News.