Having a certified and thoroughly trained sterile processing staff is no longer just desirable but mandatory at a growing number of healthcare facilities. Central sterile/sterile processing department (CS/SPD) professionals play a vital role in patient care and safety; therefore, they require a level of training equal to their level of responsibility.
“I often say, ‘sterile processing is an entry-level position that requires high-level skill’ and today this is more evident than ever,” states Chris Franklin, CSPDT, CSIS, CFER, IU Health, the Certification Board for Sterile Processing and Distribution (CBSPD), The SPD Network. “As an industry we must strive to exceed expectations and continually improve training and education for sterile processing professionals.”
Unfortunately many CS/SPDs don’t have the resources necessary to support a comprehensive training program for their staff members. Often, it comes down to the department leaders to initiate training for their teams, or the individual team members themselves to seek out educational programs on their own so that they can keep up to date on the latest technologies and techniques, and earn industry certifications.
“People underestimate the training and skills need to do the necessary job of instrument processing,” said Marcia Frieze, CEO, Case Medical. “In fact, their job directly impacts the health and safety of patients, staff and the community at large. Once healthcare facilities were provided with funds for educational seminars and conferences, now the technician in most cases needs to pay to develop their skills and grow professionally.”
It starts at the top
Marcy Konja, CRCST, CSPDT, CIS, CER, CHL, CSPDM, Senior Director, Sterile Processing Operations and Quality Improvement, SpecialtyCare, says education must start at the top with CS/SPD leaders.
“Leaders have to foster and create an atmosphere where education and certification are sought after by employees,” said Konja, who has over 30 years of sterile processing experience in healthcare and industrial settings. “Leaders can provide educational opportunities onsite with in-person meetings or through online webinars that offer CEs for completion. Many leaders track and encourage tenured staff to participate in offsite seminars and even encourage them to become involved in presenting or participating in panel discussions. Invite staff to join a local IAHCSMM or CBSPD chapter and attend their first meeting with them. Don’t have a chapter? Work with them to create one!”
Melinda Benedict, MS, CFER, Manager, Infection Control Program, Olympus Corporation of the Americas, urges CS/SPD leaders to stay up to date with the multiple recommendations and guidance from various patient safety and infection prevention organizations, including the Association for the Advancement of Medical Instrumentation (AAMI), Association of periOperative Registered Nurses (AORN), American Society for Gastrointestinal Endoscopy (ASGE), U.S. Centers for Disease Control and Prevention (CDC) and Society of Gastroenterology Nurses and Associates (SGNA).
“They can also provide value in identifying available certification programs and communicating with hospital management and manufacturers about department needs and potential best practices,” said Benedict. “For example, a new offering by Olympus to provide channel air drying solutions for endoscopes was due in part to the willingness of CS/SPD professionals to adopt such measures in their facilities.”
Address individual needs
“The field of CS/SPD is constantly changing,” said Natalie Lind, Education Director for the International Association Of Healthcare Central Service Materiel Management (IAHCSMM).
“New technologies and changing regulations, standards and guidelines require us to develop education to keep professionals up to date on the latest information. At the same time, we need to ensure that we provide education to those that are new to the field and need to develop a foundation skill and knowledge base.”
As Lind points out, training CS/SPD professionals can be a challenge due to their complex work schedules; therefore, flexibility is critical when designing educational programs so that individuals can access the programs they need, when they need them. Lind states: “Education needs to be available at any time, on demand, because CS/SPD professionals work shifts that cover 24/7 and they must be able to access education when it is convenient for them.”
Furthermore, because individuals learn in different ways, it is important for the industry to offer a variety of programs to address various learning styles. Lind states: “Just as the field is changing, education is changing as well. We need to use various methodologies to address educational needs for CS/SPD professionals at all levels. That education should address various learning styles using whatever technologies are available. We also need to address educational needs of those that are unable to attend conferences, both local and national. Regardless of the type of facility, the science of decontamination and sterilization remains the same and we need to develop education that can reach everyone.”
Enlist an educator
“A key element for improving education and training in the central service and sterile processing departments is the presence of an educator,” said Casey Czarnowski, BA, CRCST, CIS, CER, SPD Educator, Fargo, ND “The influence of an educator, whether dedicated or shared with another department, will be most evident in the area of standardization. An educator has the time to study industry standards, track industry changes, and communicate with other professionals in the CS/SPD discipline and in the industry at large. The educator has the expertise to organize and effectively deliver the message of best practice to the technicians in their department. In this way, standards and changes are communicated to CS/SPD staff from one consistent source, supported by published standards and knowledge from subject matter experts in the field.”
According to Czarnowski, one of the best things he and his team have done at their facility is to establish a team of titled and compensated preceptors. Supported by the educator, preceptors carry out the daily training of technicians. These dedicated preceptors ensure that new staff can easily and immediately get answers to their questions, feel supported in the complex work of sterile processing and inventory management, and successfully acclimate to their facility.
“Through constant communication, the educator and preceptors work together to standardize their message to staff, ensuring that the work of the department is done in accordance with industry standards and with best practices in mind,” said Czarnowski.
Loraine Durigan, CRCST, CHL, CIS, CER, Materials Manager and CS Supervisor, Florida Hospital, believes every healthcare organization should have a dedicated CS/SPD educator on staff. She notes that the educator should be certified as a Certified Registered Central Service Technician (CRCST) or Certified Sterile Processing and Distribution Tech (CSPDT), at a minimum, and he or she should hold a second certification, such as a Certified Instrument Specialist (CIS) or Certified Endoscope Reprocessor (CER), to demonstrate his or her dedication to the profession. Furthermore, Durigan says the educator must have the flexibility to attend educational seminars, including the IAHCSMM Annual Conference and Expo.
“You have to have a dedicated CS educator on your payroll because the demands of the day-to-day process in a sterile processing department doesn’t allow a working supervisor the ability to effectively train staff on any new processes, products and technology,” said Durigan.
Franklin (The SPD Network) believes having a dedicated clinical educator specifically for the sterile processing department is an invaluable asset that can significantly improve department competency and confidence. He notes how an educator can effectively provide staff with the knowledge needed to successfully perform their duties in accordance with industry standards and regulations.
“Implementing such role can have a lasting and profound effect,” said Franklin. “Most importantly, I am a huge advocate for techs to become certified. Not only is mandatory certification gaining traction, but many techs that are certified tend to have a greater sense of pride and are likely to be more engaged in their work. Certification also requires individuals to actively seek out educational opportunities in order to maintain their credentials, this keeps techs on their toes and up to date.”
Engage with vendors
“In an ideal world having a sterile processing educator on staff would be a great way to ensure all SPD employees stay up to date on the latest education and standards. However, many facilities may not have the budget for such a position,” said Mark Duro, Director of Education, Crosstex. “It is still vital to keep staff up to date on education and training. If a designated education role is not possible management can rely on vendors and suppliers for educational programs pertaining to best practices and current standards.”
“In addition, it is important to have in-service education through the manufacturers of your surgical instruments, quality assurance products, reprocessing equipment, packaging/containment systems and sterility assurance products. A rigorous education schedule will ensure staff is proficient with all aspects of reprocessing,” Duro added.
As CBSPD Executive Commissioner Gail Law points out, many suppliers offer free continuing education programs for CS/SPD professionals. She states:
“Recently I attended a seminar that was offered at a local hospital and hosted by a vendor. This seminar provided information on the updates and changes to the AAMI ST79 standards. The seminar also covered several other relevant sterile processing topics. This seminar was free of charge, provided current knowledge and offered continuing education credits. In addition to vendors offering educational seminars, sterile processing certification organizations such as the CBSPD provide web links for continuing education. Finding a mentor that is passionate about sterile processing will also present a wealth of information.”
Durigan notes that her facility works very closely with its vendors and has taken advantage of any training opportunities they have to provide. Her advice to other CS/SPD professionals:
“Work with the those vendors that have free CEs to offer but make sure the content is relevant to your department. Because we have no formal education programs for certification in sterile processing in our area, we work with one of our repair vendors who provides an online schooling program free for our uncertified technicians to gain the education and tools needed to sit for the IAHCSMM CRSCT exam.”
Sandra Countley, Marketing Manager, Surgical Asset Management, Aesculap, feels it is imperative that the CS/SPD field partner with their instrument vendors in order to improve education and training for its professionals. “Partnering with vendors on training will not only enable you to standardize your processes, but also customize your care and handling practices to fit the needs of your facility,” said Countley.
In addition to instrument care and handling, Countley says vendor partnerships can help CS/SPD professionals increase their knowledge in the following areas:
- The benefits of proper preventative maintenance practices on surgical instruments
- The effects of water quality on instrument longevity and surface condition
- The cost impact of proper inventory management
- The expense and performance impact of sterile packaging (e.g., disposable wrap, reusable rigid container systems, etc.)
“I am pleased to say that the mission of Case Medical is to not only provide quality products and services for instrument processing and positive patient outcome, but to help our colleagues in SPD learn and grow professionally,” said Frieze. “Nancy Chobin, CEO of Sterile Processing University, encouraged us to do this years ago and has been a valued mentor to Case Medical for over 20 years. On a quarterly basis until this day Nancy has worked with us to present relevant educational presentations.”
Resources for CS/SPD training and certification
Aesculap Academy Educational Courses: Find a wide variety of course offerings, many of which are tailored to the continuing education needs of CS/SPD professionals. Visit https://www.aesculapusa.com/clinical_education_programs.
Case Academy Educational Courses: Access a variety of sterile processing educational courses with CEUs at no charge, including courses held onsite at healthcare facilities, at local IAHCSMM chapters, during national and international conferences, and online. Visit www.casemed.com.
Crosstex Educational Courses and Audits: Enroll in CE courses, onsite departmental education, CRCST scholarship programs, as well as complimentary departmental audits to help ensure implementation of current recommendations, best practices, and prep for external audits. Contact your Crosstex rep, or [email protected], or visit www.crosstex.com.
IAHCSMM Certified Endoscope Reprocessor (CER) Certification: IAHCSMM’s fifth and latest CER certification exam tests for proficient knowledge of transport, testing, cleaning, inspection, disinfection/sterilization and storage of endoscopes in accordance with industry standards, guidelines and regulations, and manufacturers’ instructions for use. Other certifications include the Certified Registered Central Service Technician (CRCST), the Certified Instrument Specialist (CIS), the Certification in Healthcare Leadership (CHL) and the Certified Central Service Vendor Program (CCSVP). Visit www.IAHCSMM.org.
Olympus Endoscope Visual Reprocessing Guide: The new Visual Reprocessing Guide for the TJF-Q180V endoscope users is a step-by-step video-guide that walks users through each required action in the cleaning of the endoscope. Based on feedback from reprocessing technicians, the user-friendly guide is available through the Olympus America online portal, OlympusConnect (other on-demand guides will follow). Also available is Olympus University featuring certificate courses for reprocessing and endoscope training. Visit www.olympusuniversity.com.
SpecialtyCare Sterile Processing Certification Course: A new Sterile Processing Certification Course helps hospitals find certified or experienced technicians. Piloted in Memphis, with the help of local hospitals, SpecialtyCare now hosts job fairs for interested candidates. Classes are six to eight weeks and include classroom work and hands on experience with SpecialtyCare’s preceptors.
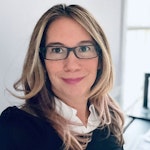
Kara Nadeau | Senior Contributing Editor
Kara Nadeau is Sterile Processing Editor for Healthcare Purchasing News.