Maintaining case cart & containers critical for safety, success
More facilities are embracing proactive instrument maintenance and repair programs, but industry experts agree sterilization containers and case carts aren’t always getting the same attention. It’s an all too common oversight that can jeopardize patient and employee safety.
“Case carts and sterilization containers should be treated like an instrument set and placed on a preventive maintenance program,” reminded Rick Schultz, author, inventor, lecturer and retired CEO of Spectrum Surgical Instruments Corp.
Contain the damage
Commonly-experienced damage on sterilization containers includes dented bases and lids, cracked or loose gaskets, and malfunctioning latches that can compromise sterility.
“When containers pop open by themselves, it’s a problem and should be treated as an open container,” said Elizabeth Franz, an educator and regional sales manager for Mobile Instrument Service & Repair. She stressed this problem is often ignored, despite the infection control-related implications of a compromised seal.
Proper cleaning and inspection after each use is critical. Sterilization containers, which are Class II medical devices, should be cleaned with a pH-neutral multi-enzymatic solution and then thoroughly rinsed prior to their next use. “The use of alkaline or acidic detergents and cleaners can strip anodized sterilization containers and render them unsafe for use,” said Marcia Frieze, President and CEO of Case Medical Inc.
Rough handling and improper cleaning are two leading causes of sterilization container damage, reminded Frieze. The devices should be cleaned with a pH-neutral multi-enzymatic solution, and then thoroughly rinsed.
“The use of alkaline or acidic detergents and cleaners can strip adonized sterilization containers and render them unsafe for use,” she warned. Proper handling requires careful inspection of all parts — a task that is typically included in the manufacturer’s instructions for use.
Filters also require focused attention to ensure they are not punctured (damage that can be caused by some retention plates), and filter retention plates can fall into the load if not properly latched.
“Using containers that are discolored, poorly sealed and dented means inspection has not occurred, or staff are not properly trained,” according to Frieze.
To ensure containers remain well functioning and safe for use, it is essential that manufacturer instructions for use are consistently followed and that all components, such as gaskets and filters, receive proper care and attention, reminded Troy Scroggins, Product Manager for SterilContainers, Aesculap Inc.
“If anything is out of line, it should be pulled [from inventory] and repaired.”
Roll away the risks
Improperly-maintained carts (and other rolling stock, such as Mayo stands, back tables and even I.V. poles) are being cited more frequently in regulatory audits, said Steve Dillon, Vice President of Surgical Instruments for STERIS Instrument Management Services. Staining, corrosion and hazardously-worn tape on surfaces are easily identified and cited during audits.
“Many facilities take for granted that very expensive and delicate items are transported through the facility in these carts,” he said, adding that if the casters are damaged, instruments inside can be jostled, shaken and damaged. This is especially problematic for rigid endoscopes due to glass rod lenses inside, cameras, and delicate and insulated instruments.
Schultz pointed out that dust, sutures, mop strings and dirt can easily collect on cart casters. Aside from possible infection control implications, poorly-maintained casters can impede proper functioning and steering, and lead to employee back injuries.
Cart bumpers are also commonly in need of repair, especially when constructed with rubber or plastic, which can allow for breaks and cracks that can harbor moisture and bioburden, according to Frieze.
Franz added that damaged bumpers are usually the culprit when cart doors don’t close properly.
“If the bumper material is damaged, [the cart] won’t travel correctly,” she said. “These are all easily identified, but like tires on a car, we often don’t look.”
To help prevent damage and promptly identify problems, rolling stock should be routinely inspected, properly maintained (e.g., keeping casters and wheel assemblies free of debris and well lubricated, ensuring that shelves are not overloaded, and verifying that latches are not loose or corroded), and repaired as needed.
And don’t forget the power of ongoing staff education. It’s the foundation for ensuring carts and containers remain in optimal condition, reminded Franz. “We don’t review SPD 101 enough. It should be reviewed for all staff members every six months.”
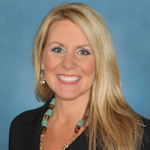