Preventative maintenance program tips
Janice Reed CRCST, Interim SPD Manager for B.E. Smith, offers the following tips to CS/SPD professionals when implementing a preventative maintenance program:
- Maintain strict adherence for checking all instruments thoroughly for cleanliness and malfunction.
- Maintain a backup inventory of instruments to be placed in trays.
- Maintain a designated bin for instruments that need repair.
- Implement and maintain a scheduled service bi-monthly or more often (depends on surgery schedule and budget) for preventative maintenance on all instrument sets and peel packed instruments.
- Have your preventative maintenance staff give periodic in-services on appropriate ways for checking instruments for malfunction.
- Make sure staff has necessary tools for doing the above task.
- Managers and supervisors: make sure yearly operating budget has designated dollars for preventative maintenance plan.
- Keep SPD communication lines open with surgeons, OR departmental staff, ancillary staff and administration.
Tips for testing scissors
Mike Vargo, Regional Product Manager, Surgical Instruments, STERIS Instrument Management Services, recommends a sharpness testing standards kit be placed at each CS/SPD professional’s workstation. He notes that many of the tests can be achieved using everyday material found in sterile processing departments and offers the following tips:
- Rongeurs should be able to cut through an index card.
- General scissors 4-1/2 inches or larger should cut smoothly through red scissor testing material while scissors 4-1/2 inches or shorter should cut smoothly through yellow testing material.
- Bandage scissors should cut smoothly through container wrap.
- Laparoscopic scissors should cut cleanly through tissue paper.
- Lap hook scissors should cut through a thick rubber band.
“Utilizing the correct medium is important for testing standards because you want to use a testing material that is similar to the intended use,” Vargo says. “When in doubt, alway err on the side of caution and remove it from circulation until your repair vendor can inspect it further.”
Instrument data management tips
Working alongside clinicians, Andrew Davison, Founder of Nomenclatura, and his team have discovered common themes across facilities when it comes to instrument data management. He offers the following tips:
- Instrument tracking software vendors typically only offer data loading — data cleansing is the responsibility of the CS/SPD.
- Instrument tracking project planning must include data cleansing activities — it’s the highest risk and longest task.
- Data cleansing is usually underestimated — be realistic, quadruple your initial figures (time & cost) and ensure your resource is dedicated full-time.
- Utilize the correct resources to perform inventory data cleansing — clinicians generally loathe this activity and often don’t have the required skillset.
- Never accept less than 95 percent unambiguous instrument records — corporate risk profiles help determine how high you must reach.
- Audit your data now — it’s too late once your Joint Commission survey has started.
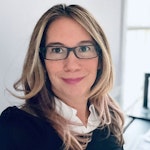
Kara Nadeau | Senior Contributing Editor
Kara Nadeau is Sterile Processing Editor for Healthcare Purchasing News.