Sterile expiration dates, addressing allergies with laundry service, daily performance tests
Submit your questions
email: [email protected]
phone: (941) 927-9345 ext. 202
Q The self-seal peel pouches that we use have an expiration date printed on the outside of each box. The individual peel pouches themselves do not have an expiration date printed on them but they do have a lot and product number on them. We follow an event-related sterility maintenance policy. Do I need to write the expiration date that is printed on the box of each peel pouch?
A I would check with your peel pouch manufacturer and get a written explanation of what the date on the outside of the box actually means. The date may not be sterile shelf life expiration. I know that for many manufacturers the date on the outside of the box is a best “use by date” which means the peel pouches should be put to into use by that date. Once sterilized the pouches then have an event-related sterile shelf life. The best use by date on the box is to ensure the self-seal adhesive has not been compromised by storage conditions over a prolonged period. It is very important that you follow the manufacturer’s instructions for storage conditions before use. High temperature exposure can cause the adhesives seals to form a strong bond to the package when run through a sterilization cycle. If you have written documentation from the manufacturer stating that post sterilization of the peel pouch sterile shelf life is event- related, then you would not need to place a sterile expiration date on each package. Of course you should continue to put a sterilization load sticker on each package. If by chance your manufacturer provides you with information that does not support indefinite event-related sterility maintenance and provides you with a post sterilization sterile shelf life for their pouches, then you will need to place an expiration date on each package.
Q I am the OR clinical supervisor and am responsible for our sterile processing area. I have an employee who claims to have an allergic reaction to the hospital scrub attire and believes it could be the detergents used by the hospital laundry service. Since we do not allow employees to take scrub attire home to launder, what would be the best way to handle this?
A I would confirm that the laundry service is a healthcare accredited facility. Accredited laundry services comply with stringent protocols which reduce the potential for allergic reactions to detergents and other laundering chemicals. Protocols require extensive copious rinsing which leaves very little if any detergent residuals on materials. I would meet with the laundry management, hospital infection preventionist and occupational health officer to address the matter and to determine if the laundered scrubs are the source of any allergens. If such is the case then corrective measures should be taken. I have heard of some situations where provisions have been made for highly sensitive employees to wear disposable scrub attire.
Q I am an RN business manager of perioperative services which includes Sterile Processing. Like every other hospital I am faced with the challenge of cutting costs without compromising quality care. The nurse manager of sterile processing insists on running daily performance tests of all the instrument washers. I fail to see the necessity for this, as all of the washers have very detailed printouts to ensure that they are performing and meeting all the cycle parameters. To me, this should satisfy AAMI requirements to monitor the washer’s performance on a weekly basis. We could reduce our budget by nearly $15,000 by eliminating the use of these unnecessary tests. That’s equivalent to a tech’s salary. She argues that the printouts are not adequate and that daily testing is the best practice. I would appreciate your position on this.
A AAMI ST79Section 7.5.3.3 and 10.2 states “…Mechanical cleaning equipment should be tested upon installation, weekly (preferably daily) during routine use, and after major repairs. The “preferably daily” note indicates that daily testing would be the best practice. The printouts are a means of monitoring the mechanical performance of the washers and are a valuable tool and means of cycle documentation. However they do not confirm other important factors of cleaning efficacy, such as adequate chemical concentrations, wash time specific to chemistry, water quality, temperature impact on chemistry performance, etc. Washer monitoring and testing is similar to the QA protocols applied to sterilizers. Sterilizers also have printouts for documentation of their mechanical performance but sterilization efficacy is monitored by the use of various monitors and testing devices (e.g., chemical indicators, test packs, air removal tests and biological indictors.) So kudos to your sterile processing nurse manager, I commend her/ him for wanting to provide the highest degree of QA of the cleaning process by doing daily monitoring of all instrument washers. If I were you I would look elsewhere for budget reductions other than compromising the quality assurance of your cleaning processes. I would also suggest that you assess your salary for sterile processing technician to be commensurate with the educational, skill, knowledge requirements and responsibilities of the critical role they have in providing vital services impacting patient safety and quality of patient care outcomes.
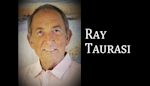
Ray Taurasi
Ray Taurasi is Principal, Healthcare CS Solutions. His healthcare career spans over five decades as an Administrator, Educator, Technologist and Consultant. He is a member of AORN, SGNA, AAMI and a past president of IAHCSMM. Taurasi has been a faculty member of numerous colleges teaching in the divisions of business administration, nursing, and health sciences. He is the author of numerous articles and textbook chapters; he is a frequent speaker at national and international healthcare conferences.
Note to readers from Ray Taurasi - In 2021, my life’s career path will transition to one of new opportunities and adventures. As a result, after nearly 19 years and 225 CS Solution columns, this edition will be my last.
“All changes, even the most longed for, have their melancholy; for what we leave behind us is a part of ourselves; we must die to one life before we can enter another.”– Anatole France
I wish you and your loved ones a healthy and joyful holiday season and a beautiful New Year! God Speed, Ray
https://www.facebook.com/pages/category/ Local-Business/Healthcare-CS-Solutions-128857 3061153887/ • email: [email protected]