Finding ‘Time’ in Lab Supply Chain
It’s an all-too familiar challenge in healthcare, escalated by the pandemic and explored in healthcare settings across the continuum of care: How do we do more with less?
In many clinical laboratories, the call to operate lean is increasingly addressed by giving more inventory management responsibilities to skilled lab technicians -- lab team members who have the technical or scientific training to contribute directly to providers’ ultimate objective of delivering positive patient outcomes.
The Centers for Disease Control and Prevention states that 70 percent of medical decisions include lab data that informs patient diagnosis and treatment. Furthermore, a health system’s lab service line typically has more patient interactions than other lines in that system. Yet, from what we at Medline are seeing from working with providers across the country, more and more lab tech time is being consumed by tasks non-specific to lab testing -- such as ordering and tracking supplies and receiving and organizing materials.
How can lab teams find more time on the bench and less in the storeroom?
Conduct a review of existing operational procedures and processes in the Lab. Internally, or with an objective third-party partner, take the time to observe and analyze what happens in the Lab during a typical week. Note the time required to complete all lab functions - from testing set-up and clean-up to ordering replenishments and putting away inventory. Remember to include the minutes techs need to get to-and-from supply rooms as well as time required to locate and gather materials in specific supply areas.
Tracking time spent on non-testing-related activities will inform decisions like where high-use products should be stored, what should trigger replenishments and who should handle ordering, and whether a storeroom needs more signage or be re-engineered altogether.
Evaluation of the type and quantity of tests and protocols that are performed in the lab should also be included in a lab review, directing the subsequent removal or addition of lab supplies as necessary.
Lab leaders get a more accurate view of the total cost of Lab with every review.
Research and tap into experience and supply chain resources from service lines and departments within the current facility or system. Other in-network teams or divisions -- like acute, emergency, periop and others – facing cost pressures and focused on improving efficiency may already be working with a supply chain partner or have inventory solutions that can be scaled cost-effectively to include Lab.
Invest in time-saving technology and services. Weighted bins, electronic shelf labels and RFID tracking for high-value devices are examples of materials management technology that can be implemented to free lab technicians up for more high-value, bench work. Ordering platforms that integrate with current ERP can reduce time in front of inventory screens. The best technology can minimize human interaction required for repetitive, low-value activities. The best service providers minimize lower value-added tasks from skilled lab technician responsibilities. Outsourced or supplier employees that provide inventory services can often provide fractional cost solutions that are an even more efficient use of funds.
By conducting a review of lab procedures and processes, tapping into existing organizational resources and investing in technology and services, lab leaders can build supply chain resiliency and find more time on the bench for their lab teams.
What may start as an exercise in finding more time on the bench can ultimately translate into a more fulfilled and productive lab workforce, more consistent and accurate lab work, and increased lab thru-put and contribution to a healthcare organization that will glean the attention of leadership and C-Suite.
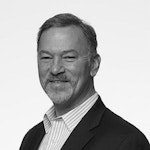
Peter Saviola
Peter Saviola, vice president of Logistics and Supply Chain Optimization, Medline