Effectively processing surgical instruments is itself a tremendous challenge where central sterile/sterile processing department (CS/SPD) professionals must employ a variety of skills (e.g., science, manufacturing principles, operations, customer relations, etc.) to get the job done. And the responsibility doesn’t end when a product is sterilized — CS/SPD staff members have to ensure that instruments are stored and then transported to the operating room (OR) in a way that protects them from damage and maintains their sterility, often within the limitations of tight, outdated spaces.
Another important consideration is protecting staff members from harm. For example, while the Association for the Advancement of Medical Instrumentation’s (AAMI) guidelines state that no loaded tray should be heavier than 25 pounds, it’s not uncommon for CS/SPD professionals to handle orthopedic trays that are far heavier.
To keep instruments protected and free of contaminates during storage and transport, and protect CS/SPD technicians from on-the-job injuries, there are many options available.
Take holistic approach to storage and transport
According to Case Medical CEO Marcia Frieze, because CS/SPD staff face many challenges when containing and storing surgical instruments — instrument damage, sterility maintenance, turnaround, identification of contents, transport, staff and patient safety — they must take a “360-degree approach” that addresses all of these issues.
“At Case Medical, we take a holistic approach to containers and storage solutions by considering how products are used and to ensure that information is readily available to address any concern,” said Frieze. “What is critical is proper reprocessing of items and maintaining the sterility of these items until they are used for patient care.”
Case Medical offers a complete set of solutions that support sterility maintenance during storage and transport. This includes:
- Containers that are universal, corrosion resistant and compatible with all sterilizers and devices based on manufacturers’ instructions for use (IFU).
- Case carts that are designed for containers and supplies to fit properly, and have perforated, smooth shelves (no wire). This design feature avoids tears when wrapped sets are pulled or placed in storage.
- Disposition monitor with locking feature that differentiates “clean” and “biohazard” or used sets placed in closed case carts.
- Tamper evident seals that not only secure the container contents, but can also identify processed sets that are ready to go and a biohazard seal to identify those that are soiled and must be reprocessed.
- CaseTrak360 software program, which provides tracking, tracing and instructions throughout the reprocessing cycle. Sets are identified and labeled and then tracked via 2D barcodes using the CaseTrak360 solution.
Maximize your space
Many CS/SPD professionals said their greatest challenge is a lack of space needed to contain and store insrtuments properly. Spaces built years or decades ago often cannot accommodate the growing number of surgical instruments required by today’s ORs.
“When a department is loaded with instrument sets and sterile supplies it impacts the workflow within the department,” said Ian Loper, Vice President of Sales & Marketing for Distribution Systems International (DSI). “Blue wraps are then stacked on top of one another making it hard for the staff to ergonomically pull inventory for cases, and the bottle necks within the department build, which impacts the overall efficiency and productivity of employees. Ultimately the department becomes fundamentally compromised and out of compliance. When stacking blue wraps it increases the chance of tears and compromises the sterility of the sets. From our findings, there is often too much inventory and not enough space to effectively manage and store the valuable instruments.”
DSI’s High Density Container Tray Storage Systems are highly effective in consolidating valuable instrument sets into a smaller footprint, which saves a CS/SPD 30 percent of its valuable floor space, according to DSI data. By consolidating the rigid containers and blue wraps into a small space, the CS/SPD can store more sets, open up the aisle space for egress compliance, avoid stacking blue wraps, and easily identify the correct sets when needed. DSI’s ergonomically designed shelves are easily pulled out of the storage system, which not only improves workflow but also enhances staff safety when they are storing and handling heavy orthopedic sets. The system also includes dust covers, the option of stainless steel pullouts, and low profile stainless steel wire shelves.
Go vertical
David Phillips, Marketing Manager for Hänel Storage Systems, explains how most CS/SPDs are out of space because they are landlocked, have a low ceiling height, inefficiently use their space, or have a combination of these issues. Another factor is the growth in tray quantity due to the increasing complexity and number of orthopedic cases.
“If SPDs utilize automated vertical storage to store their containers, they use the entire vertical height of the room, which saves valuable floor space and delivers containers to the staff at an ergonomically correct height,” said Phillips. “The former storage space can be used for other purposes, and costly on-the-job injuries caused by heavy or overweight containers can be mitigated.”
HänelSoft Inventory Control Software in the CS/SPD storage areas of a hospital, integrated with Hänel Rotomat Vertical Carousels, produces space savings, productivity enhancements and inventory control and security. With HänelSoft controlling the details of container turnover (first in-first out), expiration, location and available quantity, there is no more need to worry about compliance and where an instrument tray is located. The ability to quickly search across container identifier, set number and set description with an easy-to-use, web-based interface adds to the system’s productivity. HänelSoft not only has the capability to manage the Rotomat’s inventory, but can also be expanded to track inventory on external shelving, carts and more.
Meet customer demands
Troy Scroggins, Product Manager, SterilContainer Systems, Aesculap, points out how the right instrument storage solutions and containers can help CS/SPD professionals meet the demands of the OR, which needs the right instruments, in the right condition at the right time.
“Holes in sets, lack of reprocessing efficiency, missing or wrong instruments (due to poor organization/optimization), and dull or broken general and specialty instruments can all lead to case delays, as well as higher costs,” said Scroggins.
The Aesculap SterilContainer System has a rigid bottom that cannot be penetrated, punctured or torn; reducing the chance of case delays. The container system can be used with a wide variety of baskets, racks and instrument organization system (IOS) holders/components to organize and secure instrument sets. All of which can be used to sterilize pre-configured orthopedic, spine and specialty medical device instruments. Aesculap also has a wide variety of baskets, racks and instrument organization system (IOS) holders/components to organize and protect instrument sets. They can be used to sterilize pre-configured orthopedic, spine and specialty medical device instruments.
Get organized
Drawing upon his past experience of being an CS/SPD technician, Marcus Super, CCSVP, Director of Sales & Marketing for Summit Medical (now an Innovia Medical Company), recalls that one of the greatest challenges he faced was the lack of proper trays as it relates to instrumentation handling and longevity.
“SPD staff manage a large variety of instrument trays, most of which are not designed to properly organize and protect instrumentation throughout the use cycle,” said Super. “When you lack in this area it negatively impacts instrument organization, sterility and cleanliness, and can even cause instrument damage, as well as propose potential risks to staff. A messy tray can be the root cause of instrument-on-instrument damage, instrument tip damage from poking through a basket, a punctured sterile barrier, lengthy reprocessing times and possible injuries during the decontamination process.”
Summit Medical’s customized InstruSafe Instrument Protection Trays are made of durable, highly perforated aluminum and silicone instrument holders that lock down delicate instruments with 360 degrees of protection during sterilization, transportation, storage and in the OR. InstruSafe Trays are constructed with strong, quality materials to reduce breakage and frequent replacement, as well as to meet a facility’s unique instrument set needs. With a variety of FDA 510(k) sterilization cycle clearances, these trays are a smart, easy upgrade for use with both wrap and rigid containers.
Protect your assets
Hospitals and other healthcare facilities invest hundreds of thousands of dollars in surgical instrumentation. Mismanagement of this critical asset can lead to costly repairs, repurchases, excess inventory, and in some cases, a surgeon not having what he/she needs for a case.
“When hospitals have inventories in the tens of thousands of surgical instruments, keeping them in good working condition is critical to keeping costs down in the SPD,” said Alicia Diaz, Product Marketing Manager for BD. “During assembly and storage, instruments may become damaged due to accidental dropping of trays and/or mishandling. Rigid sterilization containers can provide protection against damaged instruments as well as sterility maintenance. These systems offer a trusted method to store sterilized instruments until they are ready to use. With container accessories, containers can be customized so instruments can be secured and organized within the container basket. Rigid sterilization containers provide peace of mind that instruments will be protected and organized until they are ready to be used.”
BD Genesis low-temperature sterilization containers help protect and organize heat and moisture-sensitive surgical instrumentation during low-temperature sterilization. They are available in a variety of sizes to accommodate a facility’s surgical inventory. Low-temperature compatible baskets and accessories are also available to help organize instrument setup. The Genesis container system consistently provides a return on investment and is a green alternative to sterilization wrap.
Maintain sterility
CS/SPD professionals spend a tremendous amount of time and effort processing surgical instruments in an effort to ensure sterility at the time of use on a patient. As Lindsay Brown, Clinical Education Manager at Key Surgical, points out, the diligent work the staff has done leading up to sterile storage could be compromised if the containment devices used or the sterile barrier created don’t function as intended.
“It’s easy to, in a way, check out of the process once a package is sterilized and say to yourself ‘I’ve done all I can do for these instruments so I’m moving on’ and give little consideration to the truth that the sterile barrier applied prior to sterilization still has a hugely important job to do,” said Brown. “Sterile packaging and containerized systems have intended uses. Instrument sets and devices such as scopes have specific baskets that are designed to give the best results during sterile storage and transportation in terms of protecting that investment. Knowing how to properly choose, apply and trust your process as a CS tech is where the challenge lies.”
According to Brown, scope baskets from Key Surgical are the perfect containment device to use in the sterilization process of rigid scopes. Constructed of durable stainless steel, the baskets feature fixed silicon brackets that help hold a rigid scope in place during sterilization and transportation. A fully removable lid allows for easy placement of the scope in the basket. The lid slides into place on the basket and locks with an easy-to-use locking mechanism. The baskets are available in various sizes, with the largest basket including a small mesh basket to hold scope accessories. They are compatible with steam, EtO and gas plasma sterilization.
Keep it covered
“The most important job after reprocessing instruments is making sure they remain safe and ready for use,” said Matthew Smith, Marketing Manager for Healthmark. “Storing reprocessed healthcare products appropriately is crucial to avoid environmental contamination and compromise of any packaging. Items like our new ‘Clean Bags’ have been created to keep items covered after reprocessing. Efficient labeling is also an important factor. Easy identification of contents and ‘clean’ status takes the guesswork out of which items have been reprocessed and which items have not. These bags are ideal for transportation and storage.”
Healthmark Industries’ designed its new self-seal CLEAN Bag to keep items covered after reprocessing. The 8” x 14” tamper evident self-seal bags are clear and printed with “CLEAN” in green lettering for easy identification of contents and “clean” status. According to the company, they are ideal for transportation and storage.
The safety of sealed
“Sterility maintenance continues to be a hot topic in many CS/SPD departments,” said Mike Faulkner, President of Sales, Innovative Sterilization Technologies. “Both rigid containers and wraps present unique challenges when it comes to maintaining sterility.”
Faulkner says the unique technology behind the company’s ONE TRAY System makes it a “truly sealed container.” He adds that ONE TRAY features a lifetime warranty. If the product is damaged, the customer can return it to Innovative Sterilization Technologies’ Ohio-based manufacturing facility, where it will be repaired to factory specifications. If the ONE TRAY cannot be repaired, the company will replace it.
“That technology, combined with our lifetime warranty, gives you peace of mind that each ONE TRAY is continually providing optimal sterility maintenance,” Faulkner added. “No more questioning the integrity of your rigid containers, postponing/cancelling surgeries due to the inherent issues with wraps, and no more investing in new trays to replace the ones that are beyond repair.”
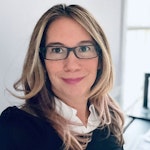
Kara Nadeau | Senior Contributing Editor
Kara Nadeau is Sterile Processing Editor for Healthcare Purchasing News.