There is broad industry awareness of the need for certified central sterile/sterile processing department (CS/SPD) professionals, but what goes into training a topnotch technician? HPN puts the spotlight on CS/SPD departments that have implemented robust certification and training programs for their staff, and the various resources these facilities are using to grow and nurture capable, knowledgeable teams.
Tie the two together
Weston “Hank” Balch, Director of Sterile Processing at University Health System in San Antonio, believes training and certification are inseparable and must be tied together in order for a department and its staff members to be successful. In his department, certification materials are integrated into the technician training process, including the International Association of Healthcare Central Service Materiel Management (IAHCSMM) Certified Registered Central Service Technician (CRCST) textbook and the Certification Board for Sterile Processing and Distribution (CBSPD) study guide.
During the 90-day on the job training program, techs also learn from the American National Standards Institute (ANSI)/Association for the Advancement of Medical Instrumentation (AAMI) ST79, and from Association of periOperative Registered Nurses (AORN) guidelines. Balch notes that during the training period, his department provides techs with time on the clock to study for the certification exam. Each week they set aside one to two hours where techs can study the exam materials and then ask preceptors informed questions on what they have learned.
“Unlike other fields like surgical technology or nursing where you have to take a credential, licensure exam before securing a job, this is not a requirement for sterile processing professionals in most states,” said Balch. “As we grow in our own professional space within the healthcare industry, it makes more sense to view certification in the context of training — that it is non-negotiable. There should be no such thing as completed training that doesn’t take into account this industry’s standard certification model.”
Walk the walk
Damien Berg, 2017 President Elect IAHCSMM, Manager, Sterile Processing, St. Anthony Hospital in Lakewood CO, believes CS/SPD techs must feel appreciated and have pride in their work in order to succeed. To foster this kind of culture in a department, Berg says managers must not only “talk the talk” but also “walk the walk.” This means working side by side with techs during each stage of the process in order to truly understand their work and the challenges they face.
“To me the job of a manager is to figure out three things,” said Berg. “The first is to determine what training techs need by actually doing the job with them. Second, find out if they have the tools they need to do their job properly, such as brushes and sinks in decontam and inspection tools in assembly. Third, assess barriers to the job. For example, if there are constant distractions or if the workspace is cluttered, this can impact efficiency.”
“If you take care of your staff and gain a true level of understanding of their work, then all of the other pieces will fall into place,” Berg adds. “It’s important to have a good compensation program, and a good training/education program that compliments it, but you must also have staff that care.”
Prioritize
When implementing a CS/SPD training program, Berg recommends that managers start with the “low hanging fruit,” such as high volume trays/instruments that techs are not getting right and are frustrating to the customer — the operating room (OR) or whatever department the CS/SPD is servicing.
“Think about the calls you receive from the ORs or clinics when your department is missing the mark on something, and then develop a training program around that,” said Berg. “If you take a shotgun approach and start training on random stuff then you’re missing the mark. Start with those issues that are bothering the customer. Get those out of the way, fix them and don’t repeat them.”
From there, Berg suggests that managers move to high-risk devices, such as flexible scopes or other items that the department is called on to process less frequently. He points out how if the department is always getting the simple items wrong, it will be a greater challenge to move onto these more complex devices.
“After I get the simple stuff out of the way, I lock it in and make sure we are getting it right. I can then develop a robust training program for these more complicated items that we see only once or twice a month,” said Berg.
Standardize Processes
Carmen Ferriero III, MBA, CRCST, Infection Control Account Manager, Getinge, likens sterile processing to a manufacturing process, and notes how standardization is key to producing an effective product — in this case safe and sterile instruments — in an efficient manner.
“I travel around a lot in my new role and see a lot of departments but unfortunately I still see many inconsistencies,” said Ferriero. “One tech will process instruments one way during the morning shift, and then a different tech will come in at night and do it the opposite way. Gaining consistency is a huge challenge in departments where you have a lot of people, three different shifts, a lot of personalities and many veteran employees who are used to doing things their own way.”
When structuring training programs, Ferriero recommends that managers develop a consistent process so that everyone – both new employees and veteran staff – is trained in the same manner. That way, they are all producing the same high quality, sterile product.
Cultivate preceptors
When developing their CS/SPD training and certification program, Casey Czarnowski, SPD Educator and his boss at Essentia Health Hospital in Fargo, ND, felt it was critical to gain input from those who would be taking part in the program — the techs themselves. They asked the techs what they wanted in a preceptor in terms of qualifications and experience. The response was that they wanted individuals who were not only certified, but also had one year of experience working in their department.
“It’s our belief that a successful department has a cadre of experienced and dedicated trainers that can bring employees through the difficulties of not only getting ready for the exam, but also gaining hands on skills,” said Czarnowski.
At Essentia Health, they have developed a 19-week CS/SPD tech training program that covers four different areas of the department. Techs are given an IAHCSMM textbook and study guide, and are assigned dedicated chapters to read during each step of the training. Along the way, Czarnowski or one of the department’s preceptors conduct quizzes and progress tests based on the actual questions for the IAHCSMM certification exam. Techs are required to gain their certification within 18 months of hire. While the training program is based on the IAHCSMM materials, the department accepts CBSPD certification as well.
When Czarnowski joined Essentia Health Hospital, only two or three techs were certified, but today, 16 out of the 31 full time employees have earned their CRCST or CBSPD certification, and eight of those have gone on to earn IAHCSMM Certified Instrument Specialist (CIS) and/or Certified Healthcare Leader (CHL) certification. Czarnowski attributes this success to the dedication of the staff in the department.
Marjorie Wall, Director of Sterile Processing at Citrus Valley Health Partners, has built a structured 1:1 preceptor onboarding program for her organization. It includes all areas of CS/SPD and beyond — from decontamination, high-level disinfection, assembly, inspection and sterilization, all the way through to supply distribution and management, and capital equipment management. The program features a variety of learning modalities, including PowerPoint presentations, online modules, written tests, direct observation and one-on-one training.
Each new hire to the department must complete this training program. He or she is assigned a one-on-one preceptor to guide them through the process. Wall notes that even those who have prior experience at a different facility and those who are certified must complete the program so that they learn the organization’s specific processes, which are based on AAMI guidelines and manufacturers’ instructions for use (IFUs).
“Citrus Valley had a high employee turnover rate in CS/SPD when we started this program but since its implementation our retention rate is stable — I’m not losing people,” said Wall. “Although the organization has had to invest staff time and resources into the training program, we get a return on our investment by not having to rehire and retrain techs every six months. It has also helped us retain long-term employees, who are now the ones serving as preceptors. Since we started this program they have become very engaged and feel empowered by the ability to pass on their knowledge.”
Offer incentives
According to Czarnowski, Essentia Health Hospital’s leadership feels strongly that certification is an important part of the organization’s culture across the board because it contributes to improved patient care and safety. They are now offering incentives to staff members who gain professional certification. Beginning in July 2017, individuals who earn a certification that is relevant but not required for their position receives a bonus. And if they maintain that certification, they will be granted a bonus yearly. Essentia Health Hospital also reimburses CS/SPD techs for the cost of the certification exam when they successfully pass it.
“This is our hospital’s upper management deciding that certification is good for our patients and encouraging our employees to pursue it,” said Czarnowski. “We compensate for certification, preceptorship, and give bonuses for advanced certification. As an educator working in a health system, I wouldn’t have it any other way. I think if you are going to require certification, which I think you should, then you have to compensate people for that.”
Collaborate
Berg says collaboration with the OR staff is another important part of CS/SPD training. At St. Anthony Hospital, CS/SPD techs spend time in every type of procedure for which they process instruments. From case opening until close, the CS/SPD techs work with the scrub techs to understand how instruments are used on the patient. In the CS/SPD there is a chart on the wall where techs check off which procedures they have observed to ensure they have the chance to rotate through all of these cases.
“This builds not only awareness of what happens in the OR, but also team work between OR and sterile processing,” said Berg. “The scrub techs, doctors and nurses begin to train my staff for me — how things go together and are taken apart — this compliments the training that we provide in the CS/SPD and completes the picture. And it has a secondary effect — when a tech makes a little mistake, such as forgetting something minor in a tray, the OR staff doesn’t escalate the issue up because they can tie a face and a name to it.”
Wall notes how the relationship between the CS/SPD and OR teams has improved at Citrus Valley Health Partners as a result of their training program. She states:
“Probably about nine months into the process we found it wasn’t just the SPD staff that had this great improvement, it was also the relationship between OR and SPD. The investment in people and all of the conversations that we’ve had with the OR have addressed many of the problems we were facing. It has improved the operations of the department — the way our employees interact with the OR — because even if we don’t have what the OR needs, the newly trained staff understand the urgency and take steps to get them what they need — it has improved that whole dynamic.”
Keep it going
“They key to training is that people get complacent — that is human nature — so training needs to be on a weekly – if not daily — basis where you are either learning something new or reinforcing current skills,” said Ferriero. “In the healthcare field things change by the minute. So let’s go back and assess how we open up instrument sets at the sink or load our washers — let’s review best practices. Get staff conditioned to the fact that at a certain time every week you have a training session on something. Having that focus on continuous improvement sets a department up for success.”
At University Health System, Balch and his team have found that a “constant quiz mode” has been quite successful for their department. During weekly staff meetings they present slides that include multiple-choice questions from certification practice tests. The techs win giveaway bags or other small prizes if they answer the questions correctly.
“It is one of the few times as a group that we can gauge how strong we are in certain areas and how confident we are in our own professional knowledge,” said Balch. “Obviously the ones who are certified knew that content at one time but for anyone who has taken a test, the difference between what you knew the day before the test and what you know a year later can be worlds apart. These quizzes are one way we can help our staff retain knowledge.”
At Citrus Valley Health Partners, Wall’s department participates in an in-service once a week or once every two weeks as a way to drive continuing education. To relieve the burden of managers, and at the same time bolster the knowledge and confidence of staff members, Wall recommends that a department’s “superstar employees” perform the in-service.
“Recognize your expert employees and develop that team environment between your new people and more experienced people,” said Wall. “Also leverage your vendor relationships. If your team doesn’t have the bandwidth to come up with its own in-service every couple of weeks, then have your vendors do some. It’s also important to note that an in-service doesn’t have to be an hour in a conference room. It can be a quick 15 to 30 minute session — everyone can do that.”
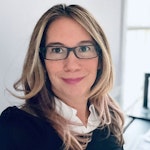
Kara Nadeau | Senior Contributing Editor
Kara Nadeau is Sterile Processing Editor for Healthcare Purchasing News.