Strategies for attaining a CS culture of excellence
In healthcare, where patient outcomes are at stake, Central Service (CS) departments must strive for excellence — each day, for each instrument and for every case. Creating a culture that allows excellence to grow and thrive is paramount to attaining that goal, and the facilitation and implementation of such a culture depends upon every CS leader and technician.
During her May 7, 2017, educational session at the IAHCSMM Annual Conference & Expo, Monique Jelks, Sterile Processing manager at Riley Hospital for Children at IU Health in Indianapolis, offered her top tips for building a culture based on positivity, effective engagement and enduring quality. For CS managers, she stressed the importance of stepping outside the office and working alongside technicians to gain a better understanding of each individual’s interests, likes and dislikes, and the team’s daily schedule, challenges and successes.
“Leaders are driven by data, but the problem is many don’t understand the balance of connecting that data to people,” Jelks explained. “Leaders who engage [their team] will find they have better data than they have ever had before.” She added that leaders who regularly engage their employees will be well respected and will quickly discover pertinent information that can help the department enhance its quality delivery. Leaders will learn which team members like to teach (a skill that can lead to effective mentoring and team leadership opportunities), which teammates are flexible and which ones are motivators, for example.
Building a culture of excellence also relies on a fair and balanced leader who creates rotating assignments through the department. Jelks used the example of a veteran CS professional who might feel they are exempt from working in decontamination because of their tenure or seniority — a scenario that only serves to bring down morale and stymie excellence. Instead, it’s these veterans who should step up and become the teacher in all departments to share their years of knowledge and experience.
Positive feedback should also be a top leadership priority, as should arranging for daily team huddles (including more detailed communication handoffs during shift transitions) to ensure team members across all shifts are informed.
“Leaders should pay attention to the details, even the small ones,” said Jelks, adding that if a team member says the departmental lighting seems too dim, for example, the manager should call Facilities and ensure a lighting fixture is replaced with a brighter bulb. “It really is the little things that drive engagement and help create great teamwork.”
Traits of a quality-focused team
A team of technicians may have very different personalities and work styles; however, those differences can add to a culture of excellence — as long as each team member focuses on understanding versus judgment, problem solving instead of complaining, and assisting instead of criticizing or bossing.
“We’re all different. We all don’t do things the same exact way, but that’s okay, as long as everyone follows the standards,” reminded Jelks. If a co-worker isn’t following standards, manufacturer instructions or policies and procedures — or otherwise seems to be struggling on the job, she said a culture of excellence will lead colleagues to readily offer assistance, rather than finger point and complain.
“If you complain without offering an idea for a solution then you’re part of the problem.” The same can be said of listening without the intent to fully hear or understand, an all too common occurrence that can erode teamwork and communication, and prevent the flow of pertinent information.
“The most important thing we can do is share our knowledge. We need to be sure we’re creating a culture of excellence instead of a culture of exclusion,” said Jelks.
That knowledge sharing must also extend beyond the walls of CS. If a challenge arises, such as Labor & Delivery sending instruments to CS without precleaning at the point of use, for example, the CS team can use that as a solid teaching moment done in the spirit of teamwork, as opposed to blame casting.
Jelks stressed that CS professionals must find creative ways to explain what they do, why they do it and why it is important. Sharing standards is valuable; however, it’s important to identify the standards-making body by its full name to avoid confusion and help pull them on board. Quickly referring to AAMI standards is a prime example. CS customer departments should be told what AAMI stands for so they recognize its importance in regard to standards.
Of course, knowledge sharing is a two-way street. Whenever possible, Jelks recommends having a technician observe an actual procedure so they can see the instruments in use and how critical it is for the surgical team to have the correct, well-functioning devices available when the patient is on the table. She has also seen tremendous success in having surgical services leaders and surgeons offer their own educational presentations to help CS gain a clearer perspective on instrumentation needs.
These presentations are not meant to be complaining sessions, but [rather] culture of excellence sessions where everyone is working toward the same goal of ensuring quality and promoting a spirit of teamwork, she said.
Last, but not least, conducting audits to measure success, problems and areas for improvement will ensure the quality mission continues long term. Checking to ensure all rigid containers have locks and filters in place is just one aspect a CS department could audit to promote quality and service excellence. Auditing is important because if errors occur, you can measure things that are perceived to be a problem.
“You don’t change processes based on perception. Measured data from audits removes the guesswork.”
Although excellence is a goal every department should strive to attain, Jelks reminded that it does not equate perfection. “Excellence doesn’t mean we’re perfect. It just means we are measuring what we do and how we do it.”
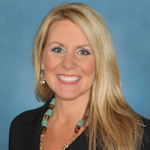