Good repair vendor relations improve safety, cut costs
Healthcare facilities are jeopardizing both patient safety and budgets if they aren’t partnering effectively and proactively with their original equipment manufacturers and third-party servicing companies. That’s because quality- and customer-focused vendors have the knowledge, resources and insight to provide ongoing training to Central Service (CS) and Operating Room (OR) professionals, and share valuable tips and strategies for keeping instruments properly maintained and rotated, and in good working condition.
As Rick Schultz, author, inventor, lecturer and retired CEO of Spectrum Surgical Instruments, explained, this education must address on how to properly decontaminate, select the appropriate cleaning brushes and inspect the devices. He also recommends staff-led training where CS employees “take ownership of the process and become the teacher.”
Maintaining well-functioning instruments also requires a facility to implement a proactive preventive maintenance schedule. Unfortunately, many facilities fail to look at maintenance from a full inventory standpoint. “Many times, they are just servicing sets that are available and ‘down for reprocessing’ in the department when the service team [arrives],” said Daniel DeShane, Regional Product Manager, Surgical Instruments, STERIS Corporation. “This is not the best way to use budget dollars and it leads to surgeon satisfaction issues, patient safety concerns and higher spend on new equipment purchases.”
Establishing a maintenance schedule based on set usage is more effective than a “set time interval” approach, reminded Steven J. Adams, RN, CA, CRCST, RN Manager of Central Sterile Processing at Sinai Hospital of Baltimore. He explained the benefits this way: A facility might own five minor instrument sets. Depending on the number of surgical cases that rely on this type of set, as well as the way inventory is rotated, some sets may be used 100 times or more if a repair interval is set for every six months, whereas the other sets may only be used 15 times or so. After 25 or 30 uses, the cutting tips of scissors, for example, may begin to dull. “Those sets will continue being used until the six-month interval is reached,” said Adams. This could lead a surgeon to use scissors that tear human tissue instead of cutting it cleanly.
It’s also important to understand that set time interval repairs will have a negative impact on the bottom line if rarely-used devices are being subjected to the same repair and maintenance schedule as frequently-used sets/instruments. “If sets are flagged according to their use, proper maintenance can occur before problems arise,” Adams noted.
Tracking the benefits
Computer-based tracking systems can help CS departments better monitor device usage and streamline their preventive maintenance efforts. Tony Thurmond, CRCST, CIS, CHL, Central Service Manager for The Christ Hospital Health Network in Cincinnati, OH, has seen firsthand how such systems can benefit CS departments and their collective organizations. “Instrument tracking has the ability to notify the technician when an instrument or tray is due for refurbishing,” he said. And the benefits don’t end there. The systems also have the ability to place messages for the technician regarding vital information on cleaning, inspecting and processing an instrument. “This allows us to catch problems, such as dullness and damage, early.”
Because not all servicing companies are created equally, Schultz stressed the need for due diligence when exploring and researching the options. Peer networking and IAHCSMM chapter involvement can prove highly effective for CS professionals to discuss vendor selection and their performance, as well as best practices and regulatory issues, he said. “Partner with your repair vendor or other vendors and encourage them to sponsor chapter meetings and supply a speaker and food. If a local chapter doesn’t exist in your [area], I encourage you to partner with your peers and IAHCSMM to establish a new chapter.”
Don’t overlook carts and containers
Another word of advice to CS professionals is that case carts and instrument containers deserve the same meticulous care and attention as the items placed on or inside them. Containers are medical devices and have a direct impact on patient safety. “An improperly functioning container [is similar to] finding a hole in a wrapped surgical tray; the integrator will change, but if the seal is compromised, sterility cannot be assured,” said Deshane.
CS professionals should inspect containers after every use — being sure to look for loose gaskets, missing rivets and dents that affect the seal/gasket. “If a container is compromised, the patient is at risk due to non-sterile instruments,” Schultz warned. As for case carts, these should be inspected at least quarterly by a qualified repair vendor. “Failure of a caster, latch or door hinge has the potential to cause injury to staff.” Additionally, the underside of the cart must be inspected for dirt, suture strands, mop strands, dust and other contaminants that can potentially end up in the sterile environment.”
Plastic retention rings for the cart shelves are also vulnerable to damage and wear, reminded Amanda Coss, National Education Coordinator for Mobile Instrument Service & Repair.
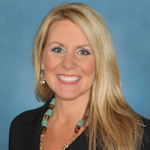