Updated: Supply Chain Experts Weigh in on Potential International Longshoreman’s Association Strike
Editor's Note: This piece will be updated as we receive further commentary from industry experts and associations.
Oct. 4 update:
The International Longshoremen’s Association and the United States Maritime Alliance, Ltd. have reached a tentative agreement on wages. They have also agreed to extend the Master Contract until January 15, 2025 to return to the bargaining table to negotiate other outstanding issues.
Effective immediately, all current job actions will cease and all work covered by the Master Contract will resume.
Oct. 3 update:
Healthcare Purchasing News (HPN) has been covering the looming strike by the International Longshoreman’s Association (ILA) that could take effect Oct. 1. The strike would impact ports on the Eastern seaboard and gulf coast.
HPN reached out to industry experts for comments. Here is what they had to say:
“Vizient’s supply assurance team is closely monitoring the potential strike by the International Longshoreman’s Association that could take effect on October 1 and impact the 36 ports on the Eastern seaboard and gulf coast. Suppliers we have spoken with have already implemented various strategies such as alternative shipping routes and shifting volumes to alternate ports, utilizing airfreight where possible, and increasing inventories to help ensure an uninterrupted supply of essential medicines and products. We are also encouraging our member providers to access the essential supply programs we have in place in the event they have a shortage to help avoid the potential for more widespread supply disruptions due to protective purchasing. We are hopeful that an agreement will be reached to avert a strike before the current ILA contract expires on September 30.”
-- Katie Korte, PharmD, MHA, BCPS, BCCCP and VP, Assurance & Continuity for Vizient
“To prepare, health systems should communicate with their current distributors to determine which products may be impacted by a port strike. Where possible, health systems should identify if domestic alternatives are available on critical items. In the short term, a strike should have little impact on health care and business should remain close to normal. Early planning and communication along the supply chain are key to helping reduce impacts that may be caused by a port strike.
“Suppliers should prepare with early planning, communication, and expediting inventory prior to October 1 through the ports are essential to creating resiliency in your supply chain when handling disruptions like a potential port strike.”
--Michael Hughes, vice president of Supply Chain – North America, Henry Schein
“This is the moment we’ve been preparing for. Over the past four years, every supply chain leader and their uncle has been emphasizing the importance of agility. As we face the threat of a port strike, we should remember the hard-learned lessons about how quickly the landscape can shift and how unprepared we can be for the unexpected.
“Let’s look back at the saline shortage that emerged after Hurricane Maria hit Puerto Rico in 2017. The island, home to a significant portion of the U.S. pharmaceutical manufacturing, faced massive disruptions. Hospitals across the nation experienced critical shortages of saline solutions. This really highlighted the fragility of our supply chains and the dire consequences that can reveal itself from a single point of failure.
“Now, as we confront a potential port strike, health systems need to act decisively. First and foremost, your emergency preparedness plans should be revisited. All stakeholders need to know the protocols if supplies dwindle. Collaborating with local public health agencies and emergency management organizations can enhance coordination and resource allocation.
“On the supplier side, the focus should be on contingency planning. Single source reliance can leave health systems vulnerable. Establishing connections with multiple suppliers creates a safety net that allows for quicker adjustments when one supplier faces disruption. Are there local alternatives? Perhaps alternative shipping routes or modes of transport can be considered to keep the goods flowing?
“In parallel, you should take stock of critical supplies and medications. Having a buffer of essential items can mean the difference between maintaining patient care and facing shortages that jeopardize health outcomes.
“Some of our customers reported that during the pandemic shortages, access to high-demand items was not only about supply availability but also about visibility. Even as the inflow of products slowed or halted, the key to ensuring clinical availability of supplies was how effectively their distribution centers or CSCs could identify and distribute goods where they were most needed, essentially acting as their own JIT provider.
“In the context of the potential impact of a port strike, it’s clear that agility isn’t just a buzzword; it’s a necessity. In the words of Oscar Wilde, ‘to expect the unexpected shows a thoroughly modern intellect.’ As so, as modern intellectuals, we should learn from past disruptions, avoid risk where we can, and continue to serve our communities — but should be equally ready to pivot.”
-- Cory Turner, senior director of Healthcare Strategy at Tecsys
“Hospitals and health systems should consider increasing on-hand inventory and consider the final implications as well as better predictions for utilization rates. Additionally, organizations should employ conservation strategies, it depends on the product and how it is used but they can employ lessons learned during COVID. Further, engage clinicians to proactively ID alternative products for most critical supplies (again, think about lessons learned during COVID). Finally, think through the impact to kits and custom packs—which components are impacted, other implications (e.g., sterilization/laundry demand, reusable single use/disposable).
“As for manufacturers, they can consider rerouting to the west coast or using other forms of transportation like rail or air freight. They need to understand the cost and time implications and communicate with trading partners.
“And for what suppliers and providers can do together, have an ongoing and transparent conversation about which products are most impacted, which are most critical and prioritize responses accordingly.
“The key is to think through all of the risks and interdependencies before jumping immediately to solutions and do it with your trading partners and your internal customers/collaborations, not in isolation.”
--Karen Conway, CEO, ValueWorks
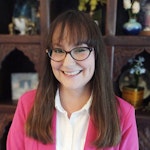
Janette Wider | Editor-in-Chief
Janette Wider is Editor-in-Chief for Healthcare Purchasing News.