Handling material throughout a healthcare organization – whether housed in a storeroom, supply closet or warehouse – involves more than just managing, moving, storing and transporting products and equipment.
The overarching process represents the circulatory system within an active facility whose clinicians and administrators require routine access to the necessary products and services to care for and repair patients.
While most supply chain executives and professionals may recognize the science behind material handling, many also recognize the art behind the strategies and tactics put in place that rely on creativity, forward thinking and horizon scanning.
Supply chain pros in the storerooms and warehouses – and to some extent the nurses and technicians who fortify supply closets and carts on nursing floors and in patient rooms – acknowledge the challenges and concerns they face with material handling and access that were exacerbated by the pandemic-driven backorders and shortages during the last several years.
Post-pandemic outlook
With the global pandemic roughly eight months in the rear-view mirror, corporate executives with material handling experience and expertise point to a plethora of challenges that remain constant, if not consistent, within industry change wrapped by the flag of resiliency.
"The tension between resiliency and efficiency has made life exceedingly more complicated for supply chain professionals who are increasingly challenged to keep their teams focused on the consequences of their failure to perform at a high level,” observed Doug Lowe, senior implementation consultant, Jump Technologies. “The ability to deliver a high-performance supply chain requires supply chain leaders to understand how processes affect their operations and cross-functional teams, and to be able to identify the root cause of a problem and the real-world solutions that can help them overcome the situation.
“Unfortunately, all too many of the resources and assets that supply chain teams rely on every day, whether internal or external, are not under their direct control, which can make it difficult to bring balance to potentially disparate forces and systems,” Lowe continued. “Prior to the pandemic, hospital supply chain teams were being driven by the demand for more efficient operations and cost reduction, less inventory, streamlined procurement workflows, and just-in-time (JIT) replenishment as their primary goals. In the post-pandemic world, as supply chain instability continues to affect product and staffing shortages, supply chain professionals are experiencing increased complexity due to high demand for supplies, increased conversion activities and a general fear of the new normal. As a result, I have seen hospitals with skids of excess supplies lining the corridors outside of central supply. Meanwhile, the stockouts and shortages continue, along with what appears to be gross overstocking and poor service.”
Lowe spent most of his career in supply chain leadership roles in various industries with his last role as manager, Supply Chain Logistics and Inventory Planning at Hennepin County Medical Center.
Shawn Ducey, associate principal, Advisory Solutions, Vizient, highlights three areas of concern that healthcare supply chain operations face. Labor shortages and staff turnover is the first.
“Labor shortages are no longer a short-term issue, and this is affecting key activities across distribution channels,” Ducey noted. “They have become the new norm. Even with some of the robotics and conveyance solutions that move product to the outbound prep areas, warehouse operations are challenged with recruiting staff for the physical and often taxing tasks of picking, packing and shipping products. The limited access to labor has labor costs exceeding inflation rates, and the competition for labor adds another level of complexity along with the cost to recruit, onboard and train.”
Warehouse efficiency is next, according to Ducey.
“It is not unusual to observe a warehouse facility that is underutilized with poor process,” he indicated. “This varies by the level of sophistication of the design (setup) and available technology. Warehouse efficiency is centered around people, process and technology. Processes need to be designed to remove waste throughout the warehouse operation and optimize use of the available technology. This includes product slotting, receiving and putting away, picking, transport and outbound shipping.”
Finally, Ducey cites long lead times for material handling equipment (MHE) as the third culprit.
“The lead time for select MHE, such as forklifts, conveyors and storage racks, is greater than 24 months and is driving up the cost for continuing operations with rentals and older equipment,” he added.
Terry Elliott, partner, Diamond Storage Solutions, warns about three lingering issues that hover between process and technology. The first is using excess inventory as a [bandage] to minimize stockouts versus deploying a robust consumption tracking and forecasting system. The second is maintaining insufficient documentation of material consumption, requiring frequent inventory physical counts that waste manpower. Finally, he emphasizes the lack of using Lean tools to eliminate waste that he defines as activities or resources deployed that do not add value. Elliott specifies four examples: “Waste [can be] in the form of transportation, such as unnecessary movement of materials or products; inventory, such as excess stock or supplies; motion, such as unnecessary movement of people or equipment; and waiting, such as idle time or delays.”
Three overarching areas represent material handling challenges that need to be addressed and overcome, according to Tom Redding, senior managing director, Healthcare, St. Onge Co.
Redding leads with facility layout and configuration. “One of the biggest concerns with material handling has to do with how well the space is organized to facilitate an efficient and effective storeroom and/or warehouse,” he told Healthcare Purchasing News. “Additionally, the space is not organized to accommodate growth, which may result in a less optimal operation over time. Lastly, the space is not designed to accommodate technology which may result in congestion and further inefficiencies.”
Material and people flow come next. “Many facilities are older with limited clear height and don’t organize the space to optimize how materials flow in and out the space,” Redding said. “This may result in back tracking to get supplies and/or creating a pinch point when accommodating inbound and outbound activities.”
Storage utilization represents the third leg. “Another challenge with material handling in a storeroom and/or warehouse is related to how well the available storage is utilized,” he noted. “If the storage is not planned and utilized correctly then it may result in a loss in productivity. Additionally, low storage utilization may require more travel time and unnecessary handling requirements to fulfill daily orders.”
David Phillips, marketing manager, Hänel Storage Systems, adds three more to the mix.
First for him is floor space. “More than ever, hospitals must do more with less – less space for storing surgical supplies, but more product for the increasingly complex surgeries being performed,” Phillips indicated. “Space is typically cut from storeroom areas, whether it’s sterile storage, materials management or central supply to provide more space for an OR expansion, for example, and those departments are then asked to store up to 40% more inventory within a much smaller footprint.”
Don’t overlook ergonomics, according to Phillips. “Storerooms, warehouses, sterile processing and even the maintenance department suffer significant man-hours lost to back strains and repetitive hand/arm injuries, not to mention falls and trip hazards,” he insisted. “Management in all hospital departments must analyze the work time lost to injuries and develop corrective actions to reduce or eliminate the causes.”
The third spans inventory management and tracking. “From the central supply room to the Sterile Processing department to the OR, inventory tracking is a challenge but critical. Imagine building a case cart that reaches the OR, only to find that a sterile wrap had somehow already been ripped, and then you need to scramble to replace that tray of instruments,” he added.
Human versus tech
Healthcare professionals can embrace two processes for addressing material handling challenges: One that doesn’t rely on technology tools, the other that uses technology tools. The former translates to lower upfront costs but potential long-term costs, the latter may require higher upfront investment costs with the potential of reducing ongoing long-term costs.
"With the deck stacked against them, supply chain professionals need to stay on the path of continuous process improvement,” urged JumpTech’s Lowe. “Healthcare is always changing, and when you add to this mix unprecedented regulatory requirements, complex multi-faceted supply chains and rapidly evolving realities within individual healthcare and on the global stage, the value of process improvement becomes clear. Healthcare organizations should strive to maintain an ongoing process improvement model that is driven by operational leadership and grounded in cost of quality, measurement and corrective action, communication, education, teamwork and recognition.”
With or without tech, supply chain pros have myriad options, according to Lowe.
“Supply chain teams can achieve this without tech tools by implementing things like information-rich daily huddles, training and development initiatives, open feedback sessions, team building activities and accountability training,” he recommended. “Meanwhile, supply chain and C-suite leaders should look for supply chain technology solutions that deliver data standardization, advanced forecasting and demand planning, real-time analytics and reporting across the organization or an entire IDN, and integrated PAR and perpetual inventory or order management capabilities.”
St. Onge’s Redding denotes the advantages of human-driven versus tech-assisted options.
“Most of the identified concerns can be resolved with taking the necessary time to review the inventory and throughput requirements and aligning the available space and storage to minimize walk time, handling requirements and reduce the potential of congestion,” he advised. “In most cases, focusing on a tech solution only will not solve the problem, only make it worse.”
But Redding cautions against rallying behind new tech investment without gauging existing capabilities.
“I believe most of the tools are available within the existing [enterprise resource planning] system to manage how well the storeroom and/or warehouse will function,” he noted. “There are other opportunities to leverage technology, which includes ‘follow-me’ robotics, [real-time location systems] to monitor aisle traffic and congestion and drones to monitor storage utilization, to name a few. Prior to jumping to a technology solution, it is best to leverage the skills and expertise of the supply chain leaders and/or outside consultants to provide their insights on how best to operate the storeroom and/or warehouse.”
Diamond’s Elliott promotes Lean philosophy as a non-tech tool to make a difference. “Foster a culture of continuous improvement, 5S (sort, set in order, shine, standardize and sustain), value stream mapping, error proofing, Kanban (visual management) and deploying a plan-do-check-act management method,” he suggested. “Select storage systems and solutions that minimize installation time, protect product integrity and facility sound Lean practices.”
If tech options generate interest, then “deploy inventory management software that uses [radiofrequency identification] technology to minimize physical inventory counts. Deploy an enterprise resource planning system (ERP),” he added.
Vizient’s Ducey acknowledges that balancing people, process and technology as options vary by organization capabilities and needs.
“Without investing in new technology, healthcare organizations address warehouse inefficiencies by utilizing a third-party logistics (3PL) provider or distributor partner for outsourcing equipment, inventory management, labor and warehouse management,” Ducey noted. “All warehouses should ensure Lean practices are in place for existing operations to remove waste throughout each of their processes.”
On the other hand, “investing in new technology can help healthcare organizations address warehouse inefficiencies, but organizations must also invest in time and training so that staff understand how these tools can optimize operations,” he continued. “Technologies include warehouse management systems, robotics, autonomous mobile robots, voice pick and conveyance to supplement labor and reduce cycle times.”
Hänel’s Phillips encourages tech solutions but recognizes that budgets and footprint limitations can redirect priorities.
“While the best ROI is found with high-tech solutions, such as an automated vertical carousel, inventory management software, bar-code scanning and hand-held devices, many hospitals still find themselves with financial or room design constraints that do not yet permit these solutions,” Phillips acknowledged. “In those instances, lower-tech solutions can provide a way to control inventory without costing a lot of money. One example is Kanban, in which just-in-time inventory levels are managed via a system of index cards and bins. This system still requires considerable amount of floor space but can provide a significant inventory management tool if none currently exist.”
Phillips promotes the Hänel Rotomat Vertical Carousel as addressing such issues as the floor space, ergonomics and inventory management/tracking issues. “By utilizing the complete floor-to-ceiling height, or even extending through a ceiling, a Rotomat can provide the storage space needed within a very small footprint,” he indicated. “This allows for better workflow, tighter control on inventory and ultimately increased productivity. Its automation and ergonomic workstation can replace traditional static systems to bring sterile supplies to the worker and the worker doesn’t need to travel distances, walk up and down stairs or interact with dangerously stacked items on wire carts or metal shelves that span from the floor to near the ceiling.”
Juggling different material handling solutions for effective, efficient product flow
Recommending safeguards against potential pitfalls and pratfalls with material handling practices and processes tend to be rooted in experienced from hindsight. Yet material handling experts offer a number of suggestions in a “do this, not that” scenario that may motivate you to stop questionable procedures or prevent them from being implemented.
“Do This: One of the primary practices that every storeroom and/or warehouse should be [practicing is] to continually cycle count inventory, monitor and address underlying issues for inventory accuracy (e.g., picking wrong unit of measure, picker performance issues, etc.). Another important practice is to continually assess how well the inventory is slotted to reduce aisle congestion but also reduce the travel time associated with picking each order. Lastly, exploring opportunities to pick multiple orders at one time and/or consider a ‘put wall’ approach for common items.
“Not That: Avoid the temptation to pick multiple units of measure from the same pick location; consider the potential to have a location for full case picks and another for ‘each’ picks. Too often, consolidating to one location results in miss-picks and inventory accuracy issues. Lastly, avoid the potential for nursing and/or non-supply chain staff to have access to the storeroom and/or warehouse inventories.”
--Tom Redding, senior managing director, Healthcare, St. Onge Co.
“Do not move to deploying tech tools without first creating robust non-tech processes and systems. Develop an understanding of what needs to be improved and deploy non-tech tools (Lean) and the best storage solutions. Then you will be better equipped to evaluate and select the tech tools that will best serve your needs.”
--Terry Elliott, partner, Diamond Storage Solutions
“There are times when Joint Commission, CMS or similar arrive for an inspection and find not only surgical trays and soft goods stacked closer than 18 inches from the ceiling, but they also many outdated/expired items. By using an automated vertical carousel with inventory management software such as the Rotomat, the surgical trays, soft goods, instruments, implants and any other sterile items can be stored in a six-sided, enclosed box maximizing the usable floor-to-ceiling height while managing and tracking all inventory transactions and expiration dates. Since the Rotomat carousel is enclosed on all sides, it also cuts down on the dust and other contaminants that can compromise sterile inventory.
“Visibility to all stored inventory is desirable to effectively manage materials. In the industrial manufacturing and warehouse sectors, companies routinely rely on integrated software systems to avoid multiple, disparate and redundant tracking. Hospital management systems should be able to allow the flow of information from department to department. This would greatly increase many efficiencies in the acquisition of new inventory, tracking inbound items, maintain proper stocking levels while in storage and report movement of inventory away from the storeroom or warehouse. Many material handling specialists have experience both in industry and in healthcare to design fully integrated inventory management systems to accomplish the goal of eliminating ‘islands of inventory’ not visible to management.
--David Phillips, marketing manager, Hänel Storage Systems
“Warehouses should have a standard process to measure and monitor capacity, inventory performance metrics, and focus on days inventory on-hand targets. Do not allow your distribution facility to become the repository for any type of dead stock storage. This includes old furniture, spare parts, obsolete products, supplies, equipment, returns etc.
“Warehouse staff should improve utilization of the available existing technology. Too often we see warehouse operations using 50-60 percent of a technology’s capability. You need to understand what you have and know how to tie it to your processes and management of the labor investment to realize full efficiencies.
“Consider collaborating with your distributor, 3PL provider, or supply chain advisory partner to review best in class solutions and process improvement opportunities that provide meaningful value in the material handling category.”
--Shawn Ducey, associate principal, Advisory Solutions, Vizient
“A few of the actions that should be at the center of materials handling best practices include fostering an environment of continuous learning within your organization, striving for clear and consistent communication between internal and external stakeholders, encouraging collaboration and knowledge sharing across teams, and implementing a kanban inventory management system. A common misstep for healthcare materials management teams that should be avoided is mistaking a PAR replenishment system for a true inventory management approach. A PAR replenishment system does not deliver the real-time data insights that hospitals and health systems need to avoid stockouts and keep patients and staff safe.”
--Doug Lowe, senior implementation consultant and supply chain subject matter expert, Jump Technologies
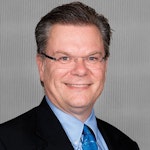
Rick Dana Barlow | Senior Editor
Rick Dana Barlow is Senior Editor for Healthcare Purchasing News, an Endeavor Business Media publication. He can be reached at [email protected].