Revolutionizing storeroom, warehouse workflow pairs human with machine
If shelving and storage serve as the bones and the skeleton of a storeroom or warehouse (see the April 2023 edition of Healthcare Purchasing News for the prequel), then the aisles and walkways, laden with humans scurrying about and vehicles scooting around, serve as the arteries and veins that support clinicians and administrators who deliver patient care and customer service, respectively.
Depending on the storeroom or warehouse footprint and layout, a healthcare organization may need some type of fulfillment traffic controller or coordinator – be that human or technology – just to keep the circulation flowing.
With the COVID-19 pandemic fomenting a labor crunch during the last several years that continues to afflict business and industry in general, many organizations are investigating and turning to technology to offset the lack of manpower as well as to generate financial and operational efficiencies.
One area attracting heavy Supply Chain concentration involves configuring and redesigning the layout of the storeroom or warehouse to revolutionize – if not streamline – workflow.
Digital domains
As the healthcare industry may not enjoy the spatial resources of other industries, supply chain leaders in healthcare must conjure up creative designs and outlines for the footprint in which they control.
“I’ve worked with many healthcare organizations that felt they were splitting at the seams and were on the hunt for larger facilities, but that may just be a symptom of planning tactically,” Turner observed. “Some strategic re-engineering and new technology integration often resolves capacity challenges and avoids the cardinal sin of simply transplanting the same inefficiencies that got you into trouble.
“At the end of the day, it is next to impossible to set up your storeroom properly without visibility into where your workflow problems exist,” Turner continued. “Even the most seasoned supply chain professional’s intuition can benefit from the kinds of visibility that the right technology system can provide.
Think digitally, Turner advises. “Take, for instance, the emerging world of digital twinning, which is now being embedded into warehouse management software like Tecsys’ Elite WMS,” he said. “Being able to digitally map your areas of high interactivity helps you digitally visualize and address bottlenecks. With those data insights in hand, it may be suitable to solve for bottlenecks with low-tech automation like conveyors and sortation systems, or more high-tech systems such as [automated storage and retrieval systems] or [autonomous mobile robots]. But it could also be as simple as relocating your fast movers and optimizing picking routes. Being able to see and manipulate your warehouse with technology allows you to make strategic decisions while driving tactical improvements.”
Timing and review frequency remain key matters to manage a warehouse optimally, recommends TJ Fanning, COO, SVT Robotics.
“When considering the design of your existing warehouse or storeroom, it’s critically important to understand the frequency at which the requirements change, and to what level of variability. These two metrics will define the level of optimization required in your facility,” he emphasized.
When inventory variability is low and requirements are fairly well-known, Fanning recommends performing a slotting analysis of items based on ergonomic picking conditions, the [stock-keeping unit] ABC curve and order container requirements as the most ideal solution. “Ultimately, this will drive fixed locations to be assigned to specific SKUs to maximize the performance of individuals interacting with specific inventory,” he added.
When inventory variability is high, however, and involves frequent requirement updates, then automation may be needed, according to Fanning. Automation options can range from using digital twin applications, like Verses.io to highlight inefficiencies, to more automated solutions like Kardex Solutions AutoStore ASRS, which automatically optimizes inventory locations after each interaction. “That means that inventory can be constantly optimized to not only reduce the automation requirements, but also increase operator performance, sometimes as much as 400%,” he added.
Fanning calls attention to the economics of real estate.
“We are also seeing that in addition to operator efficiencies, it’s critical to understand the cost of the space you are operating in,” he said. “Many facilities that I walk [through] today have poor space utilization and planning, as historically that element was not of significant concern. But with the supply chain disruptions we’ve seen in the last 24 months, many organizations are holding additional localized inventory and therefore require additional density to prevent the need to create an expansion or migration to another facility. In these cases, we see many uses for vertical lift modules, like the Modula Slim unit, which requires a very minimal footprint but uses vertical clear height to maximize density. Additionally, the operators remain on ground level, improving efficiency and safety.”
Optimizing your storeroom and warehouse layouts and inventory is critical to maintaining service level commitments to not only your customers, but your employees, Fanning urges. “Unfortunately, this is typically thought of only when it’s too late and you now must consider a new location because the current one no longer meets expectations and it’s difficult to change,” he added.
Human ingenuity
“Organizations need to have a dynamic workforce that can be fluid in how they process material through a building,” Truax indicated. “Hiring warehouse workers that have a variety of skills will enable leadership to adapt quickly to changes on the horizon. This is obviously easier said than done. That’s why training is also a key component to managing a dynamic workforce. Another key component is utilizing technology to support warehouse employees and their leadership. The more automated the processes, in this sense, the better. This does not always mean more mechanical handling equipment (MHE) to process material, however, that is also key to driving efficiencies.”
Still, Truax views automation through a different lens.
“Automated processes that help users make a specific decision, whether ordering additional non-inventory material or managing labor through the system, drive consistency across an operation,” he noted. “Simply put, having easier decision points that are defined for the user based on a set of input parameters keeps the operation consistent. To drive the input parameters, it is key to have a set of standards or guidelines to operate across an organization. This is best set by a team of process subject matter experts (SMEs) that understand the bigger impact to multiple sites in a network.”
As customer demand changes, an organization’s physical layout constraints become more prominent as user processes need to drive storage space design, according to Truax.
“Having a layout that is designed with the end user in mind, along with different principles for managing the sortation of inventory in a specific location, will help drive efficient processes,” he observed. “For example, managing the pick process in a facility is crucial. Maximizing the time spent picking by reducing the time spent traveling between picks is an effective way to improve warehouse design.”
Truax cites the newest warehouse operated by Cardinal Health at-Home Solutions, located in Grove City, OH, as an example of forward-thinking for future picking processes. The warehouse includes Swisslog’s AutoStore high-speed robots. “These robots bring products directly to our warehouse employees for packing and shipping, which not only brings more speed to order fulfillment, but also decreases human error,” he said. “This type of technology is just one example of the automation we’re infusing in our warehouses across the country – and for all of Cardinal Health, across the globe – we see these modernization efforts as a top priority in creating a more efficient, resilient supply chain.”
“In each of our distribution centers at Cardinal Health, we have a designated role called an ‘Inventory Profiler’ whose responsibility it is to utilize our warehouse management system to analyze customer demand data to position our inventory in the most optimal locations,” Farnin explained. “One ‘rule of thumb’ is to keep your fastest moving products closest to the outbound shipping dock to reduce travel time. Another strategy is to place your slower moving SKUs in the upper racks where an Order Picker (materials handling equipment) is needed, while storing your fast-moving items ‘on the floor’ where no heavy equipment is needed to pick these SKUs. This inventory profiling work helps improve our picking efficiency, quality and employee safety.”
“The first step in optimizing storage space is by using data to ensure that inventory requirements are optimal,” Langlois noted. “This can be achieved by using appropriate data analytics, taking into consideration demand but also average delivery delays from vendors by specific products rather than globally by vendors.
“Secondly, you should establish a few standard space sizes and determine their cubic capacity,” he continued. “You should then determine the cube measure of all products and use a dynamic slotting application to determine in which location each product should be located. Dynamic slotting applications will also use other data, such as the frequency of picks to locate products based on their velocity. Such applications can present a 2-D plan to visualize the result of the simulation and allow users to make changes, if need be, prior to locating products. [See Figure 1.] Once the initial configuration is completed, dynamic slotting applications will propose changes based on new data such as the velocity.”
From these considerations, healthcare supply chain leaders can assess such storage technology options as bulk racking, flow racking and unitary picking, for example, and such automation technology options as vertical carrousels, conveyors, shuttles and various iterations of goods-to-person robots, Langlois recommends.
Ongoing supply chain challenges, accelerated by the pandemic, such as manufacturing and distribution disruptions and changing customer demands can be diminished, if not resolved, by deploying some type of automation technology, according to Grant Beringer, vice president, Integrated Systems, Swisslog Americas. Yet the decision to automate and implementation of automation technology should not be a static move, he suggests.
“Distribution systems and supply chains need to remain agile to respond to change,” Berringer noted. “That’s only possible when the automation systems that are deployed can flex in size and performance over time.
“Flexible and scalable robotic automation technology enables companies to adapt to fluctuating demand and rapid growth in ways the traditional automation simply cannot,” he continued. “In applications that range from pallet handling to item picking, these solutions are giving warehouse operators the ability to scale throughput and inventory independently. They are fundamentally capable of driving higher performance with the same inventory or expanding inventory without requiring higher performance. This capability, combined with unprecedented redundancy, makes them an easy automation choice even for the hesitant.”
Berringer emphasizes the flexibility of the automation technology should adapt to the shape of the building where deployed, whether that involves upgrading older warehouses or repurposing unneeded or underutilized facilities to accommodate increased distribution capacity. In fact, he views flexible robotic automation technologies taking center stage on operational wish lists, moving “from an alternative to fixed and inflexible technologies to becoming the first choice for operators across virtually every industry,” he added.
“The key to harnessing the power of automation solutions is using software that has been designed to manage the solution and maximize its efficiency,” Berringer indicated. “Such software should provide warehouse management, material flow and automation control system functionality in a single, modular platform that integrates seamlessly with host systems and other warehouse software.”
In working with healthcare organization customers, Medline Industries designs and redesigns storerooms and warehouses using PAR optimization, velocity slotting and ABC analysis to redirect effort and time spent on operations to time spent on patient-focused care, according to Jaimin Patel, senior project manager, Engineering, Medline Industries.
“One main way is to free up space to store more inventory, SKUs, pandemic supplies and [physician preference item] bulk buys and improve the visibility of that available inventory to save healthcare workers time when searching for products,” Patel said. “Ensuring your inventory is appropriately spread throughout your facility will also aid in reducing bottlenecks.”
Patel also recommends reducing human error in storage organization and the picking and fulfillment processes.
Low-tech for high returns
High-Density track shelving with active isles. “High-density shelving allows pickers to access materials easily by incorporating easy-to-move individual shelving units attached to a track,” Salus said. “This design concept can increase your storage space by 70% in confined areas and is able to be paired with Metro accessories to keep materials organized.
Room and process planning to increase the storage space. “Each of Metro’s sales representatives are trained to help facilities build the best storage space within the space available by determining the ideal workflow and configuring the storage solutions with aisles that deliver the most efficiency,” he noted. “This is a value-added service that is included in the price of the product, no extra fee is charged. For the ‘do-it-yourselfer’ or for smaller areas Metro has invested in room-builder tools that can create a 3-D model of your space and show Metro products put in place so you can view prebuilt plans, for free, in real time.”
S hooks for corner-space storage. “S hooks get rid of the need for corner shelving to have an external post,” he added.
Color-coding storage locations. “Many customers utilize Metro’s color shelf markers to distinguish items or areas by function,” Salus indicated. “These color codes can be customized to identify items by type (i.e., IV, Blood, Suction, Ostomy, etc.), by service line (Ortho, Cardiology, Oncology, etc.), unit of use versus bulk, etc. Helping staff narrow down the area or number of compartments to search for a needed item is a huge time saver.” Salus notes that color coding remains both popular and inexpensive as an option.
Riding the conveyor belt of storeroom, warehouse design creativity
Regardless of being blessed with too much space for storage or cursed with too little, designing and organizing what you have requires ample creativity that automation simply cannot provide on its own, independent of human intervention.
As customer demands soar, peak or wane during periodic crises, such as the global pandemic, or daily activities, healthcare supply chain leaders and workers must demonstrate flexibility and open-mindedness with storeroom or warehouse layout and organization to optimize fulfillment and workflow effectiveness and efficiency, experts note. That includes using distributors in supplemental roles.
Elastic, fluid traffic patterns
“Additionally, having adequate inbound and outbound staging areas, and pick zones for logical unit of measure (LUM), bulk and forward picking can minimize the risk of product spilling into the aisles,” he continued. “Your distributor can also help optimize your storerooms by providing supplemental off-site solutions for your system, such as housing bulk products within their warehouse to declutter your space.”
Still, Cory Turner, CMRP, senior director, Healthcare Strategy & Product Marketing, Tecsys Inc., and a former regional warehouse executive with an award-winning healthcare system, supply chain leaders and professionals need to be realistic.
“As much as we’d like it to be the case, we cannot predict the next curve in the road,” Turner noted. “The key to success is to architect so much elasticity into your operations that you can bend around those curves without breaking.
“To do this effectively, it’s truly a team sport,” he continued. “Work with your partners to manage or mitigate disruption proactively. Make sure to diversify your sources — from distributor to manufacturer. Connect with your technology partners to learn about what they offer around planning solutions and leverage that technology to make your data work for you. Healthcare organizations should ensure visibility and coordination across their network rather than siloed by location or region. In the middle of the PPE crisis, a Tecsys customer shared with us that this consolidated visibility made the difference when inventory levels were critical because it let them move a product where it was needed without the typical buffers.”
Turner encourages healthcare supply chain leaders and professionals to adopt a back-to-basics approach that organizes the storeroom or warehouse according to velocity.
“In a double-deep and high-shelving environment, this is especially critical,” he insisted. “Faster-moving items should be in easy-picking locations, and slower-moving items should be in harder-to-access areas. This may be an opportunity to partner with your distributors in a way that lets each of you play to your strengths. While fast movers could live within the hospital network, you may want to leverage a distributor’s broader network and higher volumes to handle slower movers.”
TJ Fanning, COO, SVT Robotics, doesn’t anticipate disruptions going away so “operators must be extremely flexible and willing to modify their process to meet service level commitments,” he said.
Fanning cites a recent example that he calls a “hybrid cross dock picking operation” worth noting.
“The facility had experienced a delivery delay for a high-volume [stock-keeping unit], so the orders for this SKU were extremely high across a short window,” he recalled. “Additionally, the facility required live loads, so they were not able to pick in advance and stage on a trailer for shipment. To solve this, upon receiving the truck of late inventory, they received it in their [warehouse management system] and then transferred the inventory to a logical pick slot, which remained the dock door. That created a pick path for operators to pick directly from the receiving container and eliminated delays to perform putaway and replenishment functionality, which was common in their facility.”
Technology can enable rapid flexibility, he emphasizes, particularly when labor may be hard-to-obtain. “The common operators’ challenge of high variability impacts staffing in many cases, which sometimes can be insurmountable,” he said. “For example, if you have 30 operators on a shift and experience a 75% peak period, you may need to bring in as many as 23 additional operators, which is almost impossible to manage as your leadership team can’t onboard that many temp operators and still maintain facility safety and accuracy. However, that same facility with automation like Locus Robotics, or 6 River Systems, can likely operate with 10 to 14 operators on a standard day. That means peak demand will only require 10 additional operators, which is much more feasible for a leader to manage. Also, additional robots can be added with a simple phone call and offered as a short-term service agreement, which makes automation an even more flexible option.”
Robotics ready?
Fanning realizes that not all organizations may feel ready for robotics so they might consider turning to third-party logistics companies to provide fulfillment and picking services, particularly to support spikes in demand. Why? These organizations likely have already deployed the infrastructure of robotics to specifically support your unknown volume and requirements, he explains.
If automation technology may not be a proximate option, then mechanical infrastructure and information systems may need to pick up the slack, according to Paul Farnin, director, Supply Chain Solutions, Cardinal Health U.S. Medical Products & Distribution.
“Creative use of space and racking can help with carrying more inventory to anticipate spikes in customer demand,” Farnin noted. “However, the longer-term solution is the use of technology to assist our teams with demand planning and forecasting, which are at the core of Inventory management. Our collective ability – and willingness – to share demand data will be the key to our industry’s success in adapting to and better managing erratic ordering patterns. At Cardinal Health, we have recently invested in a state-of-the-art demand planning system to enable our Inventory Planning Teams with ‘real time’ data to better anticipate customer needs. More work needs to be done both upstream and downstream to share demand data and make inventory planning more predictable for distributors and manufacturers.”
Meanwhile, Cardinal Health advocates for the healthcare industry to consider demand sensing and multivariable demand planning to be part of demand planning suites — pulled together these important considerations ultimately benefit patients, Farnin insists.
Ryan Truax, director, Operations, Cardinal Health at-Home Solutions, points to market dynamics during the last several years as influencing storage footprints going forward and motivating the need for automation as an option.
“Changes in both demand and the labor market have made it critical to have a flexible layout and organizational structure,” Truax observed. “The use of different automation technologies to manage mix variability will ensure a site is processing the material effectively. If there are multiple sites across a market, it may make sense for sites to specialize in managing a specific product mix. Specialization in product mix helps to remove the product mix variability when processing.”
Truax favors a cross-dock model to reduce transportation cost and increase total distribution volume.
“Modeling out inbound [transportation] movement in a network is critical to managing labor at a site – and I see this as a ‘must’ with labor,” he said. “A flexible labor market with associates that have a variety of skills, from machine driving licenses and MHE management to basic pick, pack and ship duties, will enable an organization to easily move associates through different processes based on business needs. Being flexible in your daily production hours (increasing or decreasing) and balancing associate needs for specific shifts will also help ensure you have the right people at the right time, doing the right process.”
Automation must augment human decision-making, Truax posits, particularly involving available labor.
“An automated system that limits leaders’ decision points and provides [off-hours] output for necessary-to-process fluctuations in volume enables leaders to make advanced decisions on headcount,” he said. “This could include adding overtime opportunities or allowing associates to have a much-needed day away from the site. Allowing for part-time and weekend scheduling can level load volume across the week. Visibility into volume swings and having the ability to manage hours up or down allow for teams to manage volatile demand.”
For Emmanuel Langlois, executive vice president, Global Alliances and Partners, Generix Group North America, dynamic slotting of inventory can alleviate some of the planning pressure suffered by healthcare supply chain leaders. Langlois sees it as a “first step in reacting quickly to changes in storage requirements.” In fact, only about 10% of extra space might be needed to adjust to demand variability, he surmises.
But Langlois warns against using this strategy as a tactical crutch, particularly because many changes in demand can be forecasted in advance, which leaves more time to adjust accordingly.
“Forecasting demand is a common practice in most industries but extremely rare in the healthcare provider space,” he observed. “This is likely due to the fact that the U.S. healthcare industry has been built around a solid base of manufacturers and distributors carrying sufficient inventory to react to reactive replenishment.”
The global pandemic upended this theory, he acknowledges. “The pandemic has shown in the last few years that the current reactive model has likely reached its limit as the supply chain broke in many instances,” he indicated. “Forecasting would be a good first step in improving this situation.
“Other industries are also moving more and more towards collaborative replenishment,” he continued. “This growing business practice includes forecasting models but also includes direct vendor visibility and input in the replenishment process. The Generix Group provides a market leading Collaborative Replenishment tool to other industries.
Fresh look with eyes wide
“We have not yet reached the point where most automation systems can be standardized for all applications,” Beringer cautioned. “It often depends on the strategy, throughput and available space. However, we have reached the point where we do have best practices, much of which focus on the design and configuration of the system, as well as the implementation and the operational side.”
Beringer encourages healthcare supply chain leaders to evaluate automation options and choose to take a system for a test drive.
“With a variety of viable options available, there’s never been a better time to consider the business case for investing in enhanced warehouse automation,” he enthused. “The technologies available today can be configured to adapt to existing building limitations and deliver increased storage capacity and higher throughput. They feature modular designs that experienced integrators can leverage to deploy automation in phases that enable continued service to customers through established manual processes while the automation is being deployed.”
Beringer recognizes the stigma hanging over warehouse automation for years. “The common belief held by many was that if you bring automation into your warehouse, you are replacing human workers,” he said. “While there are those exceptions, for most companies, this is simply not the case. The goals are often to enhance the productivity of human workers, create innovative environments that attract skilled labor, and improve workplace safety and ergonomics for employees. In fact, automation solutions can be a powerful tool in attracting and retaining the skilled labor many companies need.”
Real time in time
Even though high-tech automation attracts eyes, low-tech equipment and infrastructure offers options as well, according to Dave Salus, Healthcare Market Manager, InterMetro Industries Corp.
Mobile robots may turn heads but mobile storage is another way to optimize space, Salus advises.
“As processes become clearer and product storage needs change and evolve it can be common for storage spaces to lose efficiency over time,” he said. “By focusing on placing mobile solutions where [they are] viable, your storage space is able to adjust with your storage space needs. Metro offers a variety of heavy-duty caster options that can be added to your shelving units, dunnage racks and other storage choices.”
Salus also points to adjustable shelving for changing spaces. “Super Adjustable Super Erecta shelves offer the ability to adjust shelves easily while the shelving unit is still built,” he said. “Each shelf can be adjusted in one-inch intervals to increase or decrease space between each shelf as needed. So as SKU counts or packaging sizes change, the storage levels can be easily adjusted up or down to accommodate those changes.”
As healthcare supply chain leaders reorganize storage areas, their efforts may free up more space that can go unused. Salus recommends they consider installing InterMetro’s EZ-ADD shelving options to existing units.
“Once RTLS is implemented and asset management tags are placed on the necessary equipment, staff can view their precise location in seconds and receive automatic status updates” he explained. “This technology offers real-time room and bay-level map views, list-views of medical equipment locations and detailed usage and provides alerts for equipment maintenance.
“RTLS not only helps to keep track of or identify where mobile medical equipment and high dollar assets are, inside of any storage location, advanced systems offer the ability to streamline and automate the process around who needs what, where, when, and how often, via logistics software,” Stewart continued. “As an example, if you have a centralized storage facility acting as a hospital’s distribution center for mobile medical equipment, RTLS allows teams to know, at all times, how many of those devices are physically present, but also as demand comes in for consumption/patient use, logistics automation software can intelligently assign someone to retrieve the device from a storage location and deliver it wherever it needs to go. That could be a sub room storage location, PAR room storage location, or purely on-demand to deliver at the bedside.”
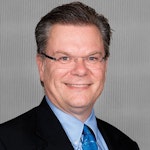
Rick Dana Barlow | Senior Editor
Rick Dana Barlow is Senior Editor for Healthcare Purchasing News, an Endeavor Business Media publication. He can be reached at [email protected].