Choose proper material handling tools to prevent warehouse from becoming a war zone
Aside from gaining access to products (which has been an enduring challenge the last two years), one of the primary tactics of supply chain is moving products effectively around with an inherent strategy of handling materials as efficiently as possible.
Labor, process and workflow and technology and tools drive effectiveness and top it off with efficiency if healthcare organizations choose their options wisely based on their organizational needs.
That’s why provider organizations must determine what product and process improvements they may need based on self-assessments of their materials handling operations. As a result, Healthcare Purchasing News queried a small group of executives well-versed about material handling and supply chain operations about relevant and useful products and technologies for storerooms and warehouses.
Fortifying the storeroom and/or warehouse with the gamut of material handling products and technologies may seem like a luxury to some but a necessity to others. So HPN asked material handling experts to evaluate more than 18 options to determine which were luxuries versus necessities to manage supply chain operations. Those products and technologies generating unanimous decisions are listed in the “Complete” categories. Those gleaning mixed decisions are listed in the appropriate “Leaning” categories. Based on current events and against the backdrop of supply chain disruptions during the last two years, the points of view may be surprising to some, realistic to others or not forward-thinking enough to a third group.
Tom Redding, Senior Managing Director, Healthcare Services, St. Onge Co., initially points to “the availability of reliable labor” as a continual challenge for most industries, including healthcare, when looking to improve material handling performance and that likely motivates increasing interest in technology.
“Supply chain leaders will explore options to proactively manage potential service failures with technologies as [automated guided vehicles], process automation, demand management and cloud-based solutions,” Redding told HPN. “These types of technologies and systems will provide visibility, access and control across the enterprise to manage the business more effectively. Leveraging these types of technologies will require a more thoughtful and coordinated effort with the broader IT/IS business plan. Making decisions in a silo will no longer work with the future of high-integrated solutions.”
However, striving for operational improvement must be balanced with the realistic capabilities of future-oriented technologies, according to Redding.
“Technologies like virtual reality are becoming more readily available as an immersive training experience for new hires, and to facilitate the change management process for incorporating operational improvements,” he indicated. “Supply chain leaders are under pressure to prepare for the future, and there is a lot of confusion in the market on what technologies are real and here to stay versus vaporware. We are seeing many potential use-cases for artificial intelligence (AI) in supply chain, but it will take time for the technology to mature and become more reliable for further adoption.”
Sidestepping away from tactical and transactional philosophies drives the migration, Redding observes.
“Health system leaders are slowly shifting their approach from a transactional supply chain mindset to a strategic one,” he noted, “and that shift brings new requirements and expectations for technology and systems, and how they will support a decentralized model of care.”
Cory Turner, CMRP, Senior Director, Healthcare Strategy, Tecsys Inc., recognizes the appeal that some of the leading-, cutting- and bleeding-edge technologies provide.
“There are more futuristic tools on the market today than ever before – everything from VR robotics to Iron Man-like exoskeletons,” Turner enthused. “With such a glut of innovation, it can be challenging for supply chain leaders to determine which ones are distractions, and which can be truly valuable to their operations. However, by embracing tools that can streamline processes and ease the reliance on human resources, healthcare supply chain leaders can address labor shortages while prioritizing patient care.
“Underneath the shiny veneer, there are great technologies that are being field tested with impressive results,” Turner continued. “When the right tools are brought together in the right environment, the possibilities for growth are endless. A strong and industry-tailored [warehouse management system] with demand forecasting capabilities coupled with AGVs, conveyance and wearable devices can not only increase productivity and efficiency, [but] it’s a formula that can empower the human workforce to be more effective.”
While AI continues to capture interest among many supply chain leaders, some experts urge caution about embracing and implementing it before operations are in proper working order.
How do supply chain experts categorize material handling product and technology offerings along a spectrum? Check out the Material Handling Technology Grid to learn where they generally assigned options.
Finding material handling solutions may be more than minding the store
Healthcare supply chain leaders and professionals may have a wealth of products and technologies from which to choose probable solutions for their material handling needs and wants, but experts urge careful consideration and planning before taking the plunge.
Why? The aftershocks from the plunge may be severe and unexpected. Six share useful tips that should motivate and direct decision-making.
Finding balance
“For the storeroom, it comes down to a balance of capacity and visibility. Storerooms are often undersized rooms with a need to store a large number of supplies. Careful consideration should be given to balancing how many items get stored, how much of each item and how often they will be replenished. It is also important to make it easy for clinicians to find what they need. Lower counts and higher replenishment frequency may be the best option to provide the best patient experience. Physical space will be the only constant in this formula. Once the [stock-keeping units] are figured out, the next step is to find the best way to fit them in the defined area. There are many options, traditional shelving, high-density track systems, bin wall, cantilevered baskets or a combination. Metro representatives provide free space audits to help decipher the best combination of solutions for your space.
“Warehouses are similar, just on a larger scale. Bulk storage is fairly straightforward. Pallet racking is typically the go-to. The unit-of-use items is where some complexity comes into play. Once items are broken down from their packaging, you begin looking at individual items of various shapes and sizes. This also increases the amount of space needed for these items. So again, it’s a look at how many SKUs will be supported from the warehouse and how many to store at the individual level. Figuring out these two metrics will determine the space required, which can be compared to the space dedicated. Once this factor has been identified, it comes down to the best combination of storage solutions to fit the items in the predefined space. This is where the Metro rep can again step in and provide free space audits to help decipher the best combination of solutions for your space.”
Dave Salus, Market Manager, Healthcare Division, InterMetro Industries Corp.
Look to overarching automation
“As a health system looks to improve materials handling efficiency across facilities, analysis of its current or implementation of an enhanced health provider-focused Warehouse Management System (WMS) becomes Job One. A fully functional WMS drives improvements in the hospital storeroom and is an absolute necessity when operating a warehouse/distribution center. A WMS can provide a higher utilization of storage space, increase labor productivity, improve warehouse activity accuracy, and most importantly, provide clear visibility and traceability to provider inventory. The WMS review or selection process also helps inform what storeroom or warehouse technology is actually ‘necessary” versus “luxury” based on provider resources, processes and goals.”
Zach Malingowski, Senior Director, Supply Chain Optimization, Medline Operations
Striving for accuracy
“One of the biggest challenges for a storeroom/warehouse is maintaining an accurate inventory value for all of their stocked products. Without an accurate storeroom/warehouse inventory, there are many operational challenges that occur, such as: Perceived stock-outs/killed orders, lack of inventory replenishment automation, incorrect financials as a result of inventory variance, and additional labor to reconcile daily inventory requests.
“At a minimum, weekly cycle counting of the highest activity products is a small investment in keeping the overall operation running more effectively and efficiently. Additionally, create a dashboard of your storeroom/warehouse inventory with key metrics, such as order fill rate by product, inventory turns by product, product lead time by product and stock-outs by product to name a few. Tracking inventory metrics will enable a storeroom/warehouse manager to proactively assess their performance and address issues before they result in a service delivery failure.
“Lastly, storeroom/warehouse inventory slotting is a critical function to achieve higher picking and replenishment efficiency. Too often, the fast movers are stocked in the same aisle, which may create congestion for supply technicians to execute their duties. As a result, picking and replenishment efficiency is impacted and ultimately it will require more labor to process the daily inventory requests.”
Tom Redding, Senior Managing Director, Healthcare Services, St. Onge Co.
Go Lean for green – and gold
“First and foremost, it is essential to have a system that takes into account all those good Lean principles. Deep dive into process by streamlining inventory control, cycle counts, stocking policy, expiration and recall maintenance. To allow for more efficient and quicker order fulfillment, make sure to maintain the ‘gold-zone’ in picking areas with the use of technology sources.
“Your data is a powerful ally in strategic decision-making. Rather than relying on intuition, basing decisions on empirical data provides an objective and accurate reference point. This is becoming more and more important as we integrate automated processes that are more attuned to the trends and patterns that may otherwise be overlooked.
“Finally, your most valuable vendors are also your partners. Building reliable vendor relationships with your technology, distributor and manufacturer counterparts provides a solid foundation for mutual wins.”
Cory Turner, CMRP, Senior Director, Healthcare Strategy, Tecsys Inc.
Enabling predictability, efficient workflow
“It’s essential for today’s hospitals and supporting healthcare organizations to safeguard data relating to patient supplies. With AI, such data enables predictability as well as the capability to forecast critical patient interventions and unprecedented changes in medical requirements.
“Robotic Process Automation and cloud-based software are still other technologies healthcare organizations may deploy for improving workflow and increasing efficiencies. Robotic automation helps staff retrieve supplies more quickly and accurately. Moreover, cloud-based software allows for efficient data collection and retrieval. Such software is also essential considering the need to maintain and access medical data across extended timeframes as supply usage affects medical outcomes. Toshiba’s innovative duplex liner-less printer, which combines two separate labels – including shipping and packing lists – into a single, two-sided label is yet another technology benefitting healthcare logistics professionals while helping their respective organizations operate more sustainably.”
Jessica Bernardo, Senior Product Marketing Manager, Label Print Solutions, Toshiba
Plan operational readiness first
“In the face of ongoing labor shortages and the need for cost efficiencies, warehouse managers and supply chain leaders undoubtedly are weighing the benefits of investing in warehouse automation solutions and artificial intelligence. The benefits are attractive: Dramatically improved productivity, reduction in operational costs, reduced (or eliminated) safety risks, space optimization, and enhanced customer satisfaction. When done well, these improvements – and the efficiencies gained from them - lead to enhanced profitability.
“While enticing, pause and consideration should be given before diving into such an endeavor. We have seen many failed automation projects – not due to a lack of capital investment or understanding of how it should work – but because of a lack of proper pre-planning and data analysis. And in some instances, automation may not be the right answer or the right next step. A facility may not have the right size, budget or resources or – in our opinion, the most important consideration – appropriate operational readiness. It is critical to focus first and foremost on the current processes in place. And, if automation is appropriate, it should support these optimal processes and drive engineering and supply chain best practices.
“Perform Value Stream Analysis. You do not want to automate a broken system. Have a comprehensive understanding of your processes and the interdependencies of various work areas (i.e., how does a change in picking product affect packaging and/or outbound delivery?). Map out current state of the flow of goods in and out of your space, identify bottlenecks and inefficiencies within the chain, list all available resources (human, tangible, and intangible) and determine if they are being utilized to their fullest potential, outline future state with goals and objectives.
“For any design, plan for future growth. Is the system flexible, mobile, expandable? Can the footprint be quickly redesigned or built vertically versus horizontally? Being able to quickly make changes ensures you maintain speed and accuracy in the future.
“Highly variable operations are typically not suitable for fully integrated automation. Implement advanced demand planning strategies within various areas of your health system. Are there predictive algorithms found within historical data that are based on seasonality or within specific treatment areas? Understanding this information is a good exercise before implementing strategies.
“Consider partial implementation strategies versus fully automated systems. We typically see partial implementation within cells at ‘end of line’ (i.e., shrink-wrapping and palletizing). Be sure your pre-planning identifies all potential bottlenecks from a future state design. For instance, we have witnessed companies increase conveyor belt speed to drive more thruput and then fail miserably when the packing cell employees could not handle the increased volume. Not only did it ‘break the system’ but it drove worker frustration and hurt morale.
“There is arguably nothing more important than employee buy-in. Even the most sophisticated system lacks value if your team members don’t understand it. Incorporate visual management and craft training programs that focus on AI and technology, drive innovation and educates employees on how to utilize the tools around them.”
Jennifer Nageotte, Partner, Diamond Storage Solutions
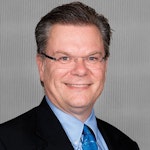
Rick Dana Barlow | Senior Editor
Rick Dana Barlow is Senior Editor for Healthcare Purchasing News, an Endeavor Business Media publication. He can be reached at [email protected].