Supply storage, management and tracking from receipt through use has long been a challenge for U.S. hospitals given the sheer volume of medical/surgical and drug supplies, the many stakeholders who handle them, and various logistical factors (e.g., limited storage space, outdated inventory management systems, etc.).
Faced with crippling cost pressures, supply shortages, and the need to maximize resources, hospital supply chain leaders are continuously seeking ways to solve supply issues, and companies are responding with new solutions aimed at taming complexity and boosting accuracy and efficiency.
Ceasing the mad supply scramble
“What happens in your kitchen when you are in the middle of cooking your Thanksgiving meal and you cannot find an ingredient, utensil or cooking pan and you need to finish the meal before it gets cold? A mad scramble for a solution takes place. Do you make a run for it? Do you panic? How much time searching before you make phone call to neighbor? It’s not a position anyone likes to be in whether at home or at work. This is comparable to what happens throughout a hospital’s supply chain on a daily basis,” said Ian Loper, Vice President of DSI.
Loper points to the challenges caused by old storage methods and disorganized supply rooms, including expired, misplaced or damaged supplies. Hospital staffs can’t manage what they can’t see; therefore, he advocates for ways to improve supply visibility in storage areas.
“Visual indicators down each row, at the top of each section, better/bigger labeling for each item being stored for each compartment, and color coding by service line are all simple ways to enhance the efficiencies and employee morale in the workplace,” said Loper.
He says DSI Direct has elevated its labeling product offering to include a variety of different ways to enhance visual indicators and labeling to help reduce the time it takes to identify and retrieve the supplies.
“When doing so, it makes it easier and quicker for the staff to look for, find and deliver the supplies to the patient, surgeon or colleague in need of the item,” Loper added.
Gaining visibility to supply storage everywhere
“Hospitals typically have visibility of their onsite perpetual inventories in central supply or central sterile, however, that does not account for all of the inventory available to a hospital,” said Zach Malingowski, Senior Director, Medline Supply Chain Optimization. “Best-in-class inventory visibility includes hospital-owned inventory stored throughout the entire supply chain network, including inventory stored in nursing supply areas, offsite warehouses, and with a third-party logistics provider.”
When evaluating hospital storage areas, Malingowski says he often finds supply rooms underutilized. He recommends maximizing existing storage space by using wider and deeper wire racks/shelving, and designing a mix of location sizes into spaces, while always including open storage space for growth.
“Inventory demand is not static; a hospital must be able to increase/decrease an item’s on-hand quantity while storing it in the most optimal location size,” said Malingowski. “The space for growth is needed so new items and higher on-hand quantities can quickly be added to support new patient services and increases in census.”
“Not only can you change the SKU number and PAR quantities, but the label can also display nurse-friendly descriptions, reflect a temporary substitute SKU number, and alert end users of a manufacturer back order or product recall,” he said. “There are a handful of vendors out there that sell electronic shelf labels, including Medline.”
Achieving just in case without the clutter
As David Phillips, Marketing Manager, Hänel Storage Systems, explains, many hospitals have reconsidered ‘just-in-time’ inventory management methods because of pandemic related supply shortages. He states:
“A ‘just-in-case’ method is more proactive and dictates a healthy stockpile to avoid running out of inventory. The trick is to find a proper balance between the two. A consequence of a poor inventory management strategy is that supplies could be prematurely exhausted or unavailable for medical procedures, which in turn can compromise patient care.”
According to Phillips, most hospital shelves are only populated with supplies from about knee to shoulder height because staff members find it too difficult to access items from the top and bottom shelves.
“The next time you’re in a hospital, look up. Vertical space overhead is often the most vacant. This area can potentially store lots of inventory, minimizing the need to expand through walls to acquire more space. It’s also far less expensive to grow vertically through a ceiling than it is to increase a footprint horizontally.”
To make vertical supply shortage space accessible and usable, Hänel Storage Systems offers the Rotomat Automated Vertical Carousel, which stores inventory in unused overhead space, densely packed for a truly efficient use of space. Onboard software integrates with the hospital’s ERP and tells users exactly the inventory quantities on hand. It also brings all stored items to the same waist-high level upon request, eliminating the need to repetitively bend, reach or search for items.
Applying Lean manufacturing principals for greater efficiency
“Nurses need fast and accurate access to potentially life-saving supplies to provide good patient care,” said David Jacobson, Marketing Manager, Akro-Mils. “When hospital storage rooms aren’t effectively managed the result can include wasted time searching for the correct supply, potential for over- and under-stocking supplies, expired product used, and additional labor time to address emergency stockouts.”
Jacobson recommends hospitals incorporate Lean manufacturing principles, such as 5S (everything has a place and everything in its place) and Kanban systems (employs visual indicators to avoid stock outs), to improve supply management productivity.
He notes that bins are used in multiple ways to manage inventory. Some hospitals use a 2-Bin Kanban system that consists of two stocked bins with one bin holding the primary stock and the second bin (usually located behind the primary bin) holding the backup stock. When the primary stock is depleted, the first bin is sent for replenishment and the backup bin becomes the primary stock. He says another approach is using bins attached to electronic scales that are connected to an inventory system. When stock gets low, central storage is notified electronically to refill the bin.
“Akro-Mils products include our AkroBin and Shelf Bins, which are widely used in hospital storage rooms and can be adapted to integrate into many types of inventory control systems,” Jacobson added. “Both bins come in multiple colors that can represent the types of products contained in the bins—or translucent to see the contents – and spaces for labeling.”
Boosting clinician confidence in supply management
The practice of hoarding supplies wreaks havoc on inventory management, according to Dave Salus, Market Manager, Healthcare Division, InterMetro Industries Corporation. A nurse putting aside products for emergency use can lead to other nurses not having what they need and creating their own supply stashes, and it snowballs from there.
“Now, the supply tech is noticing the increase in ‘consumption,’ so replenishment amounts are increased to keep up with the ‘increased demand,’ said Salus. “You can see how this can quickly spin out of control by expanding this to all SKUs in all the stocking locations that are used by countless people. This inevitably leads to excess inventory, and worse, it leads to inventory that is no longer controlled. It all comes down to trust, trust in that what is needed will be there, when its needed.”
InterMetro Industries Corporation offers a variety of supply storage and organization options to support inventory management solutions. These can be open or enclosed and deliver high density storage or high visibility and access. They include moveable aisle track solutions, cantilevered baskets, adjustable wire shelves, slanting shelves, as well as totes and bins.
Safeguarding drug supplies
Given the numerous associated costs and risks, security and safety issues around hospital drug supplies are always a concern in healthcare facilities. Phillip Van Gorp, President, USA Belintra Med IT and Storage Solutions, cites growing threats of theft and malpractice from pharmacy to bedside when medication management processes are not controlled and documented properly.
“Individual medication distribution at patient level is in great need of higher security,” said Van Gorp. “Making sure the right medication is administered by the nurse holding the required authorizations at the right moment, and to the right patient is a challenge. Bedside scanning of patient, nurse and medication is the only way to guarantee a safe closed loop.”
Belintra’s medication distribution carts allow hospitals to control, track and trace access to specific drawers by a USB controlled single sign on technologies. Medication distribution is based on unit dose, allowing for greater efficiency and cost saving. The advanced computer on wheels (COW) controller facilitates individual battery management, with DC over AC power that gives a 20 hour battery life.
“As every hospital has its own way of working, we are offering various locking alternatives on our trolleys, as well as different capacities in respect of which volumes of medication is being distributed or administered,” Van Gorp added.
Automating drug distribution
In addition to risks for drug loss, expiry and diversion, Len Hom, Director, Point of Care Marketing, Omnicell, says poor management of medication inventory can lead to clinician frustration and delayed patient therapy as caregivers are forced to search for drugs when they need them.
“Technology is the great equalizer when it comes to improving operational efficiency,” said Hom. “Cloud-based software solutions, connected to pharmacy automation solutions, can provide real-time inventory visibility and predictive and prescriptive analytics that remove manual steps in inventory management, saving time and money. Especially with today’s labor shortage, you can maximize pharmacy tech time by assigning them tasks in-app, and once the tasks are completed, the pharmacy admin can see the completion in real time. This saves time from having to make phone calls or manually tracking restocking, destocking, par level adjustment activities.”
Omnicell One is a technology-enabled service that provides visibility, insights and workflows to optimize medication inventory management. Integrated Intelligence with the XT Automated Dispensing System allows hospitals to leverage predictive and prescriptive analytics to aggregate and analyze data, delivering the visibility, insights and workflow tools to elevate pharmacy performance. Operational dashboards make it easy to quickly locate a medication across a health system, track COVID-19 medication use trends, and identify compliance issues that may indicate drug diversion.
Expanding options in medical/surgical supply management
In recent years, BD has made major investments in new supply chain automation solutions for the point of care (POC) with its Pyxis Supply Portfolio to meet the changing needs of its hospital customers. The company also offers flexible leasing options on all POC solutions through which customers can modify their “footprints” in terms of automation technology to meet changing needs.
“We want to partner with our customers to make sure they can not only meet cost, quality and outcomes (CQO) goals today, but also with whatever challenges they face in the future,” said Theo Stephens, Associate Director U.S. Region, Pyxis Supply at BD. “Using our assessment tools we can go into a hospital, understand their supply challenges and quickly come back with an automation strategy customized to address their specific pain points.”
BD Pyxis offers two open solutions through which a hospital can use existing supply storage infrastructure for management and replenishment of medical/surgical supplies. One is ParActive where each item in a par location is assigned two RFID cards. A clinician places a card into an RFID-enabled “mailbox” to alert materials management of 50% inventory depletion, and the other card to communicate a stockout. The second solution is StockStation, a barcode scanning inventory management system for POC product capture of chargeable items in the operating room (OR).
For secure management of chargeable supplies, BD Pyxis offers RFID enabled cabinets, that, along with their other solutions, are integrated with the hospital’s electronic health record (EHR) and financial systems to automate supply documentation, charge capture/billing and process reorders. The company’s open and secure POC solutions are integrated with one another to deliver data and insights all in one place.
A single approach to medical/surgical, drug supply chains
Historically, hospitals have managed their medical/surgical and pharmaceutical supply chains separately, using individual IT systems and workflows. This is changing as health systems and hospitals seek to standardize supply chain systems and processes for clear and immediate visibility into all supply spend and utilization.
“For most hospitals, there’s a thornbush of best-of-breed bolt-on systems to manage medical and drug supplies, but when you pan out to a hospital or health system level, that creates a mixed bag of data and visibility, and you miss out on that command center view — being able to see what’s going on in ‘all’ areas,” said Cory Turner, CMRP, Senior Director, Healthcare Strategy, Tecsys.
“A lack of visibility translates into ordering challenges, unexpected stock-outs, expiration and recall management issues, and ultimately not having the right products at the right time; all of these things, on top of being supply chain issues, are clinical distractions that erode patient care,” Turner added. “At a time where nursing labor shortages are rampant, using clinical resources to shore up an ineffective supply chain practice should be out of bounds, especially when the right supply chain processes and technologies can avoid that burden on nursing.”
“It harkens back to the importance of visibility and control, and how an end-to-end supply chain management strategy focuses on building a whole that truly is greater than the sum of its parts,” stated Turner.
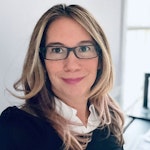
Kara Nadeau | Senior Contributing Editor
Kara Nadeau is Sterile Processing Editor for Healthcare Purchasing News.