Having had enough of the pandemic, hospitals simply want just enough supplies
Back in the go-go 1980s, low-unit-of-measure (LUM) distribution concepts such as just-in-time (JIT) and stockless were emerging as quite the rage among forward-thinking, progressive materials management leaders.
For many, these “new” – at least in healthcare – methods were seen as perhaps the greatest process improvement since sliced bread. These days with supply chains strafed by pandemic-induced backlogs and shortages, more seem to view sliced bread as an expensive novelty and likely prefer sticky buns.
During his keynote address at the Association of Healthcare Resource and Materials Management (AHRMM) conference last August in Nashville, award-winning professor and consultant Randy Bradley, Ph.D., CPHIMS, FHIMSS, Associate Professor of Supply Chain Management and Information Systems, University of Tennessee Knoxville, Haslam College of Business, Department of Supply Chain Management, highlighted three distinct Achilles heels that threaten faith in – and perhaps viability of – JIT distribution.
Those three elements? They form an equation. 1. When you have a supply shock. 2. When you have a demand shock. 3. When you have a price shock from the supply and demand shock.
“We got all three – not just one,” Bradley said. “And when demand outpaces supply we try to overcorrect.” The resulting focus on stockpiling he billed as “JIC” for “just-in-case” as one end of a seesawing trend back-and-forth. “We will see more of this,” he predicted. “When things get good, you’ll swing back.”
What the industry needs is a new philosophy, according to Bradley, called “JE” for “Just Enough.” This “requires you to do demand planning, demand sensing and demand shaking,” he added.
Where do we go now?
Supply Chain experts believe the healthcare industry still has miles to travel before that becomes standard operating procedure but remain mixed on JIT’s future demand.
“No organization wants a repeat from the pandemic, so returning to the same practices from two years ago would be short-sighted,” said Sandhya Dhir, Head of Healthcare Strategy and Development, Amazon Business. “Now is the time to embrace new technologies and new supply chain models to build more resiliency. While some of the shortcomings of the JIT model were exposed during the pandemic, managing backorders and stockouts has always been a concern for healthcare providers, to the point that industry almost turned their back on recognizing this is a problem that can have better solutions. A way to create a balance and still be able to rely on a JIT model is to ensure an organization is already set up to access multiple sources of supply as soon as fluctuations, especially when not predictable, occur. In addition, leveraging newer e-commerce technologies including ERP API integrations, approval workflows, auto-reorder tools, and real time analytics builds efficiencies during times of supply uncertainty.”
What’s clearly recognized is that the pandemic shook healthcare supply chain’s faith in and reliability on JIT to the core.
“Over the years, the healthcare industry became overly reliant on a just-in-time (JIT) delivery model and other approaches, like ‘stockless,’ that helped cash-strapped healthcare systems trim costs,” noted Michael DeLuca, Executive Vice President, Operations, Prodigo Solutions Inc. “The method had its benefits: It kept operating costs low, while still allowing hospitals to operate efficiently and order medical supplies when needed, and it placed a priority on driving down inventory-related expenses. This approach was applied across health systems for all medical supplies and mirrored best-in-class inventory and fulfillment practices of Fortune 100 manufacturers.
“In 2020, many hospitals had to re-evaluate this model in real time as they adjusted purchasing models,” DeLuca continued. “The grim reality of the pandemic proved that the healthcare industry no longer has any choice but to apply the painful lessons we have learned and pivot to a more thoughtful and strategic approach to supply chain management and demand planning. As our nation emerges from the COVID-19 crisis, it is critical for the industry to step back and re-evaluate past practices so that the industry is better prepared for the future.”
Everyone’s going to have to work together on this, according to DeLuca.
“Maintaining a more strategic level of preparedness will require a long-term commitment from healthcare systems, medical supply distributors, manufacturers, and the federal government. And most importantly, health systems need to work together and support one another in creative solutions – this collaborative spirit is what will unite the industry for whatever is in our future,” he added.
It’s a control thing
What the COVID-19 pandemic cast in doubt really is who had – and has – control over product.
“Hospitals want and need to control supplies for patient care. But with just in time or stockless methods, they are putting all reliance on a distributor or manufacturer,” indicated Cory Turner, CMRP, Senior Director, Healthcare Strategy, Tecsys Inc. “It takes control away from the hospital’s supply chain and puts it into the hands of these third parties.
“Supply chain teams are the experts in what their facilities and clinicians need in terms of products to care for patients, so supplies must be in a place where they can manage them effectively. More and more hospitals are looking at consolidated service centers (CSC) as more of a need than a want. They are increasingly leveraging CSCs to put supply chain squarely in control over supply management as opposed to relying on distributors or manufacturers.”
Still, Supply Chain experts agree, by and large, that JIT isn’t dead and done – not by a longshot.
“I think the industry has learned that just-in-time has its place, but it should not be adopted across the board,” said Tom Redding, Senior Managing Director, Healthcare Services, St. Onge Co. “When considering the use of a CSC, an organization can continue a just-in-time model, which is based on their ability to carry a larger subset of inventory to handle the larger variation in demand.
“There is some hesitation in the market to actively pursue a stockless program with a distributor, versus considering the option to do it themselves,” Redding continued. “As the market changes, the distributors will further bolster their [third-party logistics] services to assist their clients with running a CSC. The easy answer is to do it yourself but having the knowledge, experience and systems to run a distribution center should be taken seriously.”
Alex Wakefield, CEO, Longbow Advantage, concurs.
“We aren’t seeing just-in-time necessarily go away as a strategy, but supply chain teams are definitely revisiting how they approach these types of strategies,” he observed. “For some, this has come in the form of stocking up. However, the reality is warehouses or [distribution centers] can only hold so much product. For supply chains that are looking to restructure their just-in-time strategies, they’ll need to be hyper-vigilant about efficiency when it comes to storage, throughput and things like cross-docking for more immediate shipments in order to maximize the space they have. Visibility into – and maximizing – warehouse capacity and order fulfillment across the network will be more important than ever before for companies that need to increase contingency-order storage.”
Finding balance
JIT among other LUM models certainly has its limitations, which should encourage supply chain professionals to expand their toolsets, according to Steve Kiewiet, FAHRMM, FACHE, COO, CCS Medical, and Immediate Past Chair, AHRMM.
“I don’t think the concepts shattered,” he reassured. “They have been effective tools for decades. However, they are not the only tools, and it means we need to be more proactive in understanding the balance of supply chain cost and risk. This allows us to deploy the correct inventory management and supply chain tools to fit the risk and cost situation. The breakdown we all experienced here is because many supply chains became highly focused on one tool and had too strong of a focus on removing cost, etc.
“JIT was built specifically for a single-piece flow assembly line environment while operating with well-known demand and little-to-no variation,” Kiewiet continued. “Healthcare is not that environment. We still don’t have good demand signals, we don’t reliably share information freely across all links of the chain and we have a lot of variability. There are places where JIT and stockless can and will work but it won’t work everywhere. Just like healthcare is moving more and more to precision medicine and patient-focused outcomes and treatments, we need to bring in a variety of tools and methods to manage our supply chains that support this delivery of care.”
Rather than why JIT may no longer work, the real discussion centers on for what it specifically does and does not work. Some have a few ideas.
“While just-in-time inventories can be cost savers and conveniences on typical days, they are very problematic in a pandemic or another scenario that sees massive demand surge,” noted James Ludwig, Vice President, Partnerships, Premier Inc. “Experience shows that for products needed in an emergency, a hybrid approach is probably necessary: Buyers carry in-house inventory on a just-in-time basis, while manufacturers and direct sourcing companies take a just-in-case approach, reserving capacity for surge, retaining safety stock, and building rapid replenishment channels for restock.”
Ludwig cites Premier’s ProvideGx generic sourcing program as one example where Premier requires manufacturers of critical products to source from multiple, diverse locations and carry adequate amounts of safety stock in exchange for long-term, committed-volume contracts. “In the case of COVID-19, ProvideGx validated that suppliers had four-to-six months of active pharmaceutical ingredients on hand, as well as four-to-six months of finished dose form products,” he said. “With safety stock on hand, it was possible to weather surge demand of more than 150 percent, even as health systems continued ordering just-in-time. This model works for low-margin generic drugs, suggesting it could work equally well for other critical, low-margin items.”
He also indicates that “greater intelligence and improved technology can help providers estimate case load surge and automate the prediction of future supply needs. In this way, ordering is more evidence-based, data-driven and rationalized to align with anticipated caseloads. Such systems exist today and will be crucial for rationalized buying in future emergency events,” he added.
“[JIT] can work for certain items like drugs and other medical products, but pandemic-related items should have more safety stock,” said James Sembrot, Senior Vice President, U.S. Supply Chain, Cardinal Health. “At Cardinal Health, we’re also increasing safety stock of our raw materials and components used in manufacturing. This deviates from Kanban relationships we normally would have with suppliers and helps insulates us from significant disruptions if there are raw material issues.”
Medline Industries isn’t necessarily seeing a shift away from or unwinding from JIT or stockless distribution methods, according to Peter Saviola, Vice President, Logistics and Supply Chain Optimization, but they do see the move to low-unit-of-measure from bulk deliveries continuing as “more of a hybrid approach that complements JIT with a small cache of on-site inventory,” he added.
“Most health systems are now maintaining a 30- to 60-day stockpile, and looking to their distribution partners, like Medline, to have inventory available to compensate if, and when, needed. We are seeing this approach being taken across healthcare systems of all sizes – from small to large,” he said.
Mike Henry, Managing Partner, Ron Denton & Associates LLC, calls for considerable dedicated supply chain soul searching among healthcare organizations to determine JIT’s prospects and relevance.
“There’s a risk of conflating different and largely unrelated issues here,” he indicated. “JIT, stockless and logical unit of measure programs should be viewed as a means of efficiently moving routine supplies to end use locations while reducing process redundancies and friction. These programs in no way preclude the provision for providers to plan for and maintain strategic contingency inventory. In fact, these programs can enhance those capabilities by freeing up space and other resources to focus on contingency inventory and related processes. Supply Chain professionals should ask themselves: Are there routine tasks that we do every day that could be moved upstream in the supply chain that would free up our resources to focus on higher value activity?”
For JIT to experience a renaissance will require deeper and more intense collaboration between provider and supplier, according to Jake Crampton, Founder and CEO, MedSpeed.
“Even before the pandemic, there were trust issues on supply availability and workarounds – desk/ceiling stock, for example,” Crampton said. “But acute safety issues like N95 shortages during the early days of COVID-19 touched a nerve, so establishing enough trust to move back to even a new and better JIT model may take some time. Supply chain teams left no stone unturned in their search for PPE for their clinical counterparts and learned many lessons about the need for previously unheard-of contingency planning protocols. To return to a JIT model, the supply chain will need to have full transparency with the clinical staff around the rationale for the change and the playbook if another COVID-like event challenges the supply chain in the future.”
Margaret Steele, Senior Vice President, Med/Surg, Vizient Inc., admits that pre-COVID, she heard speculation that up to 70% or hospitals engaged in some degree of just-in-time or low-unit-of-measure ordering.
“Throughout COVID, we heard comments that supported the saying, ‘the only trusted inventory was a facility’s owned inventory,’” she said. “While we don’t envision these practices as dead, we do anticipate them evolving. Sequestered or protected inventory creates some additional assurance to those facilities looking to source in this manner. We’ve seen increased requests for dedicated space within a traditional distributor’s warehouse to ensure protections and accurate inventory visibility. Additionally, providers are seeking to secure secondary distribution partners to provide additional avenues in case of stockouts.”
Read on:
Next-generation distribution models must embrace that syncing feeling
Just-In-Time’s popularity fades in struggle between other, emerging models
Useful strategies, tactics that may redefine post-pandemic distribution
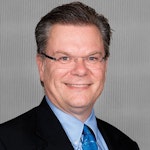
Rick Dana Barlow | Senior Editor
Rick Dana Barlow is Senior Editor for Healthcare Purchasing News, an Endeavor Business Media publication. He can be reached at [email protected].