With access to all of the resources and technology available now or in the very near future, one might argue convincingly that healthcare organizations have what they need to effectively monitor and manage product alerts and recalls.
From wired or wireless, cloud-based software to subscription-based notification services (via pull- or push-based communications) to artificial intelligence to online programmable search bots to dedicated staffers or teams with information technology skills, Supply Chain’s product alert and recall process toolbox seems rife with options.
And yet, product alerts and recalls consistently continue to evoke panic (however mild) and pressure to do more or the painful realization that not enough is being done. Of course, the question remains, how can or do you predict an alert or recall? Without precognition or any kind of prognostication, perhaps proactivity has its limitations.
Short of shoring up your offense, the focus must then shift to strengthening your defense and streamlining your reaction.
Equipped with a team of IT-savvy Supply Chain professionals (or even fluid connections to IT pros) operating within a well-documented process, online access to a notification database service that includes links to government resources, and an expedient way to track and remove a product from circulation as well as notify affected patients quickly, healthcare organizations should be set, right?
Not so fast.
Because product alerts and recalls should happen so infrequently, healthcare organizations may not give the issue a high-enough priority (despite the considerable liabilities), which dovetails into a lack of budget for necessary talent and technologies, including tracking tools and software connections to electronic health records (EHRs). They also may not realize the impact on product warranties and how that ties into Medicare regulations and private payer reimbursement.
For more information on setting up processes for product alerts and recalls, visit HPN’s online archive at https://cdn.hpnonline.com/inside/2011-03/1103-PS-Recalls.html, https://cdn.hpnonline.com/inside/2012-09/1209-PS-Recalls.html and https://cdn.hpnonline.com/inside/2013-09/PS-Recalls.html.
Alerts and recalls occur for a variety of reasons. Many tend to involve manufacturer issues – either functions or components were found to malfunction in some way or quality measures in the manufacturing process weren’t followed or documented properly; others may involve products damaged via distribution or in transit; products damaged in the cleaning, disinfection or sterilization process as component materials reacted negatively to chemical or gas exposure; or patients’ physiology reacting negatively to product exposure or implantation.
Whatever the case, product alerts and recalls remain a reality, no matter how frequent, and must be addressed in terms of tracking, tracing, notification, retrieval and all of the communications and record-keeping along the way.
Future looping
One of the strategies behind designing a new product or process or even redesigning an existing product or process involves thinking big, looking at the end game or desired outcome and working your way backward. It’s essentially akin to reverse-engineering effectiveness for efficiency’s sake.
For seasoned experts in product recalls and alerts, the underlying premise resides in convenience through automation and quick communication. Think smart notification and response. While we may not be there yet, forward thinking just may have the industry on its way.
“If money were no object, we would supplant manufacturing sites altogether and place 3-D printers, capable of printing real-time sterile product and implants, in every OR and patient treatment area across the country,” Powell envisioned. “Inventory would be tracked in terms of raw materials for printing, rather than physical product, helping alleviate the nearly endless shelf space that healthcare organizations today must dedicate to millions of SKUs that we may use on a daily basis.
“Absent of that happening, an ideal solution to this would be a WiFi- or Bluetooth-enabled sticker that automatically turned red in the event that a recall on that specific lot was activated,” Powell continued. “This sticker could also turn red upon expiration of the sterile shelf life or the half-life of a drug. This would prevent accidental use of incorrectly tracked product at the site of patient care.”
Sources point to the Food and Drug Administration (FDA) and data standards via the Unique Device Identification (UDI) initiative as the most practical and realistic option.
Lohkamp posits that interoperability and even blockchain could facilitate and streamline information transfer.
“Enabling this will require adoption of interoperable technology that could be used to share this information,” he continued. “Blockchain is a promising technology to support track and trace. With blockchain, the manufacturer could initially place the item on blockchain and each party could potentially reference that item and add transactions to the ‘ledger’. This could provide the quick visibility required. Of course, core ERP, point-of-use and EMR systems would need to be able to update or view data from the network. And to scale up, product auto-id processes, computer vision, RFID and other automatic sensing technologies would be needed to remove heavy human intervention to capture details on each individual product as it is picked or consumed.”
Digitizing the din
“With respect to recall and safety notices, there’s a lot of noise out there,” Hardin determined. “There are official FDA notices, preliminary vendor recalls (not yet FDA validated), MAUDE reports, vendor notices, incident reports, and more. Ultimately, I’d want a process that makes the management of safety notices and recalls more efficient, that considers all recall related documentation and that’s gives visibility to all related stakeholders. I envision a single technology repository (i.e., a blockchain structure) for Food, Pharmacy and Medical Devices that would be the clearinghouse and source of truth for all related transactions.”
Hardin points to integration as a necessity and validated information.
“With clear visibility to all recalls and the like we’d then have the ability to materially redesign the human and technology-related aspects of recall and safety notice management,” he continued. “For example, we’d be able to easily identify those notices that are preliminary in nature, and contrast and compare those notices with their corresponding validated FDA notices. Integrating with CRM and ERP systems would allow quick identification of provider exposure to risk – whether those materials are in house or in-patient. Such integration would also allow providers to assess the actual cost of recall mitigation based upon the time required to remediate, as well as the resource types required to execute each recall action. With this information, I can envision more informed capital equipment negotiations, including limits on how much expense the provider is willing to accept to remediate defects. Accordingly, any costs above the negotiated limit could then be passed on to the supplier.”
Suppliers would benefit because they ideally would also be able to track the remediation progress in real time, according to Hardin.
Hardin envisions nearly endless opportunities. “A chronologic single source of truth for all recalls and safety notices is the foundation from which many good things can build,” he said. “Cost is also a critical factor, and probably the primary reason why we haven’t already seen major technological advancements in this area. But the technology to make revolutionary changes already exists, and over time will become more affordable. So, I don’t think a next generation solution is very far off.”
“I would require (1) that every end-user provider scan all items into their inventory, (2) the scan must be 3-D so that all data can be on the barcode, and (3) UDI numbers would be on all products produced by and sent from manufacturers and their distributors to the providers so that they, too, are part of the 3-D scan,” Cohen recommended.
Flag the FDA, UDI
“Today, medical device recalls are reported to hospitals primarily by manufacturers,” Casady noted. “Information may be shared in spreadsheets, emails or other diverse formats that require hospital staff to interpret them. The FDA reports device recalls as well, but it can take several months before they are distributed. With the emergence of the FDA’s UDI on device packages, the time has come for the FDA to be the primary source of all recall data for hospitals across the country.
“The most efficient way for the FDA to report recalls would be through an API that is accessible by all healthcare stakeholders,” Casady continued. “The recall data would not only include legacy product codes or model numbers but also new UDI data. The matching of recalled devices to products stored by manufacturers, distributors and hospitals could be accomplished through barcode scanning or RFID sensors by all stakeholders prior to transfer/shipment and prior to patient use. Recall data should be uploaded in real-time, via the proposed FDA API, to software used to monitor storage, transfer and use of these devices [in order] to provide instant notification to all stakeholders when a device is scanned.”
“Leveraging new and developing technologies, data capture and exchange about patients’ and physicians’ use of medical products could one day become automated, linked to individual records and facilities, and located for remediation quickly and efficiently,” O’Bara noted. “Providers and patients could then be notified of recalls and alerts in real time.” At that time healthcare organizations and patients alike will recognize the “power of comprehensive, standardized and interoperable data across the entire healthcare ecosystem,” eliminating information gaps and reinforcing safer, quality and more efficient care, she added.
O’Bara acknowledges the ongoing debate between information sharing and personal privacy creates friction with the need to automate information recording. Achieving balance among these hot-button issues will lead to transparency, she indicated. “While we already have the technology to associate specific products with patient electronic health records (EHRs), the use of that information is often limited by concerns about privacy,” she continued. “Scanning medical device or pharmaceutical barcodes into patients’ EHRs at point of care as they are administered provides data that is crucial not only in a product recall or alert, but also for tracking the product’s effects.”
Artificial Intelligence (AI) should play a vital role as it provides “unprecedented computing power” for data gathered from millions of patients across many geographical locations “to enable proactive and predictive analytics that can be used to quantify occurrences of side effects, product performance issues and adverse events, O’Bara noted.
“The ‘machine learning’ of AI can detect and identify links between co-occurring and seemingly unrelated conditions or outcomes, drastically multiplying the power of data analytics to inform and educate the medical community and advance the practice of medicine,” she said. “In addition, automated information sharing has the potential to help reduce clinicians’ role in data collection and assimilation, freeing them to focus on patient care.”
O’Bara sees the capabilities of computing power hamstrung by privacy measures, and hampering efforts to analyze data around product use and effects on individual patients. Still, cybersecurity must be an “increasingly important prerequisite for locking down patient information without losing its value,” she added.
Schiller credits Mike Nolan, President of Automatic Identification Systems (AIS), for this vision, which, he further argues that “baseline infrastructure and technology already exist to make this vision a reality.
“There are applications available today that have the ability to access recall and adverse event databases where a scan of the UDI Device Identifier (UDI-DI) and Production Identifier (UDI-PI) would confirm whether a product is affected by a recall,” Schiller said. Touchpoints include order fulfilment activities at the manufacturer or distributor level where scan technology is typically incorporated, receiving activities, subsequent stocking activities and point-of-care consumption within the healthcare organization setting where scan technology may or may not be deployed, he added.
Schiller describes a potential scenario: The first validation touchpoint would occur during the product pick activity at the manufacturer or distributor warehouse. For the second validation touchpoint, prior to shipping the order, the manufacturer or distributor would include the UDI-DI and the UDI-PI into a “license plate-type” barcode for all of the product that has been packaged in the box or carton. For the third and fourth validation touchpoints, this barcode license plate would be scanned at the receiving location, and the individual product would be scanned at the stock location, capturing both the stocked quantity and the stock location. Validation touchpoints five and six occur when the product is picked for consumption and consumed at the point of care.
He also believes this model could be carried downstream into the home health setting where consumers would have the ability to scan products ensuring their safety prior to use.
Horizon scanning
Beyond capabilities and technology currently available, sources point to several options to reach the next level of development. Those options center on real-time access to information.
Artificial intelligence (AI) capabilities seem the most attainable.
“We at National Recall Alert Center are happy to report that Artificial Intelligence (AI) is already a major part of every recall we transmit to our member facilities and we use it in our four-phase data filtering system,” NRAC’s Cohen said. He further added that they would like to incorporate RFID technology in the future.
Rfxcel’s Wong calls for IoT technology to provide real-time, one-way and two-way notifications to consumers during a recall. For example, an IoT-enabled bottle can monitor storage conditions (e.g., temperature, light, humidity) and send alerts if pre-set parameters are exceeded and the integrity of the product is at risk.
“This two-way feedback introduces enormous amounts of complex data into the supply chain, which can be difficult for traditional systems to process,” Wong indicated. “Artificial intelligence (AI) can deal with these large volumes of data, enabling smarter monitoring of the drug supply chain to not only manage recalls but provide proactive warnings about products that may need to be recalled due to incorrect handling or storage.”
Because the recall process is so complex, multiple stakeholders need to be aware right away when specific devices are affected, such as implants, according to Champion’s Casady. Electronic scanning facilitates preventive measures and may portend predictive capabilities.
“Utilizing scanning and/or RFID technology can play a major role in preventing hospital administration from ever picking up and using recalled implants,” Casady said. “Further, as passive identification technologies become more commonplace, patients and their primary care physicians should also be able to be made aware of concerns.”
Casady forecasts a day when regular annual check-ups involve a scan of implants to ensure none is negatively impacted. “The specificity of UDI provides tremendous potential for artificial intelligence (AI) to help predict and identify early trends with recalls,” he noted. “Today, recalls tend to be highly reactionary with providers attempting to catch up with communications as they are released. I envision a day where data is mined to help manufacturers figure out additional related implants that are at risk. This type of predictive information could also help hospitals prepare and understand how widespread or impactful a recall might become. Eventually, past trends may also help providers navigate and determine which implants are safest to use based on prior recall data available at their fingertips.”
Workday’s Lohkamp believes that absent of a “perfect process,” providers should have enough available technology to improve their recall process. Just follow the paper-to-digital trail.
“Ideally, recall notices would come in electronically, using modern webservice technology, and actions could be quickly initiated,” Lohkamp noted. “Unfortunately, since many recall notices come in on paper or via PDF, many health systems struggle to pull the notice into an electronic format so it can be easily searched and matched. Artificial intelligence, and specifically machine learning, can be leveraged first to capture data off the document and then to go through the data to identify things like GTIN, lots, serial numbers and more. Once in electronic form, that data can be used to automatically search your ERP to determine if that item was ever purchased and if it is still on-site.”
Blockchain, robotics show promise
Lohkamp remains somewhat mixed on the applicability of such tech as robotic process automation (RPA) and blockchain.
“Within the context of recall processes, robotic process automation (RPA) could help to automate and orchestrate processes across disparate systems,” he acknowledged. “For example, if recalls are being tracked in a central system or database, RPA could be used to take details about items that are recalled and compare that to data in other systems like a Point-of-Use or even a clinical system. RPA would automate that check and report back on the results. Blockchain also has the potential to support a full track-and-trace system but will require significant commitment from the industry, including regulatory support.”
Hardin expresses concern that “access to blockchain data for risk exposure assessments, access to AI for data mining, and even sensors for location information might be directly relevant for provider stakeholders,” but they miss the big picture. A full solution must consider all stakeholders (providers, suppliers, regulators, distributors, etc.), their relative perspectives, immediacy and operational objectives, he added.
“If 3-D printers could print real-time sterile product and implants in every patient treatment area, blockchain would be essential to track the production site for the printed implants,” envisioned Premier’s Powell. “If we implemented a WiFi- or Bluetooth-enabled sticker that turned red to indicate a recall, sensors that could receive communication from a centralized communication/alert dispatch center would be critical.”
GS1 US’ O’Bara foresees the growing relevance of IoT “as one day in the near future, everything that can be connected, will be connected.
“In a healthcare setting, full connectivity in an ideal world could eventually mean that information about the devices and medications used in a patient’s care will be automatically recorded into their EHRs; the products can easily be tracked in the case of a recall, and pulled from inventory and updated, corrected or removed from patients’ treatment protocols; outcomes and side effects will be automatically captured and recorded; and authorized providers and caregivers will have immediate access to all of the data they need to follow, monitor and act on new information in real-time,” she said.
O’Bara also predicts that both AI and distributed ledger technology, such as blockchain, may transform healthcare by improving data management.
“Distributed ledgers can be useful in providing a record of trust, ensuring that the product’s chain of custody is accurately recorded in an immutable ledger – which is helpful not only for processing recalls and alerts but also for patient safety,” she continued. “Any distributed ledger technology is only as good as the information that is uploaded to it, so it is essential to use data that is based on a foundation of global standards for interoperability. When a healthcare provider is able to upload information in patient records, the unchangeable nature of distributed ledgers adds a layer of confidence that will enhance healthcare outcomes and key decisions to be made by patients with their providers.”
Alan Gormley, Vice President, Operations, EMEA, SteriTrack, encapsulates the answer residing “somewhere between the innovation adoption curve, priorities, and an acute underestimation of the benefits that end-to-end supply chain visibility can yield.
“Leveraging new technologies can be a road fraught with dangers,” Gormley warned. “Costs can be high, compatibility and interoperability can be a challenge and market adoption may not even be realized. When considering such a multi-stakeholder challenge such as recalls, market adoption is critical. Every stakeholder needs to speak the same language so devices that have been recalled from the market.”
Gormley points to the barcode and UDI as the “foundational building block of supply chain transparency” from which to develop and advance.
“A barcoded UDI provides a single language that stakeholders can communicate about a device that has been recalled and remove some of the panic that ambiguity results in,” he indicated. “Labelling a device is foundational. Manufacturers need or should move beyond labels and Direct Part Mark (DPM) devices if they want to reap the benefits that suppliers and retailers have been enjoying for years. Equally, healthcare providers need to begin to scan UDIs in their own processes and share utilization data back to manufacturers.”
Product recalls, alerts: What did you miss?
Managing and rectifying product recalls and alerts not only represent a complex and necessary process, but also a stress-inducing one. It simply cannot be ignored from a trifecta of standpoints – patient, liability and financial.
Still, it’s easy to understand how something – no matter how esoteric or granular – can fall through the proverbial cracks. Whether overt or hidden, these issues must be identified and addressed.
Healthcare Purchasing News asked five executives who deal with recalls and alerts what healthcare providers and suppliers should monitor.
Peter Casady, Founder, Champion Healthcare Technologies
“An area in the product recall process that is often overlooked, or could be done better, is medical device warranty claims and credit resolution. A 2018 Office of Inspector General (OIG) report demonstrates how this is a pervasive issue. The report cites that 210 hospitals under review did not comply with Medicare requirements for reporting recalled cardiac device manufacturer credits. See the full report here (https://oig.hhs.gov/oas/reports/region5/51600059.asp). Hospital compliance leaders are generally aware of CMS requirements and the detrimental fines issues by the OIG for noncompliance (we’ve found the average OIG fine to be [approximately] $400,000), but managing device warranty claims may not be prioritized because it is a challenging process that requires the efforts of multiple stakeholders to accomplish successfully.
“Beyond the need for multiple departments to contribute, challenges include a lack of clarity on whether a device is eligible for warranty credit, manufacturers are not transparent and timely about communication around the status of warranty claims, and hospitals may not even know how to match a credit with a specific device due to vague information from vendors.
“I believe that hospitals need to prioritize investing in an electronic platform to automate and centralize warranty claims management. This type of platform would enable streamlined and transparent collaboration between clinicians, pathologists, supply chain and finance/revenue cycle to coordinate all activities and touchpoints to ensure warranty processing in a compliant manner. When investing in an electronic platform, it’s also imperative to ensure integration with manufacturers so they can provide automatic updates on the real-time status of each device claim. Without this ability, hospitals must manually compile this information from monthly reports or by directly contacting each vendor for specific claims.”
Dr. Mark Cohen, President, National Recall Alert Center
“Overlooked: The completion of the disposition on every single product that is under recall at any facility.
Solution: We are the only organization that incorporates a five-level escalation system to assure that no recalled product “falls through the cracks.” For that reason, National Recall Alert Center has never missed a bona fide recall since its founding in 1973.
“Overlooked: Class I recalls – those that can lead to the deaths of patients.
Solution: We’ve developed a highly sophisticated triple alerting procedure and system that assures Class I products are treated with extreme alacrity at both levels – at our office when transmitting and at the provider end when receiving.
“Overlooked: Litigation control.
Solution: We are the only organization that maintains a $5-million E&O insurance policy with Lloyds of London for such events.”
Chaun Powell, Group Vice President of Strategic Supplier Engagement, Premier Inc.
“One pressing topic that is being considered globally, and specifically by the Food and Drug Administration, is to reevaluate the degree of sterilization called upon for particular items. As an example, is sterile water needed for colonoscopies? As we continue to face challenges with ethylene oxide sterilization plants, there is a decent probability that we will see a day in the not-so-distant future where sterilization of products that score 10 to -6 on the sterility assurance level (which measures the probability of a viable microorganism being present on a product after sterilization) is no longer necessary. As sterilization of devices expires at that range, it will be interesting to see if there is a subsequent test that could be run to revalidate what currently constitutes expired product, thereby increasing the shelf life.
“There are also more formal product alerts that are tied less to patient safety and more to manufacturing documentation protocols, with the intent to monitor these processes explicitly to the letter of the regulations and registrations with the FDA. We see this frequently with distributors as well. Manufacturers and distributors could examine whether these alerts are indicative of a breach of patient safety protocols, and then determine whether they are necessary or if other solutions exist to account for process regulation.”
Herb Wong, Vice President, Marketing & Strategic Initiatives, rfxcel
“The safety of products can be compromised after they leave the manufacturer. I’d use individual IoT-enabled packages (e.g., bottles) to improve safety in the supply chain because they’d provide optimal traceability at the unit level. Today, IoT-based sensors can still be cost-prohibitive, so they’re attached to shipments or pallets, not individual units. As along as everything stays together, this is not a problem: The IoT device provides proper monitoring of the aggregated items. However, if an individual case or collection of products is removed from a shipment/pallet and is not handled correctly, the mistake could go undetected. This wouldn’t occur with unit-level IoT monitoring, as individual products that were compromised would be detected early (in real time, actually). A proactive, targeted recall of the case or bottles can be issued, protecting consumers and resulting in significant cost savings and brand protection for the manufacturer.”
Michael Hardin, BMET, Senior Solutions Consultant, TractManager
“It’s easy to overlook the life of a recall. The issue is that preliminary recalls are often confused as being functionally equivalent to official FDA recalls. Recalls can be initiated in a variety of ways, like an observation of a defect, or a problem on the supplier’s manufacturing floor. They can also be identified as a result of a complaint from a provider/patient. Once the supplier is notified of a potential defect, they must conduct an investigation to validate the problem, scope and severity, as well as develop a corrective action plan. For FDA-approved medical devices, the supplier must also notify the FDA of the complaint and the ensuing investigation. Once the supplier has completed its investigation and corrective action plan, they are required to provide that information to the FDA — who will in turn conduct their own investigation and review of the supplier’s corrective action plan. It is only then that the FDA will publish an official FDA notice (if warranted).
“Suppliers will often notify providers when they’ve completed their internal investigations. These notification typically happen well before the FDA has completed its process. Every provider receives such notices on a regular basis, either by hard copy or email, and must act upon them appropriately.
“Here’s where things can get overlooked: The recall notice sent by the supplier is technically a preliminary one, meaning that the FDA has not completed its investigation. And, during the FDA’s investigation, the scope of the problem may well be redefined. There could be more products involved, different affected lot codes, or the action plan could change, for example.
“This is where things get tricky. Because I’ve seen numerous examples of providers receiving the official FDA notice, and assuming they’ve already completed the corrective action work based upon the notice from the vendor. Given that the scope may well have changed, one must really compare the preliminary notice with the official FDA notice. Leveraging the product history can resolve this, as well as reconciling preliminary notices from the supplier with actual FDA notices.”
Denise Maxwell-Downing, Vice President, Clinical Quality and Patient Safety, SteriTrack
“Omission of a recalled or warranty step can result in millions of dollars in fines or back payments for a healthcare organization. Healthcare organizations not reporting partial or full medical device credits, or replacements not charged to the healthcare organization for recalled medical devices from the manufacturers, is one area of the recall or warranty process that has been overlooked and has recently been unveiled by the Office of Inspector General (OIG). In March 2018, 210 hospitals were found to not have complied with reporting manufacturer credits to Medicare. This resulted in $4.4 million of overpayments to healthcare organizations that must be returned from the healthcare organization to Medicare.
“Disparate systems with separate workflows set the stage for a lack of availability or poor-quality data, which contributes to medical device recall or warranty processes being overlooked or ignored. Financial and revenue cycle systems assist healthcare organizations to increase accuracy and simplify claim submission and payment management processes, but due to information privacy and security rules the entire clinical record may not be accessible to obtain important information needed for financial decisions. Or if the clinical record is accessible it may contain phrases that result in imperfect matching when the biller is trying to code the procedure. Scheduling practices vary among healthcare organizations and even throughout one healthcare organization. This lack of standardization contributes to coding and billing difficulties especially when a recalled or warrantied medical device was replaced.
“To capture recalled or warrantied medical devices the process should start when a surgical or invasive procedure is scheduled as a revision or replacement. An automated, electronic scheduling form that includes the necessary, minimum data set, for the appropriate condition, value, or modifier codes for a revision or replacement procedure would identify the procedure as having a medical device that is within the warranty or recall period. Collection of only key information assists with managing privacy concerns when the data is needed by diverse professionals. If additional data is needed then communication across the diverse professionals (e.g., surgeon, perioperative supply chain, manufacturer representative, perioperative leadership) can occur. From the scheduled procedure, supply chain staff or the department’s materials manager is notified of the medical device’s recall or warranty status to ensure proper purchase order (PO) pricing occurs. The procedure is flagged for the financial system to notify the biller and accounts payable individual to ensure proper management for billing of the procedure, the device supplier and claims submission.
“This data flow supports appropriate informatics strategies for interoperability. The data will serve ‘dual purposes’ from a single workflow. The system architecture anticipates the need for data linkages and aggregation of data across multiple disparate sources. Also, employing the medical device’s unique device identifier (UDI) in the data collection and exchange assists with verification of the device against available regulatory databases, FDA GUDID and MDR, and against previous procedure claims. The association of UDI data to patients and procedures will ensure the exchange of a recalled or warrantied medical device has occurred. Close collaboration with stakeholders internal to (e.g., supply chain, billing, scheduling, risk management, IT) and external to the healthcare organization (e.g., Medicare and other payer organizations, the FDA, manufacturers) is essential for designing bi-directional data flow and maintenance of this type of process. Input from all the stakeholders ensures the process does not ignore or miss needed steps in the recall or warranty process.
“The other step of the recall and warranty process that is frequently overlooked is adverse event reporting. This step is frequently missed or ignored because the patient and surgeon are already aware of the medical device’s recall status and the medical device is returned directly to the manufacturer once removed during the surgical or invasive procedure. Flagging the procedure when scheduled as a procedure that requires an adverse event report will ensure timely reporting of the event to the registry sponsor to enable further investigation and analysis of the medical device. Registries use this data to compare costs of medical devices to current devices therapies, to establish medical device best practices, especially when off-label use of the device is the norm, and for regulatory post-market surveillance. Healthcare organizations who participate in registry data collection generally receive regular reports containing quality measure information. This information is used to benchmark their performance, to identify areas of potential quality and process improvement and for reporting purposes to governmental and accrediting organizations. The utility of medical device adverse event data to and from a registry is critical for the healthcare organization and the registry.
“Instead of working under the one task one-person paradigm, groups of individuals in the complex network need to perform related tasks together. The culture that values teamwork as a structural foundation for cooperation and synergy, instead of individual performance, is fundamental.”
Siobhan O’Bara, Senior Vice President, Community Engagement, GS1 US
“Today, manual processes are still commonly used to locate and pull recalled products from inventory. As these products are being marked with standardized data encoded in barcodes, as required by both the Drug Supply Chain Security Act (DSCSA) and Unique Device Identification (UDI) rule, those barcodes will be scanned at the point of care so that providers will be able to track identify and notify patients that received the product. In a fully standardized system, products still in inventory will be quickly and accurately located – down to a specific closet on a particular floor within a facility – by matching the barcode scans to Global Location Numbers (GLNs). Providers looking to upgrade their processes and take advantage of these improved capabilities can refer to the GS1 Healthcare US Point-of-Care Scanning Implementation Guidance (https://www.gs1us.org/DesktopModules/Bring2mind/DMX/Download.aspx?Command=Core_Download&EntryId=1583&language=en-US&PortalId=0&TabId=134) for help.
“According to Stericycle Expert Solutions’ 2019 Recall Index (http://www.stericycleexpertsolutions.com/wp-content/uploads/2019/04/StericycleExpertSolutions-RecallIndex-Q12019.pdf), in the first quarter of 2019, 164 medical devices and 94 pharmaceutical products were recalled, including almost 135 million and 13 million units, respectively.
“The ability to marry patient records with product identification and tracking (by uploading the information to EHRs and using AI and blockchain, for example, to amalgamate that data) could be the key to a more proactive healthcare paradigm. We could prevent adverse events by checking the database to verify a product is still good – it has not expired or been recalled, and specific reactions have not been recorded, for example – before it is even put into use. Leveraging data and technology to proactively track product results could improve effectiveness of recalls, minimize the occurrence of negative consequences and improve the quality of care.”
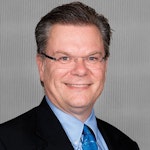
Rick Dana Barlow | Senior Editor
Rick Dana Barlow is Senior Editor for Healthcare Purchasing News, an Endeavor Business Media publication. He can be reached at [email protected].