Storeroom/Warehouse (re)design: Man versus or with machine?
As healthcare supply chain executives and professionals enter the third decade of the 21st century (and third millennium), chatter continues to build on just how much automation and machines will aide, assist, reinforce, support – or even supplant – humans.
Perhaps nowhere is this more evident than in logistics and materials handling in the storeroom or warehouse where hands-on, repetitive, and often weight-bearing tasks are carried out.
As articulating robotic arms, automated guiding vehicles and other forms of computerization and electronic enhancement of duties emerge, the question remains as to whether the ingenuity of invention to help humans work better, faster and smarter will keep pace with or outpace the ingenuity of strategic thinking.
Will people still be needed in the process or will process automation push out the people?
In short, tech alone won’t solve every problem, Slade assures. Like what? He makes a salient case with the following:
- Standardization of supplies used in healthcare – (e.g., go from 65 same size pediatric colored/character bandages to 12).
- Creation and organizational compliance to supply formularies
- Real-time direct visibility of inventory locations and use locations to suppliers
- Supplier/Vendor-managed inventory programs – eliminate intermediary processes in the planning and distribution of supplies
- Industry standard identification / serialization for all medical supplies
- Reduce variability in product packaging, labeling and identification
- Shared accountability and collaboration with suppliers in delivery and cost of supplies
- Focus on Improved reliability, standardization and consistency of supply to reduce inventory levels
- Standardization of industry advanced ship notifications ( ASNs) for direct put-a-way from supplier to storage location and end user
- Enhanced use electronic transaction sets and information exchange
- Humans ceding too much to technology do so at their own peril so they must remain part of the equation.
Jim Richardson, Portfolio Executive, Senior Consultant, Vizient Inc., prefers to think of technology as more of a resource and tool that always will need humans for control and to put to proper use.
“As technology becomes more sophisticated, yes, it can replace many tasks currently being done by people, but in the process, many new opportunities are being created for those people being replaced,” he said. Richardson cited the implementation of a WMS in a distribution center as one example.
“Warehouse workers’ job descriptions completely change,” he noted. “Before they were wasting much time searching for lost/misplaced products in order to fill an order. With the WMS in control, they can do their jobs much more efficiently and productively, alleviating stress and making their jobs much more satisfying. Also with WMS, new and more rewarding jobs are created (e.g., inventory control coordinators who use more sophisticated tools and data to keep inventory information accurate). Technology may eliminate some of the labor associated with warehousing, but it also opens up new job opportunities for the people in those facilities.”
“One fear in the workplace is that man will eventually be replaced by machines, but this is extremely unlikely in a hospital setting because social connections are so important,” Flynn noted. “There’s no doubt that technology assists surgeons and nurses to provide top-notch care, but there’s also no substitute for the human relationship between doctors and patients.
“As far as how human ingenuity and effort outweigh technological prowess, no such imbalance exists within OR storage,” she continued. “What has worked in warehouses and distribution centers for decades has yet to completely work its way into the hospital OR, SPD or off-site warehouse, even though technology sometimes provides solutions to problems before people are even aware that a problem exists. There are many technologies that can meld seamlessly into a hospital warehouse or onsite storage area that boost both productivity and accuracy without completely eliminating the need for human oversight. There are also many jobs within a hospital that require that human touch, but inventory counting and monitoring can easily be automated.”
Healthcare organizations should concentrate more on workflow planning aided by technology, according to Fred Landgraf, Senior Vice President, Supply Chain Solutions, Intalere.
“The most effective methodology is based around a strategic workflow plan that balances data produced from multiple sources of technology daily,” Landgraf indicated. “In some cases, this information can be automated depending on systems, and other times more of a manual tracking. Supply Chain and logistics companies in manufacturing, transportation and/or 3PLs manage all aspects of operations from productivity to financial, with detail around all areas of responsibility, giving the ability to improve individual departments and areas based on their own trends and achievements. Understanding the trends on a daily basis and rolling up to a weekly total or average gives the ability to plan based on the cycles every business experiences and identifying specific areas of service levels in these KPIs gives daily focus and ongoing tracking of achievements.”
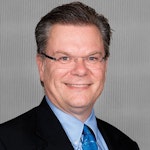
Rick Dana Barlow | Senior Editor
Rick Dana Barlow is Senior Editor for Healthcare Purchasing News, an Endeavor Business Media publication. He can be reached at [email protected].