Super storage design may call for up, up and awaaaay!
Running out of room in your storeroom, warehouse or consolidated service center generally tells you one of two things. The optimist foresees clinical and operational growth and that your organization may be handling more patients as well as more healthcare services. The pessimist (that some in finance may regard as “realists”) grouses that your organization may be buying too much stuff or not moving stock as frequently or quickly as it should.
Amid the bevy of mergers and acquisitions and blossoming consumer demands for services at lower costs, the reality may hover somewhere near the middle on a sliding scale.
Certainly, seasoned supply chain leaders and professionals want to avoid a colossal cache of clutter that might attract History Channel junk pickers and rodents. But just how orderly, organized and sterile (yes, this is a hospital storehouse after all) does your footprint need to be? How can you optimize space in a tight or wide expanse to use storeroom, warehouse or service center space effectively and efficiently?
Options abound, including going vertical, going deep (in terms of shelving), narrowing aisle width, using available storage space above doors, automating the aisles with robotics, concentrating on the “golden zone” where more frequently used products are stored. More than 10 Supply Chain executives shared their provider and supplier expertise on what to do and what not to do.
Start with the stuff
Unlike relocating to a new home or office where you clear out the “clutter” to fit your new space in the clinical business of healthcare supply chain you fit your “new” space to accommodate your stock on hand. After all, in a healthcare business setting most everything stored serves a useful purpose – patient care – and may be consumed or used in a timely manner.
That’s why Gregory Seiders, Director, Supply Chain, Advanced Logistics Management (ALM), advises Supply Chain leaders and professionals to start big, work it down and plan for processing as well as the unknown. ALM Contract Services is a division of the Claflin Co., which specializes in supply chain improvements that include storeroom design.
“Start with the big picture and design accordingly,” Seiders said. “What is the main problem I am addressing with the space? Do I mainly need to cram 10 pounds of stuff in a five-pound bag? Do I primarily need to pick a high number of requisitions a day? Do I mostly need to process pass-through inventory (i.e., JIT/LUM)? Do I mainly need to design it by category or product affinity for clinical staff? Do I primarily need to control on-hand inventory value?”
But don’t stop there, Seiders cautions. Move to the smaller picture next. “If the big picture addresses 80 percent of activity, consider the remaining 20 percent that might need some special consideration, such as consigned inventory, temperature-sensitive [products], needles and syringes,” he continued.
Factor in “processing,” too, right from the beginning, Seiders indicated, whether that involves reusables (carts, bins), people (picking, put-away, travel), waste (packaging, shrink-wrap, pallets), paperwork or technology. And plan for the “unknown,” he urged: “Set aside about 15 percent to 20 percent of space for future growth or flexibility.”
Finally, “orient shelving to create the longest aisles possible,” Seiders concluded. “This will increase the ratio of shelving to aisles, without narrowing aisles.”
Data-driven design
Several months ago, Indiana University Health, Indianapolis, opened its brand new integrated service center (SC), complete with some of the latest techniques and technologies. (See HPN’s September 2018 edition on Material Handling Innovations, www.hpnonline.com/thinking-outside-the-moving-of-boxes/). The IU Health Supply Chain team incorporated data elements to drive design, according to Dennis Mullins, Senior Vice President, Supply Chain Operations.
“Make sure you use data to help drive your design,” Mullins said. “We used product dimensions to determine how much racking we needed as well as what size bins the product fit in. We now house that information in our item master and in many cases we actually have a picture of the product.”
This month, Peoria, IL-based OSF HealthCare System, redesigned its supply chain footprint using data metrics as the linchpin.
“Regardless of whether you are redesigning existing space with no expansion or building out an off-site distribution center you want to ensure you are using a strong data-driven approach,” said Matt McGraw, Vice President, Supply Chain Integration. “At OSF we have just completed two projects to do exactly those two things, and we made the data the center of both projects. In our 13 hospitals where we just redesigned our point-of-use (POU) locations (with no expansion) we used transactional as well as volumetric data to ensure that we were stocking the highest-use items in the proper quantities to make best use of the space.
McGraw acknowledges that “this results in an overall SKU reduction in your POU locations but does significantly reduce stockouts and maximizes space.” He further admits that SKU reduction can be a “sticky subject,” which is why you have to “familiarize stakeholders with your data driven approach and create a forum to continually update and present the data. It will also be important to ensure you have an efficient logistical pathway to quickly move SKUs that may not be present to the POU as quickly as possible,” he added.
Should an organization build an off-site distribution center or CSC, McGraw urges the capture of “volumetric data for every unit of measure for every product you will be stocking” as a necessary barometer for setting rules for slotting and proper packaging for distribution to hospitals. “Make sure you have a plan as to where and why products are stocked in a particular location, focusing on efficiency during the order fulfillment process,” McGraw recommended. “Use multiple racking options to allow for the warehouse management system (WMS) to utilize dimensional data to randomly select storage locations. This takes the guesswork out of manually deciding appropriate locations.”
Clean data, clear structure
Christopher Huber, Manager, Supply Chain Consulting, Cardinal Health, insists that every design should incorporate Lean 5S methodology to minimize waste.
“There should be a proper home for every item, whether that be inventory, equipment, or supplies required to perform daily work duties,” Huber said. “These areas should be clearly marked with visual aids. Anybody should be able to walk into the space and quickly identify where things are and whether something is missing from its assigned location.”
Huber encourages Supply Chain leaders and pros to use redesign projects as “an opportunity to refresh their current inventory levels,” which reinforces waste reduction efforts.
“Prior to any redesign, a thorough data analysis should be conducted to derive optimized PAR levels,” Huber noted. “This analysis should include historic demand from clinical end users, as well as supply disposition captured in the last physical inventory. This allows for the identification of slow and no-move inventory, and generates healthy dialogue between supply chain professionals and the clinical leadership team, which minimizes the double and triple handling of identified excess inventory, and frees up space to conduct the redesign.
Take stock of stock
When it’s time to redesign your existing space, build out an expansion or acquire an off-site facility, it’s also time to measure the supplies that must fit into these spaces, according to David Phillips, Marketing Manager, Hänel Storage Systems.
“There must be a clear representation of what is to be stored and above all, have an idea of the available ceiling height,” Phillips indicated. “Establish what types of products are being stored, and determine whether they will be best stored by themselves, in bins or totes, in divided compartments, in their original boxes, or in some combination of all of these. Bins or totes are quite popular, and depending on their design, can be vastly underutilized. For example, tall bins are often much larger than the supplies they hold, and can therefore represent a lot of wasted space. A bin with a few handfuls of supplies will contain just as much air as it does actual product. A correctly-sized bin means less wasted space, especially when every inch counts.”
If you decide to go up as well as out, Phillips recommends installing one or more automated vertical carousels. “These units provide a high overall storage volume while occupying a relatively small footprint to utilize the overhead space that would otherwise go unused,” he said. “Carousels increase available storage capacity, which is particularly useful when redesigning an existing space, and turns previously inaccessible vertical space into prime real estate.”
Plan for your people
When planning a redesign, think equally about the impact a redesign or expansion will have on your people, according to Mike Maguire, Senior Vice President and Chief Supply Chain Officer, PartsSource Inc.
“Will the space be conducive to team efficiency? Are you putting your site in a place that will dramatically increase commute times, change public transportation options, or in an undesirable location? All of these people aspects are important in the consideration phase,” Maguire noted.
Beyond that, keep your supplier and customer in mind. “Ask your distribution partner for advice on your layout,” Maguire added. “They are a great source of knowledge on what works at scale. Plan to leave some extra empty space. That additional space can provide an opportunity to provide value to a supplier or customer looking to meet a quarterly goal.”
X marks the spot-on
Knowing how to approach the following supply chain X (as in Roman numeral 10) factors will help solidify the skeleton of any storage redesign, according to Karl Sliwinski, Manager, Sedlak Supply Chain Consultants.
Sliwinski targets 10 questions that should be answered for design projects.
Am I storing things I no longer use?
“If you realize that 10 percent of the items stored in an area are obsolete they should be the first to go, net impact +10 percent capacity.”
Are my storage mediums being used at an 85 percent space utilization?
“If storage areas are being utilized ineffectively you may be using the wrong type of storage medium to leverage the cubic velocity profile of the product being handled.”
Am I using my overhead (vertical) space effectively or can I go higher?
“If everything is floor-stacked 10-feet high in a 32-foot high facility you are effectively using only one-third of your available storage space. This may require investment in storage rack and lift trucks to facilitate product handling but this can avoid capital investment in facility expansion. In moving to a new space this is required to determine if you can indeed use enhanced overhead space effectively.”
Does my product usage allow me to use more dense storage mediums?
“Product storage can indicate that you have a very high space utilization, but if products are located in multiple storage locations a deeper/denser storage solution may be called for. These dense locations gain space for a facility by reducing the number of random access points a product requires. Each random access point has a foot print and overhead space associated to it and space is gained for each access point eliminated. Groupings of like storage profiles can lend themselves to enhancing capacity through the use of denser storage mediums.”
Can I narrow my travel paths without impacting efficiencies?
“A change in process and equipment can allow operators to work in smaller work aisles. A change in aisle widths from 10 feet to 6 feet is a 20 percent reduction of footprint in a typical pallet rack solution. For every five work aisles that can be reduced a new storage row for pallets is created.”
Will supported processes allow for the physical separation (located elsewhere) of items/activities currently stored or performed in the area requiring expansion?
“Plan for a minimum of three years of support for expansion efforts. If the expansion will not support what is resident in a location for that horizon thought should be given to create a plan for movement of products and activities which do not have synergy with the locations core function. If this opportunity does not exist the plan may call for relocation instead of expansion.”
If activities or storage is split between locations can skill sets be reduced to location-specific?
“Be aware of the associate skills used across the expansion area. Movement of product or activities can result in an increased training requirement due to the movement of product and activities to additional geographical sites.”
Are storage requirements for all products the same?
“Storage profiles such as freezer, cooler, temp-controlled, ambient minimums, hazardous requirement, health requirement, high value, security control, etc., all should be considered when assessing an area for expansion.”
Does product packaging impact how I store?
“Can products be decanted at receipt to reduce the overall space required due to packaging materials and maintain the ability to be stored safely? This consolidates trash to a single process at the receiving dock and should reduce product storage footprint.”
What is the pulse (seasonality, peak, etc.) of my operation?
“Plan to your peak requirements when planning for expansion. Although available space may not always allow you to expand to the required size this process will allow you to assess what operating penalties you may face down the road to allow for proper operational planning.”
Keep the dots connected
Unfortunately, no silver bullet exists for storage design, laments Bill Denbigh, Director, Business Development and Marketing, TECSYS. That’s because “design and space considerations cannot be isolated from the processes and workflows they need to support,” he insisted. Still, strategic planning influences design because an organization must weigh a multitude of issues before taking the plunge:
In-house versus outsourcing, on campus versus off campus, on premise versus cloud, today’s needs versus 5 years to 10 years out, volume of centralized services, technology and automation tools, geographic expansion of care delivery represent a few, he indicated. “The foundation of a holistic business plan facilitates the design activity,” he added.
Denbigh delved into the art and science of storeroom and warehouse design. “An optimal warehouse design underpins an efficient supply chain and relies on the implementation of data-driven warehouse design strategies,” he said. “A streamlined warehouse layout is composed of a logical and physical design that provides effective access to goods and optimizes the utilization of labor, thus maximizing performance. Moreover, an efficient design should ensure that a warehouse can be upgraded to accommodate regular or unexpected changes in operations, products or personnel, with minimum disruption of operations.”
Denbigh encourages Supply Chain leaders and pros to conduct a thorough assessment of current operations. “Start with an evaluation of your current facility utilization,” he noted. “Look at your metrics and overall performance. If you have data and analytics on facility utilization, factor these in so you can make good decisions on how to redesign your processes which in turn drive the physical design of your facility.” Turn to the Warehouse Education and Research Council (WERC) for additional benchmarking resources, he added.
Start by analyzing inventory flows and operations highlighting these five areas:
- Standardizing and rationalizing SKUs to “right-size” your overall investment in supplies;
- Maximizing space by going vertical on slow movers and keeping higher velocity items closer to the picking so operational flow is maximized;
- Eliminating no-movers;
- Evaluating picking equipment to make sure it is being used to its fullest capacity;
- Capturing demand at the point of care to establish a more precise and timely demand chain and decrease the levels of safety stock.
- Then optimize space by targeting these six parameters:
- Overall layout to minimize travel;
- Racking and pallet configurations;
- Flow charts and aisle mapping;
- Slotting and reslotting;
- Leveraging technology, whether robots, conveyors, automated storage and retrieval systems (AS/RS) or scanners, as each has a play depending on your organization and budget;
- “Use the cube” to look at all areas that can be used effectively – vertical as well as ground level.
Any supply chain operation, regardless of industry, can benefit from these recommendations, according to Denbigh, but healthcare organizations also must plan more acutely for two critical areas that will impact physician warehouse design: Regulatory requirements and disaster recovery.
“As health systems continue to centralize and expand supply chain services, we are taking on more handling requirements, such as maintaining the cold chain for medications or incorporating DSCSA [Drug Supply Chain Security Act] compliance. An understanding of these regulatory requirements today and into the future certainly impacts layout and workflow decisions,” he said. “Disaster recovery is another important consideration. As more severe weather and more malicious cyber events occur the importance of a solid disaster recovery plan has never been more important. Space needs to be reserved for preconfigured supplies to support the care continuum across the health system during these challenging incidents.”
Variety the spice of design
In storeroom and warehouse design, monotony can complicate workflow and hamper efficiency. That’s why Molly Ehrlich, Consulting Director, Vizient, encourages variety. “When redesigning existing space or expanding storage space, it’s important to avoid creating all pallet/bin locations the same size and height. Some percentage should be with a 9-foot aisle and some designed for low-unit products and some for bulk items,” she said. “For example, if you are ordering full pallets of gowns and that pallet comes in stacked six feet high, have locations that can accommodate a six-foot-high pallet. If you are offloading from pallets into racking for low-unit picking, use a storage system that better accommodates smaller cubic needs and/or place your horizontal shelves closer together in one section of your warehouse.”
Be sure to polish your “golden zone,” too. “The golden zone is the area of warehouse to keep the 20 percent of your items that account for 80 percent of your picks, and it requires a different type of racking than what is in the other parts of the warehouse,” Ehrlich said. “The items that are kept in this area should be determined by picking velocity not dollars. These are the items that have the most throughput by number of picks.”
If your organization is a “super user” of certain items, such as intravenous (IV) solutions, accommodate that. “Think about push-back racking for one area of the warehouse,” she said. “This allows you to store multiple pallets deep, giving you higher storage density. This is also a great type of racking system for storing pandemic supplies. Push-back racking can be done vertically as well as at floor level.”
Want to use vertical space more efficiently? Create a mezzanine, Ehrlich suggested. “The underneath area can be enclosed and set up to contain clean items – items that are held and picked for procedural areas – while the upper area can be utilized to store either low use goods or those boxes of holiday decorations, records, chairs that have been tagged ‘do not discard.’ If floor space is at a premium, you can set up a low-unit-of-measure picking area on a mezzanine. Installing conveyors to move product up and picked orders down improves operational efficiency for this area of the warehouse.”
If you choose narrow aisles for your storage area, “use rails – or wire – that guide the forklift,” she noted. “This will protect your product, your racking structure and, most importantly, your personnel.”
Further, a warehouse management system (WMS) enables you “to perform dynamic product slotting, making best use of open bin locations,” which extends beyond the traditional capabilities of a materials management information system (MMIS), she added.
Lastly, Ehrlich recommends investing in a “talented Inventory Manager or Operations Manager on staff. Inventory min/max changes, reorder point changes, inventory management and WMS management is a full-time job that, when done well, identifies and quickly fixes issues and allows for rapid response when they see something is headed in the wrong direction,” she said.
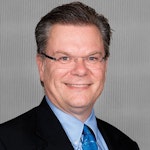
Rick Dana Barlow | Senior Editor
Rick Dana Barlow is Senior Editor for Healthcare Purchasing News, an Endeavor Business Media publication. He can be reached at [email protected].