Imagine if you could add remote control drive to your exchange carts, camera-equipped drones with pincers for picking on high shelves or software that automatically updates requisitions and patient billing when a product is removed immediately from its storage location — no need for keying into a computer, scanning or swiping?
Healthcare Purchasing News tapped executives at several leading suppliers of carts, workstations and storage equipment to geek out on some high-concept forecasting — but without giving away the store or trade secrets.
HPN asked if you could speed up the development of some feature, benefit or aspect of a cart, shelving configuration or workstation designed to improve care-giving performance, what would it be and why?
Rob Sobie, Worldwide Vice President & General Manager, Pyxis Supply Solutions, BD, pointed to expanded access to information technology and artificial intelligence.
“With the ongoing demand for efficiency, improved bedside care and the shifting location of patient care — universal rooms, surgery centers, physician’s offices, etc. — we would put additional emphasis on expanding our intelligent and secure Inventory Mobility (IM) offerings while bolstering the machine learning — often referred to as Artificial intelligence (AI) — capabilities of our systems,” Sobie said. “By making products more mobile, while continuing to drive tracking and tracing of them, and using AI to confirm the daily needs of the products, this combination would further ensure that the right products are where they’re needed, when they’re needed.”
“One of the primary ways to improve efficiency is to improve inventory availability,” he noted. “Stockouts are efficiency and satisfaction killers for the clinician, the physician and the patient as well. It detracts from a caregiver’s primary mission of high-quality patient care, delays care and causes a series of actions that remove caregivers from the bedside.
“While some might suggest that inventory management can be accomplished anywhere through a variety of scanners, wands or specialty software, in actuality, systems refined to ensure product availability, drive efficiency and take the caregiver out of the supply chain while keeping them minimally engaged in it are the keys to success,” Sobie continued. “Whereas missed scans can cause inventory counts to be wrong and product replenishment missed, RFID tagging, tracking and, where appropriate, securing inventory is the single best way to drive portability, ensure product availability and optimize care. By moving inventory to where it’s needed most, caregivers can practice care first and everything else afterwards.”
To help providers care for patients more efficiently, Capsa Healthcare sees further development of security and management of healthcare supply and support carts and workstations, according to Liz Delp, Senior Marketing Manager.
“This would include the centralized and remote management of cart fleets, inventory location and status, and overall access/control of the inventory,” Delp indicated. “The goal is to provide real-time data to the teams responsible for inventory fulfillment regardless of form. Whether it’s supplies, medications or related treatment kits, the support tools of care providers must be available at all times in all locations of the provider’s environment.”
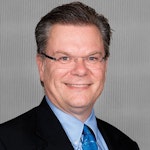
Rick Dana Barlow | Senior Editor
Rick Dana Barlow is Senior Editor for Healthcare Purchasing News, an Endeavor Business Media publication. He can be reached at [email protected].