People
Tracking patients, staff, visitors, product/service reps, including third party business associates
RFID
RAIN RFID has application in some patient workflow use cases but might not be ideal across-the-board. As with assets, RAIN RFID can be ideal for monitoring patients through chokepoints and in collection areas/waiting rooms to understand patient exit, patient movement and patient wait times, allowing organizations to modify processes and staff behavior to create better patient experiences.
— Wendy Werblin, Director, Industry Solutions, Impinj
Active RTLS is the way to go when you need true real-time location whether of people or assets. Active tags can respond to a change in state, whether that’s someone tampering with an infant tag or an IV pump moving from a patient room to a soiled utility room.
— Sagi Geva, Director, Acute Care Solutions, STANLEY Healthcare
The business value of being able to track a hospital or clinic’s most important and/or high value healthcare assets is immeasurable. Knowing where your staff is, where your equipment is, and where your patients are at any given time gives healthcare providers a performance edge that is critical, especially during an emergency or a particularly busy time.
Another way hospitals can leverage RFID to their advantage is by providing RFID tagged identification cards to each person entering your facility. This tracks individuals’ whereabouts throughout the hospital, whether they are healthcare representatives or non-employees performing tasks in the building. The ability to track outside visitors in real-time can help prevent security breaches, and other potentially malicious behavior that could be damaging to the organization.
— Keith Larkin, North America Sales Engineering Director,
Zebra Technologies
RFID alternatives (Ultrasound, Low Frequency)
Ultrasound is an excellent supporting technology for any application that requires room or sub-room resolution, including patient flow, staff workflow, hand hygiene compliance and other people-locating use cases.
LF is a critical component of security applications, like infant protection.
— Sagi Geva, STANLEY Healthcare
Processes
Tracking motion, output, performance and workflow
RFID
RAIN RFID is ideal for tracking equipment, assets, consumables and other products, with the tracking data allowing organizations to understand processes and behavior as well as utilization. The data from a RAIN system can be analyzed in a variety of analytics platforms and applications to help healthcare leaders understand which items are being used, when, where, by whom, how much, etc. for more efficient resource planning. On average 15 percent of a hospital’s assets are lost or stolen every year; RAIN RFID automates asset tracking allowing hospitals to review loss analytics and stop loss.
— Wendy Werblin, Impinj
We find that most hospitals these days are implementing location solutions really for process reasons, not just for simple locating. Use cases such as patient flow and hand hygiene compliance monitoring are entirely about process, but so are the more “traditional” RTLS applications like asset management and temperature monitoring. Real-time location makes it possible to redesign biomedical workflows for infusion pumps, for example. With a PAR level system established based on knowledge of usage patterns and real-time awareness of current inventory, it becomes feasible, and in fact more efficient, to send technicians to patient care areas to clean pumps when a certain threshold is hit, rather than to collect pumps and bring them down to central processing on a regular schedule, which is the traditional approach. This results in far higher asset utilization rates while maintaining sterilization standards, and higher productivity for nurses since pumps are always available and they no longer waste time searching for them.
Twenty-four/seven monitoring of cold storage also transforms data collection and reporting. The old ways of doing things — numerous different people manually logging readings every hour or two, and a manager manually collecting these and compiling them into a report — disappear altogether and are replaced by new processes that are essentially fully automated, while improving overall patient safety.
— Sagi Geva, STANLEY Healthcare
Products
Tracking motion, storage, use and disposal
RFID
We interpret this to be referring to tracking of items used in medical procedures. The key factor here is to ensure that information on use is tied to billing, patient information, item master, and requisition systems. Since component information is generally tracked based on the device or item barcode, barcode based systems are a good solution. For higher value items, tagging with passive RFID tags may be warranted; when stored in carts or cabinets with exciters, usage can be automatically tracked.
— Sagi Geva, STANLEY Healthcare
Tracking high-value consumables in the OR, pharmacy and interventional labs is critical to cost-efficient performance, correct patient charging and regulatory tracking. Because RAIN RFID tags come in inexpensive and easy-to-apply disposable form factors like stickers or labels, a wide assortment of items can be tracked and managed in supply rooms and “smart” cabinets that are enabled with a RAIN RFID system. Some of the key benefits include:
- Automated inventory counts that allow streamlined resupplying
- Eliminating waste from over-ordering and expired products
- Improving patient charge capture from increased consumption tracking
- Simplifying and speeding medication and supply restocking processes
— Wendy Werblin, Impinj
When surgical specimens are mislabeled, improperly preserved or lost — the consequences can be serious, especially when specimens are irreplaceable. These types of surgical errors can cause emotional distress or physical harm to patients and cost healthcare organizations a hefty price and result in delays in diagnosis and treatment, misdiagnosis, inappropriate treatment, repeat procedures or reoperations. In many cases, a breadth of errors usually occurs during transport to the laboratory.
High-performance Ultra High Frequency (UHF) RFID solutions using a combination of tools such as tags, labels, printers, IoT data platforms and mobile devices can help hospitals and surgical centers maintain chain-of-custody data about anatomic pathology (AP) specimens in real-time as they move from the point of collection to the point of delivery, to the lab. By printing RFID labels on a printer and affixing the label to specimen containers, each specimen receives a unique ID and digital voice for tracking and locating purposes. RFID fixed readers and various antennas at the collection and drop off points, as well as at different overhead locations throughout the hospital help provide clinicians with detailed timing and location info about the specimen.
— Keith Larkin, Zebra Technologies
Equipment
Tracking motion, storage, use and maintenance/repair/reprocessing
RFID
As hospital staff go about the busy work of taking care of patients, medical equipment is constantly being moved from room to room. Many organizations track these assets manually, which can be costly. RAIN RFID is a low-cost, high-benefit technology solution that automates tracking of mobile medical equipment and ensures assets are in the right place at the right time. The Impinj platform automates the tasks of tracking, locating, and managing medical equipment. Assets are tracked as they move in or out of service rooms and through a facility. The data about those items is integrated with the hospital’s systems of record, allowing staff to see asset location in real-time and gain visibility into equipment status to help plan resource use as well as scheduled maintenance. Part of the power of using a RAIN system for equipment and mobile assets is the flexibility to monitor many different asset types, from small items like instruments and telemetry packs to larger mobile items like portable monitors and IV pumps.
- Maintain availability while lowering capital equipment costs
- Automatically understand inventory levels and product usage
- Automate documentation for better compliance with maintenance protocols
- Reduce wait times for equipment by quickly locating needed items
— Wendy Werblin, Impinj
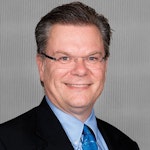
Rick Dana Barlow | Senior Editor
Rick Dana Barlow is Senior Editor for Healthcare Purchasing News, an Endeavor Business Media publication. He can be reached at [email protected].