Tips, tools for managing ambulatory / outpatient facility supply chain
Healthcare Purchasing News asked supply chain executives working in the ambulatory/outpatient arena for overt and covert ways to help an ASC or outpatient facility/department improve its supply chain operations. They shared more than 40.
Overt
Most simply, software, through even a basic materials management information system, can provide benchmarks and goals for organizations to use to reduce extreme variability in pricing in both commodities and implants. Data derived from a materials management information system (MMIS) can also assist in:
- Aggregation — Systems can collect the proper data to aggregate spend across multiple facilities. Today, many work in silos and aren’t leveraging their buying power.
- Tier Optimization — An IT platform provides the data to assist facilities in optimizing tiers and adjusting spending to achieve the higher, more cost-effective tier levels.
- Purchase Orders — Today, many organizations have multiple POs from possibly hundreds of vendors at each site. With an IT platform, facilities can assure POs are pulled in one system and paid more efficiently and correctly.
- Formulary Purchasing — Many facilities do not have a purchasing manager, therefore, there are many people ordering. With an IT platform, a formulary can be built and pre-approved to ensure purchases are contract-driven. This can also minimize off-contract or rogue spending.
- Contract Compliance Purchasing — An IT platform will help drive contract compliance, which will lead to better vendor relationships and offer better negotiation leverage with those vendors.
- Comparable Items — An MMIS system can also provide alternatives, clinically equivalent comparables that can possibly be purchased at a better price. This will drive better purchasing decisions and savings.
- Paying the right price — Just because you placed an order for an item at a given price does not mean you will be invoiced for that price. MMIS can ensure a 3-way match so that you realize the savings you are projecting on the front end.
- Order preparation — I’ll go out on a limb and say we agree pen, paper and Post-its might not be the best method for capturing products that need to be reordered. Bar-code scanners that easily capture barcode labels on all needed products from all vendors can save a tremendous amount of time.
- Order approval — Getting purchase order (PO) approval before submitting to suppliers is critical to saving money, and while conceptually this makes sense, it doesn’t always get prioritized. Shifting approval to the front end of the purchasing process can drive significant reductions in orders for products that aren’t needed. Example: An approver may know there’s more product in the nurses’ closet or that a sister facility is overstocked a particular item. People often believe they don’t need to approve orders before they’re submitted — that approving an invoice is doing the same thing, but that can cause an organization to purchase products that aren’t needed, so always shift approvals to the front end of the purchasing process.
- Order submission — We need to streamline order submission, so supply chain personnel aren’t logging into multiple websites, standing by fax machines or waiting on hold with customer service. Technology that places orders via electronic data interchange (EDI), email or autofax is a huge time saver.
- Two-way vendor communication — By leveraging EDI technology, users can establish a pipe from their system to their supplier network that exchanges information both directions. Send out a PO and receive back an electronic order acknowledgement, know when that product has been put on the truck and is on its way, and get an electronic invoice.
- Mobile apps — 92 percent of Americans have smartphones, and constantly have their device in their hand — even at work. With this, business apps on mobile devices are game changers. New supply chain apps can help by supporting the user wherever they are. Users can submit orders electronically from an app that in turn, an approver can approve and instantly submit. Mobile apps can help users complete an accurate ordering process easily and seamlessly.
- Tracking costs for better business management — I recently spoke with a large surgical department director who used two numbers to manage his business: Total revenue and total cost. We have to run our businesses with numbers. As we push more patient interactions outside of the hospital, we need to capture information to know costs by location, department, specialty, physician, patient, case, etc. Today, technology can help managers at ASCs manage their business plans against real numbers, performing tasks like tracking the movement of inventory across the entire non-acute network.
- Product formulary — One of the biggest challenges for multi-location organizations is defining a list of best practice/contracted products and enforce purchase compliance across multiple locations. Users can work with a GPO to define products that can be standardized and make sure contracts are activated. A GPO can help work with the suppliers to make sure contracts are activated and the ASC is receiving contracted prices. Then items can be loaded into the procurement system so all locations and departments are buying off the same list of contracted products. It’s key that the procurement system includes all vendors and all products, and makes the shopping experience easy for all locations.
- Cloud based solutions — Selecting cloud-based technology delivers real advantages to a multi-facility ASC organization. Being able to implement a system — especially one that’s customized per facility, but standardized at the organization level — without having to install hardware or go through a rigorous implementation at every location will greatly reduce staff time and investment.
- Materials management information system — A materials management information system will enable the ASC to, at a minimum, address its order processing and inventory and data management needs with automation. By doing so, the ASC will increase the reliability and effectiveness of its Supply Chain as well as provide the data necessary to manage the Supply Chain.
- ASC-specific EMR — An EMR should be tailored specifically to the unique needs of an ASC, without features and functions that are not relevant to the facility. With the growing types of procedures that ASCs are licensed to perform, the need to document and retain electronic records for patients is ever more important. For example, in the future, when ASCs are performing primary arthroplasty procedures on Medicare covered lives, the longer-term retention of implant records will be required.
- Instrument tracking — With these new procedures will come a whole new set of instrumentation and, like the inpatient surgical suites in the mid-80s, ASCs will require IT to aid in the management of the instrumentation, thus a tracking system can provide benefit to the ASC.
- Extend the footprint of your ERP into your non-acute care setting. Leverage the economies of scale it provides.
- Use a marketplace to extend the ERP and provide the same level of eCommerce shopping the non-acute care employee desires, but with added compliance and controls in the background.
- Use Inventory/PAR management where needed. Do not let it be a decision for company business. It likely is overkill in most non-acute care settings.
- Use hardware agnostic technology to drive efficiencies and for track and trace purposes. This will decrease your technology footprint, but provide the same level of control and sophistication.
- Apply the same big data, analytics and visualization technologies for non-acute care, non-clinical spend as you likely already do with clinical spend.
- Integration of technology costs money and makes upgrades harder…decide on the right mix of “best in breed” versus “good enough.” Non-acute care settings are not a supply chain mystery. They are a smaller version of acute care setting that in aggregate make a similar impact.
Here are five examples of Materials Management functionality that can be adopted by ASCs. This functionality can come by either fully adopting existing ASC operating system’s inventory functionality, and/or investing in bolt-on MMIS technology platforms that interface into existing operating systems.
- EDI Functionality — EDI functionality, when utilized, allows for multiple vendor electronic ordering from one platform, automatic invoice reconciliation and effective price management with pricing acknowledgements and advanced price change notifications
- Manage Perpetual Inventory — Always know how much inventory is on hand by utilizing available technology
- Manage PAR Levels — Set mins and maxes so that you don’t stock out, have too much and or too little inventory on hand
- Incorporate Bar-code and or RFID technology — Utilize your smart phones to automate the ordering process with highly efficient barcode and RFID ordering as this can cut ordering time in half
Covert
Winfield:
Data and technology can help you visualize and know where the majority of your spend goes, and therefore, suppliers are more important or strategic to your objectives. Data can help you make strategic choices around which suppliers and products truly need to be managed.
Using data to educate physicians is an indispensable asset. Data offering perspective in terms of both cost and outcomes factually illustrates to physicians, and all stakeholders for that matter, the challenges at hand. This can assist in developing physician champions, and identifying outliers that drive peer discussions. Data displaying surgeon, cost-per-case with implants and supplies allow visibility to illustrate how switching preference items will affect not only costs, but also whether it affects patient outcomes.
All stakeholders are ultimately driving improved patient outcomes and safety through integrated systems to reduce errors and streamline procurement via automation.
Lawrence:
- Electronic 3-way match and invoice approval — I started my career as an auditor/CPA, so electronic three-way matching as an afterthought causes me pain. How many organizations just pay an invoice and hope that the quantity and price are accurate? The CPA in me wants to stand on my chair and shout, “make a three-way match!” Create a PO with accurate pricing, make sure you record the receipt transaction so you know the quantity that should be paid for, and ensure the invoice matches the confirmed price and quantity. Stop hoping the invoice is accurate. Know that it is! And if it isn’t, stop and save the money.
- Automate a high percentage of order confirmations — Hidden within the EDI discussion is the very important order confirmation process. Often ASC team members need to shift among multiple roles, so it’s hard to find time to confirm that orders are received and being processed. By combining EDI technology and advanced email confirmation tools, users can confirm a very high percentage of orders electronically. When this information is delivered back into the supply chain system, users can simply manage orders by exception.
Cunningham:
- Preference cards — Regardless of care setting, updating preference cards often feels like a daunting task. However, given the lean margin space of ASCs, using technology to aid in working with high-volume physicians to review and update cards can significantly reduce cost per case and clinical variation. It also leads to better inventory management.
- Broader device catalog — Because ASCs have historically had a more limited portfolio of procedures and less device intensity, they largely have not needed access to a broad catalog of medical devices for comparison of equivalence, attributes and safety data. However, with the growth in device-related outpatient procedures, ASC will require and benefit from technology that provides greater insight into the selection of devices.
- Learning management system — ASC have traditionally been able to operate with a much smaller compliment of staff who perform multiple functions rather than the specialization that we see in the inpatient surgical suite. For example, an ASC may have surgical technicians that perform scrub nurse, instrument technician and supply chain functions. However, as the complexity of ASC procedures increase, these functions are becoming more and more difficult to not specialize, leading to broadening education and training backgrounds of the ASC staff. As a result, ASCs will benefit from a learning management system that can aid in providing the required training to a more diverse staffing mix.
DeLuca:
Not much obscure about it: Use your centralized supply chain organization to decide how to best service the non-acute care entities, then drive compliance and control by extending your existing IT footprint into the setting, leveraging existing economies of scale, and driving the most efficient, cost justified distribution process. Put contracts in place with pricing that represents committed volume, and use the process you have designed to live up to those commitments. If your users want an Amazon experience, give them one that is controlled by leveraging a marketplace that provides the shopping experience of Amazon, but the content control of Google.
Jackson:
- Invest in auto-replenishing technology that knows what your PAR levels are, and that automatically creates POs that are electronically sent to your vendor partners, thereby eliminating the manual component of ordering.
- Invest in a Physician Preference Item (PPI) Benchmarking platform. There are new, cloud-based PPI Benchmarking systems that allow hospitals and ASCs to better understand how their PPI costs for PPI items compare to those costs at other hospitals and ASCs. This can be an excellent negotiating tool when you are attempting to drive down the high costs of implants and devices.
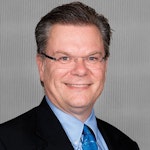
Rick Dana Barlow | Senior Editor
Rick Dana Barlow is Senior Editor for Healthcare Purchasing News, an Endeavor Business Media publication. He can be reached at [email protected].