For Supply Chain, at the intersection of cost, quality and outcomes sits the warehouse — or the storeroom for those that don’t operate a sizeable chunk of real estate to serve clinical customers.
Any permanent storage location — big, small, deep or wide — includes pros and cons of how to design and organize it for the variety of end users that may encompass supply chain staffers picking for facility distribution, clinical cart replenishment or clinical procedures, or nurses directly picking for physician request or procedural need.
Back in the mid-to-late 1990s with the emergence of the Efficient Healthcare Consumer Response (EHCR) initiative, along with an emphasis on bar coding, data management and strategic sourcing, supply chain pros expressed interest in the grocery and retail models as examples from which to adapt and implement noteworthy practices.
Since then, reviews have been mixed on just how much the healthcare supply chain can borrow from the grocery and retail models. Between the polarizing “supply chain is supply chain regardless of industry” attitude to the “healthcare is different” mindset, many supply chain pros in the industry fall somewhere in the middle. They demonstrate a willingness to pick and choose strategies and tactics that make sense for their respective organizations.
So what elements from the grocery and retail industry segments can hospitals and integrated delivery networks with consolidated service centers (warehouses) reasonably and safely enact within their own operations?
“I’ve always thought that if the space allows, a storeroom layout should follow the pattern of a grocery store,” indicated Shaun Clinton, CMRP, Senior Vice President, Supply Chain Management, Texas Health Resources. “All the aisles should run parallel to each other and the egress points of the aisles should all drop the material handler near the point(s) that would allow for easy access to the facility, i.e., elevator bank, hallway, etc. Also similar to grocery store end caps, storerooms should analyze items that are picked most frequently and locate these near the aforementioned egress points. Other frequently picked items should be placed accordingly and at hip to eye level for easy identification and picking.”
Jim Churchman, Vice President, Site Operations and Logistics, Supply Chain Management, Advocate Health Care, encouraged the “use of a singular distribution infrastructure that enables the efficient delivery to the point-of-care with appropriateness of transportation, i.e., acute-care, physician office, retail outlet, home health market and the distribution of durable medical equipment.” This involves technology for “efficiency improvements and heightened reliability” as well as “increased use of analytics to drive improvement on perfect order attributes,” he noted. “In other words, one size vehicle no longer is sufficient to efficiently serve the customer,” he added.
Cindy Measurall, Director of Supply Chain Consulting Services, Cardinal Health Inc., notes that she and colleagues commonly recommend “grocery store-like aisles” to their hospital customers.
“Grocery stores have lanes that run perpendicular to the front door, meaning that when you walk in, you can see down many aisles,” Measurall said. “Each of those aisles have signage that is easy to read and descriptive of what can be found in each aisle. This design allows for easy access and allows a hospital to place all the fast-moving items toward the front of the storeroom, and still keep inventory organized by product category. This reduces the footprint required to pick and put away supplies, which increases efficiency.”
Rodney Simpson, Corporate Supply Manager, Supply Chain Services, Orlando Health, stresses convenience and familiarity as key strategic approaches in his organization’s warehouse.
“We make the products visible to the customer,” Simpson said. “The customer wants to see the products. They know the product by its packaging, and what they are looking for and know it by a different name or how it is used. All products have a ‘front row’ similar to a grocery store. The utilization of technology, similar to retail, has provided a wealth of data to use in forecasting and efficiency for the operations.” For Simpson, the customer is the clinical nurse not wanting to spend a lot of time looking for products, he added, which is why consistency and the logic of grouping “like items” makes sense.
“The customer wants to find the products they need as quickly as possible,” Simpson continued. “Standardizing supply rooms and storerooms increases efficiencies. From the warehouse every item has a set location and is visible from the customer to see. We no longer have multiple items in a bin, one behind the other.”
Not all of the clinical areas handle the same services but their standardized supply areas look similar but not identical based on volume and type of patients, according to Simpson. “For the floating nurses and physicians, and the training of new staff there is a standard process to building the supply areas,” he added.
Teching out for checking out
James Wetrich, FACHE, CEO, The Wetrich Group, points to operational efficiency and organizational development as key strategies that forward-thinking non-healthcare companies such as Amazon are implementing to change the way products and picked and packed.
“They are using robotic technology in very creative ways,” Wetrich said. “In addition, in general, these non-healthcare companies are often operating more efficiently from a productivity standpoint… and have done a great job creating very large spans of control to minimize the number of managers needed to operate effectively.”
Due to the significant amount of stock-keeping units (SKUs), many facilities are designing warehouses using vertical strategies, such as pick modules and other high-density storage media that allows greater leverage of space and enables more efficiency, observes Brian Murphy, Director of Business Development, Ryder Systems.
“With the pick modules in place, many operations will then leverage technology, such as automated material handling (i.e., conveyor and/or AGVs), automated sortation and hands-free picking, such as voice picking or pick-to-light in zones to reduce travel time and increase the order picking process,” Murphy noted. “Specifically in PAR locations, many hospital systems have adopted technology and processes that synchronize the inventory in the warehouse with the PAR location.”
Patrick Sedlak, Principal, Sedlak Supply Chain Consultants, insisted that healthcare organizations definitely can benefit from automation and robotics.
“What we see in the new consolidated services areas are technologies that were utilized 40 years ago and, although efficient at that time, the labor and precision needed for the IDNs are far greater than in a retail or wholesale distribution center,” Sedlak said. “If you ship the wrong retail widget or short a widget, it’s simply a return or a service issue. IDNs need a much higher precision in their order fulfillment, and that’s where the automation and robotics can provide significant improvement.”
But this development remains a work in progress, Sedlak added.
“Many of the operations we see in healthcare are extremely manual,” he continued. “The IDNs took many of the processes and systems they used as stand-alone hospitals and moved them into the consolidated services centers without really stepping back and asking, ‘What is best practice?’”
IDNs also fail to use standard industry key performance indicators (KPI), according to Fred Crans, Healthcare Consultant, Sedlak Supply Chain Consultants.
“They can’t tell you how many picks per person they have,” Crans said. “These KPIs need to be implemented in the storerooms and warehouses because you can’t improve what you don’t measure.”
Making sense of slotting, smart ops
Brent Wigington, Director of Continuous Improvement, Intermountain Healthcare, emphasizes the value of adapting any lean inventory strategies for clinical storerooms or warehouses. In fact, in 2017, Intermountain completed more than 85 different Kanban locations within its supply chain operations, which has “resulted in lowering inventory, lowering obsolescence, and reducing labor,” he noted.
“Velocity slotting, smart labels with bar codes, and min/max are also strategies that are essential to effectively manage inventory,” Wigington added. “Consignment and [vendor-managed inventory] are underutilized strategies in the clinical environment, too.”
Gregory Seiders, Director, Supply Chain, Claflin Co., promotes the concept of “item slotting” as an effective way to add efficiency and increase clinical satisfaction, he said.
“Slotting is the intentional placement of a product within a storage area and can be based on different factors to meet the needs of the internal customer,” Seiders explained. “For example, a general stores or bulk storage area may be slotted primarily by velocity, i.e., how often a product is being received in and issued out to the floors. Clinical areas might be slotted by product category, such as personal care or respiratory, or slotted by product affinity. Product affinity is the likelihood of items being used together as you would see with three very different items — a saline bag, an IV set, and an IV catheter needle. While grouping these items together is obvious to a clinician, it may not be obvious — or a priority — to the supply chain resource. Prioritizing slotting can take an irritating, labor-intensive work environment and change it into something intuitive and easy, and often for little or no investment other than time. Besides the odd tweak occasionally, the setup should be quite consistent.”
Slotting is intended to meet customer needs, according to Seiders. “In the case of general stores the Supply Chain employees need the flow of products to require as little time as possible while preventing common inventory issues, such as mixed products, obsolescence and incorrect inventory levels,” he said. “In the clinical areas, the customer needs products arranged in a way that allows for quickly finding the product needed without asking, even if the clinician does not initially know where it is located. If clinicians can quickly find what they need, when they need it, patients can be better served, and the day can be just a little less stressful!”
Seiders has worked on-site at hospitals in supply chain management and currently manages employees of Claflin’s Advanced Logistics Management Contract Services division at three different hospitals in the New England area.
Mike Henry, Director, Performance Delivery – Logistics, Supply Chain Services, Owens & Minor Inc., advises Supply Chain pros to manage their available space wisely, relying on vendors and infrastructure to set the workflow pace.
“Leverage your suppliers and challenge them to provide just-in-time (JIT) delivery capabilities to limit the amount of inventory you need to store at any given time,” Henry noted. “Take advantage of the cubic capacity, not just square footage or floor space. Look for storage infrastructure — rack and shelving — that maximizes the use of the available space. Analyze your inventory velocity. Invariably 20 percent of your SKUs will represent 80 percent of your transactions. Slot these products accordingly giving them prime locations for easy and quick access, while low velocity items are stored above or below easy reach. Consider setting up a ‘quick pick’ zone, replenished from primary storage, for the high-velocity items, establishing an efficient space for routine picking of the most frequently used products.”
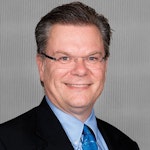
Rick Dana Barlow | Senior Editor
Rick Dana Barlow is Senior Editor for Healthcare Purchasing News, an Endeavor Business Media publication. He can be reached at [email protected].