Acolytes of the “supply chain is supply chain” mentality may pooh-pooh the “healthcare is different” mindset but they probably should think twice before trying to refashion their storerooms and warehouses into mini-Amazon operations, experts contend.
Well, why?
“The strategy of many warehouses is to use random slotting/storage based on space available,” said Rodney Simpson, Corporate Supply Manager, Supply Chain Services, Orlando Health. “I see this working in a fully automated environment that picks the orders in a warehouse for a JIT customer. In a hospital setting the customer is looking for consistency.”
In essence, when robots do the picking they can be programmed to navigate through randomness and chaos while humans require more convenience and familiarity.
“Yes, we humans need organization,” Simpson acknowledged, “and we will take the path of least resistance, and standardization.”
Put simply, forget the robots.
But wait.
“Any strategy that requires a lot of walking or stocking secondary locations should be avoided in the hospitals,” cautioned Brent Wigington, Director of Continuous Improvement, Intermountain Healthcare. “Secondary locations are frequently forgotten and product ends up expiring. Walking paths for picking should never dead end into a wall. Rewalking pathways is wasteful.”
So, robots could be useful?
“When looking at the integrated supply chain function within the hospital network — from distributor to supply chain to PAR location — there are a number of similarities to other industries, such as automotive and high-tech,” said Brian Murphy, Director of Business Development, Ryder Systems. “With that said, there are certain nuances specific to high-velocity direct-to-consumer processes and functions that likely would never be required by the healthcare system outside of home health. An example of this would be robotics for order sorting and picking.”
Sigh.
“Random storage based on cube utilization can work well in a warehouse environment but would be a disaster in a healthcare environment,” warned Gregory Seiders, Director, Supply Chain, Claflin Co. “In warehousing, using cubic footage efficiently is more important than what is using the space. Available square footage could be used for a variety of items or processes, from staging to forklift charging to material storage. Additionally, a storage location could just as easily hold one product as any other, and the basic warehousing concepts would remain the same. In a Warehouse Management System (WMS), the system can dictate where in the warehouse a received item will be stored based on the cube of the product received and the cubes of all available locations. This focus on cube utilization could mean the same item is in any number of locations throughout the warehouse, and that it may rarely be in the same place twice. Since order picking in a warehouse environment is driven by the WMS, the order picker finds the item with the same amount of ease no matter where it is stored.”
Sans system help, humans may shrug with randomness.
“In a healthcare environment, putting an item away randomly based on currently available space can turn effective supply chain employees into absent-minded professors,” Seiders continued. “Questions about where a critical product is located will be met by an exasperating ‘I forgot.’ While space utilization is certainly high on the list of supply chain priorities in a healthcare environment, permanent storage locations go a long way to achieving predictability and performance in a fast-paced workspace.”
Mike Henry, Director, Performance Delivery – Logistics, Supply Chain Services, Owens & Minor Inc., alludes to parallel, but not mirrored, imagery.
“A hospital warehouse/storeroom is not a retail space where customers browse the aisles, and they shouldn’t be set up that way,” Henry insisted. “They should be set up for efficient warehousing. In many cases hospital storerooms are set up like a retail space with like products and/or suppliers stored together. In some cases this may make sense. In other cases it does not. Slotting logic should be based on providing for the most efficient storage and retrieval of material. This should take into account product velocity and product cube and volume. Velocity establishes relative activity. Product cube and volume establishes storage type. Bulk storage of pallets should be separated from small-bin and hand-stack material.”
Strategically, retail “manipulation” represents a different management philosophy than what’s needed in a service-related storeroom or warehouse environment.
“A retailer may design a space that adds footsteps to a shopper’s route to entice them to buy more,” Henry added. “A warehouse should be set up to limit footsteps, handling and redundant activity.”
Shaun Clinton, CMRP, Senior Vice President, Supply Chain Management, Texas Health Resources, calls that the “retail loop,” something that runs counter to the pacing in healthcare.
“Clearly, it’s designed to slow a shopper down,” Clinton mused. [It’s] not exactly the best way to ensure productivity for the storeroom or warehouse staff.” Still, he said he has mentally grappled whether like items should be stocked closely together. “On one hand, it is nice to know that all the needles, syringes, etc., are in one location of the storeroom, but when there is often incremental — but vitally important — differences in sizes or packaging, it might be good to allow for enough separation so that errors are avoided.”
Automated warehousing equipment and WMS capabilities can be helpful but relative to the volume of activity they will support, according to Henry. “These systems are expensive and need a significant volume of throughput to generate a return on investment,” he continued. “Carousel and other picking systems are often designed for small parts distribution and often don’t work effectively with certain high-volume medical products such as heavy I.V. solutions or bulky products such as underpads or pillows. Warehouse Management Systems can provide for greater warehousing efficiency and flexibility. These systems, however, are not ‘plug-and-play,’ and require dedicated subject matter expertise to get the most out of them.”
Henry acknowledged that these systems typically will generate a positive ROI only when a warehouse is supporting multiple provider sites or for the largest of single-site locations. “Even when the ROI exists, it is predicated on ensuring that the systems are used and tooled to their fullest extent,” he added. “Lastly, when these systems are purchased they may be state of the art at the time, but warehouse technology is changing rapidly. Will you have the capital and expertise to invest and upgrade in the future? Is the commitment of capital and acquisition of expertise core to your mission or are there suppliers that can support the same or greater capabilities at a lesser cost?”
Healthcare organizations just need to be prudent and perform their due diligence, according to Fred Crans, Healthcare Consultant, Sedlak Supply Chain Consultants.
“There are technologies out there that healthcare knows nothing about,” Crans said. “One example is pick-to-light. If anything, they need to avoid jumping to a solution without really analyzing and understanding their own situation. Not every automated solution is right for every operation.”
From the perspective of Patrick Sedlak, Principal, Sedlak Supply Chain Consultants, the strategies and tactics used by other industries do apply to hospitals.
“In any industry — healthcare or otherwise — the lack of [key performance indicators] and labor management systems lead to poorly run operations,” Sedlak said. “They don’t measure productivity, they don’t measure accuracy, they don’t plan and build for future needs, and they are not in continuous improvement. My point is that hospitals should strive to avoid the mistakes of other industries.”
Healthcare nuances
Exceptions to the rule of supply chain transferability do exist as sources quickly point out.
In healthcare, don’t look up.
“Other industries, specifically manufacturing and distribution, seek to maximize vertical space,” said Cindy Measurall, Director of Supply Chain Consulting Services, Cardinal Health Inc. “With mobile equipment, such as overhead cranes and forklifts, items placed in vertical storage are picked and replenished in a controlled and deliberate fashion. While this makes sense for warehousing operations, medical supplies in a hospital storeroom should be placed no higher than arms’ reach due to the emergencies that often occur in the healthcare environment.”
Jim Richardson, Senior Consultant, Vizient Inc., acknowledges that basic warehousing strategies can be applied to hospitals but a few restrictions unique to hospitals pushes him into more fundamental and purist territory. To wit are four no-no’s.
- “Wooden pallets are used to ship many healthcare products into hospitals, but because of hygiene factors, wooden pallets cannot be used to transport products into the hospital departments. Most hospitals use metal carts for transport into hospital departments. The metal carts should be cleaned at least once per week.
- “Most products and supplies in healthcare and other industries are stored and shipped in cardboard cases, which are taken directly to point of use in manufacturer and distributor operations, or to shelves in retail stores. This practice is not appropriate in hospitals, especially in procedural areas, because of hygiene. Corrugated cardboard containers, because of their ability to generate and hold dust particles are generally disposed of — or recycled — at hospital receiving docks before products are delivered to departments. Products inside are transported in plastic totes or covered metal carts.
- “In industries other than healthcare, storage of cases on the warehouse floor, or on wooden pallets on the floor is commonplace. While this often occurs in off-site hospital warehouses, it is not a generally accepted practice in hospital storage areas because the texture of wood tends to hold dust and bacteria. For this reason, plastic pallets have become increasingly popular in this environment.
- “In some industries, product supplies are not susceptible to expiration dating, and can be stored utilizing last-in-first-out (LIFO) storage methodologies. While some supplies used by hospitals are not subject to expiration, the majority of products do have expiration dates, and therefore a first-in-first out (FIFO) storage strategy is recommended.”
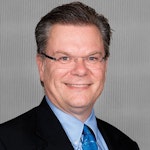
Rick Dana Barlow | Senior Editor
Rick Dana Barlow is Senior Editor for Healthcare Purchasing News, an Endeavor Business Media publication. He can be reached at [email protected].