- Be informed: Contracts are a good starting place. However, it is important to have a strong leverage point for negotiation, with aggregation and pricing knowledge, as equipment lends itself to a transactional approach. Benchmarking is absolutely critical to understanding the competitive marketplace, but it is also important to exhaust all resources and collaborate with all stakeholders.
- Be prepared: Providing Supply Chain professionals with the right applications, services and tools is the best defense against these challenges. Deploy technology to empower the purchasing team with real-time market data at their fingertips to drive decisions. Also, it is helpful to create a five-year replacement plan that allows a team to properly forecast equipment needed, allowing staff to aggregate purchases and bring maximum volume to the negotiation table.
- Be ready: Make sure the team can easily benchmark the competitive quotes against the hospital’s own historic data and allow access to market pricing driven through the collective transparency of other health systems. The resources, services and applications deployed to empower the supply chain team should be intuitive and responsive, while allowing for time to work with key stakeholders in the hospital to negotiate with confidence. Successful execution of these strategies will give the supply chain the ability to drive savings and maximize value.
- Have a plan in place that you and the organization know, understand and most importantly, support. It’s understood that there are occasions when an unplanned situation dictates that the general rule of thumb can’t apply. However, even in those situations, know the must-haves that are critical to protecting the organization while delivering the best product at the best price.
- Educate your customers. Help them help you. Understanding their needs while explaining and helping them understand your needs creates a strong relationship. Walk in their shoes so that you understand their pain points when they don’t have the equipment to support their patients, or equipment that is aged and forces their staff to work harder, not smarter. They are our purpose for existing in the first place. It is our responsibility to support them with what they need, when they need it and at a price the organization can affort as they strive to provide positive outcomes for the patient.
- Know your limits and don’t be afraid to ask for help. Capital purchasing — either for a project or a “one off” purchase” — isn’t easy. It requires communication, collaboration, coordination with the team and confidence in the team. So whether you’re a capital “acquisitions” expert or a combined capital acquisitions/equipment planner expert, you can’t do it alone. Being surrounded/supported with your team of experts is crucial to your success. It’s not always easy to share, but if you are really committed to successful outcomes, then being part of a team is the best thing you have going for you.
- Celebrate your successes and learn from your defeats. Evaluate both situations. What did you do right to achieve the success and conversely, what happened that didn’t allow you to realize the outcomes you were looking for? There will be times when you’re just not going to be able to squeeze that last dollar out of the contract, or get that extended warranty or get that extra widget. Don’t take it as a loss, but as a lesson. Determine how you achieved the positives of what you’ve achieved and how you can apply those to the next opportunity that presents itself.
- At the end of the day, share with your fellow Supply Chain professionals. Don’t operate in a silo. Let them hear how you’re challenged in doing your job. They could be experiencing the same things — albeit in different ways — you are. In spite of the fact that we don’t like to share that we may be struggling with a particular situation — or person — by sharing we might get feedback that helps us overcome those hurdles in a less painful way. Your struggles may be something they are experiencing — or have experienced — and their insight from a different perspective may help you. In the same way, sharing your successes, may be just what “the doctor ordered” to help them overcome some of the same headaches they have.
Ric Goodhue, Equipment Planner/Capital Coordinator, CaroMont Health, Gastonia, NC
- Centralization of Capital Planning and Procurement is essential to driving standardization and efficiency in managing resources and utilization across the enterprise. Investing in resources and technology for capital management can deliver huge wins in effectively managing capital improvements.
- Organizations must make the investments necessary to effectively control and direct capital planning and acquisitions. These Investments include people, technology and processes that are focused on ensuring that needs are addressed in a systematic manner while still being reactive to the requests in hand.
- Conducting an organized asset inventory and then pairing that with condition indexes and utilization information will allow you to flip the capital planning model on its head and begin to push out capital budgets based on equipment age, condition and technology obsolescence rather than just buying the latest and greatest model on the market.
Allen Archer, CMRP, Director, System Supply Chain Management, Houston Healthcare, Warner Robins, GA.
- Plan ahead to ensure end-users and equipment planners provide equipment recommendations early in the process. Start negotiating equipment purchases well before the design is complete. Doing this will save both time and costs with the project.
- Ensure the project team reviews the final proposal along with the terms and conditions to avoid unforeseen costs and budget overruns.
- Complete a full analysis of operational costs, service contracts, and consumables for each vendor’s equipment prior to selecting the vendor and equipment.
- Some capital equipment is “permanent” and comes at a great expense to purchase and install. When making a 15-year equipment ownership decision, look to many sources for information as inputs to the vendor selection decision. Avoid the route of allowing one end-user the power to select a vendor when they may not be at the hospital next year or even see the project to completion.
Steve Sutton, Director, Planning and Design Group, Belimed Inc., North Charleston, SC
- Always try to take into account all costs when negotiating equipment contracts.
- Look for an equipment distributor to contract with that can help you consolidate the purchasing of those distributor-bought items and smaller manufacturers.
- Analyze your service contracts periodically to make sure costs are in line.
Cindy Juhas, Chief Strategy Officer, CME, Warwick, RI
- Find a simple way to learn about new and innovative equipment suppliers. This is a fragmented part of the healthcare supply chain. Use a simple market share tool from OpenMarkets to start.
- Use data. Ideally, a Supply Chain professional will have access to organizations’ entire capital budget. Use this data to find opportunities to partner with suppliers across departments and timeframes. This saves time and money for all parties involved.
- Automate your capital budgeting and requisitioning process. If your organization is one of the [approximately] 40 percent still doing equipment planning via email, pen and paper — find a modern Supply Chain-specific platform to support a more efficient workflow.
- Join OpenMarkets! There’s no cost and it’s a simple way for providers to more collaboratively work with suppliers.
Tom Derrick, Senior Vice President and Co-Founder, OpenMarkets LLC, Chicago
- Insist that software updates/corrections be at no cost and that software upgrades be offered at best pricing options.
- Know the market for potential sources and pricing trends.
- Distill marketing verbiage to get to the facts straight.
- Become familiar with clinical practice trends and standards.
- When appropriate, ensure coordination with clinical engineering, the IS/IT community, facility operations/construction, strategic planning.
Jeffrey Dunkle, Sourcing Manager, Capital, BJC HealthCare, St. Louis
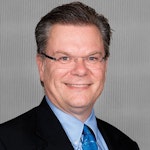
About the Author
Rick Dana Barlow | Senior Editor
Rick Dana Barlow is Senior Editor for Healthcare Purchasing News, an Endeavor Business Media publication. He can be reached at [email protected].