Historically the central sterile/sterile processing department (CS/SPD) was an afterthought to a hospital’s design. Relegated to the basement of the facility or in some far off corner, CS/SPD professionals often have to contend with inhospitable conditions, outdated equipment, inefficient workflows and a vast distance from their main customer, the operating room (OR).
More forward thinking health systems and hospitals are reconsidering the role of the CS/SPD, recognizing the vital importance these professionals play in the effective and safe treatment of patients. In turn they are investing in their CS/SPDs, providing staff members with the space, equipment and tools they need to process today’s advanced medical instrumentation.
Start with the SPD
Michael Matthews, Manager, Central Sterile for Baptist Health in Conway, AR, joined the organization six months before it opened. At that point, the basic layout of the CS/SPD has been designed and most of the major equipment purchased. Matthews notes that individuals outside of the CS/SPD made these decisions, which resulted in a “ton of wasted opportunities.”
For example, the decontamination area was built without an eye wash station or hand wash sink, and in the cleaning area the sink drains were too small. Matthews was happy to hear that the department would have a cart washer since in his previous facility he and his team had to wash their carts by hand. But then he discovered the cart washer was not located in his department but in the materials management department, which was 200 yards away from the CS/SPD.
“When designing a CS/SPD, be sure you consult the experts — don’t wing it,” said Matthews.
“I do some consulting work and have been in and out of facilities and I can tell you that I often find departments that were built without consulting a central sterile expert. It is a recipe for inefficiency and waste. In our case, we are still very new and building our practice from the ground up so right now it is not a big deal to push case carts 200 yards down a hallway to the cart wash. But in a few years when we are operating at full or near-full capacity, we will have to hire a full time employee whose job it is to push carts back and forth. That is a waste of time and money that could have been avoided.”
Matthews notes that a new CS/SPD or renovation of an existing department is the perfect time for a team to try out and adopt new technologies. At Baptist Health, the CS/SPD team has added a digital tracking system and updated their visual inspection to digital microscopy with USB microscopes from Healthmark.
“We have had so much success with the USB microscopes that we are making them standard throughout our system so all nine hospitals will be using these for instrument inspection,” adds Matthews.
Stick to standards but don’t underestimate workflow
When designing a new CS/SPD, Damien Berg, 2017 President Elect IAHCSMM, Manager, Sterile Processing, St. Anthony Hospital in Lakewood, CO, suggests that healthcare facilities start by reviewing current industry standards, including healthcare architectural standards and Association for the Advancement of Medical Instrumentation (AAMI) guidelines.
“Look at what you currently have and where the standards are at this time and make sure whatever you are going to design is going to take that all into account. You don’t want to build something nice and shiny that isn’t meeting the standards,” said Berg.
Berg says next consider the workflow of the department and develop a design that maximizes efficiency and minimizes wasted steps and tasks that don’t add value. He walks the floor with staff members to look at the flow and ask what is stopping them from working better. Considerations include how many steps it takes to walk from the decontamination sink to the washers.
To help design an efficient and effective workflow for the CS/SPD, Weston “Hank” Balch, Director of Sterile Processing at University Health System, recommends tapping into your healthcare organization’s performance improvement or LEAN department.
“While they don’t know sterile processing, they do know process and workflow,” said Balch. “So engage these professionals, explain what you are trying to accomplish and get their feedback. There are a lot of opportunities that CS/SPD leaders miss out on because they may be tempted to build the same department they had at their last facility simply because they liked it and it worked. With a fresh set of eyes, you may find that you can get very creative with your existing space for improved efficiency and performance.”
Take advantage of vendor resources
Balch also suggests that CS/SPD professionals take advantage of vendor resources when renovating or rebuilding their departments. Many equipment vendors have an individual or team that specializes in equipment placement and its impact on workflow.
The CS/SPD team at University Health System recently performed a mini renovation of its sterile storage space area. One challenge they wanted to address was holes, rips and tears in wrapped trays. They implemented a combined solution from Belintra and Halyard Health that includes Halyard Health’s sterilization wrap products and Belintra’s Sterisystem storage and transport system and logistics flow solution for wrapped trays. According to Balch, the reduction in tray touch points that the solution provides has been a vast improvement over their previous processes.
“It is a modular system in that the transfer rack comes out of the storage system so it allows for my techs in the assembly area to wrap a tray, place it on the wire/silicone transfer rack, and place it on the sterilization cart. From the moment it is wrapped, that tray is not touched again by human hands until it is in the OR and ready to be used,” explains Balch. “We’ve also implemented it in our loaner/consignment area and saw holes go down to zero overnight. It is one of the biggest solution-driven disruption to the sterile processing space that I’ve seen in a long time.”
Another example is Aesculap ’s Surgical Asset Management Program, which has been implemented in hospitals and health systems around the world, helping facilities increase both the clinical and financial value of their surgical instrument inventory and sterile processing practices.
The first step in this process is the QuickScan assessment service. This four-day service provides a low-risk, low-investment analysis of the state of instrumentation, reprocessing practices and opportunities for improvement within the SPD and the OR. The results of this assessment lead to recommendations from Aesculap’s team of SPD consultants on how to further standardize and optimize instrument assets and practices. On average, Aesculap has found that hospitals have far more instruments than are regularly used, resulting in an average instrument reduction of 17 percent after optimization.*
Belimed offers consulting services to help guide CS/SPD redesigns and renovations. According to Steve Sutton, Director of Planning and Design Group, Belimed, the company bridges the gap between healthcare architects, equipment planners and clinicians to provide sterile processing designs addressing the demands of today and tomorrow — from concept to reality.
“Our singular focus on the sterile processing world gives us the expertise to consult with healthcare architects and equipment planners to create data-driven designs,” said Sutton. “Using our simulation and throughput assessment tools we streamline and improve the overall sterile processing work environment; ensuring on time delivery of safe and sterile instruments to the OR. This unique approach results in improved efficiency and quality while driving down cost.”
Engage facility plant management
Marjorie Wall, Director of Sterile Processing at Citrus Valley Health Partners in the Los Angeles area, had been working at a large trauma center in Northern California that hadn’t invested in its CS/SPD for quite some time. The equipment was outdated, inadequate and frequently in need of repair. This resulted in process inefficiencies and a backlog in the decontamination area.
The healthcare facility made the decision to completely renovate its CS/SPD and Wall learned many lessons in the process. A major factor was that they had to design a new department within the current department’s existing footprint. They also discovered that while the older equipment used more resources in terms of electricity and water, the rebuild design called for a greater number of washers and sterilizers, and the addition of a cart washer, all of which increased resource utilization. It ended up being a three-year project because the first year was spent building out boilers and draining systems to support the new equipment.
“My biggest piece of advice is to involve all stakeholders early on in the planning process, including facility plant management,” said Wall. “It may take some effort to bring them to the table but they need to be part of that conversation around new equipment and whether existing utilities can handle that, such as the building’s boilers and air compressors. Have these conversations early on so you know what you will need, how long of a project it will be and whether the vision in your head is feasible.”
Marcia Frieze, CEO, Case Medical, points out how water quality is an important consideration when designing a CS/SPD.
“Renovating and remodeling provides an opportunity to not only improve productivity and work flow, but also improve quality,” said Frieze. “A reverse osmosis (RO) water system provides high quality critical water for the final rinse and for all cleaning steps to reduce residue and create efficiencies. Water softeners and deionizer (DI) systems have many drawbacks and few advantages in health care settings. The former removes hard water ions and replaces it with salt. The latter removes some hard water ions but not all, and does not reduce bioburden. Case Medical provides RO water systems that clean better and are free rinsing.”
Quality control is critical
Amanda H. Coss, CSPDS, CSPM, CRCST, CIS, CHL, National Education Coordinator for Mobile Instrument Service & Repair, explains how CS/SPD design has historically focused on production. She notes how work areas were designed for the task and storage was placed wherever it could reasonably be accommodated. But as sterile processing has evolved and administrators have come to better appreciate its criticality to patient care, space is needed for things beyond production.
“A great example is quality control equipment and tracking systems,” said Coss. “Whether it is allowing room for basic instrument testing or setting aside space for automated testing systems like our fully automated Scope Control rigid scope testing platform, quality assurance (QA) is a new design consideration. You also must adjust designs for computer terminals to run tracking software. Making sure these workstations are in close proximity to production stations is key to ensure convenient access.”
Creating a better work environment
“When designing a CS/SPD, after you have addressed the necessities, next consider all of those extras that make a better work environment,” said Berg. “Those items where it is not about the standards or the best workflow, but let’s put this in here since we are remodeling because it is a great thing to have.”
“One example would be having a heat sealer at each work station so that real time packaging at the place the staff is working saves time and prevents build up of peel pouched items,” Berg added.
One important consideration when designing a better work environment is ergonomics. The Pure Processing PureSteel XI Reprocessing Sink has a small footprint but is perfect for vertically soaking larger instruments, according to the company. Pushbutton height adjustment sets the sink at optimal working height for each user, and a slanted wrist rest provides the proper ergonomic working angle for arms and wrists without pinch points. Standard accessories delivered with the sink include: three FlexiPump Independent Flushing Systems for consistent, automated pre-cleaning; back pegboard to organize tools at proper height and reach; a sink liner to protect instruments during processing; water volume indicators.
*Data on file
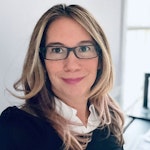
Kara Nadeau | Senior Contributing Editor
Kara Nadeau is Sterile Processing Editor for Healthcare Purchasing News.