To evaluate SPD Department of the Year nominations, Healthcare Purchasing News recruits a variety of staff members, editorial advisory board members that also are active professionals in the relevant field segments of the industry and the leader of the previous year’s winning department. Here are some notable comments and observations from this year’s judging team:
LeeSar, Fort Myers, FL, 2017 SPD Department of the Year
“While I have a heart for smaller departments achieving excellence in the face of financial constraints, I gave LeeSar the highest scores due their data-driven, LEAN approach to excellence. Their Kanban “PAR level idea for keeping sets sterile and available is intuitive and could drive OR satisfaction.”
“Overall LeeSar has taken the CS/SPD and brought it to a whole new level through its centralized, off-site processing, which delivers a broad range of services. I think their work with LEAN is very telling of their strategic, long-term approach. It also shows the commitment they have to education and training, and teamwork: process standardization, level schedule, analytics, scorecards, etc.”
“Excellent examples of quality tools being used throughout the department.”
“They understand the relationship between production, customer service, reduced infection rates, improved efficiency, lean management methods and shared governance. Their goals and objectives are clear, measurable and plan for optimal safety outcomes. Staff are involved in meeting goals and stretch goals. Simply put, their operation is state of the art. This is a showcase for best — the performance.”
[Quoting from the nomination’s Education category]: “In response, we created a vast career ladder structure and very deliberate development support from entry level through leadership positions. In addition, we received support from senior leaders to raise pay to the top of the market to reward and recognize our sterile processing professionals equitably.
“Once certified in CRCST, the employee is eligible to advance to Instrument Tech II. In this role, they are given support to obtain CIS certification, opportunities to mentor and precept, and participate in Lean projects. Once CIS certification and competency is achieved, the technician is eligible for Instrument Technician III advancement. From this role they can move up additional career levels including Lead, Support Roles, and Management. Motivated individuals can move from entry level skills and wages to advanced positions and wages in as little as three years.”
“[LeeSar’s] utilization of LEAN principles in the off-site center as well as at point-of-use is what all should be performing as standard operating procedures.”
Stony Brook (NY) University Hospital, 2017 finalist
“I would be interested to hear more about their daily ATP testing of instruments and how they are using the data in their quality program. I think the ATP test could provide real data to track decontamination quality instead of just assembly. I like that they send an SPD representative to daily OR huddles to discuss challenges and issues, and the SPD and OR management have a monthly meeting to address improvement, initiatives, procedures, and equipment.”
“For the customer service, teamwork and education/training categories, I was very impressed by this work: ‘One of the educational programs in place is for central sterile technicians rotating from every shift to observe actual surgical procedures. The technicians then provide feedback on how we can improve our service skills, this has provided excellent results in improving surgeons and nurses satisfaction by our presence in the suite.’ All of this demonstrates the work Stony Brook Medicine has done to elevate the role of CS/SPD, foster a great working relationship with the OR and give techs hands on skills and knowledge to effectively meet clinical needs.
“As for productivity and strategic outlook, the work they have done to centralize their CS/SPD function seems both efficient and forward thinking, and supportive of clinical needs: ‘Through centralization of material processing, storage, inventory control and distribution, a concept known as the Case Cart System has been implemented…. Tasks previously performed by OR technicians and nurses in the handling and processing of OR instrumentation are carried out by Central sterile Supply, leaving the OR staff free to have rapid turnover in a surgical suite. It will also enable CSS to be informed of the utilization of inventory and cost factors.’”
“Stony Brook is a traditional-based central sterile processing area that responds to their customer needs. They have developed a ‘safe space’ for instrument handling and management similar to the airline cockpit protocols. The Central Sterile Supply team is building its reputation and will become a key player in the highest standards of instrument production.”
[Quoting from the nomination’s Customer Service category]: “As part of our daily communication a representative from central sterile department attend daily operating room huddles to address any requirements for the day and issues that require attention. Our monthly central sterile /operating room meeting is held with all managers and addresses areas of improvement, new initiatives, procedures and equipment. Our Central Sterile/Operating Room Liaison works closely with the central sterile and operating room clinical managers maintaining a proactive approach in communicating tray and scopes forecasting for all surgical procedures scheduled.”
“The method of ‘Function follows Form’ is basic and creates a good foundation on which to build.”
University of Iowa Hospitals and Clinics, Iowa City, IA, 2016 and 2017 finalist
“I particularly liked their implementation of their [internal] tray audit program. I also thought their Access-based electronic tray audit sheet was innovative. Their improvement in certification percentage without mandating certification is great.”
“… The opening of the new Endoscope Reprocessing Center and their other work with endoscopes are definite improvements to customer service… Though they can’t pay for tech certification, they provide internal training. The fact that they have ‘increased our number of certified technicians by 167 percent, and our internal classes have waiting lists’ even though it is voluntary and staff have to pay for their own certification shows how committed the team is to education.”
“[They] are consistently doing what is required of them and stepping up their game for the benefit of patient care.”
“University of Iowa takes the lead [in] managing cross functional teams. [They] defended the need for an educator. [They] aligned their strategic plan with the overall healthcare organization’s organizational strategy.”
[Quoting from the nomination’s Education and Training category]: “Specific to on-the-job training we have implemented an internal tray auditing program where we are auditing over 3,000 trays a month (up from zero a couple of years ago). This not only prevented defects from leaving the department but also allowed us to give real time feedback to our staff as teaching moments. Education and Training continue to be a focus for us. We were able to demonstrate the need and add an Educator to our staff. We were also able to reclassify this position at a management level to attract top talent.”
“The Flexible Endoscope Reprocessing Center sounds like a great feat, creating a state-of-the-art facility implementing best practices for staff and function.”
Wesley Healthcare, Wichita, KS, 2017 finalist
“Their tracking of ‘OR Frictions’ is innovative. Their trend downward in OR complications shows their customer service is improving. Their productivity reports were innovative, specifically including a ‘complexity grade’ of the instrument sets being processed. They’ve found the way to make this kind of data motivating and not intimidating.”
“The work they have done to reduce OR frictions by 96 percent is a strong indicator of their commitment to customer service. The in-services and incentives [for education and training] were positive… they reimburse fees related to training or certification, and offer bonuses [for training completion].”
“Wesley understands that SPD is the manufacturing arm of the medical center and affiliates. They are proud of their customer service, production, teamwork, education and strategic planning strategies. FTEs are very lean, and it is a wonder how they accomplish all that they do with such lean staffing. Leadership gives them full support. They have contractor support and C-suite support that will allow them to expand, enhance and update their physical space.”
[Quoting from the nomination’s Customer Service category]: “Not only does Wesley’s SPD meet the needs of the OR and other department’s served, SPD has lowered its OR frictions by 96 percent over the past two years. OR Frictions, a measure created and trademarked by STERIS IMS, represents the count of avoidable errors by SPD or OR that cause ‘friction’ or problems for the clinical team. Reduced OR frictions leads to increased OR performance and surgeon satisfaction.”
“Recognition by senior leadership that OR and SPD are equal partners is refreshing.”
Source: Healthcare Purchasing News, March 2017
Team Roster: LeeSar’s winning SPD team
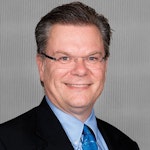
Rick Dana Barlow | Senior Editor
Rick Dana Barlow is Senior Editor for Healthcare Purchasing News, an Endeavor Business Media publication. He can be reached at [email protected].