Blame supply hoarding on Nursing’s lack of confidence and trust in Supply Chain’s ability to deliver products and services, experts tell Healthcare Purchasing News. But that quick and easy diagnosis belies the seemingly long and arduous therapeutic journey to establish — or re-establish — the professional relationship between the two groups. Provider and supplier experts share their advice.
“The only way to establish trust is to develop a plan with Nursing and do what you’re going to say you do. The trust will only last as long as they see the plan working. In our case, the plan involved real-time locating technology to manage a periodic automatic replenishment (PAR) model for asset tracking. Our facility already had the enterprise RTLS infrastructure in place, so there was little to add except tags to every IV pump and a software module for the Supply Chain team. The tags use active infrared/RFID technology, so they’re always automatically updating the software and PAR-level counts with their location — no need to walk around with scanners. We set up a central distribution model, where each unit took pumps from a ‘Clean Supply’ room. The RTLS monitored the number of pumps in those closets and sent alerts when clean inventory started getting low or when there was surplus. Distribution would replenish clean supply before the count reached zero, so when a nurse goes to that supply closet, there’s always a pump available — no reason to stash any away. They trust that there will always be a pump available when a patient needs one.”
— Doug Duvall, Solution Architect, Versus Technology
“Nurses don’t hoard supplies as a hobby, but because of a lack of trust that their supplies will be there when they need them. To break this self-preservation habit, supply chain needs to always meet or exceed their nurse’s expectations about their supplies. Then over time, nurses will hoard less and trust more in supply chain.
“I would recommend the following steps to repair and/or build relationships of trust with your hospital’s department heads, managers and their staff as follows:
“Never lie, deflect, absolve yourself or your supply chain department of your responsibilities to your department heads, managers and their staff. Always take responsibility for your or your staff’s actions.
“In cooperation with your department heads, managers and their staff, establish standards for your supply chain’s performance, such as, exchange carts will be refilled by 8:30 a.m. every morning, emergency orders will be delivered within 15 minutes, etc. Then meet those standards, without exception, every week, month and year.
“Survey your hospital departments on a quarterly basis to see if your Supply Chain department is meeting their expectations based on the agreed-upon standards. Correct any deficiencies noted in your service based on this feedback.
“Taking these three recommendations seriously will repair or build trust, in about a year or less, with any department or unit in your hospital.”
— Bob Yokl, President and Chief Value Strategist, SVAH Solutions
“I’d say there are three pillars.
Appropriate PAR levels. PAR levels should be set based on accurate usage data and should provide sufficient safety stock to cover most swings in usage. Small, low-dollar items should be overstocked. It is crazy to run out of toothpaste or lubricant packets because the PAR level is too low. I remember early in my career spending time to decide whether to keep 2 or 3 sterile tongue depressors as a par. Now I would just provide a box. They will never run out and it makes restocking easier.
Consistency of service. Consistency provides a confidence level that cannot be achieved without it. When clinicians feel assured that the PAR area is being restocked accurately and completely, their trust builds. It helps if the service is provided at about the same time every day. And if the PAR is not performed daily, the staff should be aware of the schedule. Quality should be assured through frequent inspections. All PAR areas should be kept neat and orderly.
Communication. Keeping the clinical staff informed and part of the process is critical. Staff must know about issues with product availability and what you are doing about it. If there are backorders or stock-outs the staff must know — both about the issue and what is being done to correct it. Product changes should never be a surprise. Any substantial changes to the PAR area should be announced well in advance. These three things, done well, can go a long way towards curtailing the perceived need to hoard.”
— Dave Kaczmarek, CMRP, FAHRMM, Principal, Healthcare Supply Chain Solutions
“First, implement systems at the point of use that allow proper data capture without nurses having to spend time managing supplies. At one large metropolitan area hospital, they’ve reduced the time nurses spend in the storeroom by 65 percent, which equals several hours per day of saved time in each unit.
“For inexpensive items, two bin Kanban systems are easy and very inexpensive to implement. Nurses love them because they don’t have to do anything except grab the item they need, and occasionally move an empty bin up to a top shelf. Kanban is an extremely accurate way to manage low-cost items. For the more expensive, chargeable items, use a perpetual PAR approach, with technology that allows levels to be visible and easily managed, with daily, actionable reports that can be shared with clinicians so they understand and agree on adjustments to PAR levels.
“If I’m running Supply Chain, I want to see what stocked out yesterday. If it’s stocking out repeatedly, I know I have to adjust par, and I suspect I have a hoarding problem. It’s a great time to be proactive, go find the nurse manager and say, “I see you stocked out three times in the past two weeks.” You can let the manager know that you’re aware of the stock-outs, you have a solution to the recurring issue, and you’re ready for him or her to show you around the unit, so you can be sure there’s enough on the shelf, you can get correct counts, and check for expired products. A daily stock-out report allows you to get in front of recurring issues.
“Good velocity reporting shines a light on problems right away and makes it easy to show the clinician what’s happening in their area. You can see what’s moving faster or slower than you’d anticipated, and you can adjust quickly — getting rid of the items moving slower to make room for those moving faster.
“Simple as this sounds, this level of efficient, simple inventory management doesn’t exist in healthcare today. But it can, and it should be our goal. Get rid of PAR replenishment, get simple systems that gather data, get simple reporting that we can share with clinicians, and give them the confidence that supply chain knows exactly what’s happening, so they won’t hoard and supplies won’t stock out.”
— John Freund, CEO, Jump Technologies Inc.
“Prove it by taking all steps to make sure delivering the right item, to the right place, at the right time. Keep track of fill rates and delivery times, and report the stats to each customer. Advise them what corrective is being taken if stats are not satisfactory.
“Double-check picked orders before they leave the storeroom or Central Supply. Have orders checked by roving Supply Chain [quality assurance] staff, as orders are being put away in the user departments.
“Have the Supply Chain staff sign the requisition for orders he/she fills, and by the person who delivers and/or puts the orders away.
“Provide a place for user depart staff to note that the order was not correct as of the day/time they started to put it away. Or provide a phone number that user staff can call when an error is discovered. Then have the person(s) who filled and/or put the order away go to the user department to check on and rectify the problem.
“Make rounds periodically to see what is happening. Take corrective action. Advise the customer what corrective action has been taken.”
— Jamie Kowalski, CEO, Jamie C. Kowalski Consulting LLC
“The answer is velocity reporting. We’re starting to ramp up quickly with a relatively new reporting tool — in fact, we’re rolling it out right now on our busy 2nd floor. In this nursing unit, they have IV fluids stuffed in every nook and cranny. The bins are so full, you can’t rotate the stock, and as a result, a lot of IV fluids are expiring. The nurses felt like they wanted a lot of everything on hand, and in turn, there’s a lot of waste of items that aren’t used that often. I said ‘let’s just see what you’re using.’ Now we’re normalizing what they keep on hand. For things they’re using at a high rate, we’ll stock them. The more unusual items will be stocked in the hospital and we’ll replenish on the 2nd floor as needed. We’ve been planning to change out their shelving and the overstocking in this area has slowed down the process.
“Velocity reports have enormous value, both to Supply Chain and Nursing. We can show nursing exactly what they’re using. Nursing leadership is very aware of budget and they’re committed to supporting our effort to minimize spend. The data helps a lot — now, I can show them ‘par is 50 and you’re averaging 9 each month over the 60 days.’ With this data, we can reduce par and in turn, costs.
“Communication, trust, building relationship helps as everyone becomes more accountable. But it’s a balance. You have to decide how much time and effort you want to spend watching even the lowest cost supplies.”
— Seth Larson, Director of Supply Chain Management, Chesapeake Regional Medical Center
“Some areas of the supply chain are using the concept of a ‘Service Level Agreement’ or SLA, with their nursing partners. This includes delivery, restock, and stock-out resolution timeframes, and escalation procedures if those service levels aren’t met. Posting these in a visible location adds to the credibility of the supply chain promises. It also helps facilities to start in the smallest area with the biggest pay out — in terms of both high-cost products and products apt to expire, for example, the Operating Room or Cath Lab.”
— Carola Endicott, Vice President of Services and Operations for Cardinal Health Inventory Management Solutions, Cardinal Health
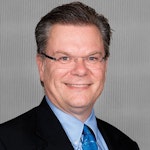
Rick Dana Barlow | Senior Editor
Rick Dana Barlow is Senior Editor for Healthcare Purchasing News, an Endeavor Business Media publication. He can be reached at [email protected].