Inspection reflection: What’s Supply Chain’s connection?
Getting ready for a scheduled facility inspection by an accrediting, certifying or otherwise regulatory agency is a lot like getting your house in order to accommodate visiting relatives and friends arriving for holiday celebrations.
Okay, maybe that’s an oversimplification, because most would agree that quality control at a healthcare facility far surpasses trying to impress your mother-in-law or college roommate. Further, these regulatory agencies expect your organization to be operating at near-peak performance 24/7/365, and not just during those tense “evaluation” times.
Of course, unscheduled facility inspections resemble more of a pop quiz without the opportunity of cramming the night before.
Either way, healthcare professionals — administrators and clinicians alike — can agree with a degree of nervous laughter that these inspections can be tense — whether the results cause alarm, relief or something in between.
So where does Supply Chain fit in all of this? Are Supply Chain pros far enough removed from the “sturm und drang” of regulatory inspections or are they supposed to be poised to support whoever needs it? Experts overwhelmingly argue for the latter.
Then the question arises about how prepared — reasonably — should Supply Chain be for scheduled versus impromptu or unscheduled inspections and visits? That’s where it can get a bit dicey. On the surface, the obvious answer is BE PREPARED ALL OF THE TIME! But just how reasonable or even realistic is that?
Mantra vs. motto
If anything, assessments and inspections have a way of uniting everyone as a team — clinical and operational, according to John Gaida, Senior Vice President, Supply Chain, Texas Health Resources, Arlington, TX.
“Scheduled visits are fine and necessary in my opinion,” Gaida told Healthcare Purchasing News. “It gets everyone pulling together on a common mission, which makes everyone that much better as a team. Clinical staff seem more willing during these times to work closer with support staff.”
Gaida listed a number of key inspection issues potentially impacting Supply Chain.
Inspectors will check out the storage rooms for cleanliness and clearance issues — both near the ceiling for access and sprinkler head mobility (see sidebar) and under the shelves for cleaning, he indicated.
Exterior cardboard shipping containers can be an issue, according to Gaida. “They don’t like to see cardboard boxes that were exposed to shipping [processes, such as] trucks, dampness, dirt, etc. They only like to see interior cardboard on the patient care floors,” he said. “Due to so many folks using [low-unit-of measure distribution] these days the interior has really become the exterior, and the preference is no cardboard at all outside the supply chain management storage room.”
Recent developments include questions about vendor sales representative access to patient care areas.
Gaida said he’s also noticed questions to clinical staff about how the organization monitors the effectiveness of care delivered to the bedside by third-party providers or sales professionals.
Outdated supplies or supplies that “give the appearance of age or being compromised” has become a focus, he noted.
If Supply Chain handles equipment cleaning for the organization they are asked to provide standard operating procedures — especially focusing on adherence to manufacturer standards, Gaida emphasized.
Emergency preparedness and safety issues may become a key factor for Supply Chain, as well as for any hospital employee, he said.
Finally, staff can be asked about product and equipment evaluations — how they are handled and what discussions are underway at the moment, Gaida said.
Scheduled inspections allow the facility to prepare in advance for the inspection, acknowledged Donna Swenson, Chief Quality Officer, Quality Processing Resource Group LLC (QPRG), Ashburn, VA.
“There really should be minimal likelihood that there are any problems when the inspection is scheduled in advance,” Swenson said. “However, facilities are supposed to be ‘survey ready’ at all times. To ensure that this is the case unscheduled inspections are useful. It is much different to find [The Joint Commission], or in my case FDA, on your doorstep in the morning than to know in advance and to be able to ensure all personnel needed are present at the facility.”
Still, it’s reasonably expected that Supply Chain has procedures in place to ensure that purchased products meet quality standards, Swenson noted.
“For critical clinical products the facility should identify the product characteristics needed, identify the companies who can provide these products and then ensure that product is only purchased from the approved suppliers,” she continued. “Suppliers should be approved in advance to ensure that products meet critical quality characteristics. This can only be done by approving suppliers and products before purchasing from the supplier. There should also be a process in place to ensure that when product is received that it in fact meets the approved product characteristics. Many times product is purchased without product characteristics being specified. This can create serious problems for the users of the product and sometimes for patients.”
The facility’s quality management system should ensure that purchased clinical products meet department specifications, according to Swenson. “I know that some people will consider this unreasonable, but if the healthcare facility wants to provide high-quality and safe patient care this approach is needed,” she insisted.
“While a scheduled inspection would certainly take some of the anxiety out of the annual visits, the organization’s goal is to always be prepared,” said Terry Murphy, System Director, Supply Chain, Lee Health, Fort Myers, FL. The equation is simple: Have appropriate policies and practices in place and follow those expectations, according to Murphy. “Say what you do, do what you say,” he added.
Yet Murphy acknowledged that Lee Health’s Supply Chain team takes a more active role in the inspection process since the organization switched to using DNV GL Healthcare. In fact, for more than 20 years under The Joint Commission’s accreditation process, Supply Chain had very little interaction during the annual process, Murphy indicated. “Supply Chain would ‘sit in’ on the [Environment of Care] session but rarely had any process questions,” he added.
“With our transition to DNV, Supply Chain has dedicated time with the surveyors during the annual accreditation process,” Murphy continued. “It is a very interactive session in which we review policy related to the performance of supply chain within the organization and the monitors and measures for key performance indicators — fill rates from our primary distributor, tracking mis-picks, shortages and overages — as well as upstream with vendor selection and performance review of specific criteria which the supplier is expected to meet.”
Supply Chain’s involvement under ISO standards has teamed the department with clinicians to report and discuss product concerns and consumer complaints, and tie those concerns back to vendor performance for product failures or additional product education needs, according to Murphy.
“Maintaining Joint Commission standards daily allows basically a stress free inspection,” said Les Coffman, Senior Manager, Materials Management, Hospital Operations, UPMC, Pittsburgh. “When inspectors arrive Supply Chain needs to ensure all of the following points are sustained: Outdate audits, gas cylinders secured, supplies are off the floor, supplies are kept 18 inches from the sprinkler heads and ceiling, clean bins, no corrugated cardboard, no wooden pallets in supply rooms, equipment must be recognizable as clean or soiled, bottom of wire racks must have a water barrier and soiled and clean equipment must be separated and soiled should be covered when being transported. We should always be prepared.”
Preparation hinges on “providing the proper education and training of staff to achieve and maintain regulatory readiness,” said Jon Braeger, Senior Manager, Materials Management, Hospital Operations, , UPMC. “Once the staff is trained to these standards, regular quality audits are made to confirm the workflow is meeting all standards.”
For example, Braeger encouraged demonstrating ongoing process improvements in storage locations, such as implementing kanban to show proper product rotation of disposable products and strengthen the supply chain’s condition and readiness.
“Having good organization of products in the clean supply room which presents neatness and order, along with providing exceptional customer service to nursing staff, brings positive comments during the audits from the hospital management team,” Braeger said. “The quality and service components, along with maintaining a high level of readiness for the materials management process supports the total organization during a survey, showing everyone is working together to provide great care for the patients.”
That’s why Supply Chain can and should be involved in system-wide education and planning sessions, said Mary Beth Lang, ScD, Executive Vice President, Cognitive Analytics Solutions, Pensiamo, Pittsburgh, and previously Vice President, Healthcare Pharmacy and Supply Chain Management Commercial Services, UPMC. “If there are products or service change requirements, then Supply Chain is able to take the lead in the implementation and training,” she added.
Procedural pull
Joe Goyne, Senior Director, Logistics, Geisinger Health System, Danville, PA, acknowledged that scheduled surveys obviously allow time for planning and preparation, which can alleviate stress from a regulatory survey. But Supply Chain is being drawn into the process more, and that’s necessary, he insisted.
To wit, Goyne noted that Geisinger’s Supply Chain team has grown beyond traditional purchasing and stocking of shelves.
“Our team is much more hands-on operationally and is embedded within nursing units as well as managing functions like patient transport, patient equipment distribution and specialty inventory management,” Goyne said. “Our Supply Chain team has even more to offer, and in my opinion, should be more involved with increased participation in surveys.”
In fact, survey preparedness involves Supply Chain directly on a regular basis, he noted. During bi-monthly reviews of standards, the Emergency Management Committee relies on Supply Chain to provide updates on supplies-on-hand and 96-hour sustainment.
“Many hospitals report having issues justifying 96-hour self-sustainment, but Geisinger has impressed surveyors with our plans,” Goyne noted. “Supply Chain is actively involved in the Emergency Management session of the survey and it’s required that Supply Chain staff are able to speak to supply and resource issues. Supply Chain is also imperative to Environment of Care when it comes to the ongoing struggles of hospital clutter both in preparation for Joint Commission visits and during day-to-day patient care. By meeting regularly with key departments, Supply Chain can mitigate issues leading up to a survey.”
Goyne argued that Supply Chain should be accountable “for knowing what we know,” he said. “Being accountable for what we do every day, preparing our staff and having them be our overseers of compliancy” is a reasonable expectation.
Yet Goyne recognized that Supply Chain may not be considered a “vital part of survey readiness” in some cases. What happens? “In those instances I find the lack of planning and preparation by others sometimes becomes an unreasonable hurdle for Supply Chain. Regardless of how well-prepared the Supply Chain team is for a survey there tends to be some last-minute re-work that needs to be done.”
Supply Chain should play a significant role in inspections “because it oversees much of the data required to demonstrate compliance as it relates to a hospital’s vendor population,” said Jackie McGuinn, Senior Strategic Marketing Manager, GHX, Louisville, CO. “It’s reasonable for inspectors to request certain data pools regarding the management of a hospital’s vendors, and the Supply Chain team needs a way to provide it, quickly and efficiently. One of the main objectives of The Joint Commission is to ensure that hospitals are protecting their organizations and their patients. Vendors introduce risk to a hospital, so it’s important that supply chain does its part to protect a hospital from non-compliance. This can be done by centralizing credentialing processes.”
Still, McGuinn observed that The Joint Commission’s flexibility in allowing hospitals to define policies and procedures “can unintentionally create confusion as to what will be reviewed at inspection time,” she said. “A guideline, such as being ‘aware of who is entering the organization,’ can vary significantly in practice by hospitals, and it’s unclear how individual inspectors will evaluate compliance to that policy. More consistent guidelines on how to monitor vendor activity will help hospitals eliminate some of the guesswork and improve compliance.”
Shock and aw geez?
Naturally, unscheduled “surprise” inspections can spike staff blood pressure readings, particularly if they’re not fully ready or reasonably prepared because daily operations don’t quite match up to what’s specified on paper.
“Scheduled versus unscheduled, while creating a sense of unknown time, shouldn’t make a difference overall as any quality-driven organization is always prepared,” Lee Health’s Murphy urged. “This is a safety and patient care culture in which we must operate at all times.”
In fact, Pensiamo’s Lang noticed that many healthcare systems “have moved to readiness at all times. It completely removes the stressors associated with a Department of Health or Joint Commission audit. It all comes back to training the teams and frequent rounding,” she added.
UPMC’s Coffman agreed. “By always being prepared, surprise visits are not stressful,” he said, emphasizing that the team should be prepared for any questions, maintaining standards for supply and equipment storage and proper data storage.
“If we are operating in a survey ready state every day — which we should be — there should be very little concern when it comes to an unannounced survey,” said Geisinger’s Goyne. “We always strive to function in this manner. Regardless, the entire Supply Chain team needs to be the eyes and ears of compliancy when it comes to our operation. We also need to be good teammates and contributors for the areas where Supply Chain may not typically be involved.”
But surprise visits don’t have to be stressful, according to Texas Health’s Gaida.
“I believe unscheduled visits are fine as long as ‘perfection’ is not expected,” he said. “It is good to catch the everyday life events of a working hospital, but it just is not the same as when an organization has had a chance to focus on preparation. Supply Chain should not be affected by unscheduled inspections — at least not like other areas.”
QPRG’s Swenson agreed that Supply Chain should be prepared to show how their purchasing and storage processes work on a daily routine basis.
“Employees of supply chain need to be held to competency standards the same as all other hospital employees,” Swenson said. “These standards should be available, and employees should be able to speak to them. Employees should be able to articulate how they impact the quality of patient care and patient safety. [The Joint Commission] should be able to see that employees are always ‘survey ready.’”
On the other hand, GHX’s McGuinn questioned whether unscheduled inspections offer benefits beyond “gotcha” moments and shocking facilities back into quality operations.
“Supply chain’s role related to an inspection doesn’t change because the inspection is a surprise,” she said. “The department will be still expected to provide the same information and data to demonstrate compliance. However, the bigger question is whether or not impromptu inspections benefit the industry. Are they reasonable? Scheduled or unscheduled, an inspector’s approach is the same, as well as the overall aim — protect hospitals, patients and staff, and ensure better outcomes. The added stress and anxiety related to unscheduled inspections is perhaps unnecessary.”
Supply Chain’s commitment to inspections, reviews
Using The Joint Commission’s key categories for accreditation and certification inspections, HPN asked supply chain experts where their departments and staff members were “directly” involved (actively participated) versus “indirectly” involved (provided as-needed support for other departments). Depending on the healthcare system, facility or department, results were mixed. In fact, those topics below in italics could go either way, according to respondents.
Direct
Environment of Care
Emergency Management
Infection Prevention and Control
Performance Improvement
Leadership
Life Safety
National Patient Safety Goals
Nursing
Rights and Responsibilities of the Individual
Indirect
Accreditation Requirements
Accreditation Participation Requirements
Human Resources
Information Management
Provision of Care, Treatment and Services
Record of Care, Treatment and Services
Transplant Safety
Waived Testing
Related sidebars: https://www.hpnonline.com/inspection-dos-and-donts/
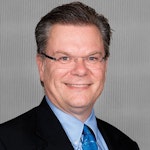
Rick Dana Barlow | Senior Editor
Rick Dana Barlow is Senior Editor for Healthcare Purchasing News, an Endeavor Business Media publication. He can be reached at [email protected].