What can the U.S. learn about using data standards?
Healthcare supply chain operations in the United States face a stream of urgent, ongoing messages about standards adoption, standards usage, standards benefits and doomsday predictions of what will happen if they don’t apply them now, rather consistently for more than a decade now. This year offers no exception.
Here at Healthcare Purchasing News, we’ve been writing about this topic for several decades, keeping track of the ebb and flow of acceptance, adoption and then complacency before evangelism emerged again. Naturally, and most unfortunately, many healthcare supply chains here still haven’t made as much progress as they should, at least as much as their counterparts in Ireland.
Maybe it’s a miracle. Maybe the messengers were wrong or a grand scale marketing plot is at work. Or, maybe our supply chains just get better at workarounds, partial adoption, or offering excuses such as “the suppliers aren’t providing standard identification barcodes, our electronic health record (EHR) system won’t integrate them, we don’t have the money to update our databases, or our nurses don’t have time to scan, etc. …”
Sound familiar?
What happens ‘over there’
Have you ever been curious about what healthcare supply chain systems are doing outside of the U.S.? We could learn a lot from them.
I had the opportunity to meet several members from the supply chain team from St. James’s Hospital (SJH) at the annual GHX Healthcare Supply Chain Summit 2016 conference in May. SJH is the largest healthcare provider in Ireland and represents; more than 1000 beds, more than 4,000 staff members, and since 1994, includes the largest teaching hospital in collaboration with Trinity College in Ireland. They annually care for 23,000 inpatients, 47,000 day cases and 283,000 outpatients.
At the conference, Pat Bailey, Materials Management Lead and Greg Magrane, E-Commerce Project Manager, from St. James’s focused on how they are achieving “world-class patient safety” success by adopting GS1 standards including Global Trade Item Numbers (GTINS), Global Location Numbers (GLNs), radio-frequency identification (RFID) and bar-code tags and then integrating them with GS1 databases. Through this technology, they were able to enhance their ability to control costs while enhancing patient safety. During our discussions they mentioned their surprise that U.S. hospitals hadn’t embraced the use of these techniques.
The decision to adopt these GS1 standards didn’t stem from doomsday messages in Ireland. It began in 1995 due to their earnest search for a solution for tracking problems at their system that encompassed supply chain automation through e-procurement using EDI and GDSN; patient care supplies; MISA Patients (continuum of care of elders); tracking of ‘Precious Samples’ from patients in the Operating Theater to laboratory; staff including porters; wheelchairs, mobile equipment, beds, infusion pumps, etc.; and fine art (SJH has an impressive art collection from donors throughout the centuries it has existed).
“Patient safety is at the core of our mission at St. James’s Hospital. Adoption of global standards contributes to patient safety, improved efficiency and reduced cost in everything we do, everybody wins,” said St. James’s CEO. “These standards and associated technologies enable the automation of processes at the hospital. This is the right thing to do for our patients and builds on our long standing relationship with the GS1 organization.”
I toured their campus in Dublin in August. They have been delivering care since 1667 at the current location, which later became a hospital in 1727. The campus is a patchwork of low buildings spread out in a section of Dublin that also is home to the Guinness Brewery operations. The facility is currently in the midst of construction adding a new Children’s Hospital on campus.
My tour guide, Greg Magrane, explained that the campus is spread out over blocks of short, and not easily navigated, buildings due to past city ordinances that inhibited building height, which also created a supply tracking and delivery challenge.
SJH also recently added the Mercer Institute for Successful Aging (MISA). The goal of the MISA facility is to “promote healthy and successful aging as well as raising standards and expectations for the care of older people,” in particular due to the aging population. The facility also creates additional track-and-trace challenges and the need for better clinical data in order to control costs and identify effective treatments.
Starting up
My interest in their operations was piqued by success stories they shared after they adopted product tracking and tagging as a way to “provide care that is safe, effective and accessible so that our patients achieve the best possible outcomes and experiences of care.”
The road to SJH e-procurement initiatives began in 1995 with analyzing their current formal supply arrangements. They identified what the supply chain contribution to cost savings could be through formal contracts and aggregation. This resulted in purchase and supply data being utilized more for decision making.
SJH found that the pathway to product identification and tracking was the only sustainable way to deliver care affordably and efficiently.
Similar to what U.S. healthcare facilities face, SJH encountered barriers in the Irish Health Market, including the lack of standardized product identification, the lack of standardized location identification, multiple product catalogs from suppliers, and inaccurate and inefficient procurement practices.
Hemophilia, instrument, tissue tracking successes
Hemophilia: The GS1 collaboration began in 2003 with a Hemophilia Initiative that was born out of crisis due to patients receiving contaminated blood products and included track and trace of blood products for hemophilia patients. It also uses GS1 barcodes to track and trace all medication (including to the home) and a medication scanning app for patients to scan medication barcodes in the home. They say if needed they could implement a recall within 10 minutes, with 100 percent accuracy. They also are saving approximately €5 million per year (approximately $5.6 million) since the start of the project.
Surgical instruments: In 2011, SJH continued with the Hospitals Sterile Services Unit (HSSU) National Sterile Instrument tracking solution with GS1. The pilot site included the implementation of a national surgical instrument tracking project that tracks reusable instruments. It provides traceability, visibility and quality assurance for the decontamination process across multiple sites. It minimizes the risk of surgical site infection and allows reusable instruments to be shared seamlessly across multiple hospitals, increasing both financial and operational efficiency.
Tissue: They have also created a system with their Operating Theatres (OT) that RFID tags all precious (tissue) sample containers taken from the OT that includes the OT location, patient identification, time, date, and status (high, temperature sensitive, etc.). The tissue samples are brought out of the OT by a nurse and taken to the central tissue transport location where they are refrigerated, if necessary, and picked up by a courier to take to their laboratory. Critical samples are handed directly to a waiting courier. All samples are tracked from the time they leave the OT until they arrive in the lab for testing. If a sample doesn’t arrive in the timeframe prescribed, phone calls are generated to the courier and the sample is physically tracked.
“No one wants to see a patient suffer through another surgery because of a lost or misidentified sample,” Magrane explained. SJH created the system after a critical sample was lost. In addition, Magrane holds training sessions with the OT nurses to emphasize the importance of their role in ensuring patient safety and proper care by using the tissue identification and transport system.
Current projects using GS1 Standards
SJH has now gone live with several suppliers using Master Data Synchronization via GDSN (Global Data Synchronization Network), standardized data formatting and the deployment of EDI for supply chain transactions (purchase orders, advanced shipping notes, receiving advice notes and invoices). The next phase is for labeling of consignments with GS1 identifiers and bar-code symbols and AIDC (automatic identification and data capture) and SJH to record receipt of goods and to complete the three-way matching process to enable prompt payment.
Future tracking projects
SJH currently is working on a point-of-care Scan for Surgery pilot to capture supplies at bedside. The pilot team includes the GS1 Director of Healthcare, the SJH Program Director, several suppliers and solution providers using GHX Powergate and SAP (the SJH ERP information system vendor).
This also includes working on a collaborative project with other hospitals and healthcare organizations in the United Kingdom (NHS and Trusts Demonstrator Sites). They hope to save time by sharing and cross-learning from NHS experiences in data capture and adoption technologies. Further, they are working on ways to engage supplier involvement in their tracking commitment with tagging compliance with an ambitious goal of transacting all purchase orders, purchases and payments using full electronic data interchange (EDI) implementation using GHX as their e-procurement partner.
During our tour, Magrane took a few minutes to check on some crates of oxygen tanks to see if their labels had GTIN codes as part of his vendor compliance tracking. He mentioned the containers and their tracking had come up as a concern, but noted that these containers were already properly tagged. We also viewed an OT supply closet that contained orderly trays of tagged critical supplies.
Magrane mentioned they are still struggling with some vendors that don’t use GS1 codes on their supplies and wondered about GS1 tagging in the U.S. I explained that the Food and Drug Administration (FDA) has created a system for vendors to identify their medical devices, and it’s currently being implemented as part of an FDA mandate to uniquely identify medical products.
As Magrane emphasized, “where there’s mystery there are margins that are being missed.”
simulated plan in the center (oval building).
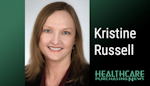
Kristine Russell | Publisher Emeritus
Kristine Russell is Publisher/Executive Editor, Retired
Healthcare Purchasing News, EVP, Healthcare Division, Endeavor Business Media LLC.