During the Independence Day holiday this past summer, the Barlow family visited the Smithsonian Air & Space Museum at Dulles International Airport in Washington, DC.
One of the exhibits was a replica air traffic control tower. Visitors were able to watch airplanes take off and land as well as read detailed displays and watch videos that explained what air traffic controllers and operators do, how they do it and why they matter.
We all have a general idea of how they operate, of course. A station at the exhibit stated that “the air traffic control systems main purpose is to prevent collisions by separating aircraft from terrain, obstacles, and other aircraft.
“Air traffic controllers organize the flow of traffic; keep the traffic flowing smoothly, safely, and efficiently; and coordinate the movement of aircraft around bad weather… provide information about weather and unexpected events and advise pilots about more efficient routes.”
In short, their efforts can make the difference between life and death.
Thoughts of the healthcare supply chain leaders operating in a similar manner came to mind. How so?
“Supply chain leaders organize the flow of products and other resources; keep the products and resources flowing smoothly, safely, and efficiently; and coordinate the movement of products and resources around changes in demand and usage… provide information about consumption and practice patterns and unexpected demand changes and advise clinicians about more efficient product and service options to help them improve business and clinical operations, their individual practices and patient care as a whole.”
In a way, their efforts can make the difference between life and death, too.
Supply chain leaders — just like air traffic controllers — function as advisers and facilitators, continually amassing and analyzing data on resource consumption patterns, clinician practice patterns (doctors and nurses) and supplier production patterns so that they can provide useful information to their clinical, financial and operational customers when they ask for it, if not before they ask for it.
Such applications of data science from a supply chain control tower represent the litmus test for the supply chain executive and leader of the future.
Of course, whether you’re ready may hinge on the maturity of your supply chain operation. A few weeks ago, Healthcare Purchasing News hosted a webcast sponsored by Ryder Systems Inc. where Ryder supply chain pros highlighted the importance and magnitude of supply chain operations as the second-largest cost center behind labor with the gap between the two closing as the years advance. (To access the webcast,visit https://www.hpnonline.com/webinars/HPN-RyderWebinarVideo-Login.htm.)
One key element for success? Effectiveness as a baseline before efficiency for supply chain practices. Basically, perform it right before you decide to improve it to the point of doing it well — or at least better.
The challenge? Ryder execs cited research from the Center for Innovation in Healthcare Logistics at the University of Arkansas that showed more than 50 percent of supply chain execs surveyed classified their operations as “ad hoc” and “defined,” which CIHL and Ryder termed as “immature.”
The bottom line: You have to walk before you run, and apparently many organizations have miles to traverse.
So the question remains: Do you have what it takes to build and maintain a supply chain control tower operation?
Doctors, nurses, your healthcare organization and the patients you serve — not necessarily in that order — depend on it.
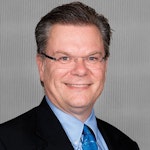
Rick Dana Barlow | Senior Editor
Rick Dana Barlow is Senior Editor for Healthcare Purchasing News, an Endeavor Business Media publication. He can be reached at [email protected].