Balancing clinical, central supply chains a critical pursuit
If there is one common and continual complaint about the Supply Chain department from their clinical customers, which, by and large, represent general, surgical and critical care nurses, it’s not just about product choice, evaluation and selection.
It’s about product availability — what’s accessible in the nursing units, on the shelves, in the closets or automated storage units. While many facilities get it right most of the time they may not get it right all of the time. Perhaps that’s an unrealistic expectation by front-line caregivers who don’t want to be inconvenienced in a pinch, or, say, ever. After all, a “perfect order” may not translate into “perfect inventory,” depending on how you parse the definition of “perfect.”
High-tech automation and electronics can help, but that hinges on budgets. Data cleansing must be routine regardless of inventory management process type — manual or automated via software, online desktop or laptop PC vs. mobile device and whether those devices “talk” to one another.
Unfortunately, most information technology tools may require assistance from, if not oversight by, the IT department, and Supply Chain’s perch on the priority list typically depends on how closely their issues connect to revenue-generating areas, such as the operating room or clinical testing (e.g., laboratory, radiology).
Without that influential leverage, Supply Chain historically is left to its own devices, figuratively and literally, as it tries to manage both the central supply chain on the nursing floors as well as the clinical supply chain in the ORs and other specialty areas. Arguably, one may be more complex than the other, depending on the talent pool and tools at your disposal.
So how can Supply Chain satisfy the apparent unified needs of these disparate customers?
Delineate the nuances
For some, you have to know and understand the limits and possibilities between the customers.
“The management of inventory in central supply can often be handled more proactively — with greater predictability — than clinical inventory in the OR, Cath Lab, Interventional Radiology, Ortho and Gastro Intestinal areas,” said Sophie Rutherford, Vice President of Business Development, Jump Technologies Inc., Eagan, MN. “In the clinical areas, there’s more erratic, less predictable use of items. Additionally, the supplies tend to be very specific, based on criteria such as patients, procedure type and physician rotation.
“The products stored in central supply tend to be a bit more predictable,” Rutherford continued. “The inventory is more routine, and historically it’s been easier to set levels based on reasonably good usage data. But just like in the clinical areas of the hospital, the management of central supply inventory will be better or worse based on the accuracy of your item usage — or velocity — data.”
From central supply to the clinical areas of the hospital, there are big differences in how inventory arrives, according to Rutherford. “The supplies coming into central store come in through the distributor, which generally results in good visibility and predictability,” she explained. “But in the clinical areas, devices and supplies often come directly from the manufacturer, sometimes via a direct drop ship into a specific department or to a specific person, and often items are hand-carried in via the sales rep. With many different ways to enter these areas of the hospital, visibility is low, control is low and management is difficult. Purchasing processes are often bypassed entirely.”
John Mateka, a veteran Supply Chain Consultant and Interim Director, Materials Management,Clarendon (SC) Health System, contended that the manufacturing, retail and restaurant industries provide ample examples for healthcare organizations to emulate. They all standardize their processes while running businesses with specific product portfolios.
For example, McDonald’s revolutionized fast food delivery through its standardized processes and menu line-ups, according to Mateka. As a result, their inventory management programs are effective and efficient because they can anticipate demand and limit stock-keeping units. Meanwhile, the grocery industry pioneered the use of bar-code scanning to track inventory that is dispensed, purchased and decremented at the cash register, providing an accurate and reliable automated inventory system, Mateka noted.
“Healthcare facilities, on the other hand, are non-standardized with a scope of service offerings that requires carrying a huge portfolio of products,” Mateka observed. “Pharmacy may be an exception because of their approved formulary, but they nonetheless have challenges as well.” Still, the central storeroom or distribution center and major departments all handle inventory in some way, he continued. Central warehouses typically use a computerized system to handle more general products and those with high turnover rates. Department or clinical inventory tends to be more specific to the specialty area and in many cases is manually controlled or placed in automated low-unit-of-measure equipment. Regardless, inventory accuracy and replenishment efficiency hinges on people consistently complying with established processes, he insisted.
“For 30 years I have struggled with inventory accuracy — with some mild success — because of the wide variety of products, non-standardization and ultimately [erroneously] recorded product receipt, issuance and dispensing,” Mateka admitted. “Central inventories tend to be more accurate than clinical departments because the area is typically computerized and more secure, and dispensing errors are minimized because of the trained technicians deployed to do the picking.
“On the other hand, in the clinical areas nurses and clinicians are saddled with the responsibility to push buttons or fill out requisitions or even place stickers from products to cards, all additional activities beyond their primary responsibility of patient care,” he added. “The bottom line is that no matter how sophisticated the inventory system is, it is only accurate as the accuracy of the receipts and issues and proper recording of those transactions. So the challenge in healthcare inventory management is how can we efficiently accurately manage and conduct the tens of thousands of transactions that are needed to receive, put away, dispense and consume, and patient charge/record the vast majority of stock products within the hospitals?”
Access, demand matters
Understanding access points and demand parameters should provide ample direction, just like in the retail environment, said Carl Natenstedt, CEO, Z5 Inventory, Austin, TX.
“Central inventory is generally kept in a controlled location with access limited to inventory management staff,” Natenstedt said. “Transactions and inventory movement are limited to those that have appropriate access, training and motivation to do it right. By contrast, clinical inventory is open and accessed by the masses. Techs, nurses, even surgeons have access and often utilize inventory straight from the shelf. To make an analogy to a grocery store, central inventory is like the grocery store warehouse open to employees only and clinical inventory is like the shelves open to the public.
“Now if we could only put checkout counters at the doors to every OR suite,” he quipped.
Either area is defined differently by the speed of change, the specific units of measure, space constraints and technology access, according to Natenstedt.
“Change happens fast and is the norm on the front lines of clinical inventory,” he said. “Products change, storage locations change, surgeon demand changes. In short, change is the only constant in the clinical inventory area. By contrast, central inventories are reasonably static as change is more controlled and directed from the top down. Clinical inventory is managed and consumed in the lowest unit of measure, whereas central inventory is often managed in boxes and cases.”
Furthermore, clinical inventory tends to be “pressed for adequate space,” which creates myriad challenges when you factor in the low units of measure and sterility demands, Natenstedt noted. This impacts technology access, too. “Clinical inventory spaces often lack access to computers and the software systems needed to run an efficient supply chain operation. This can be due to space constraints, the diversity of locations used to store inventory and other logistical constraints. By contrast, most central supply areas have workstations, mobile tools and other software and systems easily accessible to manage the supply chain,” he added.
Glenn Tamir, Director, Distribution Channels, Pegasus Medical Concepts, Mission Viejo, CA, and a Lean-driven supply chain specialist, concluded that the disparate environments do make a difference as every department carries its own challenges through its method of operations.
“An OR/SPD environment is functionally very different from a med/surg unit, or from an ED for that matter,” Tamir observed. “Then there are clinical environments at different facilities, hospitals, ambulatory surgery centers, urgent care, etc., each with its own demands and limitations.”
The clinical environment, for example, involves a higher level of high-cost items that must be available with “zero room for error,” he said. “Solutions for item-level tracking like RFID have matured to the point of allowing the use of less-costly storage systems while providing transparency and even integration into the clinical software.”
Yet med/surg storage rooms encounter similar challenges, according to Tamir. “Supplies need to be available when and where needed for proper patient care,” he said. “However, since most items are not individually tracked or charged for, the methods of knowing when to replenish an item before it runs out are more challenging.”
Dave Rolston, Vice President, Corporate Sales, Medline Industries Inc., Mundelein, IL, called it an issue of ownership.
“Traditionally, storeroom items have been managed by Supply Chain,” Rolston said. “But when you get into clinical or departmental inventories, the responsibility varies. Often, there may be an OR inventory coordinator or the Interventional Radiology/Cardiovascular Lab area may manage their items on their own. But today, there is more of a shift for Supply Chain to be responsible for these inventories. The inventories are expensive and the supplies often have expiration dates that can lead to high-dollar expense-related to obsolescence. Getting this into a more ‘managed’ system/process will likely reduce the amounts on-hand while also reducing the obsolescence.”
Matthew Mentel, CMRP, Executive Director, Integrated Performance Solutions, Mercy, Chesterfield, MO, concurred.
“Central stores inventory is typically better controlled and much more predictable, while clinical inventory can be needed in pinch, is very variable and is typically not well controlled,” he noted. Mentel attributed these differences to who ultimately manages it and how inventory is brought in.
“Central stores inventory is managed by Supply Chain personnel, where clinical inventory varies by who manages it,” Mentel said. “It can be clinical staff, Supply Chain staff, vendor or anyone else engaged in the procedural area surrounding the patient care. Clinical inventory has multiple stakeholders from an ownership perspective, including hospital-purchased, consigned and vendor-managed, trunk stock and just-in-time delivery, etc. Plus, inventory in central stores typically is less costly and has a better turn rate whereas clinical inventory typically is more expensive with much more variable pricing issues, including system pricing versus cap pricing versus component pricing.”
Managing both areas represents a delicate balancing act, according to Suzanne Alexander-Vaughn, senior product manager, marketing, Omnicell Inc., Mountain View, CA.
“Central inventory has to maintain the balance of turning inventory quickly while keeping the essential items for a broad range of needs throughout the facility,” Alexander-Vaughn indicated. “Partnering with clinical stakeholders to assess department needs, standardizing processes for maintaining and regularly updating department needs are important in managing clinical inventory locations.
“Many organizations are now looking at high-volume product that was previously managed as nonstock items as they consolidate operations across their many care locations,” she continued. “This can squeeze limited space and means each item kept in central inventory must be well-managed. Systems that can automate this process have been available for many years and are constantly updated to utilize newer technology, but any system — automated or not — requires oversight, adherence and updates to provide maximum benefit.”
Focus on the data, recommended Nancy Pakieser, Senior Director, Industry Development, TECSYS Inc., New York.
“From a software and technology perspective, it is about how the data will flow,” Pakieser insisted. “Different categories of supplies will have different data elements that follow them. Where the data is stored and how much data is needed will be variable. There is also variability in how we will capture the data — with a bar-code scanner, with an RFID tag, with weighted shelves. For general supplies, enough information to replenish stocking locations may be all that is needed. For procedural or clinical supplies, such as implants, the [Unique Device Identifier] will allow us to capture much more detail and be able to tag it to a specific physician, patient, procedure, price, etc.”
Inventory Management Sidebars:
- When Supply Chain gets inventory management right
- Speedbumps that trip up inventory management efforts
- Do logisticians dream of analog tools?
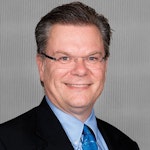
Rick Dana Barlow | Senior Editor
Rick Dana Barlow is Senior Editor for Healthcare Purchasing News, an Endeavor Business Media publication. He can be reached at [email protected].