Inventory Management Sidebars:
- When Supply Chain gets inventory management right
- Speedbumps that trip up inventory management efforts
- Do logisticians dream of analog tools?
When Supply Chain gets inventory management right
Healthcare Purchasing News inquired from a group of healthcare inventory management experts about success stories, why they worked and how those achievements might be applied to other projects. Here’s what they shared.
“An inventory management success story has to include some fundamental characteristics. First, let’s consider the most important criteria — nurses don’t run out of supplies needed to deliver patient care. To make sure this happens, nurses might expect every item, every bin to be stuffed and supply rooms overflowing so nothing ever runs out. But Supply Chain leaders would absolutely object to this approach, knowing it will result in higher carrying costs and the potential for more expiring product. Second, let’s note that nurses don’t want to be inconvenienced with supply management — complex systems requiring nursing to enter data often leads to nurses bypassing the system, which in turn reduces supply chain visibility, efficiency and can ultimately increase costs. Finally, let’s make it clear our inventory management success story must be fueled by accurate, reliable data.
“At a major hospital system in New York City, the Supply Chain team recently found great success implementing a two-bin system in areas with high-volume commodity items. This immediately led to increases in nursing satisfaction — as confidence grows in the system, nurses love the freedom of grabbing supplies they need without having to document their use — while for the Supply Chain team, two-bin has created a significant reduction in on-hand inventory, reducing inventory costs and reducing labor associated with inventory management. At the foundation, this system is all about the data. Accurate, real-time and actionable data is allowing ‘perfect inventory,’ in this case, a system that’s meeting the distinct needs of every key stakeholder.”
— Sophie Rutherford, Vice President of Business Development, Jump Technologies Inc., Eagan, MN
“The success story I would like to share is one that was achieved during my tenure at Greenville (SC) Healthcare System. This particular instance dealt with a single item as opposed to an inventory group. Although the application applied to other devices, this particular instance came about as a result of the OR administrators’ frustration about losing a particular and expensive small, Bluetooth device valued at $19,000. The issue was that this had occurred minimally three times prior, and in each case the item required replacement. Theft was not assumed to be an issue, and the assumption was accidental discarding of the item with the disposable linen. Unfortunately, it was difficult to pinpoint by whom, how and when this may have occurred.
“At that time we were trialing an RFID asset tracking program within the OR. I was aware that the company had the capability to construct a portal for a doorway and a means to affix an RFID tag to the missing item. Having purchased the RFID software and infrastructure, it wasn’t that much to add the portal and load the tag into the system. The concept was essentially very similar to those of high-end department stores with the portal at the exit. We were aware of a ‘pinch point’ or single hallway where most trash must pass through. We had an ideal location for the portal. Furthermore, we had the software capability to allow us to be notified either audibly or through email when a tag was determined to pass through the portal. Staff was informed of this process and the program was implemented. No alarms had occurred for three months and no lost devices were recorded during that time. However, one afternoon I got a call that the alarm went off. Consequently, a team went dumpster diving looking for and eventually finding the Bluetooth item.
“No action was taken. However, four months later, we received another alarm and retrieved another Bluetooth device. As a result, we had documented records of a poor practice and evidence of unintentional loss of the device. Accordingly, the OR administrator set up a new procedure that assigned someone to locate the probe after every case and sign off on its location. This simple extra step appeared to solve the problem. But it was only after we saw proof of the deficient process that made the new procedure materialize.
“Many times in healthcare there are operational processes that are very hard to manage without defined accurate information. The alert on the missing probe told the story and validated a poor practice. This RFID technology is now being deployed in many hospitals across the country to track equipment, people and things, including many inventory applications. I have called the use of RFID as providing visibility to invisible practices and processes, providing information for improved management.”
— John Mateka, Supply Chain Consultant and Interim Director, Materials Management, Clarendon (SC) Health System
“Omnicell has numerous success stories, and all of them share a number of key attributes, such as:
- The customer establishes a program for continual success after the installation which includes dedicated subject matter experts in each department, a regular cadence of system review and updates and incorporating system training as part of the new employee on-boarding
- The customer recognizes the nuanced differences required to make the system most successful within each department, and has worked to configure the system to most efficiently meet those needs.”
— Suzanne Alexander-Vaughn, senior product manager, marketing, Omnicell Inc., Mountain View, CA
“According to the National Center for Biotechnology Information, a branch of the National Institutes of Health, ‘Nurses are the primary hospital caregivers. Increasing the efficiency and effectiveness of nursing care is essential to hospital function and the delivery of safe patient care.’ The less time it takes for nurses to locate supplies, the more time they can spend with their patients.
“Color-coding is recognized as an important aspect of the core 5S of Lean Manufacturing, and these principles are applicable to the healthcare supply chain. We recently renovated a medical/surgical clean supply room utilizing an existing plastic bin storage system, and provided a color-coded ‘Fit-To-Space’ high-density adjustable rack and basket solution. Supplies are organized into customizable compartments with color-coded labels representing each item placed on the front of each basket. Items are organized by category, such as PPE, Suction/Feeding, Lab/IV, etc., arranged together in a vertical storage rack, then a chart is created and displayed to guide nurses to the desired item. By combining this visual method of color-coding, with a simple Kanban inventory methodology of two compartments or bins for each item, dramatic improvements were realized by both nursing and materials management for inventory replenishment.”
— Glenn Tamir, Director, Distribution Channels, Pegasus Medical Concepts, Mission Viejo, CA
“A large multi-hospital system in Texas merged with another multi-hospital system, and based on the new financial requirements, needed to take bi-annual physical inventories of all clinical areas across 10+ hospitals. They implemented a cloud-based, mobile device-driven solution for taking their physical inventory. They take the physical inventory in 24 hours with almost no prep time and post the results one day after the counts are complete.
“Think outside the box. Try something different and you might be amazed by the results. Take a chance on an innovative solution. Innovators are bringing modern-day technology to current problems and achieving great results. Look for all the reasons why something can work and then solve the minor setbacks, rather than trying to conservatively predict every possible thing that could go wrong and then never try.”
— Carl Natenstedt, CEO, Z5 Inventory, Austin, TX
“When we look at successful projects, what we have found is that to be effective, key stakeholders must be engaged early. Engaging end users early and then using their insights and direction in designing the project and solution is especially important in procedural areas. This is centered on designing the right process to accept the appropriate technology. The staff knows what works for the patients and will not tolerate less-than-optimal solutions.
“An example is the current perioperative transformation we are rolling out across our system. The project was structured from the very beginning to engage our clinical perioperative staff in a process and workflow redesign. Once we worked through these process improvements, we then looked for a technology partner that could support the improved process.”
— Matthew Mentel, CMRP, Executive Director, Integrated Performance Solutions, Mercy,, Chesterfield, MO
Speedbumps that trip up inventory management efforts
HPN asked a variety of healthcare inventory management experts about projects that may have missed their mark, along with the reasons why and the lessons learned. Here’s what they shared.
“An inventory management effort might fail for a number of reasons. Recently I’ve worked with a hospital system that’s about to fail in their effort to improve inventory management because they’re trying to ‘boil the ocean.’ They’ve realized they are working with broken inventory management processes from end to end – from clinical areas to central storage, even out to receiving. Now they want new technology to solve their issues all at once. But instead of taking a Lean/Six Sigma approach to break the processes down and examine them in separate segments, they want to apply technology to their existing – poor – processes and take on everything at once.
It’s exciting – this is an opportunity to leverage new technology to automate every step of their dock-to-destination supply management process. They are ready to replace current manual processes with total automation, but they’ve not yet taken the steps to understand what reengineering must occur, the new processes that must be created, and then build toward understanding how technology fits and what efficiencies will be gained and measured. Laying technology on top of old processes doesn’t have a great track record of success. I’m not anticipating it will in this case either.”
— Sophie Rutherford, Vice President of Business Development, Jump Technologies Inc., Eagan, MN
“Throughout my career I have had a number of occasions to use closed cabinets for low-unit-of-measure distribution/replenishment. And in many cases, [they] have been highly successful in recovering patient charge items and tracking inventory. But the key to the effectiveness of these cabinets is the compliance rate or the ability to ensure that users properly record what they take out of the cabinets. This has always been a challenge and continues to be a challenge. If these cabinets are not properly coded, buttons pushed and information keyed in, then the resulting inventory balances are flawed and the efficient process breaks down. For those that cannot achieve nursing compliance, a typical remedy is to have a materials [management] clerk to perform physical frequent inventories and cycle counts to ensure the reliability of the inventory levels and subsequent replacement. Needless to say, that’s a duplication of effort and inefficient.
“Above all, technology is dependent on accurate input and retrieval of information. As with any computer system the same garbage-in-garbage-out applies. However, a number of systems are available to improve this process. Voice recognition is commonly used for distribution centers to pick and put away products. 2-Bin Kanban systems that reduce individual counting by replacing empty bins are proving very effective as weight-sensitive bins that do not require data entry because quantities are determined by weight. RFID also is being deployed to automatically track the removal of products from cabinets and rooms, decrement inventories and charge the patient if appropriate.
“With hospitals and healthcare systems struggling to save operational dollars, more and more of these technologies will be deployed to manage the millions of dollars typically inventoried in hospital, clinics and outpatient facilities.
“A good barometer of this interest is reflected in my recent and current engagement at Clarendon Health System. Paul Schumacher, COO and interim CEO, along with CFO John Shaughnessy, are orchestrating an impressive turnaround strategy. Among other assignments, one of the top supply chain initiatives is to drive down inventories and improve buying patterns. With administrative support it will be exciting to review and recommend the many technologies being offered. Additionally, with the fruition of viable healthcare data standards, healthcare in general will soon be able to manage these costly products like our manufacturing and retail counterparts.”
— John Mateka, Supply Chain Consultant and Interim Director, Materials Management, Clarendon (SC) Health System
“The few unsuccessful installations all have some common threads:
- The customer has minimal involvement and allows the installation team to own the training and decisions instead of taking a lead role in truly owning the system
- There is little to no buy-in from other departments like IT and nursing
- After putting in a system, the customer takes a hands-off approach for long periods of time.”
— Suzanne Alexander-Vaughn, senior product manager, marketing, Omnicell Inc., Mountain View, CA
“Efforts that have missed the mark were often over-engineered solutions where expensive automation and technology was actually a hindering a well-operated supply chain due to a number of factors:
- High cost
- Low user compliance
- Systems management and maintenance
- Expiry of supplies
- Poor space utilization
- Nurse hoarding of supplies due to stockouts
- Low nursing satisfaction.”
— Glenn Tamir, Director, Distribution Channels, Pegasus Medical Concepts, Mission Viejo, CA
“[Successes and failures are] two sides of the same coin. A critical success factor or failure point is a solid change management program. It is important when employing any new technology or software that you engage the stakeholders and end users in a well-planned and executed training and implementation program. Otherwise, you risk a failed or delayed implementation.
“Something that can have an impact on longer-term sustainability of an implementation is the staff that manages the solution. If the staff changes, if they are moved to a different role or leave the organization, this can have a serious bearing on the ongoing compliance and performance. It is important to be aware of the reliance on a single resource and have mitigation plans in place.”
– Nancy Pakieser, Senior Director, Industry Development, TECSYS Inc., New York
“Projects that have been less successful tend to be driven in a top-down approach. There are many layers of compliance needed to support a successful project. It is critical to understand the perspective of the ultimate end-user and their day-to-day to provide a solution that delivers to a higher, overall goal.”
— Matthew Mentel, CMRP, Executive Director, Integrated Performance Solutions, Mercy, Chesterfield, MO
Do logisticians dream of analog tools?
Low-tech methods offer inventory management solutions, too/b>
by Rick Dana Barlow
To automate or not to automate?
Is that really the question when it comes to streamlining inventory and logistics practices in healthcare organization storerooms and warehouses?
To some, it is.
To others, it doesn’t have to be.
For those not mentally shackled to automation as a supply chain technology solution they cite less expensive and lower-tech options among their strategies and tactics for storing and moving stuff.
2-Bin or not 2-Bin?
Forward-thinking supply chain professionals support the 2-Bin Kanban system, whether as an alternative to a high-tech system or as the actual system in place.”An old standby for any Supply Chain leader is to implement a simple Kanban framework,” said Donna Van Vlerah, Vice President of Supply Chain, Parkview Health, Fort Wayne, IN. “Kanban systems have been used to stock supermarkets for decades and was optimized by Toyota back in the 1940s. In this manner the Supply Chain leader can stock just enough inventory/product to meet clinical needs. It also optimizes the flow between your main storeroom and the clinical staff. By using a simple delivery card or empty bin to signal for replenishment the Supply Chain leader can eliminate excess stock and streamline delivery to create the ‘just in time’ concept.”
Amy Flynn, OR/CS Market Manager, Hanel Storage Systems, Pittsburgh, PA, acknowledged the allure of higher-tech solutions, such as automated vertical carousels, inventory management software, bar-code scanning and hand-held devices where healthcare organizations can generate more return-on-investment but added that they’re not for everyone.
“Many hospitals still find themselves with financial or room design constraints that do not yet permit these solutions,” Flynn noted. “In those instances, lower-tech solutions can provide a way to begin controlling inventory without costing a lot of money. One example is Kanban, in which just-in-time inventory levels are managed via a system of index cards and bins. This system still requires considerable amount of floor space but can provide a significant inventory management tool if none currently exist.”
Jean-Claude Saghbini, Chief Technology Officer and General Manager of Inventory Management Solutions, Cardinal Health Inc., Beford, MA, concurred about the benefits of 2-Bin Kanban.”For lower-value supplies, 2 Bin Kanban allows for the appropriate level of management by setting up a replenishment system based on actual usage or consumption, pull versus push,” Saghbini said. “This also creates a FIFO – first in, first out – mechanism to help ensure that stock doesn’t age or expire. This is important because you don’t want to increase waste by throwing out product because it’s expired, old or is being replaced by a newer, better-perceived version of the product.”
John Freund, CEO, Jump Technologies Inc., Eagan, MN, expressed his support of 2-Bin Kanban as well as the watermark system.”Kanban is the Japanese word for ‘indicator,’ Freund indicated, “and using a Kanban system such as watermark or two-bin, provides a simple, affordable and accurate way to manage low-cost, high-velocity supplies. In central supply and on the nursing floors, these items can very accurately be managed using simple systems. Watermark is often selected where there is more space and for larger items. Where storage space is less limited, such as central supply, the larger bins and totes used with watermark can work well. In the storerooms within the units, the smaller bin approach used with two-bin is a great choice. With bins stacked end-to-end on a shelving unit, and the top shelf reserved for empty bins, this approach provides easy access to supplies for nurses and a very easy replenishment process for supply techs.
“Both watermark and two-bin system – when accompanied by the right software infrastructure – are simple to manage and can eliminate some of the major inventory problems hospitals experience including stock-outs, overstocking, waste due to expiration dates, and most importantly, the risk associated with using expired products for patient care,” he added.
Freund reserved another strategy for the specialty areas where more expensive supplies and devices must be stocked and managed.
“Specialty areas such as interventional radiology, cath labs and [operating rooms] have only about 15 percent to 20 percent of the supplies stocked [that] are low-cost consumables,” he noted. “With higher price tags, these items are often bought in small quantities, sometimes ‘eaches,’ and more careful item-level management is required. In these areas, scheduled cycle counting makes sense, particularly on items used with less frequency. Using Kanban for the consumables, supplemented with cycle counting for specific areas, can help ensure the hospital is continuously building good data about supply usage throughout the organization.”
Other options
While most everyone can do 2-Bin Kanban it may not be for everyone.
“Another option would be a modular drawer cabinet system for items such as implants and surgical instruments,” Hanel’s Flynn suggested. “While not the most ergonomically correct storage methodologies, when configured correctly, these traditional drawer systems can offer a somewhat high density on a smaller footprint as compared to shelving systems. Dryer cabinets are also six sided-boxes, which help reduce contamination and exposure of the stored items.
Flynn also recommended “wire partitions, wire mesh enclosures and security lockers” as an inexpensive alternative to highly automated systems [that] can offer a high level of security. “Many manufacturers offer custom and configurable enclosures and locker systems when security and traceability are needed in the storeroom or warehouse,” she added.
Robert Jones, Director of Logistics, Medline Industries, Mundelein, IL, stressed the importance of establishing a “Golden Zone” and avoiding averages.
“Incorporating a ‘Golden Zone’ for those top 20 percent of items that are 80 percent of the activity is an essential tactic for driving efficiency,” Jones said. “Focusing on a limited set of high-volume items will allow materials management to make a broader impact. In the picking process, it is crucial to consolidate these high-velocity items in the storeroom to ensure they are easy to find.”
Jones also advised against using averages to set up inventory targets and PAR values. “Using 6-12-month average usages without looking at daily transactions makes it impossible to identify the volatility of items,” he insisted. “Hospitals that base their inventory targets on averages will not be able to service for peak usages and will be left without inventory.”
Inventory must be easy to find, too, Jones insisted. “Most hospital storerooms are accessed by a variety of employees. In order to aid in their ability to easily find product, it is important to have clear labeling. This starts with proper endcap signage with facility-wide color coding that represents the items category. In order to quickly remove inventory from the on-hand count, items must have a bar code,” he added.
“Whether you are looking at high-tech or low-tech tools, it is based on the best operational process for a specific area, and usually it is the mix of these tools that produces great results,” surmised Nancy Pakieser, Senior Director, Industry Development, TECSYS Inc., New York. “However, a few examples of low-tech tools our partners have utilized would be basic 2-bin Kanban set ups, high-density storage equipment, and various visual systems based on lean principals, such as color coding, lights or signs.
As an example, Pakieser cited one health system that employed a point-of-use bar-code reading system in all of the nursing unit storage rooms, but also had color-coded tags on storage bins based on clinical use. One color represented bandages and wound care, a different color for respiratory, and so on. “They also made an effort to set up each store room in a similar manner so any clinical staff would be relatively familiar with where things would be if they had to float to a different clinical unit,” she said. “By looking at the needs of each area, identifying better operational processes then implementing the appropriate tools, both high and low tech, this health system improved overall supply chain performance and clinician satisfaction. But, supply chain folks had to understand the needs of their clinical colleagues to provide the best overall solutions.”
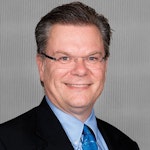
Rick Dana Barlow | Senior Editor
Rick Dana Barlow is Senior Editor for Healthcare Purchasing News, an Endeavor Business Media publication. He can be reached at [email protected].