Like any other aspect of healthcare, technology is responsible for advancing textiles to new levels. Healthcare Purchasing News reviewed a sampling of up-to-date offerings from textile vendors, from linens to cleaning products to patient and staff apparel, and everything in between. Some products are reusable, some disposable. Some textiles may be impregnated with an antimicrobial to assist in thwarting cross-transmission. Some may be tracked electronically for accountability and to reduce costs. Some may be composed of microfiber to really grab those organisms. The variations are many.
Apparel
Scrubs and their laundering and tracking have been an issue for years. Should scrubs be laundered at home or by professionals? How can they be tracked so that they don’t disappear and inventory constantly need to be replaced?
The ScrubVAULT System, a rental and laundry program for scrubs from ImageFirst, addresses those problems with technology. Jay Juffre, Executive Vice President, described the product. “The ScrubVault System is a solution that includes a scrub cabinet; secured individualized access for staff; RFID-chipped scrubs for automated tracking, reporting, and accountability; and a fully managed inventory program.”
Juffre described how their system works to reduce transmission of hospital-acquired infections (HAIs), comply with best practices, and facilitate better patient outcomes. “Our scrubs are laundered in our facilities, which meet or exceed Occupational Safety and Health Administration, Centers for Disease Control and Prevention (CDC), and Healthcare Laundry Accreditation Council standards. Our unique Triple BioShield Protection process comprises (1) a wash process that kills up to 99.999 percent of pathogens, (2) a bacteria-inhibiting softener and a protective coating applied to all textile, and (3) textile products encased in a plastic barrier for delivery. Scrubs are RFID-chipped and secured in the ScrubVAULT. They can only be accessed with unique codes, helping facilities stay compliant with Association for periOperative Registered Nurse’s Guidelines for Surgical Attire, which helps lower costs by minimizing disappearance of scrubs and by reducing staff headaches from trying to find scrubs.”
Juffre believes that reusable scrubs are more cost-effective and less wasteful than using disposable scrubs while allowing staff access to higher quality scrubs. Another costly problem with scrubs is that they tend to walk off with unauthorized users, forcing administrators to buy more scrubs.
“The biggest benefit of the ScrubVAULT is accountability,” said Juffre. “Thanks to the RFID chips embedded in every scrub and the individualized access to the ScrubVAULT, administrators will know who took what, when, and whether they returned it. This helps by minimizing the need for constant replacements purchases, containing costs with accurate and real-time inventory management, automated tracking, and confirmation that a staff member is, or is not, using scrubs that have been properly laundered to meet healthcare industry standards.”
Encompass Group is another manufacturer and marketer of reusable textiles and professional apparel, as well as disposable and single-use medical products. Kelley Terrell, Marketing Director, Techstyles Nonwovens Product Lines, described their products. “Encompass disposable staff apparel is available in the Evolution and Essentials product portfolios, with both elastic or drawstring waist options and four colors to support population identification programs for vendors, visitors, and staff. To drive compliance, Encompass Disposable Staff Apparel Evolution Series features a fabric-like material that provides superior comfort, fit, and performance. They are available in true blue or forest green. The Essentials Series is available in ceil blue or wine and are made of high-quality SMS [spunbond/meltblown/spunbond, a tri-layer polypropylene] for enhanced opacity and breathability].
“Encompass Disposable Staff Apparel is fresh with each use,” said Terrell, “to help reduce the risk of cross-contamination and to reduce costs associated reusable products used by vendors and visitors. It is a comfortable and cost-effective alternative for new fathers/birthing partners.”
If you have ever been a hospital patient, you know that southern exposure can be an embarrassing problem. Boca Terry has a solution that preserves patients’ modesty. Jyll Brink, Healthcare Sales Manager, described their bathrobe as it relates to patient satisfaction. “With the implementation of the Hospital Consumer Assessment of Healthcare Providers and Systems (HCAHPS) survey, we realized the patient’s comfort and need for dignity played a huge part in the final impression the patient had and that our bathrobes could aid in that impression; hence, the Medi-Robe was born.
“We took our high-quality bathrobes and added snaps on the sleeves from collar to cuff, allowing quick access to the patient for tests,” explained Brink. “Patients can stay in the Medi-Robe throughout the day. To walk the halls, the IV lines are fed through the sleeves, and the patient is 100 percent covered front and back.” A chest pocket with a slit accommodates a monitor while the patient is walking. Brink highlighted this point, “Comfortable robes also help children stay calmer, because they don’t see the lines all day.”
Brink outlined some areas in which cost is affected positively: The robes are designed for daily industrial washing and hospital disinfecting requirements. HCAHPS scores may rate higher because patients who use the high-end robes may perceive the hospital offers higher-quality of care. Fewer blankets may have to be purchased and washed, because patients stay warm in the Medi-Robe, even when in cold rooms while having tests performed, when formerly multiple blankets may have been used. “End result,” said Brink, “is Medi-Robes only need to be washed when they get soiled or the patient is dismissed.”
Boca Terry offers more than twenty fabrics to choose from. “All robes are custom designed to meet the needs of the individual hospital,” said Brink. “Add your hospital logo, and you are all set.”
Environmental cleaning
Microfiber hit the market like gangbusters some years ago and shows no sign of slowing down. Nevertheless, insights acquired over time have led to advances in the technology. Matt Schiering, Chief Marketing Officer, talked about what sets apart Contec’s PREMIRA non-disposable microfiber mopping solution. “Microfiber only works well the first time it’s used. After that, it’s a magnet for dirt and contagion.” Schiering believes, “Contec Premira Disposable Microfiber Pads provide superior dirt and debris removal compared to reusable textiles such as cotton or laundered microfiber mops.”
Schiering explained how the pads may help to reduce transmission of HAIs. “Premira Pads dramatically reduce cross-contamination risks, because a new pad is used each time. Disposable microfiber cleaning products, used with appropriate detergents and disinfectants, provide superior and consistent results without the risk of cross-contamination in the healthcare environment.”
Other advantages of the pads include compatibility with most mop hardware, allowing them to fit easily into supply chains and cleaning protocols; bleach-safe; 100 percent synthetic; and they will not neutralize quaternary- or peroxide-based disinfectants.
Schiering referred to the results found in Contec’s white-paper, published in 2015 and reissued in 2017, indicating that “laundered healthcare textiles, such as microfiber mops and wipes, are difficult to clean and disinfect through multiple laundry cycles, resulting in damage to the physical structure of the textiles and retention of organic residues and debris, including viable bacteria and fungi. In contrast,” said Schiering, “the use of disposable microfiber products ensures that the textile fibers are optimized for cleaning, without the risk of contamination by debris or microbes. While the transition from cotton to microfiber cleaning tools has improved cleaning effectiveness and efficiency, evidence from published studies and experiments conducted by Contec indicate that the relatively complicated process of using laundered mops and wipes can result in products with unreliable quality.
“Some may claim that use of disposable products is only a matter of convenience and a ‘nice-to-have’ thing,” said Schiering. “The performance and ease-of-use of disposable cleaning textiles is convenient. But, convenience leads to compliance, and compliance has been shown time and time again to generate improved outcomes.”
George Clarke, CEO, talked about UMF Corporation’s PerfectCLEAN line of products, which includes high-performance reusable microfiber wipers, mops, accessories, and hardware, and Brutabs, an EPA-registered disinfectant containing the active ingredient hypochlorous acid (HOCL). “The PerfectCLEAN–Brutabs combination reduces costs, is sustainable, reduces carbon footprint, and is effective against all ESKAPE pathogens1 [Enterococcus faecium, Staphylococcus aureus, Klebsiella pneumoniae, Acinetobacter baumannii, Pseudomonas aeruginosa, and Enterobacter species] and the WHO’s list of priority pathogens,”2 Clarke explained.
He referred to recent industry advertising suggesting that reusable wipers could re-contaminate patient rooms, resulting in an increase in HAIs; however, he noted, it is important to look at the efficacy of the disinfectant used. “The efficacy of disinfectants has been consistently ignored. UMF selected and offers Brutabs disinfectant tablets to accompany its PerfectCLEAN products. The active ingredient in Brutabs, HOCL, is the same as that generated by the human immune system to fight infections.”
Clarke added, “PerfectCLEAN high-performance reusable wipers, coupled with Brutabs, are the most effective solution for reducing preventable HAIs in healthcare environments.” He cited an in-house study in support of his claim, “UMF recently supported a study, working with a microbiologist and an accredited healthcare laundry, doing before-and-after swabbing of sorting tables, soiled-linen conveyor belts that had been spiked with a spore-forming bacteria, and washers and dryers. The soiled PerfectCLEAN wipers were processed according to CDC Guidelines and tested for viable organisms when they came out of the dryer. The result? Zero. There were no bacteria or spores on the surfaces cleaned and none in the laundered wipers (results on file).”
Patient-bed accoutrement
Patient beds shouldn’t be dangerous places for sick people, but they can be. The presence of the previous patient can linger. Who wants to be the next patient in a hospital bed previously occupied by a patient with Clostridium difficile (C. diff).
Soteria Bed Barrier helps to address the issue of a bed harboring pathogens. Bruce Rippe, president and Chief Executive Officer, Trinity Guardion, described the Soteria Bed Barrier as a launderable, reusable microbarrier that is a cost-effective, practical, and proven method for reducing cross-contamination and HAIs.
“The Soteria Bed Barrier is laundered after each patient, eliminating most time-consuming manual steps to clean and disinfect the mattress and bed deck. The bed turnover process is fast and simple: 90-second barrier removal, wash the mattress and deck with soap and water, and 90-second application of a clean Soteria Bed Barrier,” explained Rippe. He said the bed turnover time is significantly shorter, and no damaging hard-surface disinfectants are required for mattress cleaning. As a result, the useful life and integrity of expensive patient mattresses can be extended. A unique barcoded inspection and documentation process are also performed by laundry staff.
Adherence to CDC guidelines on laundering addresses the threat of pathogens, using detergent, high heat, and chlorine-based disinfection processes. Rippe added, “The barcoded bed barrier is inspected at the laundry to ensure a sound surface for the next patient. Cross-transmission risk is greatly reduced by the consistent, repeatable Soteria laundry process. It works by preventing bacteria such as C. diff, methicillin-resistant Staphylococcus aureus (MRSA), and vancomycin-resistant Enterococcus (VRE) from passing in either direction, to or from the mattress and bed deck. The system is designed to maintain its microbarrier capability through 200 Soteria-prescriptive, CDC-compliant launderings. An independent laboratory test validated that the Soteria laundry process consistently delivers greater than a 99.9999 percent reduction of C. diff, mycobacterium, and other pathogenic bacteria.”
As supporting evidence of efficacy, Rippe referred to a study published in the American Journal of Infection Control that concluded use of a launderable cover for mattresses and bed decks of hospital beds was associated with a decreased rate of healthcare-associated C. diff infection in two long-term acute-care hospitals.3 Another study also found that use of the Trinity Guardion bed cover resulted in decreased C. diff infection.4
Peel Away Labs has a product designed to reduce the potential for cross-contamination. Peelaways is a multi-layered, 100 percent waterproof, disposable, fitted bed sheet that allows clinicians to change bedding in less than one minute, according to Howard Brauner, Chief Operating Officer, Peel Away Labs. Explaining how Peelaways reduces the potential for HAI, Brauner said, “Peelaways replaces the fitted sheet and is available in one, three, and five layers. Each layer is 100 percent waterproof and does not allow liquids, stool, or bacteria to transmit between layers. Disposal of the sheets prevents the transport of infected bedding through the system, thereby helping to reduce exposure to HAIs.
“Peelaways is made of a proprietary blend of fibers, including polyester for strength, viscose for absorption, and bamboo for softness and its natural antimicrobial properties,” noted Brauner. “Peelaways is thirty-two percent softer than traditional sheets. The softness and ease of use provide better patient comfort with potentially fewer skin issues. Peelaways is being used in intensive care units, emergency departments, operating theaters, post-partum, isolation, patient transport, and many more areas in the healthcare world.”
Brauner also noted that Peelaways can save on costs by allowing for better management of staff time and by reducing linen loss, particularly in the emergency department. As for the operating theater, Peelaways was asked to create a special-sized sheet that would prevent liquid penetration and allow for a quick cleanup to change over the room for the next surgery.
Privacy curtains
One of the chief complaints by many patients is that hospitals are so noisy it makes it difficult to rest or sleep. Chinook Acoustics Inc, has a solution. Daana Denzel, Vice President, Operations, describes their HUSH Curtain as “an acoustical privacy curtain that absorbs noise, creating a quiet, private, and peaceful environment in healthcare facilities. HUSH Curtain incorporates vertical pockets into its design that house acoustic inserts. Installing HUSH Curtain in place of regular cubicle curtains, introduces a large amount of absorptive material into an otherwise noisy, reverberant hospital environment. HUSH Curtain meets the weight requirement of any standard track, and it installs easily.”
Denzel said the HUSH Curtain is a custom product, built to each client’s specifications. “It can be built with standard fire-rated polyester cubicle-curtain material that is laundered like normal cubicle curtains, or it can be built with a vinyl-coated linen that is antimicrobial for the lifetime of the product and can be disinfected and wiped clean in place.”
Cleaning and disinfecting a curtain while it is hanging can save hospitals huge costs over laundering traditional cubicle curtains, explained Denzel. “Since the curtain is wiped clean in place, there are no laundry costs, and no labor needed to take dirty curtains down and install clean curtains. There is no need to invest in spare curtains to have on hand when a curtain is changed out. And, finally, it avoids the room downtime that is necessary when having to wait for a regular curtain to be changed out. Cubicle curtains are notorious for being cleaned infrequently and harboring bacteria and germs.” Another important point in its favor is that it enables faster room turnover, noted Denzel. “By using our Clean in Place HUSH Curtain panel, a hospital has the ability to disinfect the curtain after every discharge easily and quickly.”
KleenEdge offers technology for cubicle curtains that allows hospitals to set proprietary protocols for their curtain exchanges. Karen Goelst, President, explained how it works. “Once set, the software will automatically manage and flag the exchange, while also gathering meaningful data, including isolation-room (ISO) exchanges (documenting MRSA, C. diff, VRE) in the background, to quantify the impact of exchange frequency on HAIs and ISO occurrences.” Goelst pointed out that, currently, no such data exists.
According to Goelst, KleenEdge’s cubicle track allows a curtain to be installed within three seconds, for an eighty percent reduction in labor. Installation does not require tall ladders or special gadgets. “Our products profoundly simplify day-to-day operations; more importantly, they create a safer environment for patients and staff by facilitating more frequent curtain exchanges, thus mitigating HAIs. The Leading Edge Panel with 7-day Timestrip, which indicates when it is time to remove and replace the panel, provides a sanitary touchpoint for the leading edge of the curtain. The edge of the curtain is the number six high-risk touchpoint in the patient room and is frequently contaminated after just one week of hanging, according to some white papers.”
KleenEdge offers both reusable and 100 percent recyclable standardized panels with their proprietary Near Field Communication Technology and Quick-Load feature. “In our opinion,” stated Goelst, “recyclable is the optimal choice, as it costs substantially less and will eliminate high inventory and laundering costs, including the cost of lost and damaged curtains in the laundering process. Also, multiple white papers have indicated that bacteria oftentimes survive on the textile curtain despite laundering.”
References
1. Santajit S, Indrawattana N. Mechanisms of antimicrobial resistance in ESKAPE pathogens. Biomed Res Int. 2016;2016:2475067.
2. World Health Organization. WHO publishes list of bacteria for which new antibiotics are urgently needed. http://www.who.int/news-room/detail/27-02-2017-who-publishes-list-of-bacteria-for-which-new-antibiotics-are-urgently-needed. Last accessed November 1, 2018.
3. Hooker EA, Bochan M, Reiff TT, et al. Decreasing Clostridium difficile healthcare associated infections through use of a launderable mattress cover. Am J Infect Control 2015 Dec 1;43(12):1326-30.
4. Kent DJ. Innovation in the village: Clostridium difficile and a mattress cover. Presented at the Wound Ostomy and Continence Nurses Conference; June 2018; Philadelphia, PA. Poster. http://trinityguardion.com/wp-content/uploads/2018/06/WOCN_Poster.jpg. Last accessed November 1, 2018.
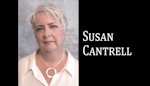
Susan Cantrell
Susan Cantrell is Infection Prevention Editor for Healthcare Purchasing News.