Fairview Supply Chain spotlights Sterile Processing
Centralized corporate sterile processing services for multiple facilities within integrated delivery networks and multihospital systems may pique interest today as an off-site or on-campus enterprise.
But it’s nothing new to Fairview Health Services’ Supply Chain department. In fact, Fairview’s System Central Sterile Services Department (CSSD) has been operating this way for 23 years, according to Lori Ferrer, CRCST, CST, Director, CSSD and Central Processing Center (CPC).
Fairview’s System CSSD occupies 8,000 square feet on the lower level of a building on the University of Minnesota Medical Center West Bank campus, according to Ferrer who joined the System CSSD as Operations Manager in 2012 and was promoted to her current post two years later.
“It started with a few hospitals in 1994 and has evolved into a processing center serving customers in eight Fairview facilities and clinic groups throughout the surrounding metro and community areas,” Ferrer indicated. “System CSSD processes all of the standardized sets for all surgical procedures across our system, as well as providing clinical trays and ancillary instrumentation needs to our customers.”
The group reprocesses 465,000 sets and packages annually. One surgical set may contain up to 150 individual instruments.
System CSSD includes 58 FTEs and 73 team members that cover leadership, instrument technicians, instrument aides, lead technicians and drivers, according to Ferrer. The System CSSD and CPC report to Supply Chain. Each of the Fairview hospital sites has a turn center that reprocesses site-specific items such as physician-preference items, rigid and flexible endoscopes, cameras, daVinci instrumentation and other delicate or very costly items, she noted. Each of these on-site CSSD areas reports to Surgical Services.
One noteworthy System CSSD project involved identifying reasons and implementing solutions for clinic and surgical instrumentation loss. Ferrer’s team visited several sites that processed surgical instrumentation and recovered some $93,000 worth of devices.
“All of the System CSSD instruments are marked with a chemical etch to identify that we own the instrumentation,” said LeAnn Born, Vice President, Supply Chain. “Part of looking at our instrument shortages or missing instruments has included going to our hospital sites to recover and retrieve instruments that may be at their sites.”
Such efforts continue as CSSD, Supply Chain and Surgical Services collaborate.
“We have a great team of Surgery, Supply Chain and CSSD professionals represented on our System Sterilization Oversight Committee and our Advisory Group from all sites who collaborate together and meet monthly,” Ferrer said. “The group establishes standard work practices, policies, product standardization, capital equipment planning and quality monitoring/auditing of current practices regarding the processing of all patient use surgical and clinical instrumentation.”
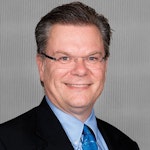
Rick Dana Barlow | Senior Editor
Rick Dana Barlow is Senior Editor for Healthcare Purchasing News, an Endeavor Business Media publication. He can be reached at [email protected].