Hiking through the canyons of a logistics trade show floor, flush with vendors exhibiting the latest material handling devices, equipment and technology, you’ll get a sense that contemporary storerooms and warehouses seem like an amusement park full of workflow-oriented operational rides.
You’ll spot colorful horizontal and vertical conveyor units, roving automated guided vehicles (AGVs), airborne and wheeled drones, motorized lifts, robotic arms with synchronized movements, electronic head-worn and wrist-worn gear programmed with augmented reality capabilities to ensure accurate replenishment and shelving position and a host of additional options sure to populate any busy Supply Chain professional’s wish list.
For high-end, high-tech and high-volume manufacturing and distribution operations, these tools buttress functionality and reinforce fundamental issues related to performance, productivity and workflow. For hospital and healthcare organization storerooms and warehouses, these tools represent a stroll through a logistical FAO Schwartz.
From First in, first out (FIFO) to Last in, first out (LIFO) to inventory turns and the vaunted “Golden Zone,” hospital and healthcare facility storerooms and warehouses may not have to be equipped with dancing robotic arms and Star Wars-like droids scooting around to get the work done.
But how do you design or redesign a storage footprint that can pivot adroitly when demand soars and when supply swells but keep the traffic patterns running flexibly and smoothly?
For more information on storeroom-warehouse design, read “Pinpointing storeroom, warehouse design slips, slides” at www.hpnonline.com/13000938, “Thinking outside the moving of boxes” at www.hpnonline.com/13001320, and “Super storage design may call for up, up and awaaaay!” at www.hpnonline.com/13001544.
Blank check booyah
Imagine having access to virtually limitless resources (challenging to do post-holiday, for sure, but could be therapeutic) to design or redesign a storeroom or warehouse with a keen eye on effective but efficient product flow and fast and seamless performance improvement.
Sound too good to be true? Well, for many, it very well may be. However, some strategists might advise you to envision the end game and work your way back. In terms of equipping a facility, this translates into picking your technology tools and then figuring out how to pay for them or scaling back.
or upgrading a storeroom or warehouse this decade centers on effective data management, sources almost unanimously agree.
For supply chain professionals, storerooms and warehouses typically involve a significant amount of energy to receive, restock and pick inventory on a daily basis, observed Thomas Redding, Senior Managing Director, Healthcare Services, St. Onge Co.
“Streamlining operations requires considerable effort on data standardization and synchronization with suppliers to allow for information to easily flow to ensure a properly designed operation can leverage its assets appropriately,” Redding said. To read Redding’s list of useful tools, read “Dear Santa Storage, this is what I want…” below.
“As markets grow tighter and more expensive, technology is replacing labor in warehousing and distribution,” Richardson noted. “Distributors and manufacturers are already using several of these advanced technologies to reduce labor costs, increase throughput and maximize customer service.” To read Richardson’s list of useful tools, read “Dear Santa Storage, this is what I want…” below.
Yet Gordon Slade, Logistics Director, Intermountain Healthcare Supply Chain, cautions against giddiness and greed when faced with even virtually unlimited resources to make improvements. Why? Available space (that tends to be ceded to revenue-generating enterprises) and product demand.
“Even with a limitless budget and resources, the focus of design and application technology in a medical supply warehouse/storeroom must consider the reality of limited physical space constraints within acute and non-acute healthcare settings,” Slade told Healthcare Purchasing News. “While healthcare facilities should always maintain a finite level of critical supplies for patient [surgical] and emergency/disaster events, supply storage space continues to receive pressure in support of increased utilization of space for patient services. This reality will continue the need for more creative, reliable and timely supply logistics solutions. Keeping this in mind, the future of warehouse storeroom physical location, design and technology must ultimately focus on meeting the changing needs and environment of the end user – regardless of available resources and technology.”
Still, Slade encourages automating existing manual process flows, storage, picking, transportation and replenishment activities, but with a few caveats.
“Automating manual processes should ideally reduce labor dependence and physical inventory space, while increasing service levels to user locations,” he added.
Slade foresees a central warehouse/storeroom as utilizing “robotic and automated solutions to receive, put away, store, replenish and pick items in defined units of measure with little to no direct labor involvement.” That also involves the ability to order cycle times reduced to minutes/seconds for urgently needed critical to life items. “Large or multi-site central storerooms could be served from a larger offsite central warehouse and/or local micro fulfillment center established on or near campus,” he observed. To read Slade’s list of useful tools, read “Dear Santa Storage, this is what I want…” below.
Slade acknowledges that automation and other new tech carries a high initial capital cost and may not yield significant improvement over traditional tech.
“Automation technologies that are stand alone in nature, and do not communicate via a standard protocol, should be avoided,” Slade insisted. “Many suppliers have products and solutions that require custom programming to interface. Managing these complex and variable environments, coupled with every changing operating system versions and different cloud databases can lead to unexpected downtime, poor reliability and system incapability issues. Successful automation system should be fully integrated under a common platform that can manage, monitor, report and adjust to desired performance outcomes.”
Fred Landgraf, Senior Vice President, Supply Chain Solutions, Intalere, delineates between scaled-down, smaller hospital-centric storerooms topping off at 1,000 square feet and large warehouse space as storeroom space exceeding 1,000 square feet typically are repurposed for revenue-generating services. As a result, redesign efforts probably should focus on the warehouse.
“Technology in a warehouse is the primary backbone of the management of the inventory, both from internal management of storage locations and inventory levels as well as external placement of orders to vendors/manufacturers,” Landgraf indicated. That’s why he recommends healthcare organizations invest in a solid warehouse management system (WMS) that will provide “adequate capability to manage inventory at the level of detail required than a materials management information system (MMIS) or enterprise resource planning (ERP) system.
“The appropriate level of WMS will give the system the capability to manage the inventory and operate in a paperless environment with the use of radio frequency technology and hand-held scanners,” he continued. Such technology will enable high-volume picking in case quantities and in less-than-case quantities with storage and material handling equipment spanning from pallet racking through carton flow rack and even potential pick modules with some level of conveyors, he added. While Landgraf sees conveyors as beneficial, he expresses concern that they “can minimize efficiency in high density picking.”
Unless space constraints warrant the use of high-density storage solutions, Landgraf expresses concern that the expense of such technology may outweigh expected benefits gleaned from it.
Landgraf favors a more open-concept approach.
“High-density storage generally requires designated pods or position for picking and give minimal flexibility in flexing to high or low volumes,” he indicated. “Handheld scanners in an open architecture environment give significant flexibility for scaling to high-volume output while minimizing expense when the physical infrastructure is designed appropriately.” He further notes that open architectural storage design enables inventory access even during power/system breakdowns and outages.
The economics of designing or redesigning storage space extends beyond making expense management more efficient and pushes into revenue areas, asserts Beth Riggio, Director, Solutions Management, Swisslog Healthcare.
“The warehouse of the future is designed to maximize usable space at hospital for revenue-generating patient care areas,” Riggio told HPN. “In many metropolitan areas, the per-square-foot cost of hospital space is at a premium. That makes storing products there relatively expensive. In addition to this direct cost there is an opportunity cost. In-hospital storage takes up precious space that could be better used by repurposing it to offer new or expanded, high-margin services. Consequently, in-facility storage has a double impact on a hospital’s budget.”
By contrast Riggio notes that centralizing storage and distribution of med/surg and pharmacy items at a Consolidated Service Center (CSC) liberates healthcare facility space for better use. “Moreover, administrators can drive down the per-square-foot cost of storage by purchasing or leasing space in less-costly areas,” she added.
Such realization fuels expansion and growth in the CSC distribution model, according to results of a Swisslog Healthcare survey of hospital supply chain executives last year. Survey results showed that 43 percent of respondents report currently distributing from a CSC and another 43 percent are considering it, Riggio noted.
As larger distribution centers, CSCs can consider different types of technology, such as comprehensive WMS, automated guided vehicles, pick-to-voice technology and even robotic goods-to-person storage systems, she indicated.
Riggio cited Indiana University Health as a particular success story that supports 17 hospitals and picks 7,500 lines per day. [See the September 2018 HPN for details or search for IU Health on HPN online.] “In a traditional manual picking model, hospital distribution centers target 60 picks per hour. However, the robotic [low-unit-of-measure] picking system at the IUH Integrated Service Center enables three people to pick 500 lines per hour at 99 percent accuracy,” she added.
CSCs also provide additional avenues for service line growth, such as pharmacy, according to Riggio. She cites a recent Swisslog Healthcare survey of pharmacy executives as finding that 75 percent of health systems currently using a CSC model report an ROI in less than 12 months.
“When pharmacy can share an existing warehouse space with supply chain, it significantly reduces the investment required to centralize operations and strengthens the case for consolidation,” she said. “When you think about all the possibilities for centralization and consolidation of distribution and management of shared services, the question is no longer simply, ‘What does the warehouse of the future look like?’ The question becomes, ‘What can the hospital of the future accomplish thanks to innovation in supply chain management?’”
Shakedown breakdowns
In cases of backorders, breakdowns, outages and shortages, Tessa Natterer, Director, Supplier Performance, PartsSource Inc., recommends looking outside the box.
“Healthcare supply chain leaders fear critical item shortages and back orders, an increasingly common problem with clinical supplies,” she said. “Clinical engineers face the same challenge as it relates to back-ordered and slow-to-ship parts and service that takes months to schedule. These challenges lead to delays in equipment repair, lost revenue, waiting patients and idle CE staff. Instead, if resources were limitless, building the artificial intelligence to predict and automate your ordering would dictate warehouse size and design specific to your facility’s patient requirements.”
And if a healthcare organization cannot achieve such AI service itself it can look to a third party serving as a warehouse extension, Natterer continued. “Based on millions of transactions made by hundreds of hospitals, we leveraged aggregate data from CE teams to determine which mission-critical replacement parts are often out of stock or have long lead times to ship,” she noted. “The identified critical products are now guaranteed in-stock at our warehouse, ready for prompt shipment to members of the PartsSource Pro community, saving hospitals significant stock out or backorder days, but not adding to their warehouse requirements.”
Because operating rooms, no matter how technologically advanced they may be, require sterile storage support, they should consider automated vertical storage equipment to help them “make maximum use of minimal space” and “to protect sterile supplies from the possibility of contamination,” insisted Amy Flynn, OR/CS Market Manager, Hänel Storage Systems.
Hänel’s sterile storage inventory management systems not only improve accuracy to more than 99 percent, but also reduce the likelihood of shortages, expired items, having to spend valuable time to correct errors, and having to spend time searching for items urgently needed in the OR, Flynn noted. “The Hänel Rotomat has been proven to boost productivity due to increased efficiencies in supply retrieval, streamline operations by lowering the need for a large staff, increase inventory security by storing expensive implants and supplies within a secure six-sided unit, provide additional security by requiring password access or keycard swipe in order to obtain supplies, improve ergonomics by keeping movement within the OSHA-suggested ‘golden zone’ between the waist and mid-chest height, and mitigate infection rates by keeping sterilized supplies within a closed environment.”
Flynn doesn’t recommend hospitals adding a roomful of individual compartment racks as their storage solution. “These racks allow sterile supplies to be organized into removable plastic compartments, but the baskets often fall out of their tracks,” she said. “The bottom of one compartment often drops into the open top of the one below it, or a bin may have multiple types of items in it, so organization can very easily give way to chaos. Even though these racks have wheels, the combined weight of all the items on board makes it difficult to roll, and someone still needs to access items by moving outside the golden zone to do so.”
Minding maturity
Deep pockets should take a back seat to efficient and intelligent use of resources, advises Carlo Malaguti, M.Arch., Senior Supply Chain Applications Specialist, Warehouse Design, TECSYS.
“Every warehouse and storeroom should be viewed as a queuing system where products received join a queue (stored) and are waiting to be serviced (shipped or used),” Malaguti observed. “The holy grail of that queue is when technology, time (labor) and space (storage) are synchronized so perfectly that inbound and outbound flow at a constant rate. No matter how deep your pockets, that fundamental concept should guide you.
“It is certainly an interesting thought exercise to imagine intelligent sortation, image-based dimensioning equipment, automatic de-stacking and sortation, automated storage and retrieval systems, robotized order picking, automated AGV loading, routing and stocking — the list goes on,” he continued. “Ultimately, though, we ought to think about diminishing returns on the technology we implement, both financially and logistically.”
Malaguti recommends investing in Auto-ID technology that connects a facility’s inventory to its storage facility. This strategy extends beyond what he calls a “well-oiled software platform and appropriate use of data capture technologies” to create a “network of datapoints to tap into the purest form of continuous improvement.
Malaguti further emphasizes the need for standards-based tracking and tracing processes.
“Devices, equipment and products need to be tracked using supply data standards, and a new generation of disposable, wireless microchip can satisfy that requirement and then some,” he said. “Other than [identifying] every single item/[unit of measure] and carrying a huge volume of data, these microchips can also communicate temperature, ‘smell’ the surrounding, register shocks and unwanted movements, or confirm location within the supply chain when interacting with wireless locators. The microchip can be inserted by the manufacturer, programmed based on requirements of the customer, and have the capacity to capture and transmit information until it reaches its final consumption point, including recycling or waste disposal data for statistical purposes.”
Dear Santa Storage, this is what I want…
Healthcare Purchasing News asked a variety of inventory management and logistics experts to stock their storerooms and warehouses with the “ideal” technology tools that befit a winter wonderland of products and services. HPN specifically called for tech tools to include versus tech tools to ignore, regardless of financial resources.
Gordon Slade, Logistics Director, Intermountain Healthcare Supply Chain
Warehouse-specific:
- Automated Materials Handling Systems (AS/RS) and other automation solutions for put- away and high vertical storage building design
- Automated robotic tote picking solutions for low unit of measure and case pick
- Automated pallet configuration and architecture to support AGV use at end user location.
- Specific items received are auto serialized with unique barcode or RFID labels and individually tracked and traced through to end use.
- Use of AI tools for predicting product usage patterns, use forecasts, optimal inventory levels, purchase quantity and frequency.
- Use of supplier-owned product (Vendor Managed Items) systems and tools to provide real-time usage, location forecasts and replenishment trigger for supplier owned products
- Exploration and use of autonomous fleet delivery vehicles from central warehouse to healthcare facilities.
- Use of aerial drones for delivery of critical and time sensitive materials to and from warehouse, lab, clinic and hospitals.
End-user inventory locations/storeroom-specific:
- Vision, RFID, auto scan and other advanced methods for tracking inventory and auto replenishment triggering
- Use of Automated Guided Vehicles, (AGV) for internal delivery of replenishment supplies from warehouse / storeroom to end user locations within hospital and clinics
- Use of aerial- and/or ground-based drones to transport time-sensitive /critical medical, tissue or pharmaceutical supplies from source to point of need
- Use of real-time AI tools to predict and adjust point-of- use item demand patterns, inventory stocking levels, along with optimal item reorder point and locations
Thomas Redding, Senior Managing Director, Healthcare Services, St. Onge Co.
Processes to automate:
- Full visibility of inbound materials from vendors (ASN)
- Automatically unloading inbound materials via robot and/or human-assisted robot
- Automatically sorting materials via conveyor or equivalent
- Automatically scanning each box via barcode and/or vision technology and completing handshake with supplier’s and internal data
- Automatically receiving and updating inventory through use of warehouse management system (as a WMS makes sense given the scale)
- Automatically restocking inventory via articulating robot and/or human assisted robot
- Automatically retrieve inventory via goods to picker system; where goods to picker systems are not appropriate for the inventory type and manual picking is required, the use of wearables (voice and picker assist device – such as a glove integrated with RF scanner) to automatically capture product data is imperative.
- Automatically pick inventory via articulating robot into transport container and order synchronization
- Automatically transport via robots through optimized transport dispatch
- Automatically generate replenishment order and confirmation through supplier visibility via blockchain technology
- Automatically optimize inventory through machine learning using product availability (via blockchain), product lead time, and product demand profile
Tech tools to consider/include:
- Articulating Robot – Enables accurate and reliable picking of inventory, eliminates manual picking.
- Vision Technology – Provides consistent capture of information, eliminates manual receiving of materials.
- Goods to Picker Technology – Allows for reliable retrieval of materials, eliminates manual retrieval of materials.
- Robots (AMR) – Ensures reliable transport of materials to/from and within storeroom/warehouse – eliminates manual transport of materials, including “follow-me” robots.
- Blockchain – Provides a mechanism for product availability, eliminates the unknown of product availability, which is a major issue for the industry
- Machine Learning – Enables inventory optimization through visibility of product demand, availability and lead time, eliminates manual inventory management.
Tech tools to ignore:
- Drones – There is a significant effort to commercialize drones for transport of materials; the use within a storeroom/warehouse could be leveraged for such things as cycle counting but it will take time for the technology to evolve, especially the battery technology and pay load capacity.
- Augmented and virtual reality picking technology – another example where the technology will evolve for assisting pickers to enable the picker to virtually see product information (such as unit of measure, expiration, product specific requirements) while picking an order.
Jim Richardson, Portfolio Executive, Senior Consultant, Vizient Inc.
Useful tech for optimal workflow:
- Radio frequency identification (RFID) — Stay paperless with accurate real-time inventories (no manual steps necessary) and every product automatically tracked from receipt into warehouse to receipt by customers. This has numerous supply chain benefits, not the least of which is near perfect inventory management to ensure no stock outs and no lost or expired product.
- Warehouse Execution System (WES) — As inventory is brought into the warehouse, RFID would allow each product to be automatically received into the WES, which would then add it to inventory and give instructions on where it should be stored in the warehouse, again, with no manual intervention necessary.
- Articulated robot arms — These could be used in combination with conventional conveyor belts to automatically unload incoming trucks. RFID sensors would read the product and purchase order (PO) information as the products are being unloaded/loaded onto conveyors by the robotic arms. It is also possible to use the robot arms to pick/pack low unit of measure (LUM) orders after they have been delivered to the packing station by the automated storage and retrieval system (AS/RS).
- Automatic Storage/Retrieval System — The received product would be taken off the conveyors by the AS/RS and based on instructions from the WES, it would be put into storage locations with no manual steps necessary. As orders are received by the WES, instructions are sent to the AS/RS, which automatically picks the cases necessary for order fulfilment. Bulk-case picks are delivered directly to a shipping station; LUM picks are delivered to an order-packing station (manual or articulated robot arm packing into cartons or totes). This would utilize goods-to-person (G2P) picking methodology, which eliminates most of the labor (movement) associated with order picking. WES issues the instructions using pick-to-lights or pick-to-voice personnel packing the LUM orders.
- Sortation systems — As picked orders are put onto conveyors (either full cartons or LUM in totes), they are automatically transported to the shipping staging areas. Here each case or tote (identified using RFID tags) are automatically sorted (using RFID sensors) onto an accumulation conveyor at the proper truck-loading dock. Because of the nature of health care provider customers, some manual loading of carts or pallets may be necessary at this point to load the carts/pallets properly, and in the necessary sequence on the delivery vehicles. This process could also be instructed by the WES using voice instructions, ensuring the correct packages get to the right customer.
- Performance data technology — Performance data is usually obtained from the warehouse execution system (WES), but additional technology can be used to present the performance data into management-friendly formats to measure and report facility and worker operational metrics, as well as customer-focused metrics.
Tech options that may not be useful:
- Vertical picking modules (VPMs) — They require manual intervention, additional integration with WES and are relatively slow to replenish.
- Vertical carousels — Similar to VPMs, but are even slower to pick from and to replenish.
- Horizontal carousels — Not used because they require large amounts of floor space and are relatively slow to replenish, requiring much manual intervention.
- Automatic guided vehicles (AGVs) — These are typically employed to replace fork lifts that move product from one location to another; with the conveyors and WES in place, this activity should be minimal.
- Autonomous mobile robots (AMRs) — These robots perform many of the same functions as the AS/RS system but do not take advantage of vertical storage space, as do AS/RS systems.
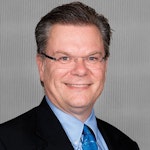
Rick Dana Barlow | Senior Editor
Rick Dana Barlow is Senior Editor for Healthcare Purchasing News, an Endeavor Business Media publication. He can be reached at [email protected].